As technology advances, 3D-printed metal structures have found their way into the industry. Not only do they have their use in highly technical applications; sometimes these structures can take the shape of beautiful art.
By Karlee Williston, IMOA
Most 3D-printed objects are less than 30cm long. So, how is the 10m long Oregon Dragon Bench possible? Instead of using powder, the bench was built layer by layer applying a robotic welding technology called “WAAM”. Made with 2209 duplex stainless steel weld wire, the Oregon Dragon Bench exemplifies how 3D-printed metal structures can do more with less.
WAAM

Take a rest on the serpentine Oregon Dragon Bench at the Nike Headquarters, but don’t be surprised if you want to get up and move. The bench’s textured, perforated surface pattern evokes the flexible fabric and lightness of athletic sneakers. The ridges are not only stylistic but also hint at how the bench was made: by layering melted metal wire. Wire Arc Additive Manufacturing (WAAM) works similarly to powder-based additive manufacturing (AM), which makes up the bulk of 3D metal printed objects and structures. But unlike powder AM, which is restricted to the size of the printing unit, WAAM structures are built without these limitations by a welding robot in an open or enclosed space.
Dutch designer Joris Laarman developed the technology less than a decade ago, and it’s quickly catching on. In 2021, the spin-off company dedicated to robotic WAAM, MX3D, installed the world’s first 3D-printed stainless steel footbridge in Amsterdam. Robotic WAAM also produces structures less expensively and faster than powder AM, largely because welding wire costs a fraction of metal powders and the deposit rates of welding are much higher.
Preventing corrosion
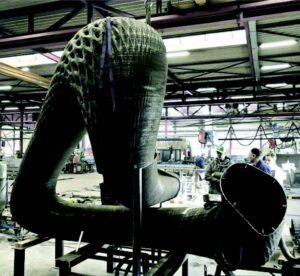
One consideration for the future of 3D printed stainless steel structures is the rougher surface finish produced layer by layer. The small crevices between each layer can be hotspots for corrosion, and thus the process favours selecting more corrosion resistant grades like molybdenum containing duplex stainless steels. The Oregon Dragon Bench has the potential for salt, dirt, and pollution to accumulate in its many tiny ridges, so the 3% molybdenum in 2209 duplex stainless steel helps resist these additional corrosion risks. 3D printing will be increasingly important to modern economies worldwide. The undulating Oregon Dragon Bench helps explain why: 3D printing allows for fantastic shapes not possible with traditional manufacturing. Importantly, the greater range and complexity of possible designs applies to industrial applications, including oil and gas and maritime, where molybdenum-containing stainless steels are already standard.
About IMOA
Reproduced with the kind permission of the International Molybdenum Association (IMOA). IMOA is a non-profit trade association representing the majority of the molybdenum industry worldwide. For information, visit www.imoa.info
About this Featured Story
This Featured Story appeared in Stainless Steel World April 2023 magazine. To read many more articles like these on an (almost) monthly basis, subscribe to our magazine (available in print and digital format – SUBSCRIPTIONS TO OUR DIGITAL VERSION ARE NOW FREE) .
Want to contribute as author? Please contact Joanne.
Every week we share a new Featured Story with our Stainless Steel community. Join us and let’s share your Featured Story on Stainless Steel World online and in print.