Q: MMA welding or ‘stick’ welding has been around for over 100 years. What has changed in recent years? With all the developments in MIG and TIG arc equipment for solid and cored wires, why does it still represent a credible welding process?
A: This is a great question, and it’s interesting to go back in history and look at the origins of the process. Around 1892, Nikolaj Slavianoff used bare iron rods for arc welding, and these acted as both electrode and consumable. The process was known as “iron soldering.” As you would imagine, melting iron rods with the arc interacting with the atmosphere produced a lot of oxides; the quality of the welds was very poor, and they had limited mechanical properties.
In 1900 in Sweden, Oscar Kjellberg used the iron soldering method to repair ships’ boilers. To improve the welding characteristics and the quality of the weld metal, he covered the steel electrodes with a mixture of sodium silicate, carbon powder, and calcium oxide and ‘glued’ the mixture together with cellulose.
The result was that when the welding arc melted the coating, it produced a gas cloud; the cloud enveloped the arc and the molten weld metal to keep out the oxygen. No oxygen means no oxidisation, so the resultant welds were immediately of a better quality with inherently better properties. In addition, the solid components of the melted coatings formed a slag which floated on top of the weld and then solidified. This assisted in protecting the cooling weld metal from the atmosphere. The slag also supported the weld puddle, enabling out-of-position welding.
The first variable current arc welding machines were available in 1907. They were heavy transformers with large amounts of copper windings (Figure. 2). Nowadays, professional inverter-based welding machines can weigh less than 10 kg and have advanced controls to improve MMA performance.
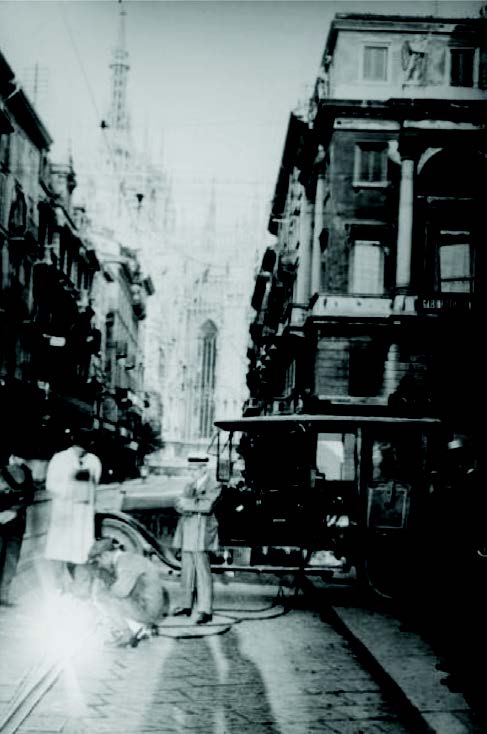
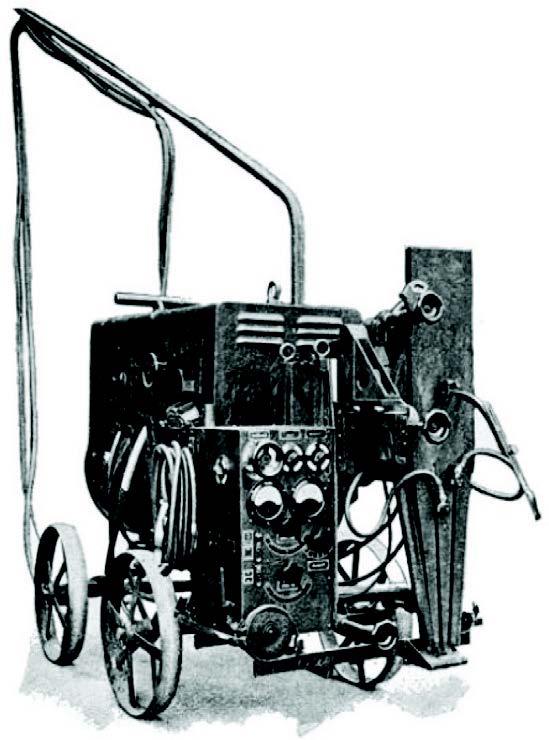
Growing range of options
To this day, the basic process of MMA welding remains the same, but the range of electrode grades available is much wider. Modern, high-quality electrode grades are specifically developed to be welder friendly with easy arc strike, low spatter, easy slag removal, a fluid weld pool and a flat bead profile. Electrodes are now available for every requirement — joining, cladding, hard facing, repairs, etc. — and in almost every grade: high alloy grades, super-austenitics, the duplex family, nickel-based grades, low alloy, low hydrogen, aluminium, cast iron and copper. There are some grades of electrodes available that have mechanical properties of the weld metal that are comparable to solid wires. Some of the newest developments include B2 SC and B3 SC electrodes, respectively developed for welding creep-resistant 1.25% Cr, 0.5% Mo alloyed steels (Grade P11 and similar) and 2.25% Cr, 1% Mo alloyed (Grade P22 and similar). The new formulations are designed for applications that require high toughness in the post-weld heat treatment, as well as after step cooling treatment. The weld metal is also designed for increased rupture resistance at high service temperatures. Filler metal chemistry is carefully controlled so that weldments have a maximum X-bar (Bruscato Factor) of 10, resulting from a very low level of impurity elements to reduce susceptibility to temper embrittlement.
In another development to help fabricators reduce the risk of hydrogen cracking and porosity, manufacturers of low-hydrogen electrodes have modernised electrode coating formulations to decrease moisture pick-up in high humidity conditions. These electrodes carry an “H4R” designation, indicating less than 4 ml of diffusible hydrogen per 100 g of deposited weld. H4R electrodes have less than 0.4% moisture absorption after 9 hours of exposure at 27°C and 80 percent relative humidity.
Improvements have been made to packaging as well. Vacuum-sealed multi-layer foil packages are now available so that electrodes can be used straight out of the pack without the need for pre-heating or baking. While small (1.5 – 3 kg) vacuum-sealed packages cost more than a large container, they provide a payback by reducing the amount of electrodes discarded and eliminating a potential source of hydrogen cracking and porosity. Welders working in situations where rain can contaminate electrodes need to be very conscious of using fresh electrodes. Smaller electrode packages ensure better integrity in adverse conditions, plus they save trips to the rod oven.
To summarise:
The MMA welding process has been around for over 100 years and is here to stay.
- It has very low entry-level costs, the arc machines are lower cost than any other power source and they can run from a generator.
- The process is very portable. No shielding or purging gas is needed, particularly useful whilst on site.
- It is very flexible; every welding position is possible with the correct electrode selection.
- Huge range of available electrodes for every grade, welding operation and final properties. Developments and improvements to the range are ongoing.
- The advanced, modern arc machines have many properties to make welding easier.
- It is usually the process that every welder starts to train with, so there is a lot of experience out there.
Should you have any queries about any of the above, please drop me a line.
Peter Stones
IEng MWeldI IWE/EWE
As part of the ESAB Specialty Alloys Group, Peter is technical support for stainless and nickel alloy filler metals. Peter is actively involved with TWI and is a non-executive director of The Welding Institute. Peter worked for Sandvik for 10 years and was Global Product Manager for Sandvik Welding up to 2018, when ESAB purchased the filler metals business.
Email: peter.stones@esab.com