Heat exchangers transfer thermal energy in both heating and cooling processes. Due to the wide variety of processes in the chemical and petrochemical industries, knowledge of the materials used in the design of heat exchangers is of paramount interest to fabricators.
By Srikumar Chakraborty – ex ASP/SAIL, freelance consultant
Heat exchangers transfer heat between media, which may be a gas, liquid, or a combination. Fouling undermines heat exchange efficiency. Corrosive fluids associated with intensified fouling may be due to the selection of improper or sub-standard materials, design flaws leading to variable heat transfer, flow resistance degradation, and drops in pressure. When designing the thermal and mechanical properties of heat exchangers, reputable manufacturers consider process characteristics such as fouling rates and the acidic corrosivity of fluids, taking guidance from their R&D team.
Heat exchanger equipment
Heat exchangers are widely used in the petrochemical, chemical and refining industries where chemical technology processes (evaporation, rectification, drying, etc.) are associated with the need for heat supply or removal.
Physical properties – High heat transfer coefficient (requiring high thermal conductivity for tube/ pipe material), as low thermal expansion coefficient as possible considering the materials used for tube/sheet plates, tube support and shell to provide resistance to thermal cycling.
Mechanical properties – Good tensile and creep strength properties (high creep rupture strength at the highest temperature of operation and adequate creep ductility to accommodate localised strain at notches). Good fatigue, corrosion fatigue and creep-fatigue behaviour.
Most austenitic stainless steels with a chromium (Cr) content of at least 18% can be used at temperatures up to 870°C, while grades 309 and 310 can tolerate temperatures up to 1150 -1200°C. The high fracture toughness and impact strength of grade 310 means it has good resistance to fractures. The low corrosion rate minimises the corrosion allowance required. Grades 309 and 310 also offer corrosion resistance to abnormal chemistry, which may result from upstream leaks or chemistry control failures resulting from a mix-up of shell and tube fluids.
Heat exchanger equipment
Heat exchangers are widely used in the petrochemical, chemical and refining industries where chemical technology processes (evaporation, rectification, drying, etc.) are associated with the need for heat supply or removal. Physical properties – High heat transfer coefficient (requiring high thermal conductivity for tube/ pipe material), as low thermal expansion coefficient as possible considering the materials used for tube/sheet plates, tube support and shell to provide resistance to thermal cycling. Mechanical properties – Good tensile and creep strength properties (high creep rupture strength at the highest temperature of operation and adequate creep ductility to accommodate localised strain at notches). Good fatigue, corrosion fatigue and creep-fatigue behaviour.
Most austenitic stainless steels with a chromium (Cr) content of at least 18% can be used at temperatures up to 870°C, while grades 309 and 310 can tolerate temperatures up to 1150 -1200°C. The high fracture toughness and impact strength of grade 310 means it has good resistance to fractures. The low corrosion rate minimises the corrosion allowance required. Grades 309 and 310 also offer corrosion resistance to abnormal chemistry, which may result from upstream leaks or chemistry control failures resulting from a mix-up of shell and tube fluids.
ASM Metals Hand Book
Grade | Intermittent | Continuous |
304 | 870 | 925 |
309 | 980 | 1095 |
310 | 1035 | 1150 |
316 | 870 | 925 |
321 | 870 | 925 |
Table 1. Maximum service temperature (°C) in austenitic grade stainless steel
Material selection for heat exchanges
A general procedure for identifying the most appropriate material for a heat exchanger application would consider the following:
- Requirements of the heat exchanger;
- Strategy evaluation;
- Raw material selection;
- Cost calculation;
While an assessment of costs for any equipment breakdowns or tube replacement should be considered, the raw material selection factors affect the performance of the heat exchanger. Heat exchangers account for over 30%of the total market share of petroleum and chemical products requiring heating, cooling, or condensation processes. They play an essential role in product quality and process economy by utilising heat. The trend is for heat exchangers to develop towards large-scale, high-efficiency, high-alloyed products with low-temperature difference and low-pressure loss. In many situations, particularly offshore and remote locations, heat exchangers can be configured to provide maximum heat transfer for a minimal footprint while maintaining safety.
Although stainless steel grade 310 is subject to stress corrosion cracking, it is more resistant than grades 304 or 316. It has good resistance to oxidation in intermittent service in air at temperatures up to 1040°C and in continuous service at 1150°C. It also has good resistance to thermal fatigue and cyclic heating, exhibiting remarkable flexibility, durability, toughness, high tensile strength, corrosion resistance and stability at elevated temperatures. Heat exchangers manufactured from stainless grade 310 are used for cooling and heating processes in space heating, refrigeration, air conditioning, power stations, chemical plants, petrochemical units, petroleum refineries, natural gas, heat treatment furnace parts and sewage treatment. A classic example of a heat exchanger is an internal combustion engine in which a circulating fluid known as engine coolant flows through radiator coils. Air flows past the coils, which cools the coolant and heats the incoming air. Another example is a heat sink, a passive heat exchanger that transfers the heat generated by an electronic or mechanical device to a fluid medium, often air or a liquid coolant.
Composition % | C | Mn | Si | P | S | Cr | Ni |
Stn310 | 0.25 max | 2.0 max | 1.5 max | 0.045 max | 0.030 max | 24-26 | 19-22 |
Stn310S | 0.08 max | 2.0 max | 1.5 max | 0.045 max | 0.030 max | 24-26 | 19-22 |
Tensile strength – 520MPa min. Yield strength – 205 MPa min | % Elongation – 40 Hardness -205 BHN |
PREN 25, & in Sea water 22 similar to 316 grade |
Table 2. Chemical composition & mechanical properties (primary alloying elements being Cr and Ni)
Properties
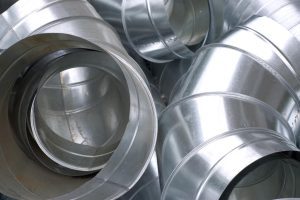
Stainless steel 310/S products are non-magnetic as annealed and become lightly magnetic if cold-worked.
The difference between grades 310 & 310S (described as a low-carbon version of 310) is the carbon content. Both grades are used in high-temperature applications. The lower carbon content of 310S minimises carbide precipitation and improves weldability. The mechanical properties for both grades are the same.
Both grades contain 25% Cr and 20% Ni, making them highly resistant to oxidation and corrosion. Grade 310S is less prone to embrittlement and sensitisation in service. The high Cr and Ni content make these steels suitable for applications that reduce sulphur atmospheres containing H2S. Both are widely used in moderately carburising atmospheres, as encountered in petrochemical environments.
For more severe carburising atmospheres, grade 310 is not recommended for frequent liquid quenching as it suffers from thermal shock. The grade is often used in cryogenic applications due to its toughness and low magnetic permeability. Similar toother austenitic stainless steels, heat treatment cannot harden these grades. They can be hardened by cold work, although this is rarely done in practice.
Grade 310/S for heat exchangers
While designing and constructing heat exchangers, it is necessary to satisfy the multilateral and often contradictory requirements as far as possible. The main issues are compliance with the conditions of the technological process, a possibly higher heat transfer coefficient, low hydraulic resistance, resistance of heat exchange surfaces against corrosion, accessibility of the heat transfer surface for cleaning, manufacturability of structure from the point of view of fabrication, and the economical use of costly materials. This final point requires the consideration of factors including:
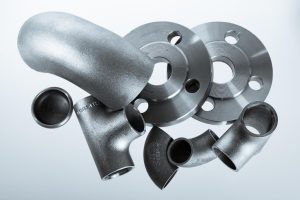
- Fabrication characteristics – Stainless grades 310 and 310S rolled pipe, tube, plate/sheet in bent condition, and any forged component can be fabricated by cutting the products as designed, as these grades can withstand working temperatures in the range of 975-1175°C. Heavy work is carried out down to 1050°C by standard methods and equipment.
- Machining – the machinability of grades 310 and 310S is similar to that of grades 304 and 316. Work hardening can be a problem, and it is customary to remove the work-hardened layer using slow speeds and heavy cuts with sharp tools and good lubrication. Powerful machines and heavy, rigid tools are used.
- Weldability – Grade 310/310S products in any shape are a great way to connect two pieces of metal and have many advantages over other welding methods. Grade 310 is corrosion and heat-resistant, does not require a heat treatment step, and can be welded using various welding equipment. It is also ideal for projects that involve environmental protection and safety aspects.
Stainless 310/310S grade is welded with matching electrodes and filler metals. Products are readily welded by standard welding manuals using techniques such as GMAW (MIG), GTAW (TIG) and SAW. Preheat and post-heat are not required, but post-weld solution annealing is essential for corrosion service in liquids. Pickling and passivation of the surface to remove high-temperature oxides are necessary to restore complete aqueous corrosion resistance after welding. This treatment is not required for high-temperature service, but welding slag should be thoroughly removed. Grades 310/310S are solution annealed by heating to 1040-1065°C, holding at temperature until thoroughly soaked, then water quenching.
Design and fabrication
The primary function of heat exchangers in the petrochemical industry is solvent condensation undergoing chemical cooling and heating reactors. The design of the equipment is based on temperature ranges, product mix, pressure drops across the exchanger, fluid flow capacity, cleanability, repair and maintenance. Seamless or welded tubes of suitable materials are used without compromising quality during manufacture.
Fouling problems – cause & remedy
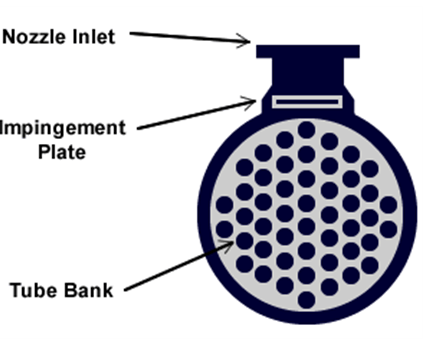
Fouling is a membrane separation phenomenon resulting from several mechanisms: precipitation of sparingly soluble salts, adsorption, cake or gel formation, and pore blockage because of the composition of the water in the system, causing a decrease in the heat transfer coefficient with time. Klarex’s (Netherlands) self-cleaning heat exchanger consists of a design that reduces the surface area by approximately 20%.
Scaling occurs because the water flowing through the heat exchanger contains impurities such as calcium carbonate, magnesium, chloride or iron. Fouling represents the theoretical resistance to heat flow due to a build-up of a layer of dirt or other fouling substance on the tube surfaces of the heat exchanger.
A method for reducing the formation of deposits on the inner walls of a tubular heat exchanger through which a petroleum-based liquid is flowing comprises applying fluid pressure pulsations to the liquid flowing through the tubes of the exchanger and vibration to the heat exchanger to effect a reduction of the viscous boundary layer adjacent to the inner walls of the tubular heat exchange surfaces. Reduction of the viscous boundary layer at the tube walls not only reduces the incidence of fouling with a resulting beneficial effect on equipment life, but it also has the desirable effect of promoting heat transfer from the tube wall to the liquid in the tubes. Using a coating on the inner wall surfaces of the exchanger tubes may further reduce fouling and corrosion.
Conclusion
The high nickel content of austenite 310 grade is superior to grades 304, 316, 321 and 309. It combines high corrosion resistance and high-temperature properties with good ductility and fabrication characteristics. Due to the chemical composition of this grade, with chromium up to 25% and nickel up to 20%, products manufactured in grade 310 provide solid corrosion resistance, excellent resistance to oxidation, and superior strength at high temperatures up to 1150°C. High nickel (25+%) alloys are most commonly used to construct process equipment, including heat exchangers, when superior corrosion resistance and high-temperature mechanical properties are required.
About this Featured Story
This Featured Story appeared in Stainless Steel World April 2024 magazine. To read many more articles like these on an (almost) monthly basis, subscribe to our magazine (available in print and digital format) – SUBSCRIPTIONS TO OUR DIGITAL VERSION ARE NOW FREE.
Every week we share a new Featured Story with our Stainless Steel community. Join us and let’s share your Featured Story on Stainless Steel World online and in print.