SABIC petrochemical site at Jubail, Saudi Arabia.
Oil and gas price rises have raised costs for the petrochemical and chemical industries, thanks to background inflation aggravated by the war in Ukraine. Yet this may accelerate an already existing trend toward cutting greenhouse emissions by turning to green energy, seeking alternative feedstocks and building up the circular economy.
By James Chater
Scarcity
The Covid pandemic and Russia’s invasion of Ukraine are two factors that have exposed the frailties of global trade. Extended, interdependent supply chains are under strain, and worrying security gaps are affecting the supply of such essential items as food, energy, fertilisers, raw materials and semiconductors. Globalism appears to have reached its limits and is being reappraised in the light of security issues.
In the middle of all this stand the petrochemical and chemical industries, which are challenged by rising costs and a relative scarcity of fossil fuels as the world reduces its dependence on Russian oil and gas. This squeeze affects the industries in two ways, as fossil fuels serve both as feedstocks and energy sources. Chemical and petrochemical companies, especially in Germany, face rising costs and can expect lower profits. In Asia, producers are scrambling to find alternative feedstocks. These pressures are likely to accelerate the inevitable transition towards greater sustainability in the process industries. In other words, reduced dependency on fossil fuels can kill two birds with one stone: blunting Russia’s ability to wage war while reducing the carbon footprint. However, whereas heat, electricity and mobility can be generated without carbons, chemicals and petrochemicals cannot be produced without them – at least, not yet. Therefore, the solution is to create a circular economy in which carbons are re-used instead of being released into the atmosphere. If “zero-carbon” is impossible, “lower-carbon” is achievable.
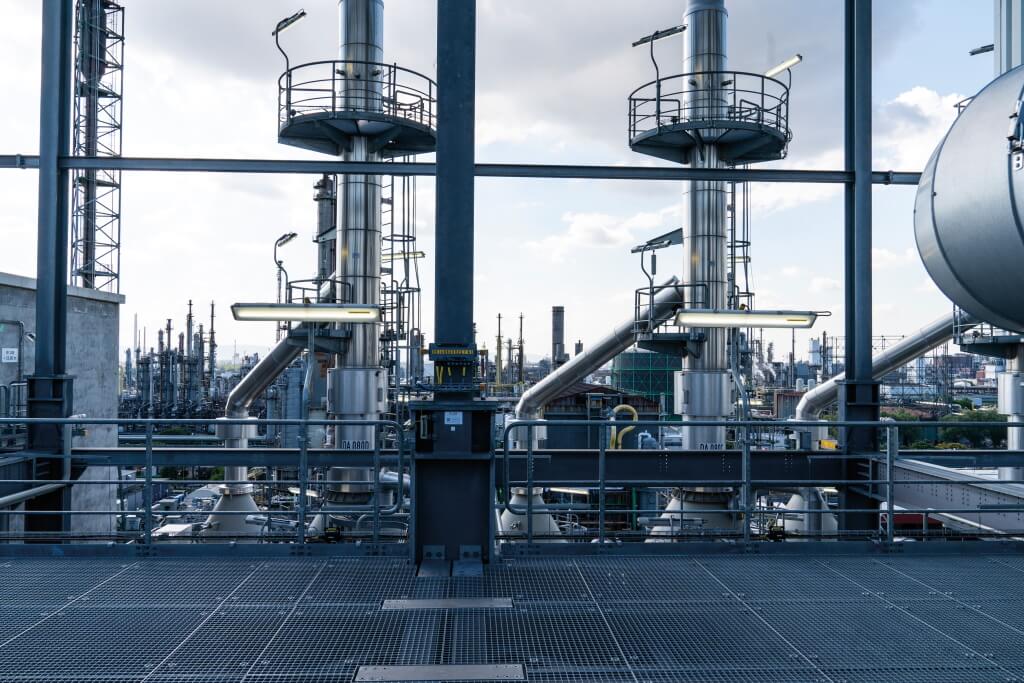
Projects

The demand for fossil fuels from the process industries has been rising and is expected to increase. Moreover, these industries will account for a larger market share as renewables take over the energy market. When fossil fuels were cheaper and perceived as abundant (not so long ago!), an uptick in projects occurred as the oil & gas majors sought to add value to their primary products and cater for rising demand for plastics and fertilisers. This trend particularly affected especially the United States, keen to exploit its shale resources, and China. The latter is expected to see 512 petrochemical projects start up between 2021 and 2025. (Note: this estimate precedes the war in Ukraine). Among the many projects, we can name only a few: Zhejiang Petrochemical Daishan Xylene Plant 2, which is in the construction stage; BASF’s Verbund site in Zhanjiang, Guangdong, which is nearing completion; the BASF-Sinopec expansion of their Verbund site in Nanjing; and Sinopec’s expansion of ethylene and oil refining capacity in Hainan Province. In the Asian region, butadiene capacity additions are expected to hit 3.65 million tons per year between 2021 and 2025, nearly half the region’s capacity additions.
BASF, the dominant player in Europe, is building an alkylethanolamines plant in Antwerp and a 2-ME plant and an acetylene plant in Ludwigshafen.
In Russia, Lukoil is building a polypropylene complex at its Nizhny Novgorod refinery. In the USA, ExxonMobil is expanding its chemical plant in Baytown, Texas, and Chevron Phillips Chemical is expanding its propylene business with a C3 splitter. BASF is working on an MDI expansion in Geismar, Louisiana.
The fertiliser sector, now at the forefront of concerns over food security, is one in which Russia and China are dominant. It is, therefore, good news that carbon-free ammonia plants are being built by Monolith Materials in the United States; y Vestas and Haldor in Denmark; by KBR in Alberta, Canada; and by a consortium of Ørsted and Yara in the Netherlands.
Green energy
The replacement of methane by renewable energy in ammonia production is part of a wider trend toward the greening of (petro)chemical plants. Renewable energy is being used to provide the heat and pressure needed to split molecules such as CO2, water, oxygen and nitrogen into reactive elements. At least two such projects are underway: Solvay’s hydrogen peroxide facility in Voikka, Finland, which will be totally wind-powered from 2023; and SABIC’s polycarbonate facility in Cartagena, Spain, which is scheduled to start up in 2024 and will be the first chemical plant run on solar energy. BASF was planning the world’s first petrochemical plant fuelled 100% by renewable energy for Mundra, India, but the project was paused because of Covid.
Scientists want to go further, dispensing with fossil fuels altogether by using electricity not just as a source of heat but as a direct input into the reactions. However, progress on this depends on the price of renewable electricity falling to a level where this is economical.
Bio-feedstocks
Renewable feedstocks are another means to reduce the carbon footprint of the process industries. Waste-to-fuels, waste-to-chemicals and biofuels-to-chemicals are all processes that can reduce, if not eliminate, net carbon emissions. A few recent examples include Lummus and Synthos’s bio-butadiene (synthetic rubber) technology; Gasum’s plant near Helsinki that will convert biowaste into biogas for transport, industry and fertiliser production; and numerous partnerships between industry and scientists.
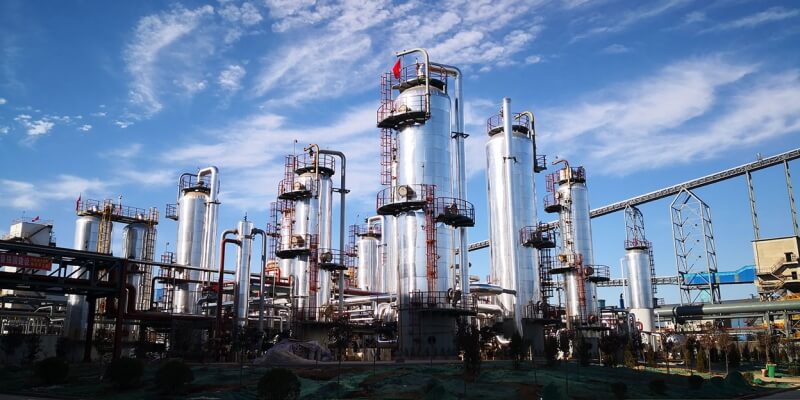
Recycling
Through our domestic recycling routine, we have become aware of how quickly plastic recycling has developed in recent years. The “European Plastics Pact” aims to make plastic packaging reusable or recyclable while increasing collection, sorting and recycling capacity. Dow is partnering with Topsoe to develop a technology to purify pyrolysis oil feedstock derived from waste plastics for use in circular products, to be used at a plant in Terzeuzen, the Netherlands. Lucite
(Mitsubishi Chemical Corp.) and Agilyx are working on a project to recycle PMMA, while a PET monomer recycling process is being developed by Axens, IFPEN and JEPLAN. The northeast of England will see a commercial-scale plant to recycle plastic waste into hydrocarbon feedstocks for use in the manufacture of new plastics. Plastic Energy and TotalEnergies will build a plastic recycling in Seville, Spain.
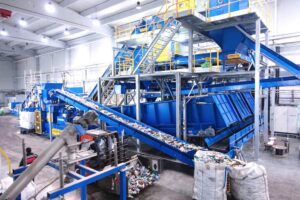
More exciting still are technologies to capture and recycle CO2 that would otherwise be emitted during steel, building material, cement and chemical production. Recycled CO2 can be used in a variety of ways: as ingredients for fuel, plastics and food, to accelerate the growth of algae or as an ingredient of concrete. An important product of CO2 is methanol, an alcoholic solvent used in chemical processes and fuel production. In Iceland, CRI in 2012 built a demo plant in which renewable energy is used to electrolyse water to isolate hydrogen, which is then reacted with waste CO2 to produce methanol. One Icelandic geothermal plant recycles its CO2 to produce methanol. In a chemical plant at Tongyezhen, China, CO2 from a lime kiln is combined with hydrogen and CO2 from a coking furnace to produce methanol. Recently, Inovyn announced a project to recycle CO2 for methanol production in Antwerp. These projects are vital for decreasing harmful emissions while reducing reliance on fossil fuels.
Materials
Chemicals and petrochemicals use perhaps a wider range of stainless steels and special alloys than any other industries. These materials are advantageous because they are easy to clean, non-porous and adaptable. Also, the combination of acidic conditions, high pressures and heat require the toughest of alloys. They are applied in acid gas strippers, tanks, crystallisers, digesters, hydrocrackers, reactors, heat exchangers, filters, pipes, tubes and air separation units.
Austenitics are used for their corrosion resistance, plasticity and toughness. Milder grades can be used on inoxidable acids, whereas oxidable acids (sulphuric, hydrochloric, acetic) require stainless steels containing increased nickel with Mo, Cu and Si: superaustenitics and nickel alloys such as Hastalloy. Sandvik’s new superaustenitic Sanicro® 35 is designed for heat exchangers in refineries and (petro)chemical plants where high strength and strong resistance to both heat and corrosion are required. Duplex and super duplex grades are often used in applications where heat conditions are not too severe. Their strength is useful in recycling plants, which also use martensitics and wear-resistant steels in abrasive applications such as belt conveyors, crushers and screens.
Highly corrosive-resistant materials such as zirconium alloys, titanium alloys, tantalum, niobium, nickel alloys and copper-nickel alloys are often used to clad vessels, with milder grades used as backing.
For ammonia and urea applications, certain specialist grades have been proposed, such as Sandvik 2RE69, Sandvik 3R60 Urea Grade and Sandvik’s duplex grade Safurex, developed for the Stamicarbon process.
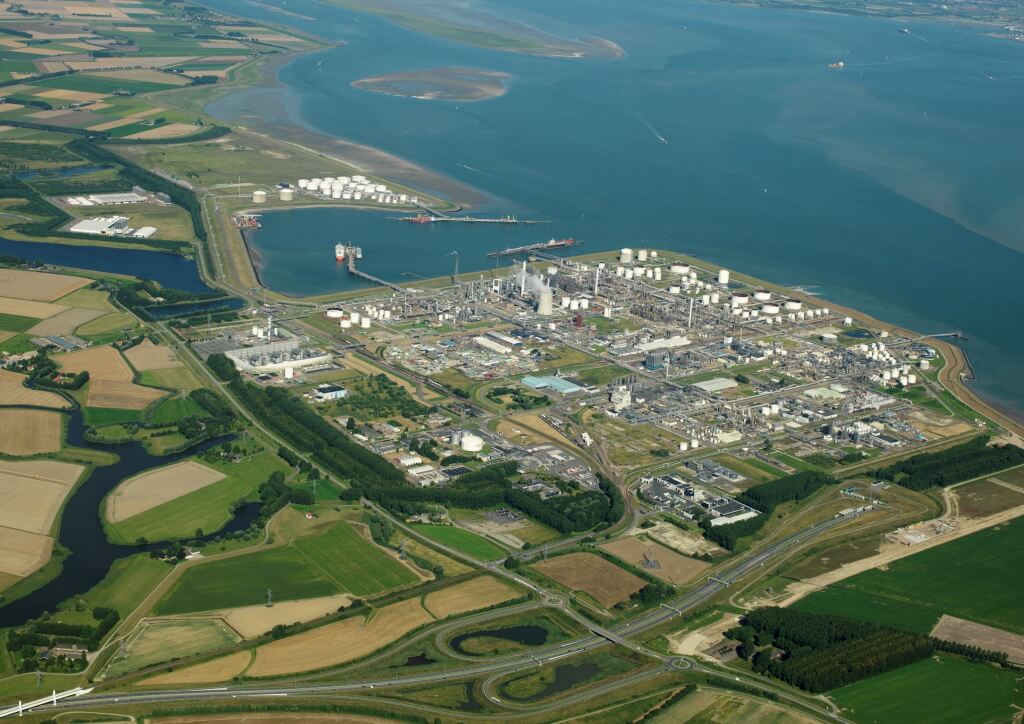
Fertiliser and food scarcity
Ukraine has been described as the world’s “breadbasket”. The war has disrupted exports of both cereals and fertilisers. Russia and Ukraine supply a large part of the wheat consumed in the global south, while Russia is a major supplier of fertiliser to the rest of the world. According to the UN, Russia is the largest exporter of nitrogen fertiliser and the second-largest exporter of phosphorus and potassium. Worse, the rising cost of natural gas has made it more expensive to produce fertiliser, particularly affecting the livelihoods of African and South American farmers and the food security in these regions. Putin’s victims are not limited to Ukraine.
Every week we share a new Featured Story with our Stainless Steel community. Join us and let’s share your Featured Story on Stainless Steel World online and in print.