Article by Brittani Schroeder, KCI Publishing
Since their inception, Nippon Steel Corporation has been consistently raising the bar as a leading manufacturer with a wide range of world-leading capabilities, including the manufacture of seamless stainless steel pipes. To this day, the company has continuously adapted and innovated for their clients in a range of industries and continues to strengthen their manufacturing capabilities to address evolving client needs.
Before manufacturers Nippon Steel Corporation and Sumitomo Metal Corporation merged in 2012, Nippon Steel Corporation had been a strong leader in welded carbon steel tubes and pipes; Sumitomo Metals was strong in the field of seamless tubes and pipes. The merged company was renamed to Nippon Steel Corporation in 2019. Since the beginning, Nippon Steel has offered clients many advantages and manufacturingcapabilities, which have helped the company build a strong reputation andgain ground in the global marketplace. Nippon Steel’s state-of-the-art manufacturing capabilities and technologies are carried out across multiple steelwork facilities, major research centers, and laboratories located throughout Japan. Manufacturing highquality and dependable products has solidified Nippon Steel’s reputation as along-term supplier for top-tier companies across a multitude of industries.
Serving a range of industries
Nippon Steel has a total of five business segments, which include steel, engineering, chemicals, new materials, and system solutions. The steel segment operates through seven product-based units: pipe & tube; flat products; bar & wire rod; plate; construction products; railway, automotive and machinery parts; and titanium & specialty stainless steel. With their advanced technologies and superior services, the Nippon Steelpipe & tube unit is a major world player,especially in the energy sector, which includes oil & gas development and power generation.

in research and development; pictured is
the Amagasaki plant which has extensive
R&D capabilities.
Each of Nippon Steel’s three steelworks – Kansai Works/Amagasaki Area, Wakayama Area, and Kyushu Works/Hikari Pipe & Tube Unit – bring their own merits to the company’s tube production. The Hikari Works produces more common stainless steel grades such as 304 and 316, whereas the Kansai Works Amagasaki Area produces high-end material like nickel-based alloys. The Kansai Works Wakayama Area is able to produce 10”- 16” SMLS and STLS in addition to their main productions of OCTG and line pipes. A main focus for the company over the last few years has been on the petroleum and power generation industries. When NORSOK was becoming the standard requirement for the offshore market, Nippon Steel was quick to adapt and include the proper practices into their Kansai Works Amagasaki Area and Kansai Works Wakayama Area mills. The NORSOK standards were developed for the petroleum industry to ensure adequate safety and cost effectiveness for industry developments and operations.
An in-depth look at applications in industries
When the company is manufacturing equipment for use on FPSOs, offshore platforms and other umbilical and subsea systems, 25 Cr Super Duplex is the grade of choice, because of its high corrosion resistance. The power generation industry has also led to significant demand for metal grades such as SUPER 304H™ and HR3C™. Currently, a large amount of the company’s SUPER 304H™ and HR3C™ are used in the coal-fired power market. Needs for steel pipes for coal-fired power generation are decreasing due to CO2 emission control; however, these materials are also used in biomass power generation and natural gas combined cycle power generation. Nippon Steel is therefore developing materials to meet those needs. In the chemical and petrochemical industries, Nippon Steel has gained a major share in the heat exchanger market by meeting client needs. Some of these needs include providing consultation to their clients, ensuring everything is created to the user’s specification, and there are no problems during production.
This is in addition to Nippon Steel’s dedication to its punctual delivery promise. The company’s range of manufacturability for Ni-alloy tubular products has been expanded to ~OD 10” (outside diameter), and the company is aiming to enlarge their footprint in the piping market as well. Nippon Steel has also expanded further into these industries by focusing on nickel-based alloys, particularly UNS N08825, N06625, and N10276.
Specialty materials and a highquality manufacturing processes
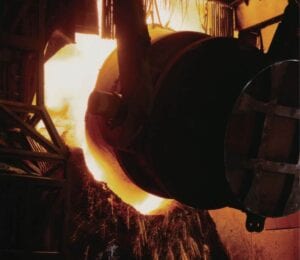
Nippon Steel is proud to be the number one materials supplier in terms of quality and technology, especially in stainless seamless and nickel alloys in the energy field. The company has been known to work with a wide range of specialty materials, along with more ‘workhorse’ grades. Their line-up of nickel-based alloys includes both common grades like N08825 and N06625.
Regardless of the material being used, all of Nippon Steel’s products are manufactured in one of the company’s own steelworks, which ensures that each and every tube and pipe is produced using high quality materials. Each product is constructed using original, non-counterfeit material so that a specific product can then be trusted to successfully perform the job it was designed to do.
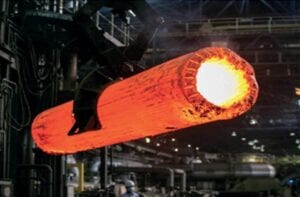
steel products, both in Japan and overseas.
This product dependability is essential since the majority of all Nippon Steel products are used in critical service environments. Nippon Steel can closely monitor and trace the in-house manufacturing at the steel work facilities throughout Japan, and can therefore strictly enforce integrated quality control and traceability for all of their products. By having access to their own mills and manufacturing facilities, Nippon Steel can accommodate a large range of sizing options for their clients, ranging from the smallest sizes to OD 16”, depending on the specific metal grade being used. For special purposes, the forged pipe plant in Kansai Works/ Amagasaki Area can manufacture stainless seamless steel (STLS SMLS) pipe up to OD 762mm, and DFARS (Defense Federal Acquisition Regulation Supplement) can be supported at all of the mills in Amagasaki, Wakayama and Hikari. The wide range of capabilities Nippon Steel offers ensures that client expectations are not only met but always exceeded.
An investment in research and development
Research and development (R&D) are two extremely important practices to Nippon Steel and they have made huge investments. The company has two major R&D centers that excel at researching and developing new products or improving existing ones. The first, located in Amagasaki, has approximately 300 employees on hand, and the second, located close to Tokyo, has 700 employees, all dedicated to furthering the company’s product offerings.
Anti-PTASCC solutions for petroleum refineries
A recent development that has delivered
positive results is grade 347AP (anti-polythionic). AP series stainless steels have a track record of being widely used across Japan. Since the early 2010s, the use of AP stainless steels has been steadily increasing worldwide, including North America, Europe, and Southeast Asia.
Conventional stainless steels such as Type 316L, Type 317L, Type 321(H) and Type 347(H) have a higher risk of PTASCC (PolyThionic Acid Stress Corrosion Cracking) in hydrotreating, hydrocracking, and delayed coker units of petroleum refineries. PTASCC can occur with the combination of three factors; formation of polythionic acid due to exposure the metal sulfide scale to oxygen and water in the aqueous phase, residual tensile stress, and sensitized microstructure having the Cr carbide precipitation at the grain boundary by welding. Nippon Steel manufactures a unique AP (Anti-PTASCC) series austenitic stainless steels as a solution to PTASCC for petroleum refineries. The most important characteristic of AP series austenitic stainless steels is an excellent PTASCC resistance without PWHT and/ or thermal stabilization.
Applying AP series austenitic stainless steels has been proven to save fabrication and turnaround operation costs. For the benefit of fabrication, PWHT and thermal stabilization heat treatment heating up to 1,650ºF (900°C) for four hours are not required. Thus, 347AP can make fabrication duration shorter and fabrication cost lower compared with conventional austenitic stainless steels. Also, to the benefit of turnaround operations, conventional mitigation methods for PTASCC, such as neutralization using soda ash and nitrogen sealing, can be eliminated during turnaround. Therefore, the loss of gross margin and maintenance cost for neutralization are saved.
Looking forward
Nippon Steel Corporation has proven themselves a leading global manufacturer with a wide range of capabilities across many industries. With their significant investments in research and development, their wide range of materials – from nickel, to duplex, to stainless, to carbon, and alloy steel – in addition to reducing cost and lead times for their specialty products, the company has become the first choice in a range of industries. As a company, the overall aim is to never become complacent. Nippon Steel will continue to be there for their clients and offer them product solutions and new materials that will improve their businesses and keep them ahead of the competition. Clients can trust that Nippon Steel will always provide the highest quality products, manufactured to the highest standards.
Nippon Steel Corporation presented in Stainless Steel World Japan held on 16th to 17th February regarding UNS S34752 with superior sensitization resistance and creep rupture strength to UNS S34709. The characteristics of S34752 are superior sensitization resistance by both extra low Carbon control and higher Nb/C ratio and maximum 30% higher creep rupture strength by both Cu and B additions compared with S34709. In addition, UNS S34752 indicates higher SRC (Stress Relaxation Cracking) resistance than S34709 without PWHT (Post Weld Heat Treatment). S4752 has already registered to ASME Sec. VIII as Code Case 2984. We believe that S34752 is applied for heater tubes or heat exchanger tubes in a complex refinery and petrochemical equipment as the replacement of S34709 because of saving fabrication cost by both thinner wall thickness of material and the elimination of PWHT, and decreasing SRC risk during actual operation.
Every week we share a new Featured Story with our Stainless Steel community. Here you are provided with an online abstract, the full story features in our print and digital magazine. Join us and let’s share your Featured Story on Stainless Steel World online and in print.”
Featured Story by: Brittani Schroeder
All images were taken before the COVID-19 pandemic, or in compliance with social distancing.
Read the full article.