Figure 1. Field welding and installation of 24” DSS line pipe.
A large gas production pipeline project in the Sultanate of Oman utilised duplex stainless steel for its superior corrosion resistance and mechanical strength. This article discusses procurement and construction challenges and the best practices developed to overcome these challenges.
By Dr JR Saithala, M Ghafri, P Manivannan, H Barve, I Tobi, & A Kharusi, Petroleum Development Oman
Duplex stainless steel (DSS) UNS S31803 grade material was selected for this gas production pipeline project due to its high corrosion resistance and mechanical strength, which are crucial for operations at high temperatures (>100°C) and pressures (>100 bar). The project involved the installation of 120km of DSS line pipe in various sizes, including 8-inch, 16-inch, and 24-inch lines, with wall thicknesses ranging from 5.4mm to 15.5mm. The 16-inch (30 km) and 8-inch (51km) lines were commonly used for gas production flowlines and manifolds, with wall thicknesses of 10.5mm and 5.6mm, respectively. The project’s main 24-inch pipeline, which is 34 km in length, marked the first time in Petroleum Development Oman’s history that a DSS pipeline of this size, in terms of outside diameter (OD) and wall thickness (WT), was designed, procured, constructed, and installed. The 24-inch line pipe is coated and buried to ensure its external corrosion protection.
The thickness of the line pipes was driven by hoop stress, which is the stress caused by the internal pressure acting on the pipe walls. On the other hand, the pipeline size was based on hydraulics and flow rates, which determined the necessary diameter to transport the required volume of gas. Best practices in line pipe manufacturing and site construction were implemented to ensure the successful fabrication of DSS materials in the oil and gas industry.
In this article, we will talk about the challenges faced during the procurement and construction of a line pipe project in Oman, as well as the best practices that were implemented to overcome these challenges. Despite the obstacles that arose, the project was completed ahead of schedule, thanks to these practices. This allowed for early installation and commissioning of the pipeline, which was a significant achievement given the difficulties encountered during the project.
Procurement challenges
This project required a material that could withstand the corrosive process conditions for a design life of 25 years. While several options were considered, such as carbon steel and carbon steel plus inhibition, these were deemed unacceptable due to maintenance and operational intervention requirements. DSS was chosen for its durability and minimal maintenance requirements. Large diameter and high wall thickness were selected to meet design parameters. However, large-size DSS line pipe procurement posed significant challenges as pipe manufacturers were limited. Three pipe mills participated in the bid, and each proposed different raw material forms and welding methods. As raw material in coil form posed severe challenges in pipe forming and welding for the line pipe size with 24” OD and 14.5 and 15.55mm WT, plate form was recommended. However, only a few mills offered raw materials in the plate form in compliance with the project’s technical requirements.
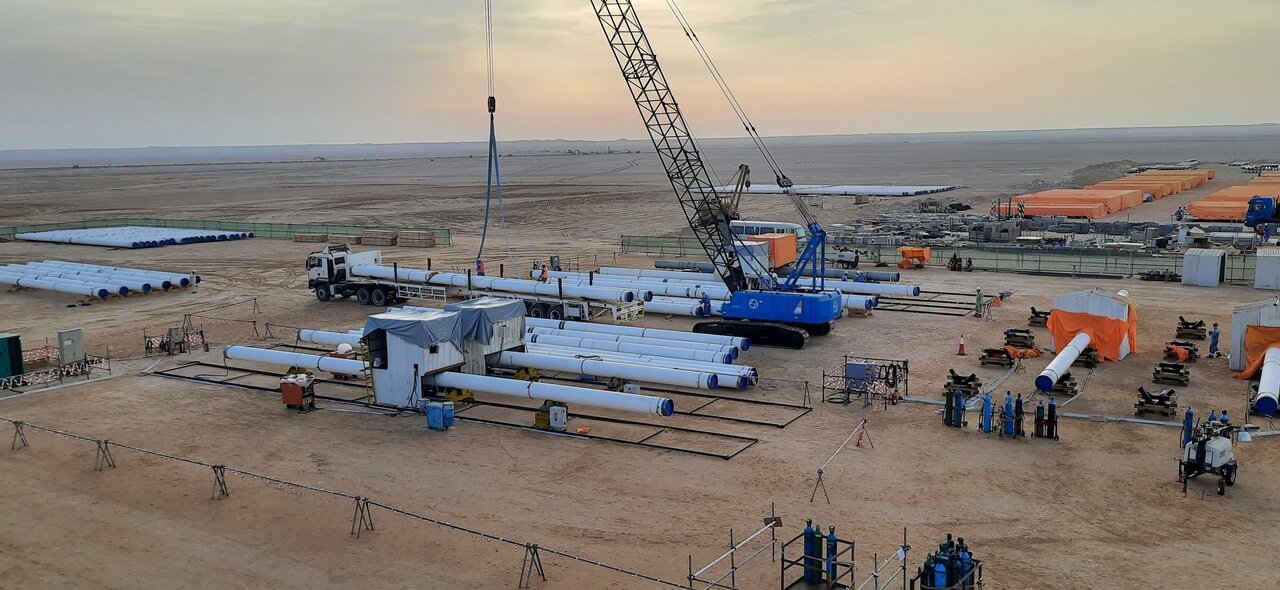
Line pipe manufacturing
With limited pipe mill participation in the bid, the technical bid evaluations from three different pipe mills were scrutinised for their capabilities, past experiences, and compliance with the stringent technical requirements. All requirements were discussed and elaborated with the chosen pipe mill to ensure compliance without any ambiguity at the ordering stage.
The manufacturing procedure, Inspection Test Plan (ITP), welding and non-destructive (NDT) procedures, and other relevant quality method statements were thoroughly reviewed. A pre-inspection meeting at the mill verified the system and methodology for the new manufacturing process of 24” pipe through plate forming, welding, and offline heat treatment and 16” & 8” pipe through coil forming, welding and online heat treatment.
Fabrication method & welding technique
To manufacture the 24” DSS line pipe, plates were examined for laminations using ultrasonic testing and joined prior to forming using submerged arc welding. Longitudinal seams were designed with a double-sided full penetration joint configuration. The long seam of the pipe was welded with filler metal in all passes, using plasma arc welding (PAW), submerged arc welding (SAW), and gas tungsten arc welding (GTAW). The welded pipes were subsequently solution annealed, meeting NORSOK conditions in an offline heat treatment furnace. Challenges encountered during manufacturing included modifying weld metal chemistry to ensure a minimum of 0.14% nitrogen and a minimum Cr and Ni content of the base material. CVN energy values were improved through different trials during the MPQT qualification. The heat treatment furnace was validated during MPQT qualification, complying with NORSOK requirements. Welding repair procedures were also qualified, meeting original weld requirements, and weldability tests were conducted following construction welding variables and testing the weldment in the as-welded condition, meeting ISO 17781 and project specifications.
The success of any project hinges on adopting best practices in the construction phases, and welding is no exception. To achieve higher pitting resistance at the root (which is exposed to the process conditions) in the as-welded condition, weld metal was designed with SDSS filler wire to meet the pitting resistance of the base material (which was solution annealed). In the field, it is a harsh environment where the mercury rises to 55°C, and the resultant ambient metal temperature of the pipe to 60°C poses high challenges to meet the inter-pass temperature requirement for welding DSS. Critical welding parameters (interpass temperature and heat input) were qualified under the worst conditions during procedure qualifications to avoid construction difficulties. Welders and welding operators were also systematically trained before deployment.
Another critical factor is the oxygen content, which must remain below 500ppm, or the value demonstrated in the welding qualification procedure to avoid oxidation. This was achieved by introducing dual inlet and high flow rates, as well as a double sealant purge dam with a dual inlet to maintain low oxygen content at the root.
High-purity shielding and purging gas (99.997%) were also applied. To ensure maximum efficiency, most of the joints were welded with an internal clamp with an integrated purge dam, including bends and tie-ins through a modified internal clamp. It’s worth noting that 24” pipe production has inside welding, which differs from 16” production with coil methodology, where the root pass is welded with autogenous welding. These best practices ensure the success of the welding process, making the project a resounding success.

Technical challenges
The construction of large-scale projects often comes with various challenges, some of which include the first-time implementation of new ISO 17781 requirements along with new company specification requirements on hot tensile tests and SCC tests on field girth welds. One of the main challenges that arise when dealing with larger diameters is maintaining oxygen content below 500ppm to avoid oxidation at the root. Stress corrosion cracking test (SCC): Strict technical requirements were specified, including four-point bend test as per NACME TM0316 for autogenous welding. SCC tests were conducted on the 16” line pipe production weldment in a third-party lab accredited by ISO 17025. The same SCC test requirements were subjected on the girth welding produced in the field, even though all passes were welded with filler metal, to evaluate the heat affected zone (HAZ) of the line pipe with autogenous weld. As the girth weld is not subjected to solution annealing, the welding parameters were tuned to ensure the girth weld and its HAZ meets the SCC test criteria of no pits.
Elevated tensile test: Performed at the design temperature, this is an important property for this line and shall meet room temperature mechanical strength requirements.
Charpy impact test: Was conducted to meet ISO 17781 Quality Level 1 requirements even though Quality level 2 is accepted for oil and gas environments. Also test temperature applied in line with ISO 17781 -46deg C, in spite of the minimum design temperature being warmer than 5deg C.
Pitting corrosion test: ASTM G48 test was conducted on the weldment in the as-welded condition without altering the root condition. No pickling was performed to simulate the production weld, and the entire thickness was subjected to test method A. The test was successful and weight loss was lesser than 4gm/m2.
Overcoming project schedule challenges
The project faced technical challenges in meeting yield strength, hot tensile, corrosion, and impact tests. COVID-19 restrictions affected raw material and product shipments, but effective remote inspections and frequent communication with suppliers and manufacturers helped maintain manufacturing quality. Deviations from specification requirements were managed through technical authority approvals. Qualifying submerged arc welding posed challenges, but optimising welding parameters improved toughness and corrosion test requirements. Double welding before transferring to the site improved productivity and helped meet project schedules.
To ensure manufacturing quality, technical alignment and pre-inspection meetings were held in the mill, and close monitoring and collaboration with vendors were established to mitigate COVID-19 restrictions. A third-party inspector was mobilised to the mill for effective monitoring and quick resolution.
Construction of this larger diameter DSS pipeline required special equipment including internal clamps, purge monitors, flow meters, boroscope inspection equipment and highly-skilled welders. The COVID-19 pandemic posed significant challenges in mobilising high-skilled welders, equipment, and tools to the construction site.
Summary
In conclusion, the successful fabrication and installation of a large diameter DSS pipeline underlines the resilience of the oil and gas industry in the
face of unexpected challenges like the COVID-19 pandemic. Despite disruptions and logistical hurdles, the project was completed before the deadline, meeting all requirements, and demonstrating the benefits of innovative practices and effective collaboration between pipe mills, contractors, and end users. The use of digital tools for remote inspections and close monitoring of vendors helped ensure compliance with project requirements, while technical authority approvals managed any deviations. The project’s success is a testament to the dedication and technical expertise of the team involved, who overcame all odds and obstacles to deliver a high-quality and reliable pipeline. This project serves as an excellent example of how best practices, technical alignment, and innovation can help organisations overcome challenges and achieve their goals.
Acknowledgements
The authors would like to express their gratitude to Petroleum Development Oman, as well as the individuals, contractors, and suppliers, associated with this project. Their contributions and support have been invaluable in making this project a success.
About the authors
Dr Janardhan Saithala has 15 years of experience in materials & corrosion engineering and currently works for Petroleum Development Oman in Project Delivery. Janardhan has published 25 papers on duplex stainless steel and is a Fellow of the Institute of Materials Minerals and Mining (IOM3).
Mohammed Ghafri has 18+ years of experience as a material and corrosion integrity engineer, specialising in the oil and gas industry. His expertise includes material selection for surface and subsurface applications, and material integrity in high-temperature steam and critical sour environments. He is a subject matter expert in Wells, Sour, and Steam material selection and is becoming a qualified HSE assessor.
Pasupathi Manivannan has 25+ years of experience in welding engineering, covering metallurgy, inspection, quality control, and assurance. For the past eight years, he has worked at Petroleum Development Oman, handling over 15 oil and gas facility construction projects covering different metallurgical chemistries.
Harshal Barve is a Mechanical Engineer with 28 years of experience in petrochemical and refining plant design, cross-country and interfield pipeline design, oil and gas field development and pipeline project execution. He works at Petroleum Development Oman as a Senior Technical Authority in Pipeline Engineering and Project Delivery.
Ishaq Tobi has 23 years of experience in the oil & gas industry managing a diverse range of pipeline and construction projects. In addition to his extensive experience, he serves as a cluster leader for gas projects. Ishaq Tobi holds a BA from Sultan Qaboos University.
Amjad Kharusi is an experienced Material & Corrosion Engineer with a demonstrated history of working in the oil & energy industry. Skilled in Material Selection for surface and subsurface, Failure Mode and Effects Analysis (FMEA), Coatings and Corrosion Management, Amjad is a strong operation professional with a MSc focused in Corrosion Control Engineering from the University of Manchester.
About this Featured Story
This Featured Story appeared in Stainless Steel World April 2023 magazine. To read many more articles like these on an (almost) monthly basis, subscribe to our magazine (available in print and digital format – SUBSCRIPTIONS TO OUR DIGITAL VERSION ARE NOW FREE) .
Want to contribute as author? Please contact Joanne.
Every week we share a new Featured Story with our Stainless Steel community. Join us and let’s share your Featured Story on Stainless Steel World online and in print.