Heating water and indoor spaces accounts for almost half of all building energy needs globally. Although electric heat pumps are increasing in popularity, the vast majority of heating relies on the burning of fossil or renewable fuels. Heating methods involving combustion can tax the equipment due to high temperatures and the formation of corrosive byproducts, potentially compromising not only efficiency but also safety. For this reason, modern heating systems increasingly rely on molybdenum-containing stainless steel.
By Thierry Pierard for IMOA
As demographics shift and standards of living rise worldwide, the volume of heated indoor spaces has surged by almost 25% since 2010. Minimizing fuel consumption, thereby reducing greenhouse gas emissions, is imperative to reach our climate goals. For these reasons, heating systems must continue to become much more efficient.
There are a variety of traditional residential heating systems, depending on the climate, fuel availability, and prevalent technology. However, most systems work by burning some kind of fuel, heating either water in a boiler or air in a furnace. Hot water then circulates throughout the building across a system of tubes, heating the rooms via radiators or radiant floors. Hot air, by contrast, circulates through ducts into the living spaces.
Most fuels, whether fossil, such as oil, gas and coal, or renewable such as wood or biogas, create emissions in the form of flue gases. Depending on the fuel, they consist predominantly of nitrogen, CO2, and water vapor with small amounts of nitrogen oxides (NOx), SO2, and particulate matter. These potentially noxious gases are vented to the outside through a flue pipe or chimney. When flue gases cool below their dewpoint at around 56°C, the water vapor condenses to form water, which in combination with the other compounds can create aggressive acids. Each heating system has its own particularities and requirements. At less than 60°C, the relatively cold flue gases from a gas condensation boiler are very different from those of a wood burning stove that are as high as 600°C. The former requires a flue that is resistant to acidic condensates, while the latter needs one that is heat resistant. Surprisingly, both can use the same molybdenumcontaining stainless steels, to last a lifetime.
Besides flue gases, circulating and sanitary water can also pose a major corrosion risk in residential heating systems and affect their efficiency. The presence of aggressive substances, especially chlorides and free chlorine, found in treated water, can attack the surfaces of boiler water circuits. With hard water, calcium and magnesium can form insulating scale deposits that reduce thermal efficiency and can cause premature failure of components. Molybdenum-containing stainless steels with their smooth surface and high corrosion resistance provide complete solutions for all things combustive home heating: boilers, stoves and fireplaces, chimney flues and hot water tanks.
Boilers: stainless steel contributes to efficiency
The boiler is the heart of a hot water heating system. Depending on the technology, boilers burn gas, oil, wood, or even coal to generate heat. Much of the heat is then transferred through a heat exchanger to a water circuit while unused heat in the flue gases is vented to the outside. To increase efficiency and reduce the environmental impact of a boiler, it is essential to minimize the amount of heat lost this way to the outside and use it to heat the circulating water instead. The cooler the flue gas, the more energy has been used to heat the house and sanitary water for bathrooms and kitchens. Modern condensing boilers, as described in the illustration below, are therefore some of the most highly efficient heating units on the market today. A boiler’s durability and performance depend also on the fuel type, how it is operated and maintained, and the material it is made of.
The materials used for the combustion chamber and the heat exchanger largely determine the longevity and performance of a boiler. These components, traditionally made from cast aluminum, ceramics, and steel are increasingly produced in Type 316L stainless steel. The 2% molybdenum in this alloy provides very good resistance to pitting corrosion and good high temperature strength. In the most recent high-efficiency condensing boilers, Type 316 Ti, and in some premium models, even 904L stainless steel are used. With its 4% molybdenum content, 904L has even better corrosion resistance, practically guaranteeing a long service life.
Schematic functioning of conventional and condensing boilers
Conventional boilers have a burner and a heat exchanger in the combustion chamber. The hot gas heats the water in the circuit and then when still hot, it escapes through the flue, losing a lot of the valuable energy to the outside. In contrast, condensing boilers are much more energy efficient, as they use a condenser after the combustion chamber to extract more heat from the flue gas by preheating the incoming water from the heating circuit. Through this, the gas temperature drops below 60°C, its “dew point”, where it condenses and acids form. The combustion chamber and the condenser are designed to resist corrosive fumes and acidic condensate, respectively. The condenser allows the collection of the condensates, instead of releasing it into the air, reducing air pollution.
Stainless steel slips into chimneys
The hot gases from boilers, furnaces, and other combustive heating systems must be vented through a chimney. Traditional masonry chimney flues are rarely watertight and aggressive condensate and acidic flue gases attack and deteriorate the mortar joints, which allows wetness, dangerous gases, and smoke to get into the house. Therefore, they require a lining. However, many older heating systems have significantly deteriorated liners or no lining at all. Modern liners are often double walled generally with an insulation between the walls. Type 316L stainless steel is now used as a high performance flue liner for the inner wall. This grade resists acid condensate as well as acidic flue gases and high temperatures. The outer liner can be of the same material or Type 304 stainless steel in mild environments. A stainless steel flue liner with its smooth surface finish makes it more difficult for soot to adhere to, allowing smoke to exhaust faster. Lessening soot build up also reduces the risk of fire.
Comparatively light and easy to install, stainless steel is suitable for lining both existing chimney flues and new installations. A wide range of shapes and diameters of sleeves and chimney outlets are possible with Type 316L stainless steel. Compatible with all fuels, the alloy is ideal for wood, oil, and gas-fired boilers, and allows dry or damp smoke to evacuate at high and low temperatures. Traditionally double walled stainless steel liners were used to avoid dangerously hot pipes in the house and to maintain the flue gas temperature to ensure a good draft and avoid condensation. However, with condensing boilers the insulation solves a different problem. The flue gas temperature is so low, that it has almost no natural draft, and therefore maintaining its temperature is extremely important to allow the gases to escape. Double walled stainless steel pipes can also be used by themselves, without a traditional masonry chimney for support. This solution is cost effective, light and easy to install, it saves space, and can add a beautiful and dramatic element inside or outside the house.
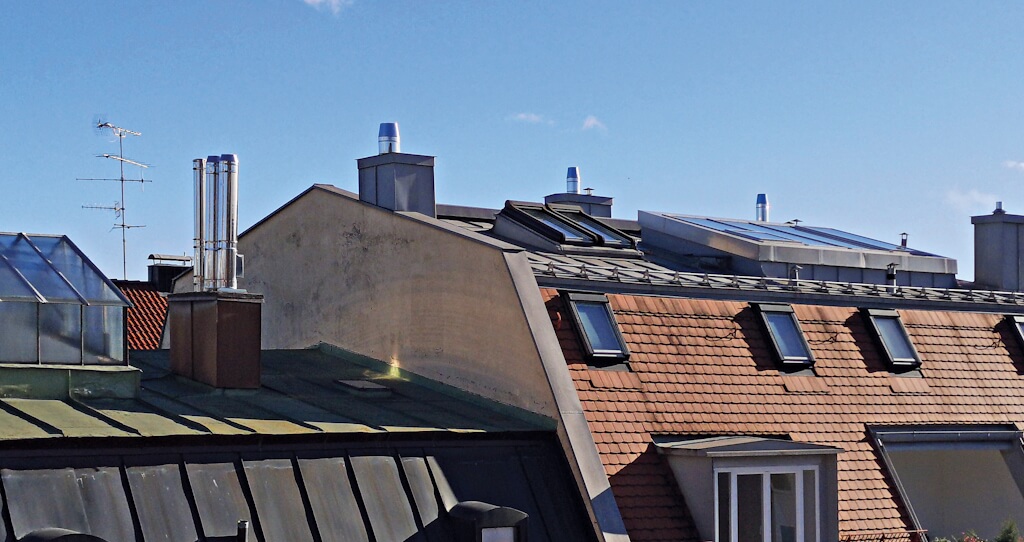
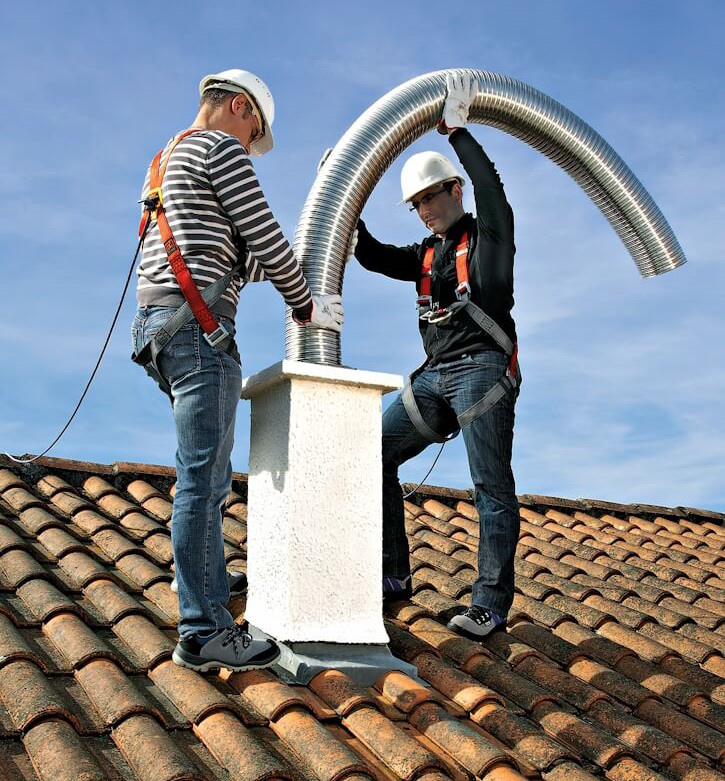
Hygienic stainless steel hot water tanks
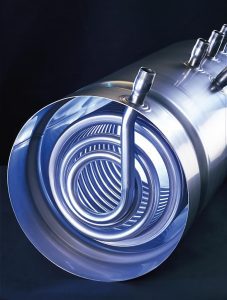
Hot water tanks store heated water, mainly for domestic use in bathrooms and kitchens. Type 316L stainless steel meets the highest requirements for hygiene and durability and can withstand most corrosion risks from all types of potable water. Unlike enameled steel tanks that require regular replacement of their magnesium anode, Type 316L stainless steel requires minimal maintenance. Just like with a chimney flue, a stainless steel tank lining is smooth, which mitigates scale build up and thereby reduces maintenance and prevents premature aging of the water tank. Heat exchange coils, also made of Type 316L stainless steel, offer the same advantages in addition to good thermal conduction. In chloride-containing hot water, stress corrosion cracking (SCC) is always a risk. To mitigate against SCC, Type 444 ferritic stainless steel with 2% molybdenum and 2205 duplex stainless steel with 3% molybdenum are also popular for the lining and heating coils of hot water tanks. Thanks to its high strength, duplex stainless steel hot water tanks are also much lighter than conventional tanks. The most efficient heating systems available today are all moving towards designs with molybdenum-containing stainless steel. Type 316L stainless steel is used across a range of heating applications, improving the efficiency and durability of boilers, chimney fittings, sleeves, and outlets, flue pipes and liners, hot water tanks, and tank heat exchange coils. Additionally, in some models 904L austenitic stainless steel, Type 444 ferritic stainless steel, and 2205 duplex stainless steel are used for specific applications. Having said that, with emission-free electric heat pumps enjoying double-digit growth rates, home heating is now quickly moving away from burning fossil fuels – but not from molybdenum-containing stainless steels. Their corrosion resistance and hygienic properties are essential for heat pumps as well –however, that is for another article.
Reproduced with the kind permission of the International Molybdenum Association (IMOA). IMOA is a non-profit trade association representing the majority of the molybdenum industry worldwide. For information, visit www.imoa.info
About this Featured Story
This Featured Story appeared in Stainless Steel World May 2024 magazine. To read many more articles like these on an (almost) monthly basis, subscribe to our magazine (available in print and digital format) – SUBSCRIPTIONS TO OUR DIGITAL VERSION ARE NOW FREE.
Every week we share a new Featured Story with our Stainless Steel community. Join us and let’s share your Featured Story on Stainless Steel World online and in print.