Investment casting is a commonly used method to fabricate metal components in the aerospace industry. It is valued for its ability to produce precision components, as well as versatility and integrity in a variety of metals and high-performance alloys.
Text and images by 3DEO
While casting is one of the oldest techniques to make metal parts, having been invented over 5,000 years ago, this more traditional manufacturing method is commonly used to make components with standard alloys like stainless steels (including 17-4 & 15-5 PH), carbon steel, aluminum and brass, as well as nickel-based super alloys (including Inconel 718 & 625).
Typical aircraft, space and aviation applications include parts for the following components: air and fuel systems, cabin control systems, engines, environmental control systems, hydraulic systems, landing control systems, interface controls for operators, and the internal mechanism. Aerospace components must be able to withstand operational wear and failure, so they rely on superior durability and increased tensile strength, as well as flexible design capabilities allowing for thin walls, slots and undercut holes, and high-quality surface finish.
While being well-suited for the high demands and quality requirements of the aerospace industry, investment casting allows engineers to present elaborate designs and parts of different weights and sizes. Additionally, investment casting typically produces a superior surface finish and can reduce the need for secondary operations or machining. That said, however, investment casting also comes with its set of drawbacks:
- Lead times are especially long across the entire manufacturing process; from developing the tooling and molds suitable for the process to the actual production timeline and cycle run times.
- Holes cannot be smaller than 1/16 in. (1.6 mm) and should be no deeper than about 1.5 times the diameter.
- Many process factors affect the integrity of the mold and resulting part, so the quality management system is challenging, especially in a highly regulated industry like aerospace.
- Part functionality problems may arise due to variability, resulting in failure or unpredictable product performance.
- Overall costs stretch beyond just unit economics, especially for short-run productions, due to significant mold, setup, run times, minimum order requirements, and the expense of iterations.

Many engineers and supply chain managers are accustomed to working with the above drawbacks, and oftentimes don’t realize there exists an available solution that upholds the high-volume delivery of investment casting. And while advanced technologies like metal 3D printing have long been considered as a prototyping-only method, 3DEO, a high-volume metal 3D-printing company, is competing with investment casting’s production and economies of scale.
An introduction to 3DEO’s Intelligent Layering®

Intelligent Layering® was specifically designed to tackle the high cost and low throughput problems typically associated with metal additive manufacturing. Provided as a service by 3DEO alongside its proprietary automation platform, the result is a production method that virtually eliminates machine amortization as a part cost driver. It also attacks cost through the use of commodity metal powders, which can be as much as twenty times less costly than powders used in powder bed fusion.
There are no degrading processes in Intelligent Layering®, so part-to-part and machine-to-machine repeatability enables a high yield process. As a result of the tightly packed fine powder, 3DEO offers surfaces in metal additive manufacturing at 100 Ra or better.
Due to the lower variability between parts, as well as predictable ductility and strength, 3DEO has been helping more aerospace companies de-risk their supply chains and produce higher quality, lower yield loss components, specifically working with 17-4 PH stainless steel. To make an accurate comparison, let’s take a look at the capabilities and properties of 17-4 PH investment cast parts vs. 3DEO components.
The effects of porosity in investment casting 17-4 PH vs. 3DEO-printed 17-4 PH
While measuring the low porosity in 17-4 PH indicates alloy strength, hardness and density, comparing the amount of low bulk porosity between investment casting and 3DEO can be misleading. Both exhibit lower porosity when compared to many other manufacturing methods. It’s the predictability and consistency of the porosity part-to-part that makes a large difference between the two, due to local regions of high void content in investment cast parts. This is best exemplified in the durability and elongation of the parts during testing.
Stress-strain curve comparison
The stress-strain curve is a measurement technique to gauge the material strength of a fabricated metal under load. Because the same metal can be manipulated differently during manufacturing, it is imperative to perform these tests to see how the metal may or may not change its shape when subjected to certain magnitudes of force.
Stress, therefore, is measured as the ratio of the applied force to the area of material in which it is applied; and strain is the ratio of change in dimension compared to the metal’s initial dimensions. Both stress and strain are always present, and must be measured to gain a full purview of the metal’s performance.
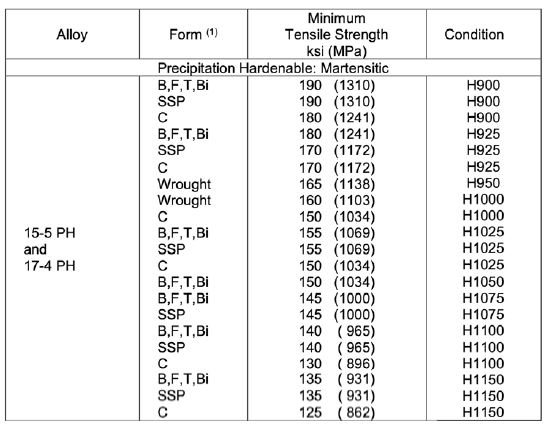
Another way to look at stress-strain is if you imagine having a semi-filled balloon. When you push on it, or deform the balloon, the resistance it shows is the internal stress. The change in dimension is the strain. Any time a material undergoes strain, the metal will try to regain its initial state through internal stress.
In the case of comparing the manufactured mechanical properties of investment cast 17-4 PH to 3DEO printed 17-4 PH, we perform a tensile test. In one study, researchers measured the effects of casting porosity on the tensile behavior of investment cast 17-4 PH stainless steel. Figure 1 displays examples of engineering stress-strain curves from investment cast 17-4PH stainless steel in the H925 and H1100 conditions. As we can see quite clearly, the strain to failure varies significantly, primarily due to the effects of internal voids – or the inconsistency of material porosity present in these investment cast parts.
Some tests in this study exhibited failure strains (engineering strain) that would not meet commercial specification requirements for castings; 6 and 10% for H925 and H100, respectively, AMS 5355 (Ref 1). When compared to 3DEO’s printing process, which results in similar levels of porosity, however consistent structural porosity, the stress-strain curve not only yielded superior results than that of investment casting, but as you can see in this image, the results are near-identical in performance. In addition, the effect of casting porosity on the mechanical behavior of investment cast 17-4PH stainless steel was studied.

It stated that: “Interdendritic porosity, formed during solidification and shrinkage of the alloy, reduces the yield strength and ultimate tensile strength roughly in proportion to the reduction in load bearing cross-section. The effects of casting porosity on ductility (% strain, % reduction in area) are more severe, in agreement with research on other alloy systems. In this study, 10% porosity reduced the ductility of 17-4PH stainless steel by almost 80% for the high-strength H925 condition. Tensile testing at -10C (263 K) further reduces the alloy ductility with and without pores present. In the lower strength H1100 condition, the ductility is higher than the H925 condition, as expected, and somewhat less sensitive to porosity.”
This is represented in the below tables. As you can see in Figure 3. (C = casting), the minimum tensile strength for H900 is 1241 MPa. As compared to 3DEO’s printed 17-4 PH, which surpasses the industry standard for MPIF, when heat treated at H900, it is already surpassing the tensile strength of investment casting at 1300 MPa.
Bringing this into actual customer stories, a number of 3DEO’s aviation and aerospace customers have reported greater than 60% failure in the nondestructive testing (NDT) process for investment cast parts due to poor material quality and inconsistencies part-to-part. As one could imagine, this adds a lot of additional, and often unexpected, costs and extra work.
Areal fraction comparison
Fracture-related mechanical properties (ductility, strength, toughness, etc.) of cast alloys are sensitive to both averages and extrema of microstructural attributes. What we see repeatedly with investment castings is that even if several pieces of the same component are cast by using the same exact process and average process parameters, as well as the same average alloy chemistry, they still may not result in the same fracture-related mechanical properties, despite having the same average microstructure. These inconsistencies are represented here in Figure 5.
On the other hand, with 3DEO, because our printing and sintering process holds much uniformity in material properties component-by-component, the quantitative fractography is nearly identical between parts.

Design and manufacturing considerations
In addition to the material and mechanical property comparisons between investment casting and 3DEO, there are a number of additional benefits that customers get from adopting their manufacturing processes to additive manufacturing.
Additive manufacturing is praised for its ability to accommodate unique geometries and angles difficult to create using other manufacturing methods. When looking at the needs of aviation and aerospace customers, where additive manufacturing shines in design and part functionality includes:
- Internal channels
- No drill-and-plug operations
- Gradual curves for less pressure drop
- Burr-free junctions between channels
- Powder-free process
- Captive features, straight/undrafted/overhung surfaces
- Webs, holes, tabs, gussets, slots, and hooks difficult to ensure in molding
With investment casting, total cost of parts can be deceptively difficult to calculate. In order to understand total cost, you have to consider all costs associated with a supplier, especially location/transportation requirements, secondary processes or post-operations necessary, yield loss due to low quality, and more.
Increased speed to market
Speed to parts can make the difference between you hitting or missing your quarterly numbers. Likewise, slower than expected deliveries can mean you’ve disappointed your customer
by missing your own deadlines. When things go wrong with investment casting, it can take weeks or months to get back on track. Meanwhile your customers continue to be disappointed about something that is out of your control. If parts aren’t to spec, they can require costly mold modifications, reworking or maintenance.
References available on request.