A project developed by the TWI in the UK had the objective of developing and assessing a low-cost, single-use, tooling system based on silicon nitride for welding high-strength titanium alloys, particularly focusing on Ti-6Al-4V.
Text & images by TWI
Friction stir welding (FSW) is now a well-established process for joining light alloys. The relatively low temperature (~500°C) required to soften and plasticise aluminium alloys allows the use of steel based FSW tools, a material which is readily available, low-cost and has a good welding life.
However, tool materials and designs for welding higher temperature alloys such as titanium present a significant challenge, because not only must they be able to withstand high welding forces and torque levels, they must also operate at high temperatures of typically 1000-1200°C. Refractory metals, such as tungsten and molybdenum, are the current preferred materials, but there is only very limited use reported by industry. These have historically provided a FSW tool with properties capable of making welds, however, the cost of the material, producing the tool features and the weld life put a very large burden on the commercial viability of FSW in all but very high-value applications. Therefore, a lower-cost tooling system could make FSW more financially accessible to a wide range of industries.

The approach
Following discussions with ceramic suppliers, it was identified that the significant cost elements in ceramic FSW tools were the bulk volume of ceramic and the finish grinding of the tool profile post-firing. To reduce bulk volume, a ceramic insert mounted in a reusable metallic holder was considered the best option. To eliminate the final grinding operation, the insert would be machined in the green state and then fired. The insert geometry adopted incorporated a tapered body for accurate location and flats for providing a drive feature. The insert had a 3mm probe length. A tool holder was designed to support and transmit the torque to the insert, as shown in Figure 1.
A weld procedure was developed for welding Ti-6Al-4V; ceramic inserts from two different suppliers were assessed making bead on plate (BoP) welds. The assessment consisted of visually inspecting the inserts and then measuring their geometry using an Alicona Infinite Focus, non-contact profilometer. A two-metre-long BoP weld was then made, sectioned, and assessed visually by macrograph inspection and transverse tensile testing. Finally, the insert geometry was again inspected using an Alicona Infinite Focus non-contact profilometer. The pre- and post-geometry inspection enabled an assessment of the amount of insert material lost during welding.
Results
The insert-based tooling system performed well during welding trials, and the insert holder proved reliable, reusable and provided a good accurate location for rotation. The insert wear observed from the first supplier was consistent; importantly, there was very little material lost from the probe tip, which will maintain the weld stir depth to minimise the chance of producing a weld with lack of penetration. The calculated volume loss of material from pre- and post-weld scanning was 71.39 and 72.62mm³ for the two inserts assessed, representing 0.11% by volume of the stirred material volume of the 2m long weld.
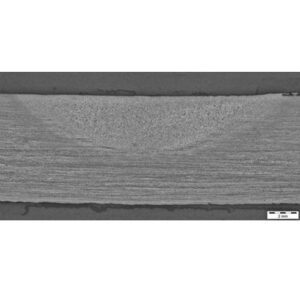
Conclusion
In developing a tooling system capable of making 3mm deep, 2m long bead-on-plate (BoP) welds, in Ti-6Al-4V using single-use ceramic inserts, TWI has demonstrated the feasibility of using a single-use ceramic insert tooling system for welding high-strength titanium alloys. With the inserts costing less than €50, this lower-cost tooling system could make FSW more financially accessible to industries other than aerospace, where the product would benefit from the high-quality welds produced by friction stir, but could not justify the cost of the current FSW tooling systems.
This project, therefore, represents an important step forward in high-temperature FSW with results showing feasibility and practicality of approach. Follow on work will enable further investigation of the loss of material in the weld, leading to a new solution that can be adopted by industry.
This project was funded by TWI’s Core Research Programme.
About TWI
TWI (The Welding Institute) is a membership-based organisation, supporting both individuals and companies alike. It exists to provide authoritative and impartial expert advice, knowhow and safety assurance through engineering, materials and joining technologies. Descended from the British Welding Research Association (BWRA), TWI has grown into one of the foremost independent research and technology organisations. We span innovation, knowledge transfer and problem resolution across all aspects of welding, joining, surface engineering, inspection and whole-life integrity management.