3D printing or additive manufacturing (AM) has rapidly revolutionized the production processes with various materials. Stainless steel is a widely used material in manufacturing, known for its strength, durability, and resistance to corrosion.
By Dr. Sastry Kandukuri, Global Practice Lead, AM and Senior Principal Specialist, Materials Advisory Energy Systems; & Chen Ze, DNV Global Additive Manufacturing Centre of Excellence & Researcher at Nanyang Technological University, Singapore
The advent of 3D printing has revolutionized the way products are designed and manufactured. Stainless steel is one of the first metallic materials adopted by AM with broad applicability for its excellent engineering properties. The ability to produce complex geometries with precision and speed has opened up new possibilities in various industries, including aerospace, automotive, medical, and consumer goods. 3D printing of stainless steel is one such application that is gaining traction and changing the way products are made. Complex geometries or superior mechanical properties have been achieved through the unique features of additive manufacturing.
However, undesired microstructures and metallurgical defects were reported along with the complicated physical and chemical reactions during the layer-by-layer fashions of manufacturing. The reliability and repeatability of AM processed stainless steel parts are well-recognised challenges, among many others. Hence standardisation for AM of stainless steel is imminent to all stakeholders in the ecosystem.
Qualification and certification based on developed standards, rules and regulations are necessary to demonstrate the quality assurance satisfying the industry requirements. A cost-effective Qualification and Certification pathway is crucial to accelerate the adoption and industrialisation of AM of stainless steel.
![Figure 1. Overview of qualification and certification for metal AM [Ze. Chen. A Review on Qualification and Certification for Metal Additive Manufacturing. https://doi.org/10.1080/17452759.2021.2018938. ].](https://stainless-steel-world.net/wp-content/uploads/sites/3/2023/06/Qualifaction-Activities_DNV.png)
[Ze. Chen. A Review on Qualification and Certification for Metal Additive Manufacturing. https://doi.org/10.1080/17452759.2021.2018938. ].
Various methods
There are different methods of 3D printing of stainless steel, each with its advantages and limitations. The most common methods are binder jetting, directed energy deposition, and powder bed fusion. In binder jetting, a liquid binder is deposited on a bed of stainless steel powder to create a 3D shape.
The binder is then cured to solidify the shape, and the excess powder is removed. Directed energy deposition involves using a laser or electron beam to melt stainless steel wire or powder and deposit it on a substrate.
Powder bed fusion uses a laser or electron beam to melt a thin layer of stainless steel powder on top of each other to create a 3D shape. Powder bed fusion and directed energy deposition are the most common techniques developed for stainless steel printing, and the commercialised feedstock for stainless steel 3D printing includes austenitic, martensitic, duplex stainless steel, etc.
Enormous potential
One of the benefits of 3D printing of stainless steel is the ability to create complex geometries that would be difficult or impossible to make with traditional manufacturing techniques. The flexibility of the technology allows designers to experiment with new shapes and designs that can improve product performance, reduce weight, and increase efficiency. For instance, in the aerospace industry, 3D printing of stainless steel can produce lightweight, high-strength parts that can withstand extreme temperatures and pressures.
Another advantage of 3D printing of stainless steel is the ability to produce small batches of custom parts on demand. In the medical industry, 3D printing of stainless steel can create personalised implants that fit each patient’s unique anatomy, reducing the risk of complications and improving recovery times.
There are many examples of 3D printed stainless steel products, which showcase the technology’s capabilities and potential applications. Here are a few notable examples:
Aerospace parts: One of the most prominent applications of 3D printed stainless steel is in the aerospace industry, where the strength and durability of the material are essential. For example, GE Aviation has used 3D printing to produce fuel nozzles for its LEAP engines, reducing the number of parts from 20 to 1 and reducing weight by 25%. Similarly, Airbus has used 3D printing to produce a partition for its A320neo aircraft that is 45% lighter than the original part.
Medical implants: 3D printing of stainless steel has the potential to revolutionise the production of medical implants. For example, Australian medical device company Anatomics has used 3D printing to produce a custom-made sternum and ribcage for a patient, which was implanted during a complex surgery. Similarly, Oxford Performance Materials has used 3D printing to produce spinal implants that are customised to each patient’s unique anatomy.
Consumer goods: 3D printing of stainless steel can also be used to create high-end consumer goods. For example, Dutch designer Joris Laarman has created a series of 3D printed stainless steel chairs and tables, using complex geometric shapes that would be impossible to make with traditional manufacturing techniques. Similarly, Italian fashion house Bulgari has used 3D printing to create a limited edition watch with a stainless steel case.
Industrial parts: 3D printing of stainless steel can also be used to produce a variety of industrial parts. For example, Swedish engineering company Sandvik has used 3D printing to produce a cutting tool for the aerospace industry that is more durable and efficient than traditional tools. Similarly, Dutch metalworking company K3D has used 3D printing to produce a custom-made manifold for a hydraulic system.
Overall, 3D printing of stainless steel has enormous potential for a wide range of applications, from aerospace and medical implants to consumer goods and industrial parts. As the technology continues to evolve and become more accessible, we can expect to see even more innovative uses of 3D printed stainless steel in the future.
Challenges
However, 3D printing of stainless steel has its challenges. The cost of the equipment and materials can be high, and the process can be slow, making it less suitable for high-volume production. Additionally, the final products may not be as strong as those produced by traditional manufacturing techniques, and the surface finish may require additional post-processing. Despite these challenges, 3D printing of stainless steel has enormous potential in a wide range of applications. As technology evolves and becomes more affordable, it is likely to become an increasingly important manufacturing method.
The ability to produce complex, customised parts on demand can improve product performance and efficiency while reducing costs and waste. The combination of 3D printing and stainless steel offers an exciting future for innovation and progress in many industries. An overview of the qualification and certification for metal AM is illustrated in Figure 1.
The process of qualification for metal additive manufacturing involves demonstrating the ability to meet specific requirements. This may include reviewing specifications, verifying designs, managing feedstock and materials, following manufacturing processes, conducting product testing and inspection, and preparing and reviewing documentation, among other activities.
On the other hand, the certification process is intended to ensure that the metal AM process complies with qualified parameters, standards, or specific requirements. This may involve conducting unscheduled surveys of the metal AM process, performing testing and inspection, verifying traceability, witnessing test specimens, verifying compliance with requirements, and documenting compliance through the issuance of a certificate.The primary focus when considering the use of metal additive manufacturing technology for specific products should be on its feasibility and qualification. This will determine the selection of materials and processes, such as powders, wires, sheets, PBF, DED, binder jetting, and sheet lamination, based on the opportunities presented by existing or new products.
Feasibility considerations
For existing products, feasibility considerations should include direct printing for small-batch production or bypassing long supply chains/lead times, structure optimisation for lightweight and non-assembly through redesign, and repair and remanufacture. For new products, design considerations should aim to achieve multiscale, multifunctional, and hierarchical structures with desired properties, while also establishing technical and product design specifications based on capabilities, productivity, and application requirements such as hardness, toughness, strength, fatigue, corrosion resistance, and wear resistance.
Quality control measures such as characterisation and review of materials, assessment of operation procedures and process parameters, and testing for consistency and robust production performance validation should be implemented to ensure serial production qualification during metal AM processes and post-processing. Certification activities should be conducted to certify conformity of single or batches of products, with the level of certification required depending on component criticality, thus bringing trust to the product.
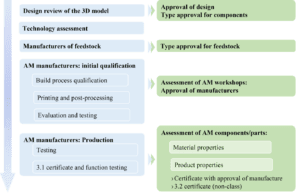
Qualification/certification requests
Qualification or certification requests for metal additive manufacturing may originate from AM service providers, product owners, or end-users. The evaluation of such requests typically begins with a design review of a 3D model, with the approval of the design or type approval serving as the first deliverable.In most cases, a technology assessment is also necessary for AM stakeholders seeking market access to identify potential failure modes. In parallel, qualification of the feedstock may also be carried out to obtain the type approval of a feedstock certificate.For AM manufacturers, initial qualification is required before production can commence, including build process qualification, printing and post-processing, and evaluation and testing.
Approval of an AM manufacturer compliance certificate can be obtained based on the assessment of the AM workshop during the initial qualification process. For AM with sufficient production readiness, the assessment of AM components or parts can be carried out through testing of material and product properties, such as functionality or pressure testing. Approval can be granted based on the 3.1 certificate (a statement of compliance issued by an authorised inspection representative by the manufacturer under European standard EN 10204) and function testing, with the possibility of obtaining a certificate with the approval of the manufacturer and a 3.2 certificate (a statement of compliance issued by an inspector designated by the official regulations under European standard EN 10204) for non-class.
There is a systematic pathway for the approval and certification of AM-related processes and products at DNV. The latest published service specification, DNVGL-SE-0568, describes the qualification management services related to the qualification of AM manufacturers, service providers, and AM parts specified in DNVGL-ST-B203 (DNV GL 2021).
Opportunities
Metal AM presents an opportunity for the shipping industry to produce spare parts and minimise lead times, costs, stock requirements, and environmental footprints. To instill confidence in the users of AM parts, certification guarantees that these parts are as reliable as their conventionally manufactured counterparts. DNV awards thyssenkrupp the first Additive Manufacturing Approval of Manufacturer Certificate based on a probehead for taking gas samples in a hot gas atmosphere, as shown in Figure 3. It is additive manufactured from austenitic heat-resistant steel and has a longer service life due to integrated cooling channels. The newly issued certificate makes the ThyssenKrupp TechCenter Additive Manufacturing the world’s first producer of 3D printed parts for maritime applications to obtain manufacturer approval from DNV.

About the authors
Dr Sastry Kandukuri has worked at DNV’s Head Office in Oslo since 2007 and is Global AM Lead and Senior Principal Materials Specialist. In 2018 hewas instrumental in establishing the DNV Global Additive Manufacturing Technology Centre of Excellence (AM CoE) in Singapore. In addition to authoring more than 25 DNV standards and guidelines, he has been involved in many other Standards organisations including ISO, ASTM, API, ASME and has extensively contributed to the development of AM standards at Singapore Manufacturing Federation as well as Singapore Military AM standards working group.
Chen Ze is a Consultant at the DNV Global Additive Manufacturing Centre of Excellence & a Researcher at Nanyang Technological University in Singapore. He graduated with a double master’s degree from theUniversity of Science and Technology Beijing and Nanyang Technological University in 2009, and has over ten years of working experience in materials as a metallurgist. Ze is specialised in metallurgical processes and material advisory. Currently, he is working on qualification and certification while pursuing his PhD with a research focus on metal AM processes.