Tim di Maulo, Aperam CEO
SSW.– Mr di Maulo, in 2020, EcoVadis, a leading business sustainability rating index, gave Aperam a Gold rating, placing you within the top 5 % of companies globally. You earned a Management level label from the Carbon Disclosure Project (CDP). Last September, you were certified to be operating at the ResponsibleSteel™ Standard, the first stainless steel producer to reach this certification. Why has Aperam chosen this way, and how?
Timoteo di Maulo.– It is simply a matter of looking ahead for our industry, as well as for our children and our planet. We have a strong focus on H&S and develop social programmes for our employees to continue recommending us as a good employer. Besides, Aperam has been committed to environmental responsibility since its creation. It is rooted in our DNA, and part of our business model. We have taken many important initiatives, and are reaping much success from them. Our FSC®-certified forest in Brazil allows us to produce sustainable charcoal, which fuels our blast furnaces. And of course, on a strictly industrial level, renewable resources are our main production method and we intend to maximise them further. On this specific topic, we have taken our Greenhouse Gas Emissions (scope 1+2) to less than half of the stainless steel industry, and 82 % less than the global steel industry. We have already cut these emissions dramatically in the past. Compared to 2015, we gained another 20 % on our scope 1+2 CO2 footprint and aim to achieve a total 30 % CO2 reduction by 2030, before becoming carbon neutral by 2050.
SSW.– With the acquisition of ELG, you seem to be moving towards recycling. What does this mean in environmental terms?
TdM.– Stainless steel is sustainable. It is a 100 % recyclable material without loss of quality. But the use of scrap becomes key if we are to minimise the CO2 emissions created in production, limiting our need for primary alloys. The European stainless industry already recycles intensively, and is head and shoulders above the Asian exporters. For example: the EU average is 2.2 tons of CO2 per ton of stainless steel produced, versus 12 tons in Indonesia. This is due to our input in Europe, which is already more than 80 % recycled scrap. Aperam is fully committed to optimise that. We have founded Recyco, our recycling unit, which recovers and treats the metallic content from melt shop dust for reuse. This reduces the need for waste landfill as well as for extractive and high environmental impact raw materials. ELG is now part of this recycling business unit, moving us towards a business model based entirely on circular economy principles. Our endeavours bring stainless steel producers closer to our processing customers, so that we can better sort and maximise collection, and close the loop with renewed production. More generally on the environmental side, we will also keep on disrupting the industry and making progress in other areas such as energy and water use with ambitious 2030 reduction objectives.
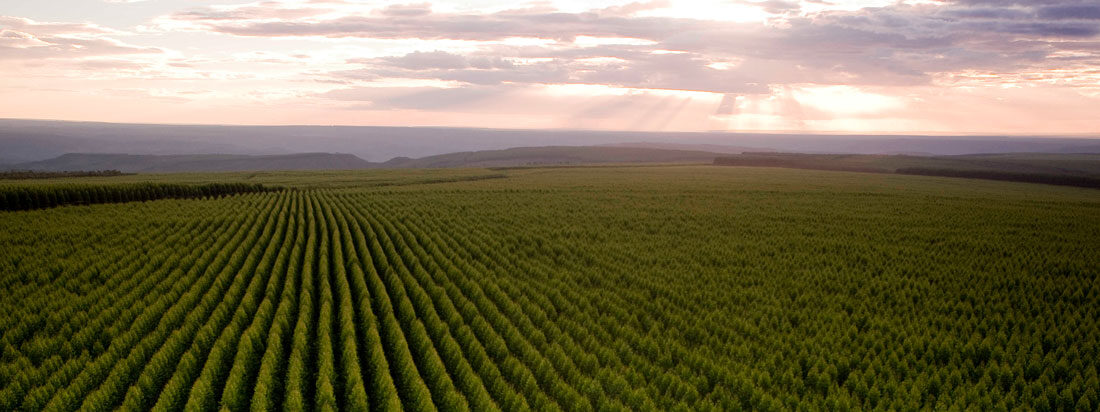
SSW.– Has this shift towards sustainability changed your business approach? With the acquisition of ELG, Aperam no longer seems to be simply a stainless steel producer…
TdM.– With the inclusion of ELG, Aperam will have about 30 % of its workforce creating value from working in the renewable, regeneration and recycling upstream market. The recent reconfiguration of the geopolitical and economic context makes it increasingly important to use local and circular resources – and confirms that respect for all stakeholders is key to living a desirable future.
At group level, our market offer has also expanded. More than 25 % of our profits will soon stem from sectors other than traditional stainless steel (where we intend to stay best-in-class). The important thing to remember about our efforts is that we don’t just produce stainless steel, we also provide solutions to accompany the transformation of our collective way of life. We create tailor-made products for clients in the renewable sector to speed-up energy transition. We support the progress made in energy storage, particularly with hydrogen-related products.
And in e-mobility, our expertise helps greatly in the manufacture of batteries for the vehicles of tomorrow. We intend to be a driving force in all these areas and help these megatrends shape our future.

SSW.– What are the other critical levers to make Aperam’s ambitions a reality?
TdM.– I would add that ultimately, our company is all about its people. Those who work for and with Aperam represent its heart, its strength and its purpose. Our first challenge is therefore to guarantee complete safety for our people, who lead the change towards sustainability on a daily basis. This takes precedence over everything else, including efficiency and costs.
With that in mind, it is gratifying that we have achieved so much in this field over the last few years. Our lost time injury frequency rate is half that of the stainless steel industry, and keeps going down. While we have a long way to go towards reaching our zero-accident objective, our ambitions remain high as we aim to constantly outperform our sector average. But it goes beyond that. We also thrive on employee satisfaction as a whole. 86 % of our people recommend Aperam as a good place to work, placing us among the top employers in Brazil and France! We encourage local development, for example via our Aperam Acesita Foundation, through which we promote the training and support of communities where we operate in South America with activities in education, culture, environment and social promotion. Caring and doing all we can for our employees and their families is rooted in our DNA.
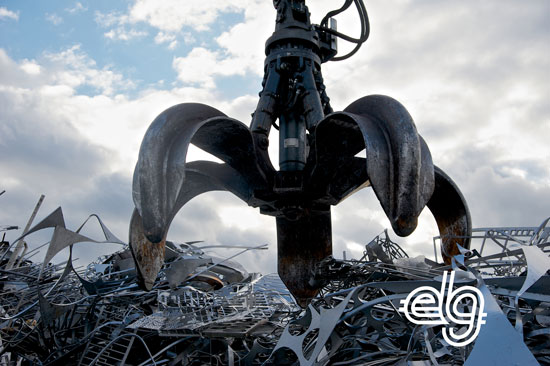

ELG Acquisition: a big push towards recycling activities…
It was news that caused a big stir in the steel sector: last December, Aperam announced it had completed the acquisition of ELG, a world leader in the recycling of stainless steel and superalloys. ELG specialises in the collection, trading, processing and recycling of stainless steel and high performance alloy scrap, with approximately 1.2 million tons of material per year, employing about 1,200 people on 51 sites in 20 countries. Investing sustainably in recycling improves Aperam’s leading position in terms of environmental footprint and serves its CO2 reduction objectives. The CEO of ELG, Donald Weir, commented on the acquisition: “We are very pleased to join the Aperam Group and look forward to continuing to create value for all our customers. ELG will benefit from Aperam’s industrial facilities, which will provide new opportunities for growth and innovation. Together, we will be able to set up an innovative circular economy model in the stainless steel sector.”
From scrap to steel… to scrap again!
“We are combining our work on CO2 emission reduction with efforts to improve the circular economy of our business. Scrap recycling and waste valorisation are key actions we are looking to improve year by year”. This statement by Laurent Piranda, Global Head of Environment and Industrial Risk, tells it all. The acquisition of ELG in December places Aperam at the heart of the circular economy. Through ELG, Aperam stainless steel will be produced using exceptionally high levels of scrap (more than 90 %). Customers will benefit from knowing that the stainless steel they purchase from Aperam has the lowest CO2 footprint.
To expand on this, although many of the products our customers produce have very long lifespans, eventually, the stainless steel becomes scrap. And when it does, ELG is there to collect and reprocess it into raw materials. Aperam then uses this raw material to produce the stainless steel that our customers transform into their end products. From scrap to stainless steel and back to scrap again, the cycle continues, ultimately creating the sustainable world our future demands.
Steel or… carbon producers?
Not all stainless steel is created equally… And its users should know it. Worldwide, the majority of producers use nickel pig iron and other ferro alloys to create the main input materials. Producing these requires a significant amount of energy, which is generated by burning coal. This production process results in high CO2 emissions and large amounts of residual waste. By comparison, European stainless steel is produced from scrap – up to 90 % for Aperam – melted in electric furnaces. This process results in a much lower level of CO2 emissions and has a minimal environmental impact. What this means is that whenever stainless steel is brought into Europe, a significant amount of carbon emissions are generated on the other side of the planet and delivered as an indirect import. This has the effect of increasing the overall CO2 footprint of the European industry and that of its end-consumers and citizens, countering efforts to decarbonise locally.
To put this into context: at the end of May 2022, European countries had imported 873 kt of stainless steel, which generated 6.9 million tons of CO2 (scope 1+2+3a). If the equivalent volume of stainless steel had been produced at Aperam’s European plants, it would have saved 5 million tons of CO2 on the same scope.

“Carbon calculator”, EPDs: raising awareness among (demanding) market players
The CO2 emissions associated with stainless steel production are becoming ever-more important as a guide to purchasing, and in enabling customers to make informed choices. That’s why Aperam has taken leadership in this area by recently launching its “carbon calculator” to provide information to others in the market about the real environmental impact of imported stainless steel flat products.
The calculator quantifies the level of CO2 emissions linked to different imported materials. Its calculation is based on Aperam’s knowledge of the processes used by stainless steel producers worldwide. Providing a monthly and a year-to-day value of imported CO2, this index also highlights how much CO2 would have been saved, had the imported material instead been produced in Europe by a sustainable means of production.
Aperam has long been an industry leader in embracing sustainable development. A commitment that does not stop at its own performance, but also aims to move the whole market forward. In addition to the “Carbon Index”, the company uses Environmental Product Declarations
(EPDs) to communicate the environmental impact their products have across their lifecycle – including total carbon footprint as well as water and energy used throughout the supply chain.
Based on an independently verified lifecycle assessment, these EPDs help customers calculate the environmental impact of their own application’s lifecycle. This last point can be of particular interest to the building and construction sector when working under a ‘green building’ regulation. But regardless of sectors, all customers are increasingly demanding, and concerned by the true environmental balance of the products they process. This trend is supported by the regulators and, of course, by the end customers. Aperam is fully involved in this process. With the information the company provides, customers can ensure that their stainless steel suppliers are both efficient and sustainable. It also allows them to specify the material’s country of origin on their own products and solutions, giving them a unique competitive advantage.

ResponsibleSteel™ Certification: evidence of commitment
Last but not least, in September 2021, Aperam was the first stainless steel producer certified to be operating at the ResponsibleSteel™ Standard by the independent auditors AFNOR. The ResponsibleSteel™ initiative is the first global sustainability certification programme for the steel sector and its certification follows a stringent audit of the company’s practices. The announcement followed an in-depth third-party audit of European operations. Tim di Maulo, Aperam CEO, said at the time: “It is reassurance to our stakeholders that we produce responsibly. With Aperam, our customers have selected a partner of choice, offering them responsibly produced solutions that are also 100 % recyclable and low carbon – solutions that are much needed for the sustainable society we strive to live in”.
Every week we share a new Featured Story with our Stainless Steel community. Join us and let’s share your Featured Story on Stainless Steel World online and in print.