Large-scale 3D metal printing company MX3D has successfully produced a structural connector in duplex stainless steel, designed in collaboration with engineers from Takenaka, one of the largest architecture, engineering, and construction firms in Japan.
Text & images by MX3D/Takenaka
This project demonstrated the progress in producing highly customized and engineered steel connectors using robotic 3D metal printing, i.e. Wire Arc Additive Manufacturing (WAAM). Destructive and non-destructive testing on a series of printed duplex steel connectors shows a strong and consistent performance of mechanical and material properties. The successful tests are a crucial step towards certification of the structural connector, which parties intend to use for innovative building projects.
Innovative infrastructure
In 2019, Takenaka Corp. and MX3D initiated a collaboration to explore the possibility of robotic WAAM technology to produce large customized steel connectors for the infrastructure industry. The project’s goal is to automate both the design and production of complex connectors for large structures in the building industry. As the complexity of structures increases, skilled labour is scarce and build speed is key, so innovation is required. Following the successful production of the first connector prototype, the collaboration focused on mechanical and material properties testing, a crucial requirement for acceptance by the market.
Rigorous testing

Destructive testing on a series of printed structural connectors showed strong and constant mechanical and material properties, paving the way to certification. Tensile tests, fatigue tests, and buckling tests performed on the connectors showed convincing results. CT scans revealed the interior was dense and solid. Moreover, compressive failure tests confirm the clear effect of mortar filling on buckling resistance and ultimate strength. A 4mm-thick connector filled with mortar has approximately the same strength as an 8mm-thick connector (2.2 kN vs. 2.3 kN resp.), reducing the material required by 50% and making the freedom of form that 3D metal printing offers even more advantageous. The material properties and mechanical testing achieved desired specs and consistency, establishing the relevance of robotic 3D printing to the industry.
Duplex: the ideal material
The initial prototype series of connectors was printed in duplex stainless steel. The alloy is renowned for its good mechanical properties and excellent corrosion resistance, ideal for structural applications. The hollow steel structure filled with concrete is highly effective and economical for safety performance. The other steel bears bending and tensile forces and the inner concrete core delays or prevents local buckling of steel.
Researchers from Takenaka Corp. used information from the physical testing of material specimens to generate a FE simulation model and assess the connectors’ mechanical behaviour. These results were then tested against the real-life behaviour of the connectors undergoing compressive load. The results provided by the simulations were very close to the behaviour shown during the mechanical tests. Furthermore, tensile strength tests showed a highly consistent pattern, required for architects and engineers to include this technology in their tool kit. The full research will be published soon. Following the successful fabrication of the optimized and printed structural steel connectors and the strong test results, the partners involved intend to implement the bigger version(s) in an actual building project.
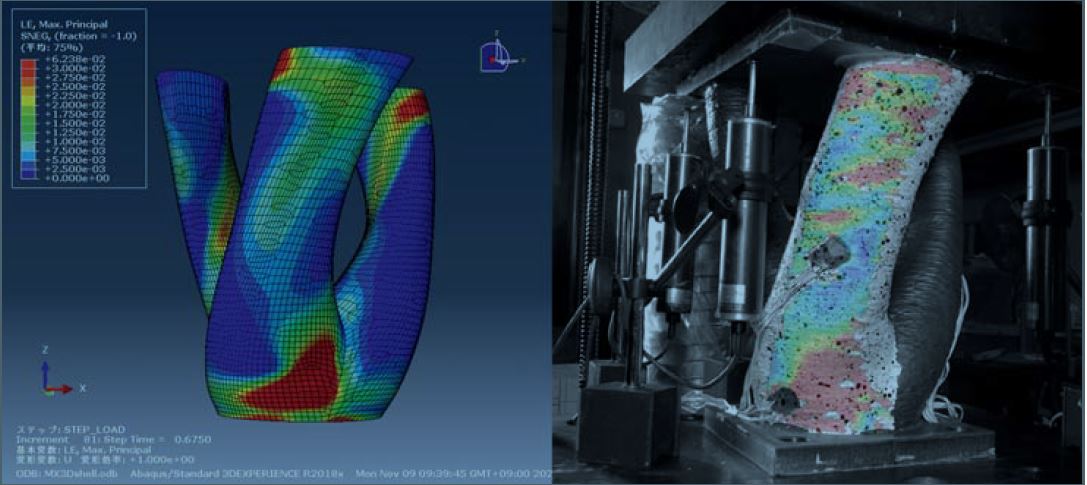
Opening up AM use in construction
Closing the digital design loop is key for the architecture, engineering and construction industry. The MX3D robotic WAAM technology used to produce these connectors allows for full digital control over the design, production, timeline and cost with logistic benefits and integration with BIM applications. MX3D’s MetalXL now enables fabricators to quickly start 3D metal printing large-scale metal applications in their own facilities.
The strong mechanical and material results from the research project confirm the relevance of robotic 3D metal printing for architecture, engineering and construction and open up a new generation of structural connections for the AEC industry.
Every week we share a new Featured Story with our Stainless Steel community. Join us and let’s share your Featured Story on Stainless Steel World online and in print.
Featured Story by: MX3D/Takenaka
All images were taken before the COVID-19 pandemic, or in compliance with social distancing.