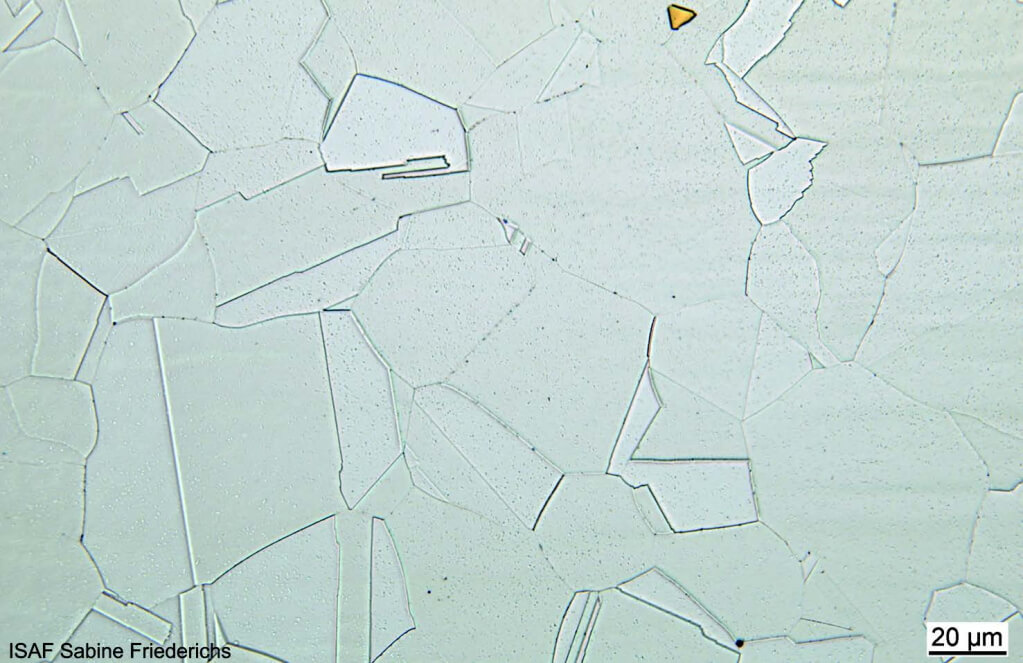
Alloying austenitic stainless steel with strong carbide-forming elements such as titanium can avoid the precipitation of chromium carbides.
By Sabine Friederichs, Technical University of Clausthal, Germany
Austenitic stainless steels are widely used in the chemical, petrochemical and nuclear industries. They are composed of iron, chromium, nickel, sometimes molybdenum and a small amount ( 0.1 %) of carbon. This composition leads to outstanding corrosion resistance in combination with good mechanical properties.
Another advantage of austenitics is their excellent biocompatibility which leads to them often being used in the biomedical industries.
Corrosion resistance is created by a thin, approximately five nanometers oxide layer that forms on the surface of the material. To form this passive layer, the chromium content in stainless steel must be at least 10.5%. If more chromium is added, the passive layer becomes more stable, and the corrosion resistance increases.
However, in the temperature range of 500- 800°C, these steels have the unfortunate tendency to form intergranular corrosion (IGC) and intergranular stress corrosion cracking (IGSCC) in certain, i.e. chloride environments. Chromium carbides can form in these conditions, mainly along the grain boundaries.
Chromium carbides (Fe, Cr)23C6 have a negative effect on corrosion resistance, as they bind a high chromium amount out of the matrix and thus impede or prevent the formation of the passive layer.
It is worth mentioning that other compounds such as the sigma or chi phase (Fe36Cr12Mo10) can also reduce corrosion resistance because these phases remove chromium or molybdenum from the austenitic matrix.
Avoiding precipitation of chromium carbides
There are two ways to avoid the precipitation of chromium carbides. On the one hand, the total carbon content can be reduced. Unfortunately, this only delays the susceptibility of corrosion but doesn’t prevent it.
The second possibility is to alloy the steel with strong carbide-forming elements such as titanium or niobium.
The quantity of titanium alloyed depends on the content of carbon and nitrogen. In general, the optimal titanium content is determined according to the following formula:
%Ti = 5x (%C + %N)
Therefore, the steel grade 316Ti contains a small amount of titanium, which stabilises the structure at temperatures over 800°C. This prevents carbide precipitation at the grain boundaries and protects the metal from intergranular corrosion due to the chromium depleted zone.
Titanium shows a greater tendency to carbide formation than chromium and reacts preferentially with carbon to form titanium carbonitride, so that no chromium depletion forms in titanium stabilised stainless steels and a uniform oxide layer is maintained.
However, the formation of titanium carbides and titanium carbonitrides in the microstructure leads to a higher hardness due to the solid solution strengthening effect. It also reduces the notched impact strength, ductility and machinability.
About the author
Sabine Friederichs has worked at the Clausthal University of Technology (German) for 33 years as a metallographer and material tester/inspector in the Institute for Welding and Machining.
In addition to metallographic examinations, her tasks include tensile tests, notch impact tests, and hardness measurements. She is also qualified to train material testers. Sabine also supervises students, interns and trainees, plus she works as an honorary examiner for the Chamber of Industrie and Commerce. Email: sabine.friederichs@tu-clausthal.de