UREMIUM29 is a super duplex stainless steel specifically designed for use in the most demanding high-pressure sections of urea plants, such as the stripper. This vessel is characterised by very harsh operating conditions due to the combination of high temperature and pressure and a highly corrosive environment with ammonium carbamate.
UREMIUM29 has shown excellent resistance to this corrosive medium. High mechanical strength is another important advantage of this material compared to other austenitic materials. Its superior performance make it an excellent candidate for use in various urea plant applications.
By B Calleja & A López, Tubacex Innovación AIE, Spain

The corrosion of stainless steel is a recognised problem in the high-pressure section of urea plants. The stripper is the most critical equipment in the urea process. The function of a stripper is to remove unconverted ammonium carbamate from the urea solution. Working pressure and temperature range within 140-200 bar and 180-210°C, respectively. High temperature, high pressure and the presence of ammonium carbamate make the conditions in the urea stripper extremely harsh. Preventing corrosion in the stripper is crucial to guarantee urea plants’ safe and stable operation.
TUBACEX supplies tubes, pipes and special products in several corrosion-resistant materials for urea plants: high Cr-high Ni-Mo austenitic stainless steels and various types of duplex stainless steels. An example of manufactured stripper tubes is presented in Figure 1. UREMIUM29 (UNS S32906) is an austeno-ferritic stainless steel with 29% chromium, with very high resistance to carbamate-induced corrosion, recommended for the tubes of high-pressure equipment.
Excellent corrosion performance
UREMIUM29 and other steel grades that can be applied in different sections of a urea plant were tested in an experimental setup specially designed to simulate the highly corrosive conditions of a urea stripper. During the tests, oxygen was eliminated from the experimental setup due to the current tendency to decrease O₂ levels to reduce costs and increase plant efficiency and safety. Therefore, the atmosphere generated inside the autoclave was even more severe than in real strippers, as most active urea plants work with oxygen injection.
The main objectives of this study were to identify the basic mechanisms controlling corrosion in urea synthesis process and to establish the relationship of these mechanisms with the chemical composition and the microstructure of the tested steels.
Five different materials were investigated:
- UNS S31050: 25Cr-22Ni-2Mo austenitic stainless steel.
- UNS S31803: 22Cr-5Ni-3Mo duplex stainless steel.
- UNS S32750: 25Cr-7Ni-4Mo super duplex stainless steel.
- UNS S32760: 25Cr-7Ni-3.5Mo-0.75W super duplex stainless steel.
- UREMIUM29 (UNS S32906): 29Cr-7Ni-2Mo super duplex stainless steel.
The immersion tests were conducted in a five-litre Zr autoclave. The test solution contained a mixture of urea, ammonia and water. Temperature and pressure for the experiments were set in the upper level of the typical ranges in a stripper. The solution was de-aerated before starting the tests. Test duration was 15 days. ASTM G31 (Standard Practice for Laboratory Immersion Corrosion Testing of Metals) standard indications were followed for specimen preparation and corrosion rate measurement using the gravimetric method. The corrosion rate and measured depth of attack for each studied steel are summarised in Table 1.

UREMIUM29 clearly shows the lowest corrosion rate and attack.
Lowest corrosion rate
Figure 2 depicts the cross-sections of the test specimens after 15 days of immersion in the autoclave. Considering the measured corrosion rates and the metallurgical investigation, the following aspects can be highlighted:
- UNS S31050: with the highest corrosion rate, experiences a uniform attack. The high corrosion rate is related to the absence of oxygen, which avoids attaining stable passivation in this austenitic grade. UNS S31050 is currently established as a successful material for urea, as its corrosion rate when oxygen is present is very low.
UNS S31803, UNS S32750 and UNS S32760: the corrosion rate of these duplex stainless steels is less than half the corrosion rate of the austenitic stainless steel (UNS S31050). The microstructure of these duplex stainless steels reveals a preferential attack of the austenite phase, although when chromium content is lower, an attack of the ferrite phase is also observed. The depth of attack increases as chromium content in the matrix decreases. - UREMIUM29 (UNS S32906): this super duplex shows the lowest corrosion rate with the lowest depth of attack. In this case, a selective attack of the austenite was also detected. Chromium content is high enough to guarantee the passivity of ferrite under the conditions inside the autoclave. Austenite suffers a slight attack as no oxygen is present. This preferential attack of the austenite has been reported to disappear at longer exposure times, as anodic protection of the austenite can occur when the ferrite/austenite area has become large enough as a result of corrosion of austenite. The results of this analysis were very satisfactory for UREMIUM29, the super duplex solution for application in the most corrosive sections of urea plants. In this study, where the conditions achieved in the autoclave were extremely harsh (high temperature, high pressure, corrosive test solution, absence of oxygen), this grade showed superior corrosion resistance.

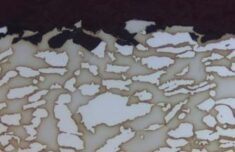



Figure 2. Cross sections of the tested specimens: a) S31050, b) S31803, c) S32750, d) S32760 and e) UREMIUM29.
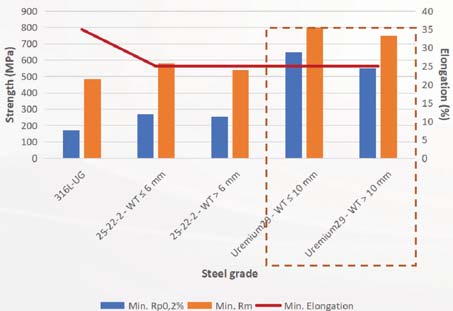

Figure 3. Mechanical properties of UREMIUM29 at room and high temperature.
High mechanical properties
Another advantage of UREMIUM29 is its very high yield and tensile strength compared with other austenitic materials typically used in urea plants. Even at high temperatures, the material shows excellent mechanical resistance, with low strength derating, as shown in Figure 3. This means that there is a scope for wall thickness reduction with UREMIUM29, which implies important cost savings.
Full range of products
For complete utilisation of the advantages offered by UREMIUM29, TUBACEX has developed the full range of products requested in the different parts of urea plants. During the last few years, the company has extensively worked in the manufacturing of special products, such as small bars (R35, R65, R95), plates, bolting hardware, welding consumables: TIG rod and wire, SMAW electrode, strip band, etc. Pictures of these special products and the corresponding microstructures are depicted in Figure 4.
These products were also tested in the autoclave at the same corrosive conditions previously explained. The achieved corrosion rate and depth of attack for each product are summarised in Table 2. The corrosion rate measured for small bars, plates and bolting hardware was very low: around 0.1 mm/year. Corrosion rates were also very low for welded products when UREMIUM29 filler metal was used, and slightly higher when super duplex filler metal was utilised.

Case study
A UREMIUM29 ferrule was analysed after being in operation in a real stripper for 19,300 hours. The microstructural analysis was conducted on one section to characterise the tube, and in another section to examine the hole in detail.
The outer surface showed a higher attack than the inner surface. The attack was not preferential, as it progressed through both austenite and ferrite phases. The ferrite content was measured, giving values around 54%. The ferrule hole, which was more affected, showed a similar corrosion mechanism. The attack was not preferential, as can be observed in micrographs shown in Figure 6. No point with localised corrosion that could dramatically progress was detected.
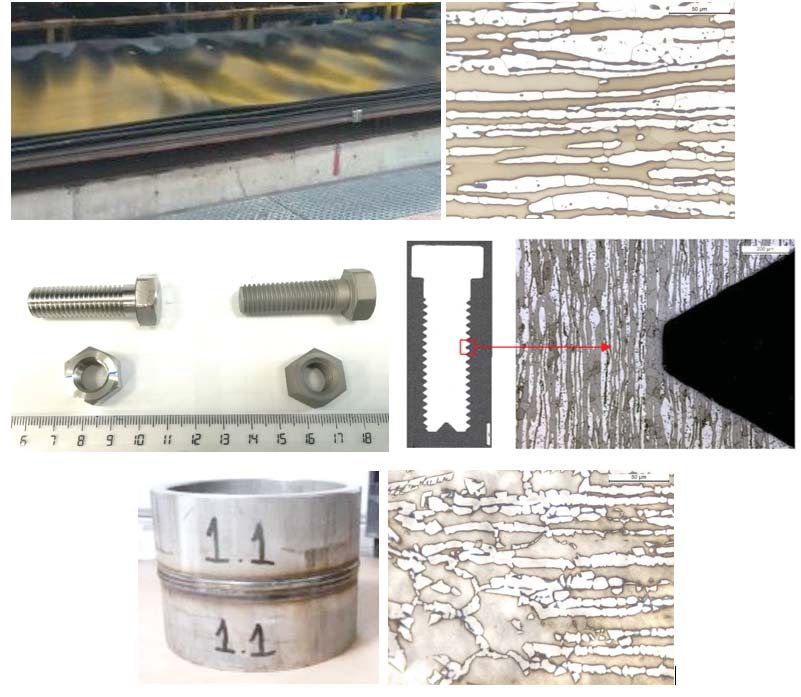
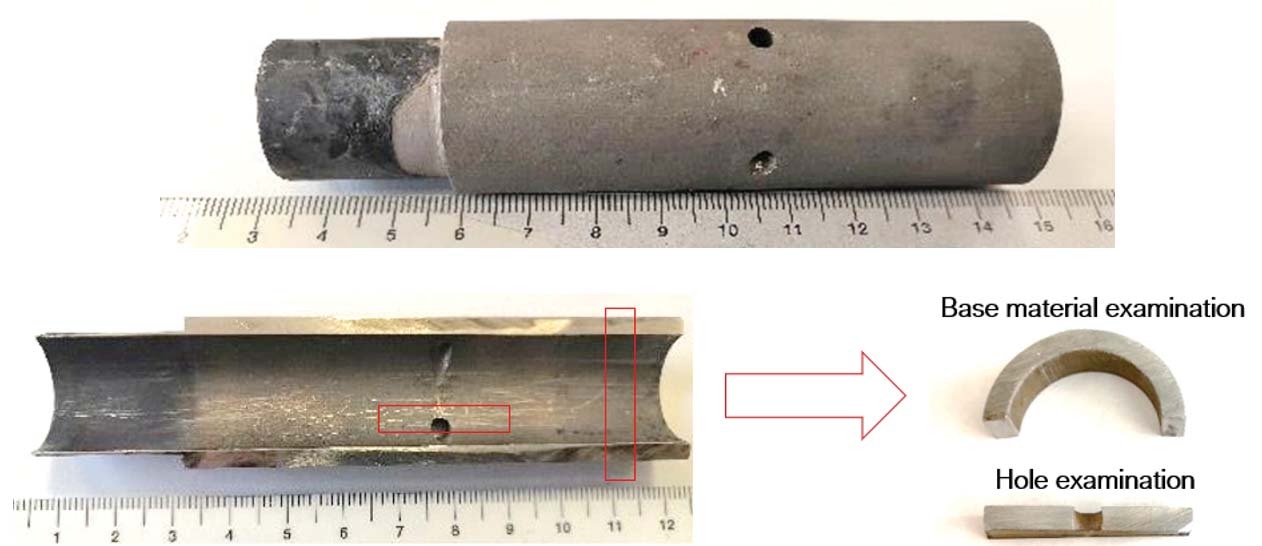
Conclusions
UREMIUM29, a super duplex specially designed for the most corrosive environment of urea plants, shows a very low corrosion rate in the full range of products manufactured by TUBACEX with only a slight selective attack on the austenite phase due to the absence of oxygen. The good formability and weldability, together with its high mechanical properties, make this material an excellent solution, in terms of resistance and cost, for the high-pressure tubes in urea equipment, as it increases the efficiency and service life of urea plants. The analysis of a UREMIUM29 ferrule after more than two years of service confirms the excellent performance of this material.

Figure 6. Longitudinal sections of UREMIUM29 ferrule.

About the authors
Beatriz Calleja
Beatriz Calleja is a materials engineer characterise in the field of metallurgy, with more than 15 years’ experience working in a materials laboratory. Currently, she is the manager of the R&D laboratory of Tubacex Innovacion, leading several R&D projects, developing new steels and improving manufacturing processes. She is skilled at performing failure analysis, using several microstructural characterisation techniques, providing material recommendations and heat treatment conditions for product engineers, and so on.
Alejandra Lopez
Alejandra López holds a degree in Mining Engineering specialising in Metallurgy from the University of Oviedo and an MBI (Master’s in Business Innovation) from Deusto Business School. Her more than 20 years’ professional experience began at the Asturian Materials Technology Institute, ITMA, as a Research Engineer and later at Sidenor R&D. She is currently the R&D Director at the Tubacex group where she leads R&D activities at the corporate level working on developing and optimising materials, processes and solutions for applications in various sectors such as energy, chemical process and mobility.