The Stoofbrug pedestrian bridge, designed by MX3D, was opened by Queen Máxima of the Netherlands on 15 July 2021.
It is breakthrough time for a relatively new technology that combines arc welding with robots and computer software. Wire Arc Additive Manufacturing allows 3D-printing of large objects at less expense and in a far shorter time. After years of extensive research, commercialization has begun, and heavy industry is set to be transformed.
By James Chater, Stainless Steel World
Welding + Robots + AM = WAAM
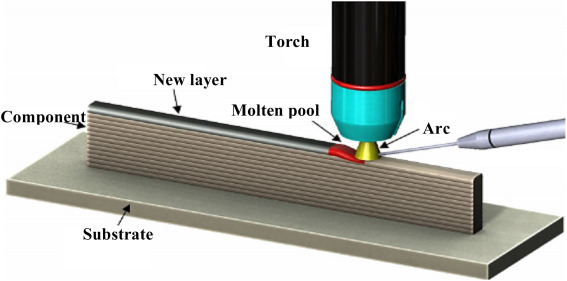
Who would have thought it? Additive manufacturing (AM), until recently limited to small, complex components, is now being applied to much larger objects. This is achieved by combining standard welding equipment with CAD/CAM software similar to that used in AM, allowing metal deposition to be carried out with robots, over a volume not confined to an enclosed chamber. This is not equivalent to welding as conventionally defined, i.e. joining different parts. Instead, the whole object is welded layer on layer, in one piece, just as in 2D or 3D printing. The implications for heavy industry, both in terms of manufacture and deliverability of spare parts, are momentous.
WAAM has emerged as one of the most promising techniques for AM manufacturing of large components. It has the advantage of relying on existing welding equipment (GTAW/TIG, GMAW or PAW). The welding arc deposits melting wire in successive layers in a process governed by CAD software that directs an omnidirectional robot arm or gantry system. The component’s dimensions depend on the length of the robotic arm, which can currently go up to about 6 or 7 metres but will likely increase in the future. By allowing near-net shapes, WAAM technology brings enormous savings in the consumption of materials, while the elimination of casting and machining means a part can be produced in hours or days rather than weeks. As with all AM, complex and hollowed shapes are easier to achieve than with older methods.
A variety of metals can be used, alone or in combination: carbon steel, stainless steel, Al-, Ni- or Ti-based alloys and refractory metals such as niobium, tantalum, tungsten and zirconium, heat-resistant materials used in nuclear power stations.
Investments
The main challenge posed by WAAM is the need for large investments in both equipment and expertise, across institutions ranging from academia, government agencies and private companies. One of the leading efforts is based on the University of Cranfield (UK), which has been collaborating with other universities and institutions and with private firms (Airbus, BAE Systems, Lockheed Martin). Earlier this year the university helped form a consortium, supported by Innovate UK, bringing seven organizations together in an academic-industrial collaboration. More recent is the Europe-based Grade2XL project, a consortium launched in March 2020 that consists of companies across the supply chain (software producers, equipment suppliers, welding companies and end users) working to develop WAAM technology and increase its commercial viability. This year two of the collaborators, Valk Welding and RAMLAB, delivered a 3D-printing cell with two workstations to the French tube manufacturer Vallourec.
“AM” or “3D printing”?
“Additive manufacturing” (AM) and “3D printing” are just two of many terms denoting the process of layer-on-layer printing controlled by computer software. An earlier term, coined by Chuck Hull, the co-founder of 3D Systems, is “stereolithography” (SL), which first developed in Japan in the early 1980s and used ultraviolet light. In 1984 two patents for SL were filed by Chuck Hull and by three French scientists. The dawn of the 21st century saw the introduction of different technologies which reduced the costs of manufacturing in 3D. After 2010, “AM” and “3D printing” emerged as umbrella terms for these techniques, and they are still battling it out. The former term is preferred by professionals and technicians, whereas the latter is more popular and familiar. I tend use the term “AM” as a noun but “3D-print” as a verb.
Applications
Aerospace
Like AM, one of the earliest markets for WAAM was aerospace. Cranfield University took the lead by building a 1.2m-long WAAM-printed titanium aircraft wing structure in a record 37 hours; this was followed by a larger aluminium wing part. A major application is a tool for printing carbon-fibre components called a lay-up mold. These are made either from steel or from invar (nickel-iron alloy), the latter having the advantage of keep thermal expansion to a minimum during curing. Lincoln Electric and Boeing are collaborating on a composite cure tool. Cranfield also collaborated with Thales Alenia Space and Glenalmond Group on a prototype of a titanium (Ti-6Al-4V) pressure vessel to be used in future space missions.
Meanwhile, French manufacturer Stelia Aerospace has WAAM-printed aluminum panels for an airplane fuselage. AM, and with it WAAM, is expected to play an important role in space, especially in building habitats on Mars.




Offshore and marine
The tubular components and piping of offshore facilities are critical and must not be allowed to fail from corrosion or fatigue. AM and WAAM are one way to increase the structural integrity and strength of these components, so there is every motivation to increase use of WAAM technology in the future. In 2021 Vallourec supplied Total with a WAAM-printed waterbushing (a device for counter hydrocarbon kicks from wells in construction) for its EIG Well in the North Sea, the first time such a safety device has been 3D-printed. RAMLAB supplied the WAAM technology.
WAAM technology is ideal for marine applications because of the large volume of ship parts. In 2017 a prototype ship’s propeller, the “WAAMpeller” was created by a consortium Damen Shipyards Group, RAMLAB, Promarin, Autodesk and Bureau Veritas. It was fabricated from a nickel-aluminium-bronze alloy at RAMLAB in the Port of Rotterdam. Two years later, Sirenha (Naval Group) and Centrale Nantes used WAAM to create the world’s first hollow propeller blade, in stainless steel. Recently, Cranfield University successfully WAAM-printed a marine impeller (water jet propulsion unit) in 316L.
What is MFG?
In early October, manufacturers will be celebrating MFG Day. It stands for “manufacturing”, though it took me a few seconds to figure this out! It was proclaimed in 2019 by then-President Trump and is held each year on the first Friday of October. It coincides with the start of the academic year, and one of its goals is to allow engineering companies and students to get to know each other. Hi-tech engineering jobs are hard to fill, and MFG meetings are one way of raising awareness and tackling the skills shortage.


Other transport
WAAM is attractive as a way of making the complex parts of vehicles, especially of the sport or specialist type, where production runs are limited. PIX is working towards WAAM-printing the chassis of its self-drive vehicle. The Dutch company MX3D used WAAM to generate an aluminium bicycle frame.
Infrastructure and art
The same company built the Stoofbrug, a pedestrian bridge spanning a canal in the heart of Amsterdam’s old centre. The distinctive swirling lines were created with WAAM technology, four robots being deployed. The structure paves the way for the future use of WAAM in other architectural projects. Among MX3D’s partners were ABB, Air Liquide, ArcelorMittal, Autodesk, AMS Institute and Lenovo. The structure is equipped with sensors that monitor its performance. Finally, WAAM has made an incursion into the world of art. MX3D collaborated with artist Ricardo Regazzoni to WAAM-print a 4m tall steel sculpture known as the Tresse Tower. It is made of stainless steel, with gold plating applied to the tips. The sculpture stands in a private garden in Eygalières in the south of France.
Certification
The surge of interest in WAAM has provoked a flurry of activity from bodies concerned with certification and standards, mainly as it concerns the marine and offshore industries. DNV, the Norwegian safety agency, has been at the forefront in investigating failures and formulating standards for the use of AM and WAAM. In 2018 Australia’s AML was the first WAAM facility to be certified by maritime certification authority Lloyd’s Register. In 2019 ASTM drafted the WK69732 guide for WAAM, this draft standard is still under development. The same year DNV published its WAAM guidelines. A guideline towards WAAM- and LPBF-produced certified parts, managed by DNV-LG, appeared in 2020, involving the collaboration of several offshore companies.


Update
The text in the Certification box has been updated. In the original text it was said the WK69732 guide for WAAM was already published. This is incorrect. As of February 2022, it is still in draft.
Every week we share a new Featured Story with our Stainless Steel community. Join us and let’s share your Featured Story on Stainless Steel World online and in print.