Story by: James Chater Photo: Siemens
Until quite recently, materials development was often thought to be a mature discipline. When it came to increasing heat or corrosion resistance, it seems that researchers were approaching the limits of what was possible. No longer! Thanks to new manufacturing techniques, artificial intelligence (AI), multidisciplinary approaches and collaboration across a range of companies and scientific institutes, new possibilities are opening up at an exhilarating pace. This article attempts to give some indication of what is out there in terms of new research tools and new grades.
New industrial revolution
In the past, the stainless-steel and CRA industry was often seen as conservative: end-users, especially in the oil & gas, construction and nuclear industries, tended to stick with what was tried-and-tested and familiar, not wishing to risk safety with relatively unproven materials. Occasionally a better austenitic presented itself, or an austenitic grade was replaced by a duplex one, once the different welding procedures were understood. Moreover, new grades take time to develop, and seeking approvals is a lengthy and arduous process.
In recent years, however, this relatively staid approach has been shaken up by a number of factors: there have been significant collaborations to improve safety and quality and reduce ecological footprint without increasing costs; also, new inroads have been made by new manufacturing techniques such as 3D printing and by the digital revolution in general, and especially in Artificial Intelligence. Furthermore, the cut-throat global market makes it less and less easy to ignore innovation.
Collaboration
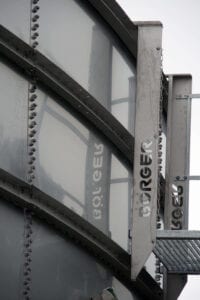
Cost-cutting (achieving equal or greater quality at lower cost) has been the main driver in alloy innovation. For example, low-nickel and zero-nickel alloys avoid exposure to high nickel prices, and duplex grades reduce the use of certain high-cost alloying elements. Other grades were developed to fill gaps, i.e., to obviate the need to over-specify. Others still meet the need to withstand severe conditions in a particular application. Alloy research is an important part of a metal company’s R&D. Rarely however, does this occur in isolation. For example, to develop its urea duplex grade Safurex® (SAF 2906™), Sandvik teamed up with fertilizer technology provider Stamicarbon. Industeel also developed urea grades in collaboration with end-users. In another example, Posco developed high-manganese steel for LNG applications, then teamed up with Exxon’s research institutions to develop the technology further.
But perhaps the greatest contributions to alloy research have come from science institutions (in the USA, these institutions are often linked to the military or the energy industries) and from universities, often in collaboration with companies. Universities have spear-headed research in such areas as high entropy alloys (HEAs) and magnesium alloys (used in Mg ion batteries and hydrogen storage).
Did you know?
■ The first alloy was developed over 5,000 years ago: it was bronze, which is copper alloyed with a small amount of tin. So began the Bronze Age, which came between the Stone Age and the Iron Age.
■ It has been estimated that HEAs can give over 592 billion new CCA (concentrated complex alloy) bases with between three and six principal elements (1). Best get cracking!
Deep learning

Computational alloy design is a rapidly growing field. AI, machine learning and deep knowledge allow computers to ‘predict’ viable alloys without going through the trial and error of physical experiments. One of the companies leading the way in this field is Intellegens, which used its algorithm to develop a new Ni alloy for direct laser deposition in 3D printing, thereby saving an estimated 15 years of research and 10 million USD in R&D costs.
The same company is collaborating with Boeing to accelerate product development on aircraft parts by using machine learning to optimize additive manufacturing (AM) for new metal alloys. Intellegens also worked with GKN to develop a Ti alloy with improved thermal conductivity for use in the 3D printing of aircraft heat exchangers.
3D printing
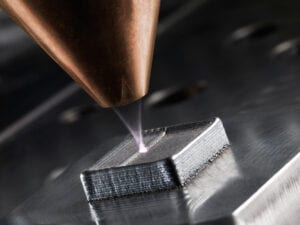
The 3D printing process has opened up the possibility to use metal powders with enhanced properties (especially strength and work hardenability) to make complex components at a much
lower cost. The new technology is driving the development of a vast array of new materials, ranging from polymers to Al alloys, ceramics, Ni and Ti alloys, graphene and so-called 4D materials, which are 3D-printed and change shape as they are heated or cooled. One such Ni alloy is EOS’s NickelAlloy HX, a heat-resistant alloy used in Siemens gas turbines. Milder grades are also being developed for 3D printing, for example DEW’s austenitic Printdur HSA, a nickel-free metal power which is stronger and harder than 316L. 3D printing of titanium alloys has been enhanced by the addition of copper to produce stronger Ti alloys than those used in traditional manufacture.
New From India India has a thriving 3D industry, worth around 71 million USD and serving such markets as aerospace, auto, engineering and medical equipment. However, it is only recently that the country has started to produce metal 3D printers of its own. The first two examples are based on powder metallurgy. In late 2019 Wipro, partnered by the Indian Institution of Science, launched a metal 3D printer based on selective electron beam melting technology. A month later Intech Additive Solutions launched its iFusion printer, which uses Selective Laser Melting technology and is available in two formats, the smaller designed for laboratories and universities, the larger for factories. the addition of copper to produce stronger Ti alloys than those used in traditional manufacture.
New grades
Apart from the grades already mentioned, we can here summarize some important innovations in recent years:
Martensitics
Corrodur 18, from DEW together with Schaeffler AG, is a nitrogen martensitic stainless steel for bearing applications. It has high hardness combined with good impact-bending energy and good corrosion properties.
Ferritics
The demand for ferritics in auto exhaust systems has been rising. Outokumpu developed a high-chromium ferritic grade, Core 4622 (EN 1.4622), suitable for façades, elevators catering and the automotive industry.
Austenitics
Tsingshan has developed QN1803/304D, based on type 304 but with less nickel and more nitrogen and copper. Outokumpu’s Supra 316plus has higher nitrogen content, 21% Cr and lower
Ni and Mo. It has better mechanical strength and higher corrosion resistance than standard Cr-Ni-Mo austenitic grades. It can be used for containers of corrosive liquids, architecture and several process applications.
Posco has developed PossFD, a very soft, easily formable austenitic to replace copper in refrigerant piping.
Super-austenitics
Sandvik has developed Sanicro® 35 to bridge gaps between stainless steels and nickel alloys. It combines the corrosion resistance of hyperduplex grades with the heat resistance of other super-austenitics. It is a suitable for heat exchangers in several industries.exchangers in several industries.

Duplex This group of materials has been gaining favour as an alternative to various austenitic grades at limited temperatures. Recent years have seen a great expansion in the choice of both lean and superduplex/hyperduplex grades. Lean grades fill the need for low-nickel grades in structural, load-bearing applications where corrosion is mild. Allegheny supplied its ATI 2003™ from the largest stainless-steel roof in the world, at a new airport in Doha, Qatar. Later, Outokumpu launched LDX 2101® (Forta LDX 2101), ideal for process pipes, hollow sections and structural tubes. Then came the same company’s LDX 2404® (Forta LDX 2404), used in storage tanks, flanges, valves, flood & sluice gates, among others, and also suitable for some applications in pulp & paper, bioenergy, biofuel and biomass conversion.
Outokumpu’s success prompted NSSC to come up with NSSC 2120® as an alternative for type 304 in the cargo tanks of chemical tankers and in other structural applications. In 2019 NSSC launched an upgrade, 2351, which can serve as an alternative to both 304 and 316 in brackish water and tanks and containers in the food and pharmaceutical industries.
NSSC paid great attention to ease of welding, and Outokumpu responded with its Forta FDX 25 and Forta FDX 27 grades, designed for better formability. Both grades are suitable for plate heat exchangers, pump components, flanges and valves, the second being more corrosion-resistant than the first. During roughly the same period, Sandvik produced super- and hyper duplex grades to increase corrosion resistance and avoid stress corrosion cracking in the ever-sourer conditions of deep-sea oil and gas installations. SAF 2507 super duplex was developed to resist extreme corrosion combined with high stresses in chloride environments like seawater, with high added chromium, molybdenum and nitrogen. SAF 2707 went further, adding more alloying elements for even more acidic conditions.
Other super alloys
Apart from the nickel/titanium alloys mentioned so far, developed for
3D printing and mainly used in the aerospace industry and in prosthetic devices, there is a class of specialized materials designed to provide extra corrosion or extra strength in very specific conditions. A super-hard material was designed by Arizona State University and the Army Research Laboratory, an alloy of copper and tantalum that can withstand extreme impact and temperature, making it ideal for ballistic protection applications for armed forces.
High entropy alloys
Finally, an important development has been the focus on high entropy alloys (HEAs), a group that has been around for some time but that has attracted greater attention only recently, thanks largely to their potential in 3D printing, and to the fact that AI has accelerated their development. (Also, up to now they have been expensive to produce, though efforts are being made to reduce costs.) Unlike alloys in the past, in which a base element (usually steel) is alloyed with smaller proportions of other materials, HEAs normally consist (depending on how you define them) of between three and five elements combined in equal or near-equal proportion per atomic weight. (It is this equality in the proportions that increases the materials’ entropy.) It has been found that some of these alloys have higher strength-to-weight ratios, fracture resistance and tensile strength, as well as greater corrosion and oxidation resistance than conventional alloys.

Examples of HEAs include:
• VNbMoTaW – combining a high yield strength even at a temperature of 1,400 °C, outperforming superalloys such as Inconel 718;
• CoCrFeMnNi – the first HEA with a single FCC solid solution phase in the as-cast state. It combines low-temperature mechanical properties with high fracture toughness, good ductility and yield strength at low temperatures;
• Al0.5CoCrCuFeNi – has a high fatigue life and endurance limit, possibly exceeding some conventional Fe and Ti alloys.
Most of these materials are still at the testing stage, with AI-assisted research underway at such institutes as Pohang University of Science & Technology (POSTECH) in South Korea, the Max Planck Institute in Germany and NETL in the USA.
They could be used in a wide range of applications: cryogenic (refrigeration, LNG storage), high-temperature environments (gas turbine engines, jet engines), hydrogen storage tanks, radiation resistance, electronics, electromagnetic shielding, coatings, and anti-bacterial materials. HEAs, with their extraordinary properties, are thus a credible alternative to many Ti and Ni alloys.

Conclusion
Thanks to recent advances in manufacturing technology and IT, a brave new world of alloy R&D is round the corner. This new cycle is an integral part of what has been called the second industrial revolution (based on information technology), and it has only just begun. Seemingly infinite possibilities lie ahead, with many new, viable alloys still awaiting development. Roll over, bronze!
References
https://www.nature.com/articles/s41467-019-09700-1
Every week we share a new Featured Story with our Stainless Steel community. Here you are provided with an online abstract, the full story features in our print and digital magazine. Join us and let’s share your Featured Story on Stainless Steel World online and in print.”
Featured Story by: James Chater
All images were taken before the COVID-19 pandemic, or in compliance with social distancing.