Chemical plant for production of ammonia and nitrogen for fertilization.
Duplex is improving in many different senses. The addition of new grades, especially in lean, hyper-duplex and super-duplex, means that end users are more likely than before to find a grade exactly tailored for a given application. Better fabrication and welding properties, especially in 3D printing, allow massive and stress-bearing objects to be made in less time and at a lower cost. Duplex is also improving the processes and products it serves, bringing higher quality, lower maintenance and longer life.
By James Chater
After World War II, Japan underwent an industrial revolution based on the concept of kaizen, or “continual improvement”. Something similar has happened in the field of duplex stainless steel, where continual improvement has led to an expansion of duplex’s share of the stainless steel market, as more and more applications are served by a continually expanding portfolio of niche grades.
The use of duplex stainless steel is increasing in several industries, driven largely by tougher corrosive environments in the oil & gas and petrochemical sectors, high growth in Asia Pacific and technological developments in the field of fabrication and 3D printing. In this article, we look at some of the sectors that are fuelling this growth.
Outlook

Like the stainless steel market, the duplex sector is expanding fast. According to a recent survey, worldwide demand is estimated at USD4.4 billion in 2024 and is projected to reach USD6 billion by 2030, at a CAGR of 5.4%. Construction, oil & gas and petrochemical will account for most of the growth. (The “Duplex Stainless Steel – A Global Market Overview”, Global Newswire, 19 November 2024).
In North America, Mexico is an especially dynamic market for duplex because of its growing automotive, oil & gas and petrochemical industries. However, no country has grown so dramatically as China, where in 2023 output stood at 393,400 tonnes compared to just 828 tonnes in 2005. Duplex’s share of the country’s stainless steel output has also risen, from 0.1% in 2005 to 1.07% in 2024, with a CAGR of 21.4% between 2019 and 20231. (It should be noted that this optimistic projection predates the US presidential election and is likely to be affected by the tariffs on US imports – including 25% on all steel and aluminum – that will come into effect in March.)
Two major trends affect the high-end (super and hyper duplex grades) and the low-end (lean grades). Super- and hyper duplex are among the fastest-growing segments, because of the increased demand for materials that withstand extreme environmental conditions in the oil & gas, petrochemical and desalination industries. Meanwhile, lean grades are replacing austenitics in certain applications, because of their superior corrosion resistance and lighter weight, which can result in material and cost savings.
Just over a quarter of all output consists of tubes and pipes, followed by pumps & valves, fittings & flanges, welding wires, rebar & mesh, and others.
Sectors
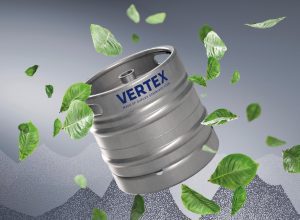
The primacy of tubes & pipes reflects the fact that the largest market is oil & gas, with an estimated share of 34% of the total in 20242. Despite the so-called “energy transition”, production of liquid fuels is predicted to increase by 1.9 million barrels per day (b/d) in 2025 and 1.6 million b/d in 2026 (EIA figures). This production is likely to be sustained by the presence in the White House of a climate-sceptical US president who is in favour of expanding operations that were off-limits to the Biden administration.
Duplex grades are being increasingly used in critical applications such as umbilicals, valves process piping and heat exchangers. At the end of 2023 Alleima reported two major orders
in this segment, one for tubes and umbilicals (for an offshore project in Brazil), the other for corrosion-resistant-alloy OCTG tubes. More recently, Petrobras ordered from Tubacex CRA OCTGs for its offshore developments. Two further examples are GD Engineering’s QOCs (Quick Opening Closures), used on FPSOs to quickly access pipelines and pressure vessels, which are made of super-duplex because of the favourable strength-to-weight ratio, crucial on floating vessels; and Oliver Twinsafe’s 12″ Class 1500 super-duplex valves, specified for the Shell Jackdaw platform in the North Sea, which are specially built to withstand the extreme conditions of the North Sea and therefore of outstanding size and complexity. A third example is the massive Gas Production Swivel Inner Part on Shell’s Prelude FLNG, forged in duplex and weighing 14,500 kg.
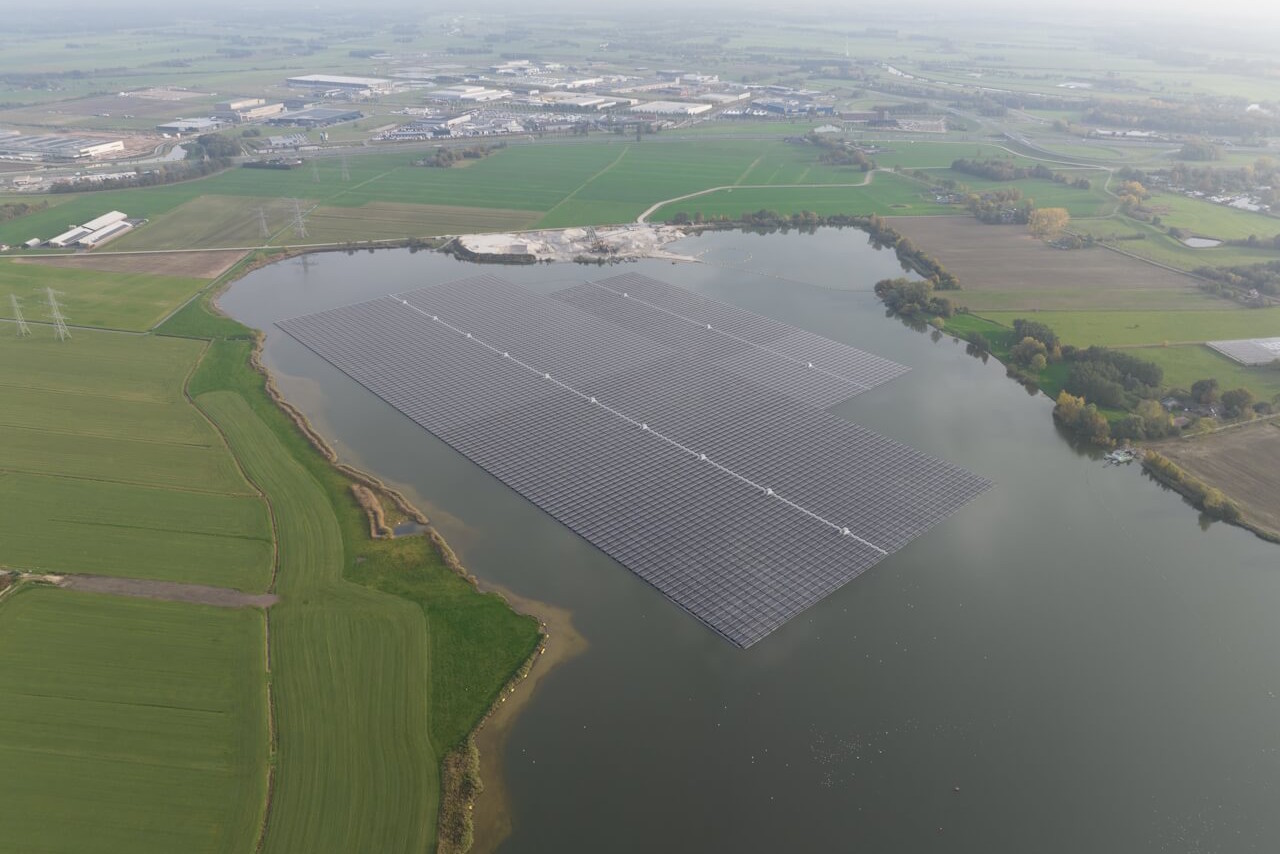
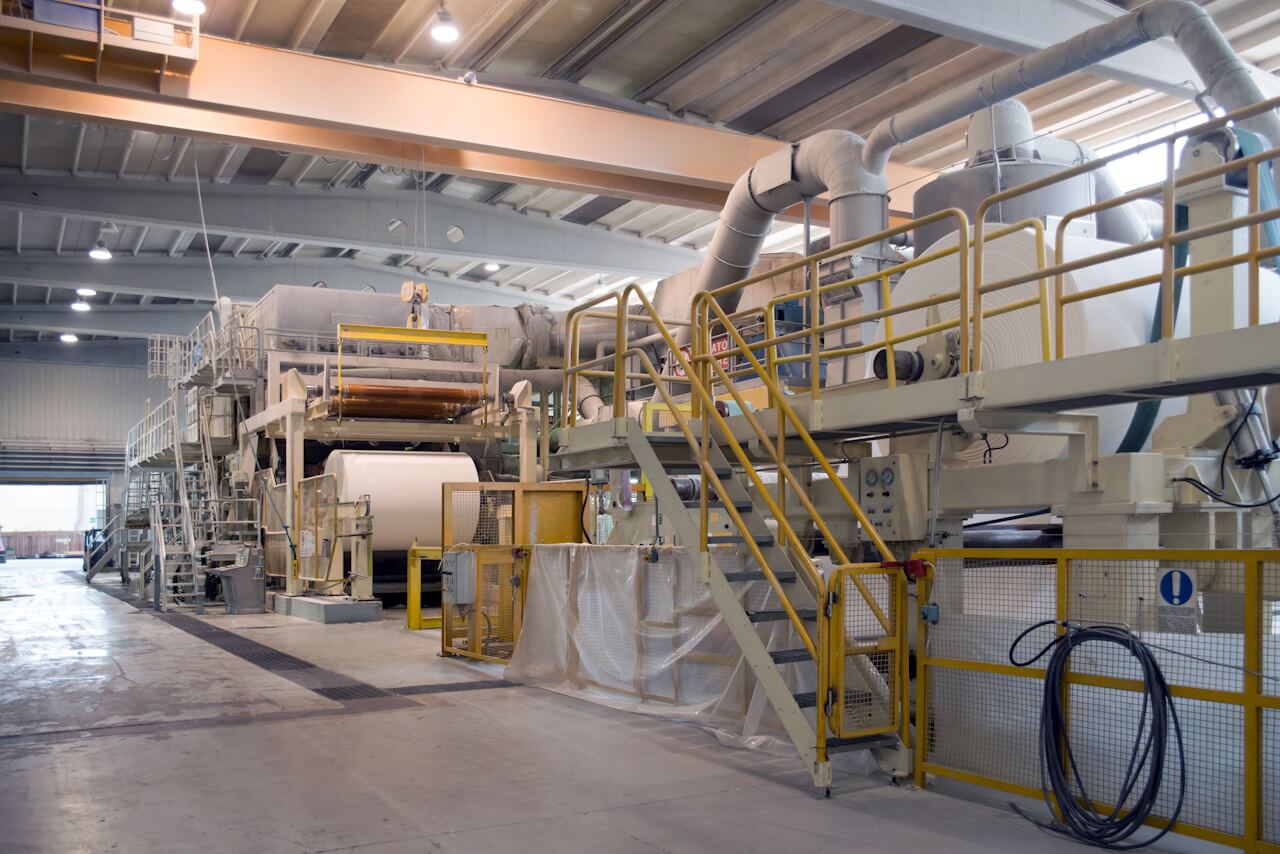
Apart from offshore oil and gas, many other marine structures require duplex, including floating solar installations and offshore wind farms, to cope with salt corrosion, sand erosion and rough seas.
Chemicals and petrochemicals are other dynamic industries in which duplex plays an important role. East Asia (especially India and China), the Middle East, and the USA are thriving markets. In East Asia, Stamicarbon is supplying its proprietary fertilizer technology to numerous projects, including a new high-pressure (HP) stripper for Mangalore Chemicals and Fertilizers in India, an upgrade of New Gold Chemical’s urea plant in Hulunbuir, and the new build of a similar plant in Zhangjiagang City. Super duplex is systematically applied in urea manufacture. In the 1990s Stamicarbon developed Safurex®, developed in partnership with Sandvik (now Alleima), to provide resistance to active ammonium carbamate corrosion, chloride-induced stress corrosion cracking and other challenges unique to high-pressure urea synthesis equipment. This broadened into a family of proprietory super duplex grades known as E-type material for urea, ammonia and nitrates applications. These materials are used in strippers, condensors, HE tubes, plates, bars, flanges, fittings, piping, valves, couplings, welding consumables and more. They offer longer life, lower weight, increased HE surface area, lower maintenance and other advantages. The severely corrosive conditions of heat exchangers induced Alleima to develop SAF™ 3006. This super-duplex grade, with 7% nickel, 30% chromium and 3.2% molybdenum, is especially designed to handle acidic and caustic environments. It is an upgrade from grade 2705, which has proved able to resist stress corrosion cracking in chloride conditions. The new grade is designed to provide better resistance to hydrochloric, sulphuric, formic or other acids and is intended, above all, for seamless heat exchanger tubes. Another appplication where duplex is important is the construction of double-hulled chemical tankers. Again. it is East Asia that is leading the way: in China, Xin Jiangzhou Shipbuilding Heavy Industry is making its debut as chemical tankers builder with orders for four vessels from Singapore-based MAC.
Pulp & paper is another industry where corrosive chemicals are used. Growth of about 1.41% per years is expected between 2025 and 20293. Decline in demand for newsprint has been more than offset by demand for packaging (much of which, ironically, derives for E-commerce). A number of duplex grades are used at various stages of the manufacturing process. The most common is 2205, used in the digester (where the wood chips are “cooked” under high pressure). The bleaching process (which uses chlorine dioxide solutions, hydrogen peroxide or ozone) and reactors can also use duplex, for example super-duplex 2507 in the piping. Super-duplex is also used in the suction rolls of the fourdriniers, machines through which the paper passes at around 100 km per hour while it is dewatered and rolled.
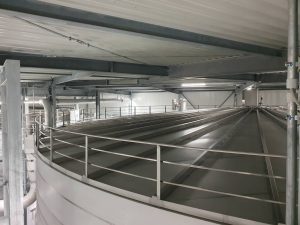
Food & drink is another sector which has transitioned from using only austenitics to increased use of duplex. As in pulp & paper and desalination, it is the combination of corrosion and erosion that is driving this trend. For example, NSSC’s duplex perforated metal was introduced as a stronger alternative to austenitics for sanitary strainers. Longer life, improved buffing and polishing, lower thermal expansion, higher corrosion resistance and strength are among the qualities claimed for this product. Once again, it is East Asia where growth is strongest: the Indian government has approved 41 mega food parks, 376 cold chain projects and 489 proposals for food processing capacity expansion.
Water and desalination are both areas in which duplex has superseded austenitic in more demanding applications. A case in point is the Tateno Dam in Kumamoto Prefecture, Japan which stores water temporarily to prevent flooding. The screens, pipes and gates used in the discharge process require strength and wear resistance, so lean grade SUS821L1 (equivalent to 2120) was applied, even though 304 was the grade originally considered. Similarly, in Stadtwerke’s large drinking water storage facility in Ulm, Germany, grade 2101 was applied for the tank bottoms and lower shell, and a super-duplex grade for the upper section of the shell and the roof to handle chlorine dioxide.
Other examples (from geothermal to biogas, carbon storage and infrastructure) could be cited to show the improvement duplex brings, including longer life, lower maintenance, savings in weight, energy and cost, and more.
Fabrication improvements
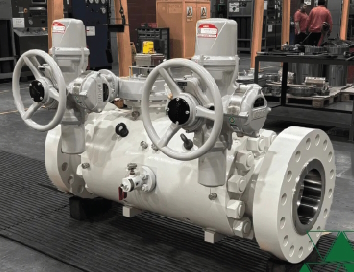
It has been argued that fabrication techniques for duplex are more difficult to master than for austenitics. This is doubtful, and it is fairer to say that the techniques differ and require extra training, which may have been a disincentive in the past. Also, fabrication techniques have evolved to make the use of duplex more worthwhile. Nowhere is this more evident than in 3D printing, thanks to which items such as turbine blades, fuel nozzles and HEs can be made with less wastage of materials and in a much shorter period. Thanks to WAAM, expensive items such as impellers can be made on-site. 3D Metalforge of Singapore is one of a few companies that developed parameters for 3D-printing of super duplex. Other technologies being harnessed to include super duplex include fusion welding, precision casting, laser welding and machining. Swiss Steel Group recently launched its UGIMA®-X 4460 duplex grade to simplify the machining process. Also, Thielmann developed a technique to mould duplex stainless steel for very thin weldings, the result of which is a beverage keg made of super-duplex. It is 30% lighter than traditional kegs, is less likely to cause injury and withstand heavy-duty use over a long service life. Cheers!
About this Featured Story
Appearing in the April 2025 issue of Stainless Steel World Magazine, this Featured Story is just one of many insightful articles we publish. Subscribe today to receive 10 issues a year, available monthly in print and digital formats. – SUBSCRIPTIONS TO OUR DIGITAL VERSION ARE NOW FREE.
Every week we share a new Featured Story with our Stainless Steel community. Join us and let’s share your Featured Story on Stainless Steel World online and in print.