Q: I work for a company welding pipeline for the oil and gas segment. On a fairly regular basis, we have difficulty achieving the required ASTM G48 corrosion test requirements of 40°C when welding super duplex stainless steel. We use an SFA/AWS A5.9 ER2594 super duplex filler metal, and we have less than 50% pass rate at 40°C. Do you have any suggestions please?
Column by Peter Stones, ESAB
A: There are a number of suggestions, and they fall into two categories. The first is modifications to the welding process and the filler metal selection, and the second is to improve the test piece preparation.
I will assume that the welder is sticking closely to the welding parameters, that the heat input and interpass temperatures are kept to a minimum, that maximum heat input < 1.5kJ/mm and the maximum interpass temperature <150°C. The importance of these numbers cannot be stressed enough with super duplex, as the high chromium (25%) and nickel (10%) content will start precipitation of intermetallic phases in a matter of minutes if the temperature is exceeded. These parameters are relevant to both GMAW and GTAW processes. Sigma phase ferrite that has been precipitated in the microstructure will seriously reduce the corrosion resistance of the weld. The ferrite acts as microscopic pockets of weakness because the structure is ferrite in these areas and is no longer a duplex mix of austenite and ferrite with all the inherent mechanical strength and corrosion resistance.
If the welding is not an issue, then I would recommend using a super duplex filler metal with a high PRE (pitting resistance equivalent) number. Each manufacturer should be able to supply you with a PRE number for their products, and in any event, the number can be calculated from the composition supplied on the datasheet using the formula:
Pitting Resistance Equivalent
(PRE) = %Cr + 3.3x%Mo + 16x%N
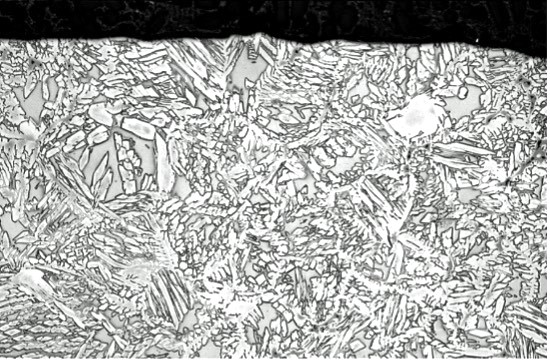


Remember to use the minimum percentages in the formula as a worst-case scenario. ASME Section II Part C has a minimum requirement of 40 for the PRE for the super duplex grade. However, there are products on the market with a PRE = 42.5, so using one of these would give you a little advantage. If permitted within the client’s specification, another solution would be to overmatch the filler metal and use a hyper duplex grade. This grade has a PRE = 49, and G48 corrosion tests have been achieved in excess of 60°C.
The preparation of the test piece after welding is also crucial to the corrosion resistance. Very basic procedures such as removing any sharp corners (and indeed machining them smooth) will make a big difference; again, check whether it is permitted within the client specification.
The following graph illustrates the efficiency of different post-weld cleaning processes on the pitting potential of the weld. The more highly that you can polish the test piece, the higher the ASTM G48 temperature it will be able to achieve. The best results will be obtained with pickling. In the oil and gas sector, the requirements for the ASTM G48 corrosion test temperature for super duplex changed about ten years ago. Prior to that, the requirement was for 30°C and was not really an issue. The increase to 40°C is still causing some issues, as you are experiencing, but it is quite achievable. Please feel free to contact me for a more detailed discussion.
Meet the columnist
Peter Stones IEng MWeldI IWE/EWE
As part of the ESAB Specialty Alloys Group, Peter is technical support for stainless and nickel alloy filler metals. Peter is actively involved with TWI and is a non-executive director of The Welding Institute. Peter worked for Sandvik for ten years and was Global Product Manager for Sandvik Welding until 2018 when ESAB purchased the filler metals business. Email: peter.stones@esab.com
Every week we share a new Featured Story with our Stainless Steel community. Join us and let’s share your Featured Story on Stainless Steel World online and in print.