^ Launch of Sanicro® 35
Article By Joanne McIntyre, photos courtesy of Sandvik Materials Technology
While the past eighteen months have seen many challenges for all companies, the Sandvik Materials Technology team had cause to celebrate. With the launch of Sanicro® 35 and the addition of SAF 2205TM+ to the portfolio, Sandvik is streamlining supply chains and saving end users money.
Outlook
Stainless Steel World spoke to Marcus Hillbom, Manager Technical Marketing & Customer Service, and Andreas Furukrona, Product Manager and Team Manager, about these innovative new grades and what they mean for bar and tube users and distributors.
Since Sanicro® 35 was launched in August 2020 a lot has changed globally, largely due to the Covid-19 pandemic. Fortunately, as Andreas explains, since the third quarter last year, there have been strong recovery signs in European and US stainless steel markets. “We were able to end 2020 on a good note with a robust upturn in the general engineering sector. As we move into 2021, we can see the beginning of a recovery.” The future looks bright for Sandvik’s latest material releases.

Marcus Hillbom (left) and Andreas Furukrona.

Sanicro® 35 tubing combines the best features of a super-austenitic stainless steel and a nickel alloy.
Tubes for the toughest applications
Andreas is keen to tell Stainless Steel World readers about Sanicro® 35, Sandvik’s innovative new alloy, which combines the best features of a superaustenitic stainless steel and a nickel alloy. The grade has excellent corrosion resistance for service in seawater applications and other highly corrosive environments.
“When selecting material for severe applications, normally a choice is made to either select duplex or higher nickel alloys such as alloy 625,” explains Andreas. “But what if you could combine all the desirable properties of these grades into a single material? To achieve this, our R&D team set out with a clear objective; to produce a new grade that bridges the gap between high nickel alloys and duplex, which could be manufactured in any Sandvik mill in the world. The successful result saw Sanicro® 35 launched in August 2020 in heat exchanger and hydraulic and instrumentation (H&I) sizes. We have high expectations that this will be at the same level of innovation as SAF 2507™ was for Sandvik once upon a time.”
The composition of Sanicro® 35 makes it a cost-effective alternative to more expensive alloys, explains Andreas. “In severe applications for heat exchangers where alloy 625 is often specified, for example REAC air coolers, this grade can do the same job at a lower lifetime cost. With just half as much nickel, the material provides excellent resistant to pitting and crevice corrosion as well as stress corrosion cracking, while also being more economical.”
Ongoing heat exchanger trials in different regions are proving the value of the new grade.

The SAF 2205™+ bar is optimised to withstand extreme corrosion.
H&I tube and fittings trials
Sanicro® 35 is ideal for H&I programs that typically require tubes ranging from 6 to 12 mm (1/4 to ½ inch). “At the same time, we have potential partners trialling the grade to produce small bore fittings which can be used with the tubing to provide a complete package,” explains Andreas. “Ongoing galvanic trials will demonstrate that this tubing can be successfully used with other types of fitting, for example 6Mo, so you don’t have to switch the whole system.” Andreas explains that the vast majority of H&I tubing is specified in 316L, with the remainder being spread over nickel alloys such as alloy 625, 400, duplex, super duplex, 904L, etc. Sanicro® 35 can effectively replace all these grades, eliminating the need for a distributor or supplier to keep multiple products in stock.
“So not only is it more cost effective, it will also streamline the supply chain While it will take some time for this to be implemented, we are working closely with end-users to gain their acceptance of the grade and start integrating it into their standards.”
No welding issues
In addition to having very high mechanical strength, Sanicro® 35 also has good weldability, as demonstrated in trials using nickel alloy consumables. “Alloy 59 is the recommended filler material, and when using proper welding parameters, there are no issues in welding this material. In fact, it’s generally accepted as being easier to weld than duplex,” explains Andreas.
Great market response
Launching a new product is always a cause for excitement, and as Andreas explains, the team were not disappointed when Sanicro® 35 was released. “We planned to make the introduction at the NACE conference, which had to take place via webinar in 2020. We had around 400 participants, and the number of specific questions that came in was incredible, somewhere around 150 questions in all. We divided the questions by region and had our local experts address these within their own areas. Interest has remained very high, so we are keen to get the material into some projects. We are very positive about the market response and have sent test coupons to some key companies.”
“Apart from its unique ability to bridge the gap between duplex and high nickel alloys, the fact that this is a truly global grade is very appealing to the market. It will be made in all our mills, ensuring availability everywhere. We already have it in stock; we’re ready to go!”
Exceeding the toughest requirements

With PRE balanced between the ferrite and austenite phase, corrosion resistance is equal throughout the microstructure of SAF 2205™+.
Products Profile
Sandvik Materials Technology is a world-leading supplier and manufacturer of advanced seamless stainless steels and special alloys for demanding environments. Established in 1862, nearly 160 years ago, its global operations have utilised product innovation, technology leadership and sustainable operations to set the industry standard in the 160 countries in which it operates.
Sandvik offers a wide range of highly engineered material solutions and services that make industrial processes more efficient, profitable, and safer for the automotive, aerospace, oil and gas, petrochemical, pharmaceutical, renewable energy, medical devices, and industrial industries. The high-performance tube and pipe (heat exchanger tube, high temperature tube and hydraulic and instrumentation tube), bar, hollow bar, billets and blooms, strip steel, and more combat common metallurgical challenges.
Sandvik’s new SAF 2205™+ grade of stainless steel bar is adapted to meet oil and gas end-users’ demands. As a super-clean material with enhanced pitting corrosion resistance, it has great mechanical properties and better weldability, explains Marcus.
“Specifications in the oil and gas industry have become increasingly stringent since the Deep Water Horizon disaster in 2008. A major shift took place in 2018 with the introduction of ISO17781, IOGP S-563, and in 2021 the latest revision of NORSOK M630. We also saw that the major oil and gas companies were increasing their specifications beyond NORSOK. Common denominators included an increase of the impact strength values, improved corrosion resistance, and a preference for additional testing such as the austenite spacing.”
“The development of SAF 2205™+ incorporates the new standards while also surpassing the strictest end-user specifications. The SAF 2205™+ bar is optimised to withstand extreme corrosion and is certified for the very latest subsea requirements.” “The new material was designed from the ground up”, continues Marcus.
“Impurities in the raw materials were decreased, particularly phosphorous and sulphur, to create a material resistant to pitting and crevice corrosion. The grade is also PRE balanced between the ferrite and austenite phase so that the corrosion resistance is equal throughout the microstructure. This means that there are no weak links in the chain when it comes to corrosion resistance.”
In terms of weldability SAF 2205™+ performs even better than Sanmac® 2205, due to the material’s purity. “End-user specifications increasingly include a demand for a high reduction ratio, so we designed the product routes to incorporate that. The new grade has a minimum 4 to 1 reduction ratio for all sizes from 75 to 260mm.”
The Sandvik team expects to increase the SAF 2205™+ product range within a short time frame. “While we are currently selling bars up to 260mm, the outcomes of the impact testing show that SAF 2205™+ has values which are 50% better than normal duplex grades. Therefore, we plan to increase the product range up to 300mm or even 400 mm if possible, to meet market demand.
Distributors and suppliers
Because SAF 2205™+ fulfils the latest industry standards and complies to the most stringent end-user specifications, the grade offers enormous advantages for distributors and customers in the pump and valve industry, explains Marcus. “By including extra tests not required by the standards, such as ultrasonic and austenite spacing tests, they only need this one material on the shelf. It’s a one-stop-shop for preengineered oil and gas items.
Distributors no longer have to waste time upgrading material or arranging local testing: it’s already approved and ready to be used from stock.
This is particularly advantageous for the pump and valve industries who often make one-off products. Having a material on hand that complies to the major end-user specifications allows you to minimise storage space and save weeks in production.”
“Feedback from the pump and valve industry confirms that they are happy to have a material that is ideally suited for their projects and saves them hours of looking at specifications, talking to distributors etc.”
Testing exceeds standards
To future-proof SAF 2205™+ against further revisions of end-user specifications, Sandvik carries out a range of tests on the material before delivery, including:
- Measuring of austenite spacing for material sizes from 50 mm and above, according to DNV RP F112, to verify the fine-grained structure,
- Extended hardness test close to surface,
- Ultrasonic testing according to ASTM, EN and API 6A standards.
“In addition to a 3.1 certificate, we provide microscopic images, test results from all additional tests and full documentation of heat treatment and ultrasonic testing,” continues Marcus.
“An extra microscopic examination ensures that the microstructure is homogenous from the surface to the centre. Any problems with the microstructure in a bar material can usually be found in the centre. For example, if the quenching of the bar is insufficient, sigma-phase and chi-phase will form in that area, compromising both the mechanical and corrosion properties. Sandvik is the only manufacturer that performs this extra test.”
Austenite spacing and ultrasonic testing ensure a fine microstructure of the material and that it does not have any inclusions. “Usually, it’s up to the valve or pump component producers to carry out ultrasonic testing, but we do it to save our customers time and money. It’s an assurance to our customers that there are no hidden impurities that will affect the final component.”
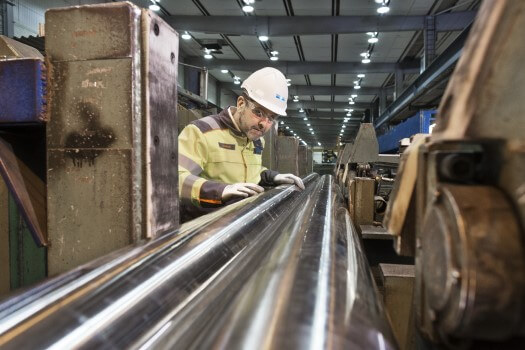
Visual inspection and marking for identification are carried out on every bar.

Submitting materials to rigorous testing before dispatch saves customers
time and money, and will eventually streamline the supply chain.
New bar materials to follow
“There is a growing demand for more durable and sustainable bar materials in the general engineering industry” continues Marcus. “We’ve seen strong growth in the sales of duplex and super duplex in recent years, not only in oil and gas applications but also in other business segments.
Looking ahead, we believe that the market for bar stock products will continue to grow. This year we will extend our portfolio and begin selling bar stock material in nickel-base grades; the first to be launched in the spring of 2021 is Sanicro® 825. This will be followed by the introduction of Sanicro® 625, -925 and finally -718.”
Join Sandvik webinars
The global Sandvik webinar program, set to run through 2021, covers various topics ranging from solving corrosion issues to material selection challenges. Webinar hosts share materials expertise knowledge and discuss the issues users regularly face, while providing insights into choosing the right material for demanding projects to fulfil productivity and performance expectations.
Visit the technical centre on the Sandvik website for additional details, to register for upcoming webinars or request access to ondemand videos.
About this Featured Story
This Featured Story is an abstract of the 4 page Featured Story in our Stainless Steel Magazine. To read the full Featured Story and many more articles, subscribe to our print magazine.
“Every two weeks we share a new Featured Story with our Stainless Steel community. Here you can find here the online abstract, and you can access the full story in our print magazine. Join us and let’s share your Featured Story on Stainless Steel World online and in print.”
– FEATURED STORY BY JOANNE MCINTYRE
All images were taken before the COVID-19 pandemic, or in compliance with social distancing.
Read the full article.