A finished, machined solid titanium agitator shaft for a PTA plant.
Rolf Kind produces large-sized open die forgings for chemical and petrochemical equipment, machinery construction, oil & gas exploration and refineries, and power plants. It manufactures these parts at its state-of-the-art facilities in Germany and ships them worldwide. Stainless Steel World was keen to learn about the global market for these high-end products.
By Joanne McIntyre, Stainless Steel World
“Asia has grown to become our most important market,” begins Markus, “mainly due to significant investments in new-build chemical and petrochemical facilities in the region. By contrast, in Europe and the US there are almost no new-build facilities so the focus is on revamping aging plants. In the past 25 years, companies that formerly imported equipment have developed to building equipment themselves, particularly in South Korea, Malaysia, Taiwan and Singapore. Asian companies are technically excellently equipped to build first-class equipment.”
Purified Terephthalic Acid industry
Purified terephthalic acid (PTA) is the base material for a huge array of plastics. The product is refined in large PTA plants using a complex process. Markus: “This is a very interesting application for us. There are two main PTA plant licensors worldwide: BP Amoco and Invista. Both specify that titanium for critical equipment, such as heat exchangers and agitators. Titanium is the ideal material due to its corrosion resistance, and its mechanical properties which can withstand the high mechanical load on the agitator shafts.”

applications.
“PTA plants contain huge agitators constructed from solid titanium, and we manufacture both the shafts and the mixing equipment. In the past four years, this business has boomed in Asia, and it’s still growing as licensors have focused on top quality products coupled with increased production efficiency. In China, for example, new environmental and energy efficiency restrictions mean operators must completely revamp plants built 10-15 years ago.”
To manufacture the huge agitators required for PTA plants, Rolf Kind processes the largest titanium ingots in the world, weighing up to 15 metric tons. “The shaft flanges have a diameter up to 1100 mm, with a length of up to 13 meters. These massive, solid titanium pieces are highly specialized items that very few companies in the world can manufacture,” Markus explains. “PTA plants also require titanium heat exchangers which can be quite massive. The tube sheets can measure up to 2.5m in diameter and 330-400mm in thickness.”
Polysilicon applications
Markus explains that another important growth area in the SE Asian area is the production of polysilicon.
“Polysilicon is a crystal created during a chemical process at temperatures of up to 840°C, which requires a material that is corrosion resistant under those extreme temperatures. The standard material used is Inconel 800H/ Alloy800H, which contains 32% Ni and 20% Cr. It has excellent properties under these high-temperature conditions.”
Polysilicon is used to produce screens for computers, mobile devices, televisions, etc. “In the past decade, the quality of the crystals produced has become increasingly important. TVs with 100-inch screens demand very pure polysilicon crystals, so the quality demands on the plants have increased enormously. Equipment ranging from nozzles and flanges to heat exchanger tube sheets and piping is all required in Inconel 800H”.

Quality at the heart of the plant
It’s clear that the items produced by Rolf Kind are at the heart of chemical plants. “When a large chemical company builds a PTA plant, they invest up to EUR 1.5 billion, and the agitator shafts are the most critical equipment in the plant. If the agitators didn’t perform correctly, the entire plant would shut down at tremendous loss of production per day. This is one of the reaons why they demand excellent quality. Very few companies can even make these extraordinary products that are very large and very difficult to manufacture. You need deep technical skills to be able to forge and machine such items.”
Increasing demands on equipment
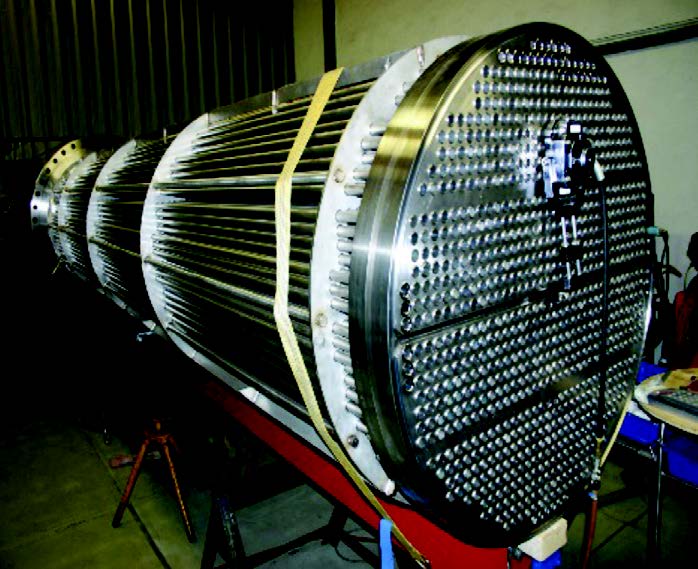
The demands on equipment for the (petro) chemical industry have risen significantly over the past 15 years in terms of size and material grades, explains Markus. “Energy efficiency is crucial now. In the past, customers used to build three different production lines and combine these at the end of the process. Today they want a single, large production line with the same output as three separate lines because it’s more energy efficient. That’s driving demand for larger equipment.” “Secondly, the material requirements are getting higher. Many material specifications were updated after the Deep Water Horizon disaster; extra margins were added for materials, and higher alloyed grades replaced standard materials. This is particularly true for equipment which needs to run for a long time, e.g. up to ten years. On the one hand, we have better control mechanisms and lots of developments for remote-controlled equipment such as underwater testing equipment. On the other hand, customers require more super-critical alloys to be on the safe side. So companies who used to use stainless steel or duplex now tend to use nickel-based alloys instead.”
Looking ahead five years
So how does Markus see the market continuing to develop? “Over the past 18 months, we’ve seen many postponed projects,” Markus explains. “During the pandemic, financing became more difficult to arrange as the market became very conservative and people couldn’t travel and discuss projects in detail. However, equipment must be built to meet increasing demand, plus many plants are waiting to be revamped. In the next five years, we expect the market to be over-busy, which can extend lead times and cause delays.”
“Hydrogen is an upcoming change for the coming 5-10 years, which will be important as the disadvantages of electric-powered cars become clear. In Germany, car batteries built in Asia using raw materials from South America is politically problematic for environmental reasons. Secondly, where does the electricity come from to charge electric cars? In Germany, we have cancelled nuclear power, we don’t want to keep using coal, but we have a sharply rising need for electricity. I think electric vehicles are an intermediate phase. In the long term, new technologies are required and hydrogen will be a key component. This is where big companies will invest in the coming decade.”
Markets outside Asia
Having covered how the Asian market is developing, it was time to hear Markus’ thoughts on how the (petro) chemical industry in other regions is faring.

“In Europe, there is one new PTA plant in Turkey coming up, but otherwise very few major new investments. The industry is focused on renovations of existing plants and gaining energy efficiency. The market, therefore, has different demands, and in particular, shorter lead times. If there is a breakdown, we need to supply good quality material reliably and on time, so the customer knows any problems will be quickly solved.”
“The USA is a little different as it’s a huge market by itself and therefore not dependent on international business. The market is not as price-sensitive as Asia, but it isn’t easy to import forgings because US customers want locallymade products.”
“There is enormous demand in the US market. With many rather aged plants dating back to the 1960s and 1970s, there is a lot of revamping and even new construction underway. I expect this will also include new-build nuclear power plants to reduce CO2 emissions dramatically.”
Evolution of the US (petro)chemical market
The US market continues to evolve, and the landscape is steadily changing, explains Markus.“Asian investors now find it interesting to invest in new-build plants in the US. When fracking drove down the oil price in the US, operators began to look for local refining and processing capacity. For example, the Taiwanese chemical giant Formosa is investing USD 9.4 billion in a chemical manufacturing complex on a 2,400-acre site along the west bank of the Mississippi River in Louisiana.”
”In the Gulf region, Houston and its surroundings are dominated by the oil and gas business. We’ve seen companies such as Saudi Aramco, the largest oil-producing company in the world, investing heavily there. There is also a lot of activity in alternative energy markets, so the classic oil giants will evolve in the next 20 years.”
Unique projects
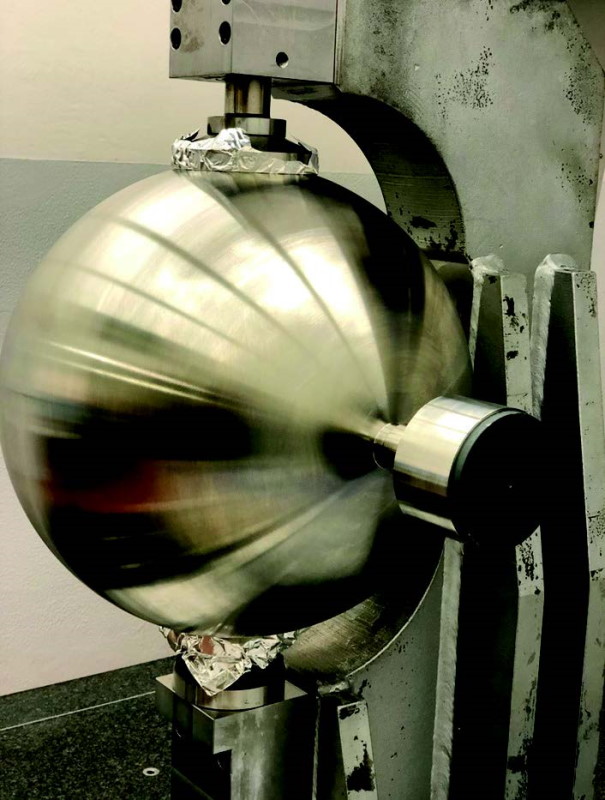
Although the Rolf Kind team produces massive items for demanding applications, occasionally, they are asked to make something a little unique. The LARES 2 project for the European Space Agency is one such example. The 340 kg sphere, with a diameter of 424 mm, was made from the particularly resistant and heavy-tomachine material Alloy 718 / W. Nr. 2.4668 / UNS N07718. The end customer is grinding about 1200 facets into the sphere, which will serve as a ‘laser mirror’ to passively study the earth’s gravitational field. “It was a very exciting project and is the first item we’ve produced to go into space.” Another example is an enormous forged valve housing made for a US company and destined for use in an oil field near Belarus. “The housing was for a Blow Out Preventer valve on the seabed and is one of the largest forgings we’ve ever produced. It was tested under 700 Megapascal pressure, made from solid Inconel 625 and forging weight 14,5 tons.”
About Markus Kind
Markus Kind is the Commercial Managing Director of Rolf Kind GmbH. Markus has finished his studies as Master of Business Administration (MBA), Bachelor of commerce in Cologne in 2002. He entered into the family business in 2005 and took over the lead of the company together with his brother Ralf Kind (Technical MD) in 2014. Markus in responsible for International sales and the development of the company into the global markets.
Rolf Kind sponsor of Stainless Steel World 2022
Rolf Kind is a sponsor of the Stainless Steel World Conference & Exhibition which will be held in Maastricht, the Netherlands, 27th – 28th September 2022. Meet the team and pose your questions to their experts! https://stainless-steel-world-event.com/
Every week we share a new Featured Story with our Stainless Steel community. Join us and let’s share your Featured Story on Stainless Steel World online and in print.