Q: We fabricate items in 316L, 304L and duplex grades. Can you explain what causes heat tint in stainless and the best method for getting rid of it? Occasionally we see evidence of rust spots on the surface of some stainless items, so we suspect the quality of the base material, but the certificates indicate that it is to specification. What do you suggest?
A: The thing that makes stainless steel stainless is that it contains more than 12% chromium. In 1913, Harry Brearley of Sheffield, UK, was the first person to find a way to add chromium into molten iron and produce “rustless” steel. The chromium oxidises in air to produce a very thin layer of chromium oxide, which is very passive and gives the surface its corrosion resistance. Even if the layer gets damaged, the chromium oxide layer will reform once the steel is exposed to air. When the passive layer is damaged and the surface is in a non-oxygen-containing environment (for example under water), various methods of corrosion occur in stainless steels.
Causes of damage
Common causes of damage to the passive chromium oxide layer include weld defects such as porosity and arc strikes outside of the weld groove. (Note that such arc strikes are typically grounds to reject a weld). Spatter can also damage the chromium layer, which is why it should be removed (and also why low-spatter filler metals and processes are important).
Iron contamination due to mixing tools used on carbon steel and stainless steel is another issue.
Due to humidity, ferrous particles on the surface of the stainless steel corrode and rust. This could be one of the causes of the appearance of ‘rust spots’ mentioned in the initial enquiry. Note that rough surfaces due to uneven weld beads or grinding marks collect deposits more easily and increase the risk of corrosion.
Excessive heat tint is also an issue. This occurs when the natural oxide layer on the surface of stainless steels thickens due to heating and being exposed to air during welding.
The colours produced are similar to temper colours and are created by a light-interference effect. Generally, the darker the colour, the thicker the chromium oxide layer, but what also needs to be considered is that chromium that has migrated from the surface of the base metal has depleted this area of chromium. To ensure that the corrosion resistance properties of the welded material are brought back to the same level as the unwelded base metal, the heat tint and the chromium depleted layer underneath both need removal.
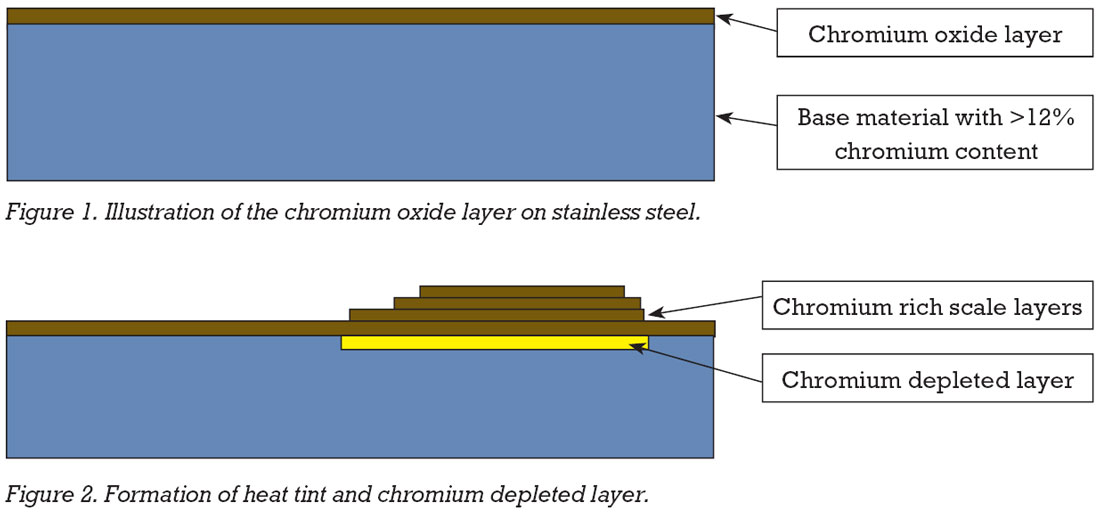
Post-weld cleaning methods
Choosing the proper post-weld cleaning method can address the causes of rust spots. Some of the options are:
• Chemical pickling, which uses a mix of nitric and hydrofluoric acid in paste or liquid forms, removes the surface of any area to which it is applied. It will remove the chromium scale heat tint and the chromium depleted layer underneath.
• Chemical passivation uses a strong oxidising agent, such as concentrated hydrochloric acid, to replace the passive chromium oxide layer.
• Electropolishing does not selectively remove chromium scale; rather, it polishes ‘microtips’ from the whole surface using a direct current and an electrolyte such as sulphuric acid.
• Mechanical methods such as grinding and polishing will remove any surface defect, but it is important not to leave a rough surface and not to contaminate stainless steels with iron oxides from low alloy steels. Shot blasting and wire brushing are other mechanical methods that are employed.
With reference to Figure 3, this illustrates the effectiveness of the different cleaning methods on the pitting corrosion resistance of stainless steel. This shows that grinding at “5” is three times more effective than wire brushing at “6” and that the most effective method is pickling.
Consider the following as a best-practice sequence. Start by mechanical polishing to a high level and follow with chemical pickling to remove the chromium scale and the chromium depleted layer. Finish by applying a passivation agent to restore the chromium oxide layer for optimum corrosion resistance.
Please appreciate that this is only a summary on this topic, and feel free to email me if you would like more information.
Meet the columnist
Peter Stones – IEng MWeldI IWE/EWE
As part of the ESAB Specialty Alloys Group, Peter is technical support for stainless and nickel alloy filler metals. Peter is actively involved with TWI and is a non-executive director of The Welding Institute. Peter worked for Sandvik for 10 years and was Global Product Manager for Sandvik Welding up to 2018, when ESAB purchased the filler metals business.
Email: peter.stones@esab.com