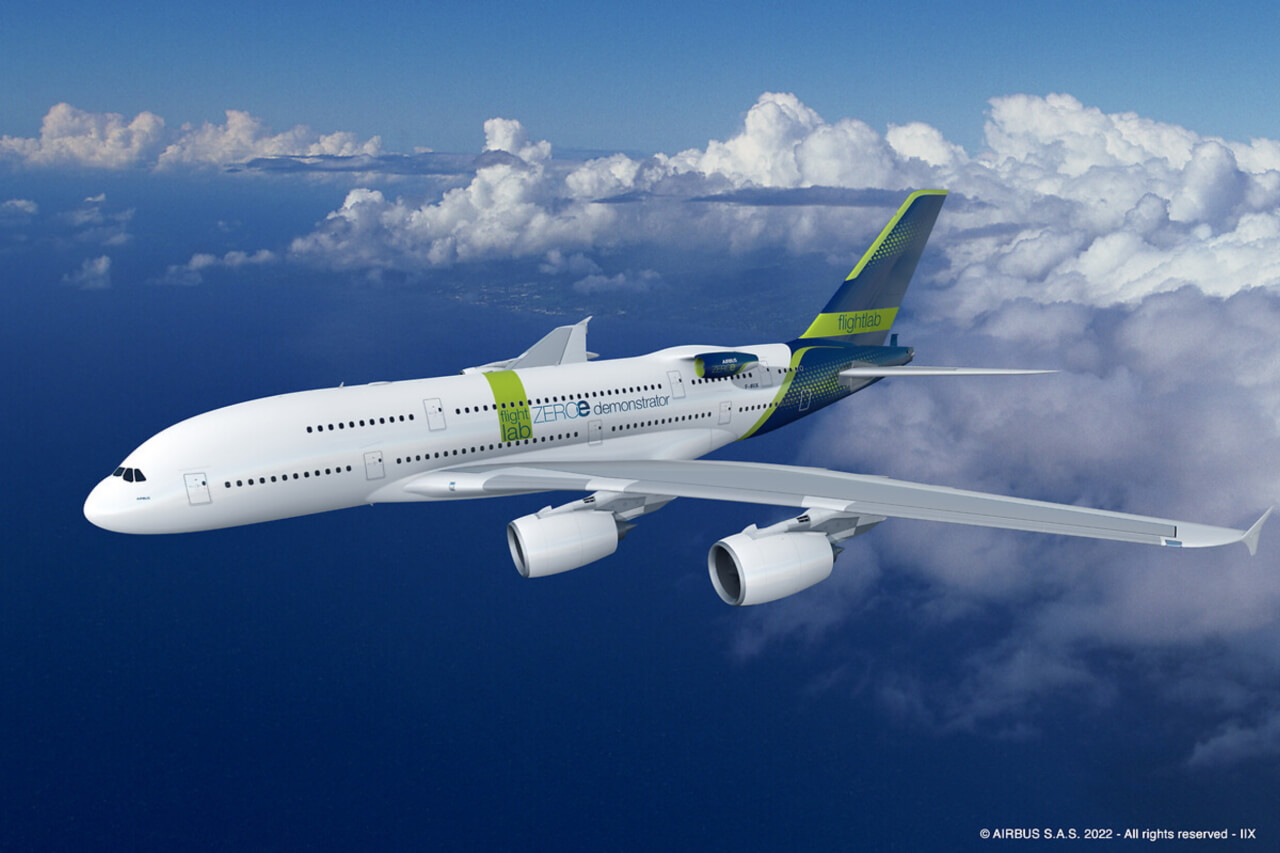
The Airbus A380 flight test platform will put hydrogen combustion technology to the test. © AIRBUS S.A.S. 2022
First Covid 19, now war in Ukraine: these have been unsettling times for the aerospace industry. Not only has commerce with Russia ground to a halt, but a question mark hangs over future titanium supply. With fossil fuels now more expensive, the search for carbon-free alternatives is likely to accelerate.
By James Chater
Supply uncertainty
Are we seeing the end of globalisation? Even before the war in Ukraine, supply chains were stretched, causing inflation. In last month’s issue, we saw how the war was affecting natural gas – it is having a similar effect on aerospace. Trade with Russia is likely to be disrupted for some time. Its aviation sector has been ostracised and is likely to collapse. For the rest of the world, the main problem is aerospace’s reliance on Russia’s titanium processing capacity. A shortage of titanium will lead to a shortage of parts, which will lead to higher prices and delays. Since 2014 Boeing has diversified away from Russian sources and has paused all buying from this country. Airbus, however, is more dependent on supplies from Russia and could be in difficulties if sanctions are imposed on Russian titanium.
Aircraft
The last few decades have seen a drive towards lighter, more fuelefficient designs. In aircraft bodies, composites have replaced aluminium, and titanium is the preferred metal for fasteners because it is compatible with composites. In engines too, higher temperatures have necessitated the use of titanium.

Among the larger aircraft being developed today, the Boeing 777X is the latest example of this trend. This successor to the Boeing 747 is a longrange, wide-body, twin-engine aircraft that was to have appeared in 2020, but because of the Covid pandemic it is now scheduled to appear later this year. Its engine promises to deliver 10% lower fuel use than the competition. The GE9X, developed by CFM (a joint venture of GE Aviation and Safran) is the world’s largest commercial jet engine, with 3D-printed titanium nozzles that optimise the exhaust flow.
In the midsize, twin-aisle range, Boeing is developing an aircraft due to enter service in the late 2020s. Variously known as the 797 or the New Midsize Airplane (NMA), it will be equipped with a new turbofan.

The narrow-body market is dominated by the Airbus A320neo and Boeing 737 MAX families. Both use CFM LEAP-1A engines, while A320new also uses the Pratt & Whitney PW1000G.
Both are likely to be replaced by an open-bladed jet engine that will contain metal 3D-printed parts. The RISE (Revolutionary Innovation for Sustainable Engines) is intended to reduce fuel consumption by up to 20% compared to predecessors and is expected to launch in the mid- 2030s. The design foresees the use of composite fan blades, heat-resistant metal alloys and ceramic matrix composites (CMC).
New to the A320 family is the A321 (extra long range), a variant of the A321LR. Launched in 2019, it will enter service in 2023. It will have the longest range of any single-aisle airplane.
Heavier than the other members of the A320 family, it will require more powerful engines and stronger landing gear, though specific details are not available.

3D printed bracket installed on the pylon of the Airbus A350 XWB. Photo: Frédéric Lancelot – Master Films.
Aircraft of the future
After these models have been rolled out, we are likely to see far-reaching changes in the design and appearance of aircraft. Several companies are developing a “Flying-V” or “blendedwing” aircraft, in which the passenger seating, fuel tanks and baggage hold are built into the wings. These are fuel-efficient alternatives to jumbo-jets, though given the fate of the A380 their commercial success seems far from assured.

Supersonic flight is making a comeback and is likely to be succeeded by hypersonic flight. Boom, based in Denver, Colorado, is expected to produce Overture, the first civilian supersonic jet since Concorde, in about 2026. With their X-59, NASA and Lockheed Martin want to build a supersonic plane that does not produce a sonic boom. Then there are rocket-plane hybrids that will fly at several times the speed of sound: China is said to be developing a Mach16 jet that can fly from China to New York in one hour. First flight is expected in 2024. SABRE is developing a rocket plane, fuelled by hydrogen and oxygen, that can fly at Mach 5.4 in the atmosphere or Mach 25 in space.
Commercial flights are slated for the 2030s. A step further is the oblique wave detonation engine, which uses controlled explosions rather than combustion to propel a rocket. The University of Central Florida has demonstrated a prototype and will test a rocket launch by around 2025.
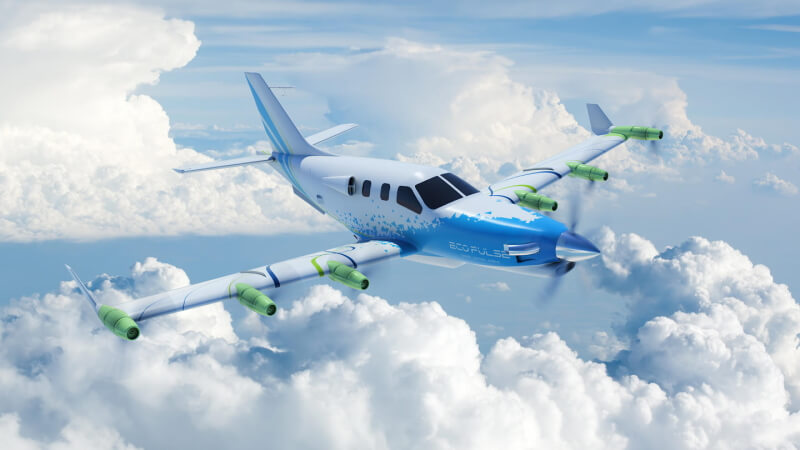
The EcoPulse distributed propulsion hybrid aircraft demonstrator is being developed by Daher, Safran and Airbus with the support of France’s CORAC civil aviation research council.
Low- and zero-carbon fuels
Most aircraft still rely on kerosene, a petroleum derivative, but with surging oil prices and emissions both hot-button subjects, this is about to change. Electrical propulsion is already a reality for city aircraft and “air taxis”. For larger aircraft, other solutions are necessary – at least, until superconducting technologies can increase power density. SAF (sustainable aviation fuel) is already an area of intense research and testing. This usually takes the form of biofuel, which is derived from such substances as organic waste orcooking oil. Airbus has already tested a combination of kerosene and biofuel on the A380, A350 and A319neo.
It has ambitious plans to transition to 100% biofuel. British Airways, in collaboration with Phillips 66 and engine manufacturer Rolls-Royce, are also carrying out tests. In Turkey, a refinery powered by wind energy is turning algae into jet fuels.

Also being tested are hydrogen and processes to reverse-engineer carbon dioxide into jet fuel. Hydrogen can either be run through fuel cells in a chemical reaction to produce electricity or (in big planes) can be combusted directly. Airbus is testing both technologies.
Hydrogen is bulky, and much space can be gained by liquefying it. This cryogenic process (H has a boiling point of -235°C) is being developed by Airbus, which is designing liquid hydrogen tanks that will be made of a metallic substance or a composite.
And finally, jet fuel from thin air! There are various methods of turning CO2 into fuel. A group of Oxford scientists have invented a way of capturing CO2 from the air and turning it into jet fuel using an iron-based catalyst and hydrogen. NASA has developed a technology that can convert CO2 into fuel by using solar-powered, thin-film devices, using sunlight and titanium dioxide composites to perform the reaction. And Californiabased Emerging Fuels Technology (EFT) has produced jet fuel from carbon dioxide using an electrochemical process.
Conclusion
The titanium supply situation depends on how long the war lasts and how much it will damage the world economy. In 2021 Boeing predicted GDP growth of 2.5% per year until 2039, led by narrowbody aircraft working the domestic and short-haul routes, followed by widebody airplanes on the long-haul routes.
The war is likely to put a dent in this and trigger an increase in the share of military compared to civil aircraft. For security reasons, there is an urgent need to increase titanium processing capacity outside Russia.
Did you know?
– Titanium use in aircraft was pioneered by the US SR-71 spy plane. During the Cold War, Lockheed sourced a lot of its titanium from the Soviet Union through several intermediary companies to cover their tracks. This time round, aircraft builders may face difficulties procuring their titanium products.
– Having been unable to sell enough of its A380 jumbo aircraft, Airbus has decided to auction off its parts. If you want a souvenir of this aircraft, keep the dates 23-25 June free!
– By using 3D printing to produce parts for its 787s, Boeing expects to save approximately 2 to 3 million USD per plane (www.ge.com).