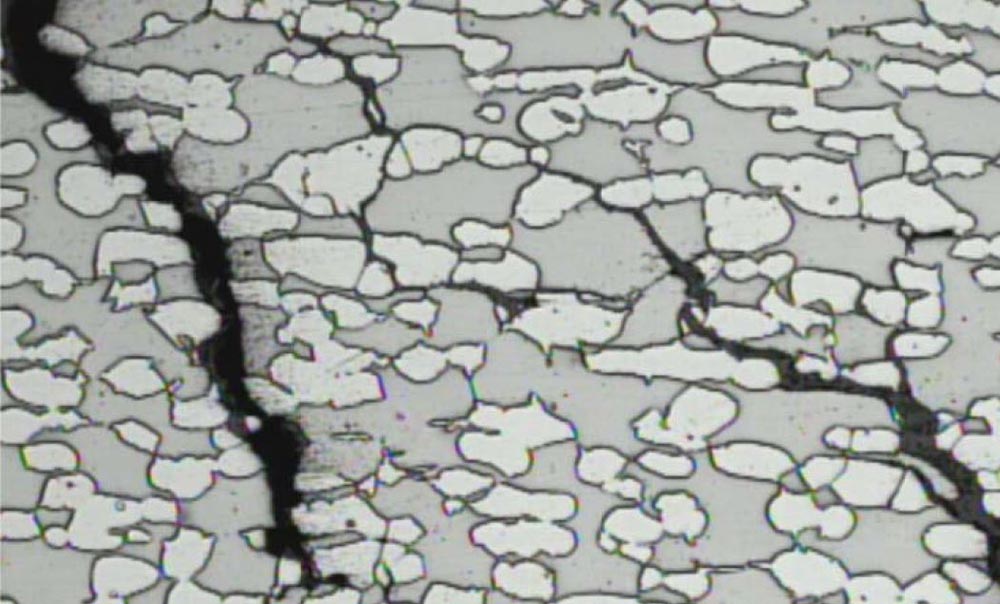
By Roger Francis, RFMaterials, UK
Caustic soda (NaOH) is widely used in industry, and at lower temperatures and concentrations carbon steel is commonly used. However, at higher concentrations and temperatures the corrosion rate increases, and there is a significant risk of caustic stress corrosion cracking (SCC). In such cases it has been common to switch to nickel alloys, with a significant rise in cost. This paper shows that duplex stainless steels have good resistance to both general corrosion and SCC in caustic solutions over a wide range of concentrations and temperatures. The limits of use and some successful service experiences are presented to show how duplexes may be applied cost effectively.
Caustic soda (NaOH) is widely used in industry for a variety of purposes, including pulp and paper, soap, detergent, catalyst recovery, mineral processing, pH control and many others. As caustic concentrations and temperatures increase, the corrosion rate of carbon steel increases, and also the risk of SCC.
The recommended limits of use to avoid excessive corrosion of carbon steel in caustic soda vary from 50° to 80°C depending on the source1, but carbon steel is often used at higher temperatures with a corrosion allowance.
The limits of use of carbon steel to avoid caustic SCC are in NACE SP0403 (Figure 1), and it can be seen that the temperatures significantly exceed 80°C where carbon steel is allowed with stress relief2. However, there are frequently SCC failures of carbon steel at elevated temperatures and one reason for this is that not all commercial caustic soda is pure.
The most common method for caustic production is the diaphragm process and this will always contain chlorides, typically at around 1% concentration, but individual batches maybe 5 or more times this. The presence of chloride significantly affects the corrosion of carbon steel. In addition, diaphragm grade caustic also contains ~0.3% chlorate, which is an oxidizer and can move the potential to a region where SCC is likely. Caustic soda made by the membrane method contains low levels of impurities, but it is more expensive.
It can be seen in Figure 1 that where carbon steel is not satisfactory, nickel alloys are recommended. The most common ones are alloys 400 (UNS N04400), 800 (UNS N08800), 600 (UNS N06600) and nickel 200 (N02200). This alloy change represents a significant increase in the cost of equipment. What is less well publicised is the fact that duplex stainless steels perform well in caustic soda, and at lower cost, although they do have limits of use, as is discussed below.