The maritime sector has adapted to IMO 2020 regulations limiting polluting emissions by fitting high-quality exhaust filtering systems.
Text & images by Inossidable magazine Nr 225 by Centro Inox
Recent adaptations to exhaust filter systems within the maritime sector include new constructions featuring innovative exhaust gas sorting systems and the use of ‘green’ fuels such as LNG (a fuel with very low percentages of pollutants).
Many shipping companies in the maritime sector are still using bunker fuel with high sulfur content. Scrubbers are therefore making a valuable contribution to meeting the new regulations. A scrubber is essentially an exhaust cleaning tower which functions as a huge particulate filter, allowing shipping companies to reduce their sulfur emissions to a level corresponding to the required 0.5%.
IMO2020
The IMO 2020 regulation limiting polluting emissions by ships has been in force since 1 January 2020. In particular, the rule limits the amount of allowable sulphur in the fuel oil used onboard ships operating outside designated emission control areas to 0.50% m/m (mass by mass) to lower the environmental repercussions of shipping and to protect ports and coastal areas. The maritime sector has responded by either turning to more fuel-efficient low-sulphur fuels or installing scrubbers. Many shipowners have chosen this second solution, installing this equipment to clean their ship’s exhaust gases, believing that this choice will bring considerable advantages over time, despite the costly initial investment.
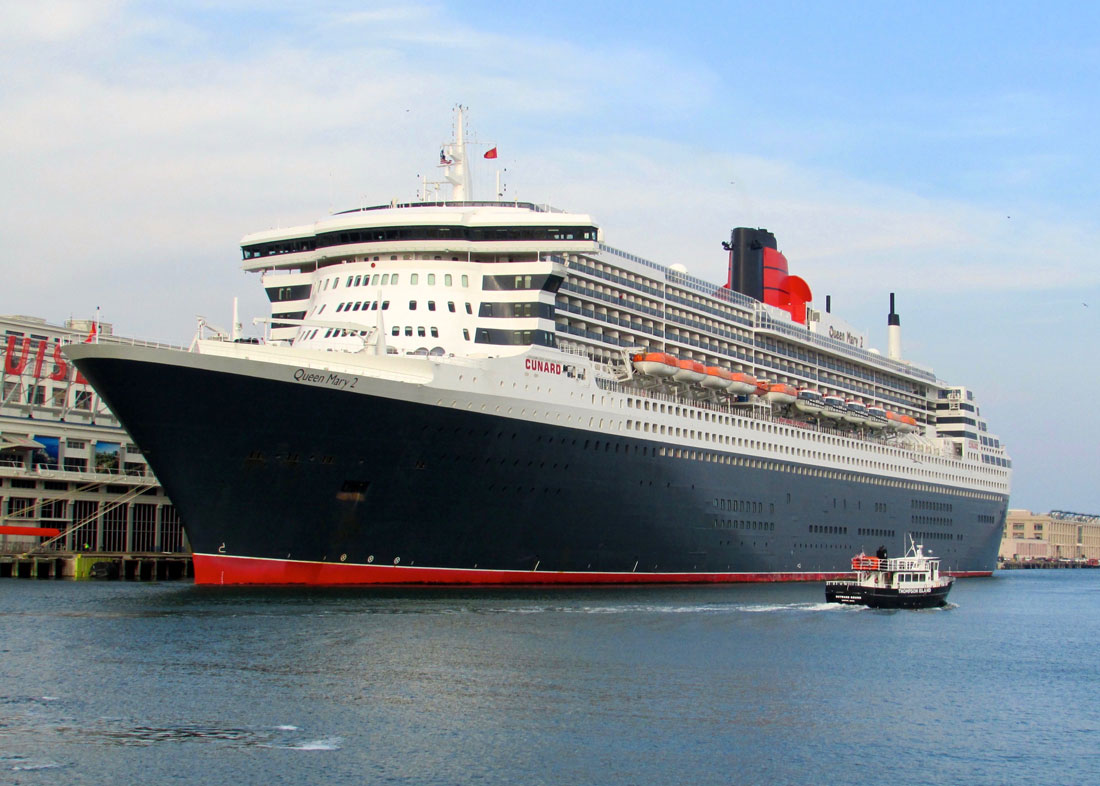
Highly aggressive agents
The devices used to purify the exhaust gases are in constant contact with highly aggressive corrosive agents, often at high temperatures. Therefore, it is essential when selecting the construction materials to focus on high-performance alloys to ensure a lifecycle compatible with the duration of the vessel on which they are fitted while respecting normal maintenance operations. As a result, the companies involved in the construction of scrubbers are oriented in their choice of alloys towards high-performance stainless steels, and in particular on duplex, super duplex and super-austenitic stainless steels.
Italian production
This article presents the experiences of an Italian company involved in the manufacture of scrubbers in stainless steels with high corrosion resistance characteristics. Specifically, the outer shell is made almost entirely of super-austenitic stainless steel EN 1.4547 (UNS S31254), while some internal components are constructed using super duplex EN 1.4410 (type 2507). For external parts such as flanges, fittings, etc., the ‘standard’ EN 1.4301 (AISI 304) and EN 1.4401 (AISI 316) are used, even in their low carbon content versions.
To realise the components mentioned above, we started with sheets of variable dimensions: 2000x4000mm / 2000x6000mm and thicknesses of 4/6 mm, but also 2000×8500 and thickness 8 mm, or 1500 x 3000 mm and thickness 15 mm. These basic products are then processed with presses, plasma cutting machines, and 2D and 3D laser welding, thanks to the possibility of utilizing over 25 welding stations. However, manual welding is also used for some parts. The material, thus prepared, is then transferred to a separate building for final assembly.
Finally, the component is subjected to an appropriate pickling treatment with eventual final passivation. The company that manufactures these important accessories for the maritime sector has, so far, manufactured more than 100 scrubbers of various sizes, with diameters ranging from 1750mm to 3200mm and with lengths ranging between 8300 and 12500 mm.

References
Nicro Spa, www.nicro.it Ecospray Technologies, www.ecospray.eu
About Centro Inox
This article was provided by Centro Inox (through its magazine Inossidabile), a non-profit association involved in the study and development of stainless steel applications in Italy. For information visit www.centroinox.it
About this Featured Story
This Featured Story appeared in Stainless Steel World October 2022 magazine. To read many more articles like these on an (almost) monthly basis, subscribe to our magazine (available in print and digital format – SUBSCRIPTIONS TO OUR DIGITAL VERSION ARE NOW FREE) .
Want to contribute as author? Please contact Joanne.
Every week we share a new Featured Story with our Stainless Steel community. Join us and let’s share your Featured Story on Stainless Steel World online and in print.