The tranquil town of Lindlar, near Cologne, Germany, is home to a world market leader with almost 145 years of experience producing and processing high-quality special steel components. Over the past few decades, the Schmidt + Clemens Group has expanded worldwide, particularly with tube systems manufactured using centrifugal and static mold casting processes. Today, they are the first point of contact for clients in many industries.
By Catrin Senger, Stainless Steel World Germany
Schmidt + Clemens (S+C) has positioned itself as a full-service partner that provides its customers with material and application advice from production and commissioning right through to the entire service life of the product. This full service also includes the company’s innovation centre, which focuses on developing and continuously optimising materials.
Lars Niemczewski, Chief Communication Officer, explains: “We know our strengths, continuously expand them and use them in a targeted manner for our customers.”
The stainless steel specialist aims to increase the productivity of customers’ systems. S+C achieves this through high product quality, efficient manufacturing processes, further development of the materials, the greatest care in post-processing, and extensive and qualitative tests. Not to forget its excellently trained and qualified workforce; S+C employs over 1,000 people at its six production and service sites and three sales offices worldwide.
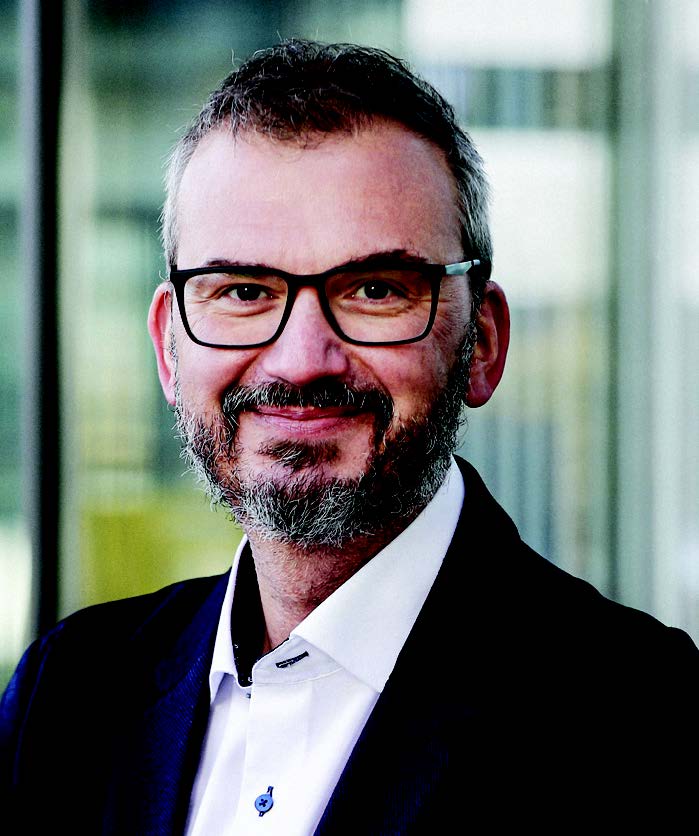
Lars Niemczewski: “Manufacturing close to the final contour saves machining processes and costs

Christian Lenz: “Centrifugal casting also achieves a longer service life than conventional sheet metal products.”
Proudly made by S+C
How exactly does S+C use its strengths for customers? The company has over 75 years of experience in both centrifugal casting and static mold casting. Depending on the dimensions and customer requirements, the stainless steel specialist can fall back on the appropriate manufacturing process for each component. The company’s Lindlar facility is one of the most modern foundries for stainless steel centrifugal casting in the world.
Mr Niemczewski gives a brief overview of the manufacturing processes. “In vertical and horizontal centrifugal casting, components are produced with a high-purity and high-density structure. The centrifugal casting process perfected by Schmidt + Clemens is usually the first choice for the production of hollow, rotationally symmetrical components, regardless of whether they are cylindrical or conical in shape.”
“Components with complicated geometries and different cross-sections are best produced using the static mold process. The production takes place either in the machine or hand molding process. The products manufactured in this way are impressive right from the first cast, thanks to the high degree of freedom in design and geometry. Manufacturing close to the final contour saves machining processes and costs.”
“The static casting process is particularly suitable for smaller and complex castings weighing up to 25 kg and measuring up to 400 mm in length.” In addition to the various casting processes, S+C offers forged components of high-quality special steel. The cast blanks are carefully post-processed mechanically in a wide variety of work processes. In this way, a ready-to-install system component is created from a raw part. The S+C welding department ensures compliance with uniform welding processes and thus high product quality. Here, system components are used to create entire tube systems.
S+C relies on seamless quality control; each workpiece is checked at the various production phases. Whether chemical composition or dye penetrant testing, X-ray examination of weld seams, mechanical tests and metallographic examinations – all tests are carried out in the company’s own test and laboratory centre, which is certified according to international standards. S+C has also developed its own, even stricter quality standards. In this way, the company ensures consistent product quality at all production sites worldwide.
Research & innovation

S+C runs its research and development department at its headquarters in Lindlar as well as in its subsidiary in Spain with great commitment and willingness to invest. It is considered to be one of the largest and best-equipped specialist departments in the industry. In the innovation centre, which is the technological heart of S+C, the process, technology and material knowledge collected over the years is bundled and further deepened by the S+C experts. This expertise is also shared and expanded in direct and intensive contact with customers, renowned research institutions and universities worldwide.
The resulting research work allows the company to not only produce tailor-made products of the highest level, but also technologies that form the prerequisites for these products. One such example is the XCS 3000 test stand, which is unique worldwide. Here, new high-temperature material developments from the Schmidt + Clemens Group are tested under conditions exactly replicating the real conditions inside a steam cracker. The innovation center is also the nucleus for material innovations. The S+C materials experts have developed a large selection of special alloys, including Centralloy® alloys and micro-alloys, specifically for the requirements of the petrochemical industry. For example, the Centralloy® HT family of materials has been designed for use at very high temperatures in steam crackers and in direct iron ore reduction. These materials are resistant to high-temperature corrosion, last longer than other materials and are extremely dimensionally stable thanks to the centrifugal casting manufacturing process.
High-temperature applications
S+C’s Centralloy® HT family of materials are speciality products designed for high-temperature applications, able to withstand the most extreme loads in industrial furnaces. Christian Lenz, Head of Sales Special Products at Schmidt + Clemens, explains the special features and advantages of the S+C dry rollers for industrial furnaces.
“Furnace rollers made of low-alloy materials could require constant water cooling, which leads to high energy costs. In addition, the applications are maintenance-intensive and prone to failure; the average lifespan is extremely limited. S+C has offered an alternative which increases the lifetime significantly: using high-alloy, heat-resistant materials means that the furnace rollers do not need to be water-cooled.”
“The dry rollers enable high savings in energy costs in hot rolling mills for example,” adds Mr Niemczewski, pointing out a cost advantage. “In connection with the reduced energy costs, there is great potential for savings in heat treatment systems because there is no need for water, and the service life of the S+C dry rollers is two to three times longer.”
Areas of application
The components and solutions from S+C are corrosion-resistant, heat-resistant or wear-resistant because they have to deliver top performance over the long term. They are used in a wide variety of industries.
In addition to the petrochemical industry, S+C components can also be found in mechanical and plant engineering, as well as in energy technology such as in hydroelectric and coal-fired power plants, and in process and industrial furnaces.
The materials experts at S+C have therefore developed a material that can withstand working temperatures of over 1,200°C, especially for use in heat treatment systems: Centralloy® 60 HT R. Mr Lenz emphasises the unique selling points: “Conventional rollers made of chrome-nickel steel are suitable for use up to a maximum of 1,180°C. During operation, they form a surface layer of chromium oxide. This protects the rollers from wear and corrosion. However, the chromium oxide on the surface starts to evaporate above 1,000°C. To restore the protective layer, these gaps must be replaced with new chromium molecules from the matrix of the material. This causes the chromium carbides, which are responsible for the strength of the material, to decompose. The result is an increased susceptibility to wear of the rollers.”
Dry rollers from Schmidt + Clemens made from Centralloy® 60 HT R perform differently. “The nickel-aluminium alloy reacts with the ambient oxygen and builds up a protective layer of aluminium oxide on the surface,” continues Mr Lenz. “Due to the higher density of the aluminium oxide layer, less oxygen penetrates the material, slowing down the chemical reaction. Aluminium oxide remains stable even at temperatures up to 1,250°C and does not evaporate. Our dry rollers, therefore, have sufficient strength to withstand the stresses in the oven, even at very high working temperatures. As a result, they achieve a service life that is two to three times longer than that of conventional rollers.”

Temperatures of up to 1250 degrees Celsius are no problem for the special materials from S+C.
Another application – rotary kilns for the thermal treatment of colour pigments, for example, or for producing battery powder. The tubes are heated indirectly and can have different temperature ranges.
“Imagine a large, rotating tube,” explains Mr Lenz. “In this application, large means a tube with a diameter of up to 1,200 mm and a length of up to 18 meters. The centrifugal casting process achieves such dimensions with the greatest possible precision.” He adds, not without pride: “Centrifugal casting also achieves a longer service life than conventional sheet metal products because the casting process achieves an extremely high level of dimensional stability.”
In this way, S+C supports its customers to increase the productivity of their systems. “We want to reduce standstill, reduce exchange. Our structures and materials ensure a better service life,” summarises Mr Lenz in a nutshell.
To this end, S+C is continuously working on expanding the range of materials developed in-house.

S+C products are ideally suited to demanding applications.
Top 100
The efficient manufacturing processes and the further development of new materials are based on S+C’s irrepressible thirst for innovation. It is therefore fitting that in February 2023, the stainless steel specialist impressed the jury in the TOP 100 competition for the third time. TOP 100 is the only innovation competition in Germany to honour company innovation management and success. S+C triumphed in a demanding and scientific benchmarking process.
S+C’s innovation potential was measured in the categories of innovation success, innovation climate, innovative processes and organisation, external orientation/open innovation and innovation-promoting top management.
With this award under its belt, Schmidt + Clemens will certainly continue to present forward-looking innovations in the future. It’s focus will firmly remain on combining customer requirements with ecology and economy.
Facts & Figures
Founded: | 1879 |
Manager: | Jan Schmidt-Krayer (CEO) and Dominic Otte (COO) |
Head office: | Lindlar-Kaiserau, Germany |
Other production sites: | Spain, Czech Republic, Saudi Arabia and Malaysia |
Offices: | USA, India and Brazil |
Turnover: | EUR 322 million (2022 |
Employees: | > 1000 |
Operating area: | Almost 13 hectares |
Products | Spun, static and investment castings and forging of high-quality special steels. Engineering, Plant Engineering, On-Site Service |
About this Featured Story
This Featured Story appeared in Stainless Steel World April 2023 magazine. To read many more articles like these on an (almost) monthly basis, subscribe to our magazine (available in print and digital format – SUBSCRIPTIONS TO OUR DIGITAL VERSION ARE NOW FREE) .
Want to contribute as author? Please contact Joanne.
Every week we share a new Featured Story with our Stainless Steel community. Join us and let’s share your Featured Story on Stainless Steel World online and in print.