Shearwater Platform, operated by Shell, with walkway leading to wellhead jacket. Off the coast of Aberdeen, Scotland. Photo © Stuart Conway.
Oil & gas prices have fallen from their 2022 highs, but the sector is flourishing, with many projects underway. concerns about global warming are driving companies to reduce their carbon footprint. 3D printing is finally transforming the industry, while demand for duplex and other stainless products remains strong.
By James Chater
Outlook
Oil & gas prices have subsided since peaking at over USD 100 last year. However, they remain stronger than they were at the beginning of last year (Brent Crude stood at USD 78.71 on 10 July). This is good news for producers, especially those in the West, who have been making bumper profits. It is less good news for consumers, as higher energy prices drive up the prices of other commodities.
Many Western governments have imposed sanctions on or ceased to do business with Russia, which is being forced to sell its hydrocarbon products at a discount to India and China. Also, Russia has taken over certain foreign assets on its soil, while Western governments have done the same with Russian assets outside Russia.
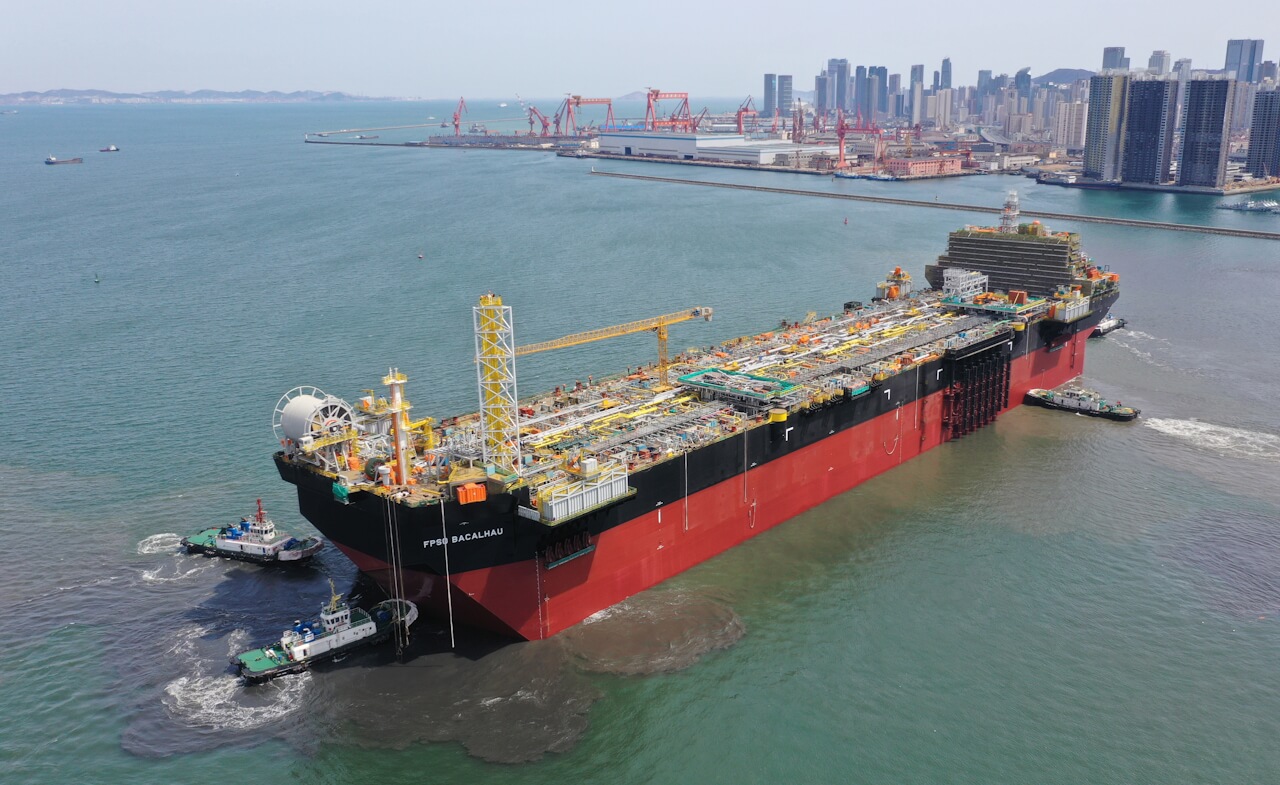
Projects
In Europe, a major challenge is to reduce energy dependence on Russia. Croatia is building a gas line to increase the import capacity of the Krk LNG terminal. Hungary and Croatia are planning to increase the capacity of a pipeline bringing gas from an LNG import terminal in Croatia to Hungary. The North Sea, though mature, continues to be productive: in December, Johan Sverdrup Phase 2 started up; Shell decided to invest in the Jackdaw gas field, awarding the EPCI to TechnipFMC. The Norwegian government approved plans to develop the Irpa and Verdande subsea fields and the production well Andvare in the Norwegian Sea. Equinor’s Rosebank, the largest undeveloped oil and gas field in the North Sea, may soon receive UK government approval (although the licensing of new fields is a political hot potato in the UK).
The energy outlook in North America is also robust. The shale fields continue to be productive, allowing the USA to export LNG to Europe. In Alaska, ConocoPhillips approved its Nuna oil field, while on the Gulf Coast, ExxonMobil started up its Beaumont refinery, adding 250,000 barrels per day of capacity.
Ukraine
A lot is at stake in the Russia-Ukraine war, not least fossil fuels. Russia took over Crimea in 2014, partly to take control of the vast oil and gas reserves in the Black Sea. The Russia-installed government in Crimea has already asked Gazprom to manage the peninsula’s resources. Moreover, Ukraine holds Europe’s third-largest shale gas reserves, located in the Russia-held Donetsk and Kharkiv regions. Ukraine has also lost control of the 45.6% of its coal reserves that lie in the occupied eastern regions.
In South America, ExxonMobil is advancing its fifth project in Guyana, Uaru, in the Stabroek block, which involves ten drill centres, 44 production and injection wells and the construction of an FPSO vessel by MODEC. Guyana also opened a tender for its first oil refinery. Equinor has awarded important projects in the Bacalhau and BM-C-33 fields in the Santos area offshore Brazil. Argentina has increased output from its shale deposits at Vaca Muerta, the world’s second-largest shale gas reserve and the fourth-biggest for shale oil.
In Africa, the energy situation is undergoing rapid transformation. Ugunda’s economy is expanding at a rate of 5-6% per year thanks to its hydrocarbon investments. One oil rig has been commissioned, and three more are being developed. Azule Energy, the BP/Eni JV, began operations in Angola. An FPSO made in China was added to the Greater Tortue Ahmeyim natural gas project off Mauritania and Senegal. Nigeria’s NNPC started drilling for oil and gas at a field in northern Nigeria that has reserves of 1 billion barrels. In Libya, Honeywell will build the Southern Refinery project. South Africa, whose coastline remains largely under-explored, could be next.
In the Middle East, the big news is the emergence of Israel as an oil and gas power. Its first crude oil exports took place in February. Its Tamar gas field in the Mediterranean has been expanding. A third pipeline was added, and phase 2 will bring online compressors already in place and add onshore infrastructure. Egypt is expanding at its vast Zohr gas field, with Saipem supplying 170km of umbilicals.
Australia and the Far East are likewise seeing a number of projects. Shell is to develop the Crux gas field in Western Australia; India’s Hindustan Petroleum Corp (HPCL) plans to start its Barmer refinery and petrochemical project in Rajasthan state by January 2024; Indonesia approved a revised plan of development for its Merakes and Merakes East gas fields.

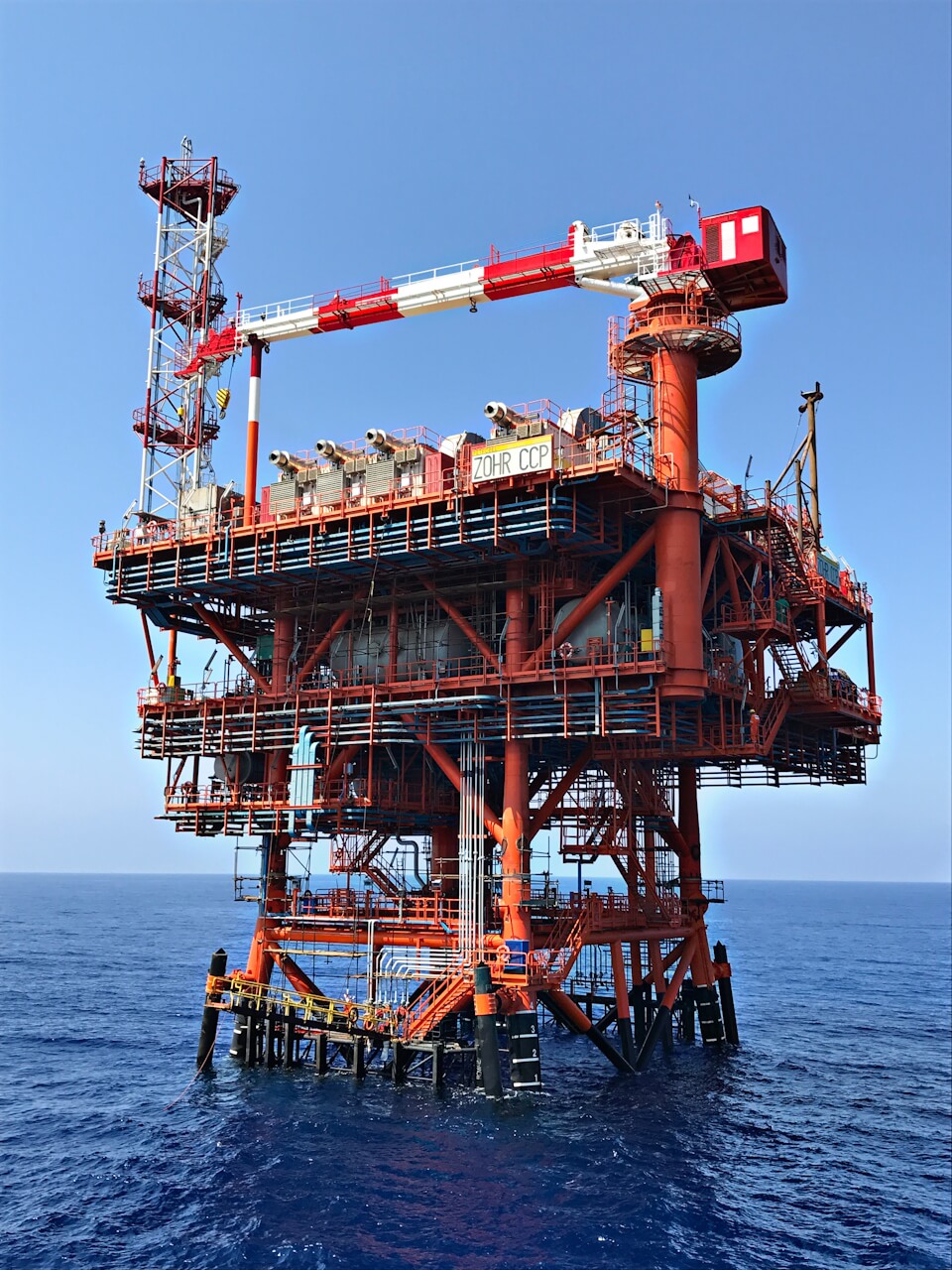
The giant Zohr offshore gas field in Egypt, operated by Eni, was discovered in 2015. Commissioned in December 2017, in August 2019 gas production exceeded 2.7 billion cubic feet per day. Photo: Eni.
Emissions abatement
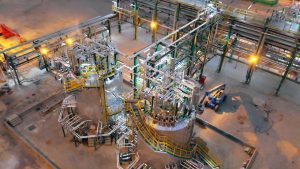
Oil & gas development has transformed the economies of many countries and regions that were previously poor or import-dependent. But given the climate emergency, should these new developments be happening at all?
In fact, many oil & gas companies are investing in green energy and are struggling to reduce their ecological footprint. “Sustainability” is a buzzword in the oil & gas industry as stringent emissions targets become ever more demanding. Just in the last year, many CO2 sequestration and storage (CSS) projects have been initiated all over the world. In the Houston area, 11 companies have joined forces to reduce emissions around the Gulf of Mexico. One of the first such projects offshore is Chevron’s Bayou Bend Carbon Capture and Sequestration hub in the Gulf of Mexico. Likewise, ExxonMobil has joined forces with MHI (Japan), Pertamina (Indonesia) and CNOOC/Shell (China), while similar projects are being developed in the North Sea: Equinor-Wintershall Dea, BP-Harbour Energy, TotalEnergies-Equinor-Shell (Northern Lights), to name only a few.
Taking one step further towards recycling, Chevron is also collaborating with Air Liquide, PetroChina and Keppel on a CCUS project (carbon capture, utilization, and sequestration) in Singapore. The CO2 that is not sequestered will be used to make cement, plastics or fuels.
Methane is 28 times more powerful as a factor in global warming than CO2. Technologies being developed to cut methane emissions include drones equipped with sensors, and TotalEnergies’ AUSEA technology (Airborne Ultralight Spectrometer for Environmental Applications), which detects and quantifies methane and CO2 emissions.
3D printing
In the last few years, especially the last 12 months, 3D printing (or additive manufacture – AM), has become mainstream in the oil & gas industry. This technology, already well established in the aerospace and medical industries, reduces the need for physical inventory, eliminates waste and can be several times faster than traditional methods. Parts can be manufactured on-site, eliminating time-consuming toing and froing between remote offshore sites and manufacturing centres. Expect to see many more 3D printers onboard ships and rigs in the coming years!
In May 2021, Vallourec and TotalEnergies announced the first installation of a WAAM-3D-printed waterbushing (a device that blocks hydrocarbon surges from wells during their construction)
in the North Sea. Shell has been using 3D printing to create spare parts, for instance, clamps to repair leaking pipes, on demand. Chevron used eight nickel-alloy parts 3D-printed by Lincoln Electric to help bring a petrochemical refinery back online. Equinor announced a collaboration with Norway’s Korall Engineering to produce 3D-printed parts, while ExxonMobil asked AML3D (Australia) to design and 3D-print a metal pressure vessel using the direct energy deposition (DED) process. AML3D is also behind what is thought to be the world’s largest oil & gas piping component. The manufacturing process was hybrid, using its Wire Additive Manufacturing (WAM®) process, which is derived from DED and combines an electric arc with certified welding wire.
The Dutch company MX3D has 3D-printed several parts for the oil & gas industry, notably a WAAM-produced pipeline repair clamp in carbon steel; and heat sinks, propellors, hollow impellers and pipeline fittings in various grades of stainless steel. The company works in 308L, 308LSi, 316L, 316LSi, ER2205 duplex, ER2209 duplex, 410 and other grades.
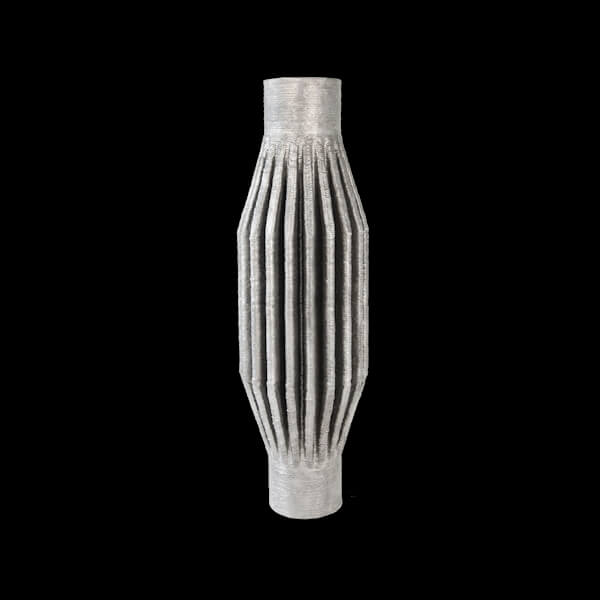
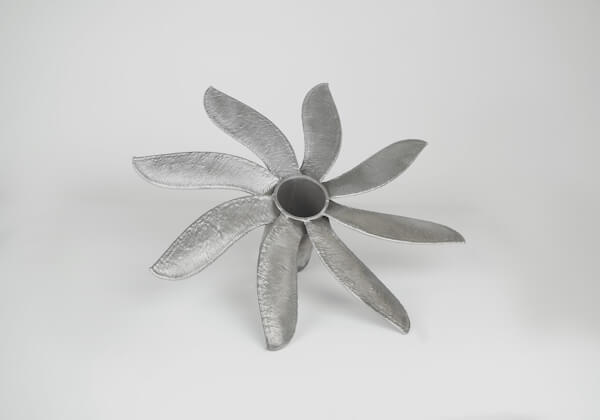

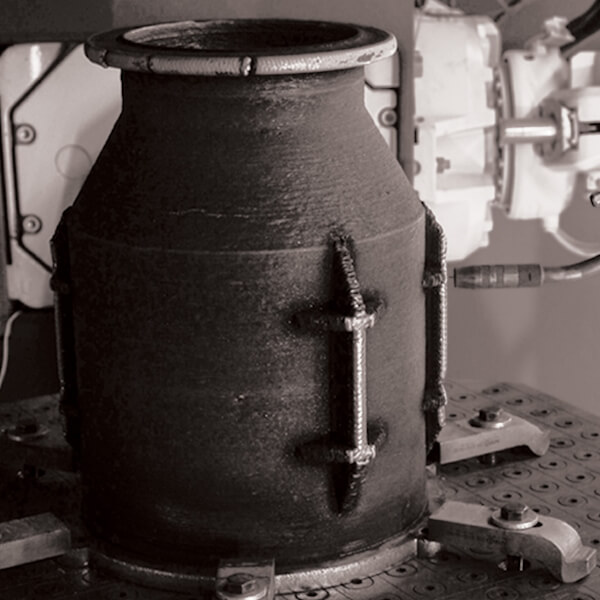
MX3D has 3D-printed several parts for the oil & gas industry. Shown here are (1) a heat sink and a (2) a blade propellor, both in 308Lsi); (3) a hollow impeller and (4) a pipeline fitting, both in 316L. Photo © MX3D.
Materials
The last 12 months have seen an upsurge in orders for oil & gas components and some innovations in what is considered a fairly conservative market.
Duplex pipe has been at the forefront, with a record-breaking project in Oman that installed a total of 120km UNS S31803 line pipe in a 34m gas pipeline, flowlines and manifolds! Duplex was also used in two orders of pumps delivered by Amarinth to the West Qurna-2 expansion project in Iraq. The first order was for seven super duplex API 610 OH1 pumps for a low shear application; the second, for three super duplex API 610 OH3 vertical in-line pumps for produced water treatment.
Umbilicals have been in great demand, Alleima having supplied them for an offshore project in Brazil. Tubacex has positioned itself to supply its products for umbilicals in North Sea fields by setting up TSS Norway. Aker supplied Eni with umbilicals for the Agogo field development located offshore Angola, the tubes being made by Tubacex. OCTG tubes, used in drilling, are in such high demand that Tubacex is building a new tube and thread finishing plant in Abu Dhabi to serve the Middle East. In addition, Alleima received two orders for OCTG tubes in CRAs, the fruit of its partnership with Tenaris.
The oil & gas industry has inspired two new alloys in the last year. N’GENIUS, based in the UK, has rethought the austenitic series in a bid to exceed in strength the traditional 300 series in line-pipe grades and CRA OCTG products. Schoeller Werk has introduced longitudinally welded tubes made of alloy 825 CTP/2.4861, a fully austenitic nickel-iron-chromium alloy. It is derived from VDM® Alloy 825, with higher molybdenum and copper content. The result is a better PREN, making it more resistant to chloride-induced pitting and crevice corrosion in seawater. CTP stands for Corrosion, Temperature, Pressure.
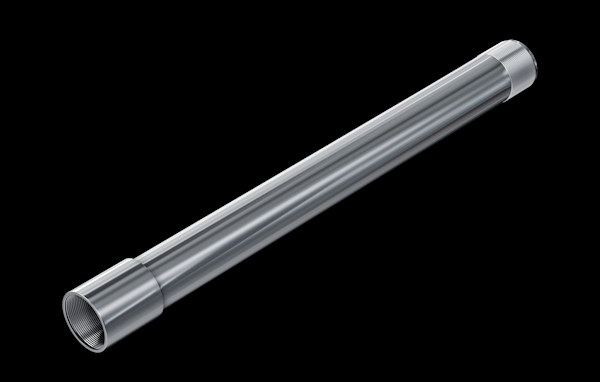
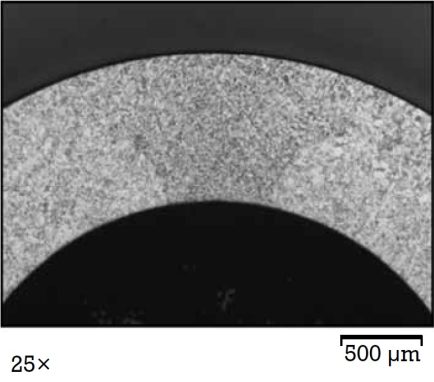
About this Featured Story
This Featured Story appeared in Stainless Steel World December 2023 magazine. To read many more articles like these on an (almost) monthly basis, subscribe to our magazine (available in print and digital format) – SUBSCRIPTIONS TO OUR DIGITAL VERSION ARE NOW FREE.
Every week we share a new Featured Story with our Stainless Steel community. Join us and let’s share your Featured Story on Stainless Steel World online and in print.