Article by Joanne McIntyre
Since 2013 David Barber has been the Global Improvement Leader Materials Engineering Discipline at Dow, USA, with more than 100 Materials Engineers, Technologists and Technicians aligned to him within the company. This year he is bringing his expertise to Dusseldorf, Germany in his role as Chairman of Duplex World.
Duplex to lower overall costs
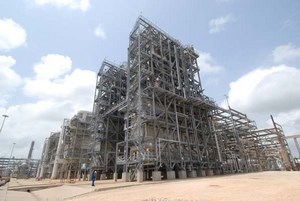
An important aspect of David’s work is implementing improvement opportunities for the materials discipline for Dow chemical facilities around the globe. “From a materials point of view there are two ways in which we can achieve improvements. One is by carefully evaluating which materials we use in various processes and the other is by improving the supply of materials to streamline costs. When we talk about reducing costs, there are two key aspects to achieving this: the short term aim of having the lowest capital costs when acquiring materials, and the long term aim of achieving the lowest cost of ownership.”
“Duplex stainless steels fit very well with our objective of achieving the lowest cost of ownership. One of the most attractive reasons for specifying duplex is that it doesn’t require painting. This lowers both the short term investment and long term maintenance costs over the lifetime of the equipment.” “Historically, the processes that we are working with and the climates we tend to operate in have required us to paint 316 stainless steels to avoid external chloride stress corrosion cracking. Therefore it’s easy to understand why duplexes are an ideal replacement material. We have steadily increased the use of duplex stainless steels since the early 1990s. It has proven to be an attractive alternative to nickel alloys in certain processes due to its superior corrosion resistance and higher strength, which translate to lower cost.”
USA a large user of duplex
“We must rely on the manufacturers to… determine the best materials for certain environments”
Trends in the discipline
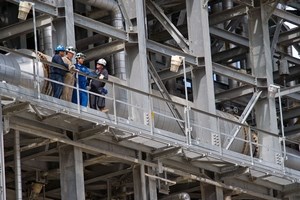
When asked if he has seen any recent trends in the use of materials David replies: “We are certainly bolder about using titanium than we were in the past and we now use a lot more of that in our processes. As a result of several acquisitions in the company we have also gained a lot of knowledge about using zirconium and tantalum and are now specifying more of both these metals. However that is only a trend within our company.”
“Personally I think that one of the most significant challenges that end users face in the materials discipline has been the reduction in the number of technical staff employed by many companies. While we operate within a lean business model, Dow has worked hard to reverse this trend recently with increased hiring taking place. I’m now seeing that happening in other companies as well. However across the industry in general I think it’s fair to say that experience with materials is not as broad as it could or should be in the end user community.”
Sustainability
Sustainability is a hot topic in the materials industry and David explains that Dow is also doing its part to operate sustainability. “For example within the materials discipline we aim to select materials that will last the lifetime of the plant as we design it. This means that we don’t use more material than is needed. In addition, using the minimum quantity means that that we can lower the weight and cost of the materials used, which is also a sustainable approach.”
Challenges
Importance of face to face events
Given that I was speaking to David during the Stainless Steel World conference I asked him how important this type of technical event was for his profession. He was quick to answer: “In my job it’s becoming increasingly important to attend conferences. Events like this fulfil an important role because face to face communication is key; you simply can’t do it all through email. It is essential to be out in the market meeting people and building relationships.” “Looking ahead to Duplex World in October, I am looking forward to learning more about developments in the use of lean duplex both in terms of new uses for the material and the increased commercial availability of the material in more components, different product forms, etc.”

About David Barber
About DowDuPont
On August 31, 2017 Dow Chemical and DuPont merged and became the world’s largest chemical company in terms of sales with a combined entity of approximately USD $130 billion. The merger brought together two innovative, science-based companies that hold leadership positions in the Agriculture, Materials Science and Specialty Products industries. Within 18 months the company will be split into three publicly-traded companies which will focus on the following: agriculture, materials science (which will be named Dow), and specialty products.