Maruichi Stainless Tube manufactures high-quality seamless stainless pipes and tubes around the globe. Most recently, it has focused on products for the semiconductor and automotive markets with innovative grades and ongoing, large-scale investments in technology. Decarbonisation, both in-house and in the markets it serves, is also a priority. Stainless Steel World spoke to President, Mr Takashi Onishi, about how the company continues to evolve in its pursuit of excellence.
By Joanne McIntyre
About Maruichi Stainless Tube
Two years have passed since Kobelco Steel Tube changed its name to Maruichi Stainless Tube and joined the Maruichi Steel Group. In addition to manufacturing high-quality seamless stainless pipes and tubes, Maruichi Stainless Tube also produces high-growth products such as semiconductor bright annealed (BA) tubes.
Maruichi Steel Tube, the parent company of Maruichi Stainless Tube, have been offering customers dedicated services since its establishment in 1947. As a specialist welded carbon tube maker, the company has amassed technological know-how and expertise throughout its global facilities. It has state-of-the-art tube mills, cold reduction and continuous hot-dip galvanising lines at 16 locations in Japan and 17 overseas: 3 in the USA, 2 in Mexico, and 12 in Asia. These facilities enable the company to meet its customers’ needs for a wide range of round tube sizes (8mm to 508mm) and similar sizes of square and rectangular tubes (from 11×11×1mm to 400×400×19mm). Maruichi Steel Tube has built a reputation as a leader in the welded carbon steel tube industry. The Group offers high-quality products and speedy service to local customers while also serving end users through an extensive overseas network.
Two-year performance trends
Looking back over the past two years, the Group has achieved excellent results despite the uncertain global situation. In terms of its 2021-2024 medium-term planning strategy, the company has achieved:
- Return on Sales (ROS) of over 10%
- Expansion of its bright annealed tube business in response to strong demand
- Adaptation to the trend towards decarbonisation by developing new products for emerging sectors, such as hydrogen
Looking forward, plans to achieve further efficiencies include the promotion of labour-saving investments, productivity improvements, and increased operational efficiency.
A review of 2021 results shows net sales 24.4 billion yen (EUR 171 million) and an operating profit 3.1 billion yen (EUR 22 million), and a ROS of 12.7%.
Stainless steel pipes
“Even during the COVID19 crisis, domestic demand for renewable energy (boilers for biomass power generation, waste to energy boilers, etc.) remained strong,” explains Mr Onishi. “However, due to the worsening situation in Ukraine, prices for raw materials such as nickel have soared, as have costs for energy such as electricity and gas, as well as other secondary materials. Despite this, the company has continued improving sales prices in Japan and overseas.”
Growing demand for coiled tubes
The company started manufacturing coiled tubes in March 2019, with overseas exports starting from 2021 targeting the oil & gas and petrochemical sectors. “Since then, Maruichi has continued to receive orders from state-owned oil companies in the Middle East,” explains Mr Onishi. “For example, earlier this year, we received an order for a large project requiring 56,000 meters of tubing. Rising resource prices have stimulated investments in development, and demand for coil tubes has also recovered. In addition, the sales volume of coil tubes for the semiconductor sector is increasing year-on-year.
To meet the strict requirements of its customers in this sector, the Group has invested heavily in testing facilities. We aim to increase the 2020 sales volume by a factor of five by 2023.”
Although a latecomer to the coiled tubes market, the company intends to capture market share by working with high-value-added and difficult-to-process materials such as high nickel and duplex stainless steel.
Name change: Kobelco ► Maruichi
In April 2020, Kobelco Steel Tube Co ltd changed its name to Maruichi Stainless Tube Col, Ltd. The name change strengthened the global production and sales network of the Group while enhancing collaboration in manufacturing technology and further cultivating growth opportunities. “The new corporate name clearly identifies our affiliation with the Maruichi Steel Tube Group and our continued commitment to manufacturing seamless stainless steel pipes and tubes within the Group,” explains company President Mr Takashi Onishi.
Booming demand for semicondutors
Maruichi has set out a strategic investment plan that will see it spend 3.4 billion yen over three years. These include improving automation and productivity within its plants, renewing ageing facilities, and improving safety and environmental issues. An additional 2 billion yen will be invested to increase bright annealed pipe production capacity.

“The need for bright annealed (BA) tubes has grown in response to the booming global demand for semiconductors. This has resulted in our production capacity increasing to 178,000 tubes per month by the end of August 2022,” explains Mr Onishi.
“In addition, in response to the construction of new large-scale semiconductor plants in the USA, South Korea, China, Taiwan, Japan and elsewhere, we are building a fourth bright annealed tube plant with an area of approx. 2400 m2 on the premises of our Shimonoseki plant. The plant will be equipped with two BA furnaces and manufacturing facilities, which increased monthly production capacity to 200,000 tubes by the second half of 2022, rising to 250,000 tubes by the second half of 2023.” “We expect the booming demand for semiconductors to continue for some time,” continues Mr Onishi, “and 2022 is expected to surpass the record-high market size achieved in 2021 due to increased demand for in-vehicle semiconductors (EV, automated driving) and factory automation. Our manufacturing and quality assurance systems are highly regarded both in Japan and abroad, and orders are increasing rapidly from North America, South Korea and China, where large-scale semiconductor plant construction projects are underway. We expect this situation to continue for the foreseeable future, with full production capacity utilised at our BA tube plants.”
Demand from the automotive sector is also expected to remain strong for the time being, as the sector is the second largest consumer of BA tubes after semiconductors. “Demand for fuel line tubing used in direct injection engines is expected to shift from gasoline engine vehicles to battery EV vehicles and FCV vehicles in the future,” explains Mr Onishi.
The hydrogen transition
“To progress towards realising a decarbonised society, we have been working on producing high-pressure hydrogen pipes for use in hydrogen stations. Hydrogen stations are equipped with a mechanism whereby hydrogen is procured from external sources or produced on the station premises, pressurised by a compressor, stored in a pressure accumulator and supplied at high pressure by a dispenser to various fuel cell vehicles. Compressors, accumulators, dispensers, and the piping connecting them is required to withstand a high-pressure hydrogen environment. High-strength 316 series stainless steel pipes with a cold-worked finish are used for these. This cold-worked 316 series stainless steel pipe is required to be very safe in harsh usage environments, so stringent specifications are imposed regarding strength and dimensional tolerances.” As the company has continuously met those demands, it has built up a great track record in Japan and continues to contribute to the realisation of a decarbonised society.
New USA plant
To meet demand in the USA, where several large-scale semiconductor plant construction plans are taking shape, the company has established Maruichi Stainless Tube Texas Corporation (MST-X), a subsidiary to manufacture BA tubes, in Seguin, Texas, USA. The company is capitalised at approximately USD 75 million and plans to increase its capital in stages. Maruichi Stainless Tube owns 42.5%, Maruichi Steel Tube 37.5%, and another company 20%. The plant site is approximately 135,000m2, with the building measuring approx. 15,000m2. The main equipment – a drawing machine and BA furnace – will be installed, and monthly production is planned to be around 90,000 pieces produced by 120 employees. The company aims to start operations in Q1 of 2024. Maruichi Steel Tube’s business plan in the United States and Maruichi Stainless Steel Tube’s advanced manufacturing technology will be utilised to meet customer needs in terms of quality and service.

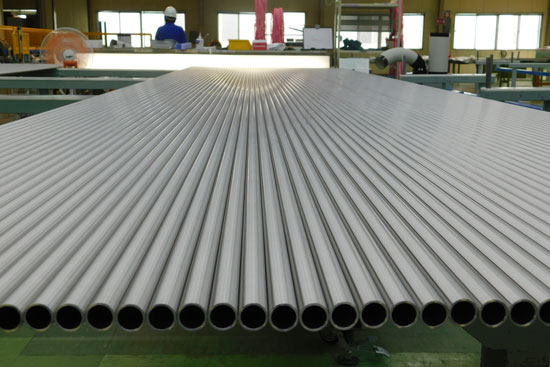
Alloy KRSA-A31: decarbonising vehicles
“While vehicles that do not emit CO2, such as electric and fuel cell vehicles, will continue to rise in popularity, for the time being, gasoline vehicles will continue to play an important role,” continues Mr Onishi. “Therefore, reducing the environmental impact of gasoline vehicles is essential in moving towards a decarbonised society. To help solve this problem, we have developed a new high-strength material (KRSA-A31) for gasoline direct injection (GDI) tubing.
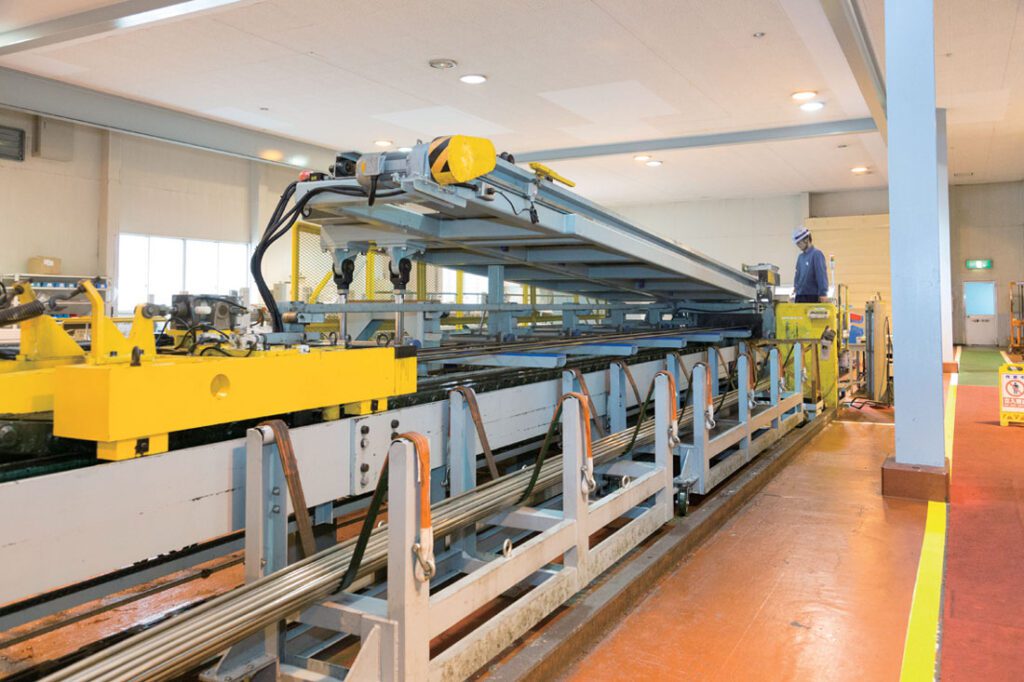
This material reduces the environmental impact of gasoline vehicle direct injection engines by increasing injection pressure and enabling thinner fuel line tubing. This further improves fuel efficiency through reduced weight and increases the productivity of component manufacturing through thinner fuel tubes.”
The alloy design concept for KRSA-A31 is based on SUS304N2, which is mainly used for high-strength fittings such as bolts and nuts. KRSA-A31 achieves both dimensional stability during the brazing heat treatment process and high strength due to its chemical composition optimisation and advanced processing.
After simulating the brazing heat treatment at 1100°C, KRSA-A31 was able to maintain its high strength, while 0.2% proof stress of SUS304N2 dropped. These results demonstrate that fuel injection pipes constructed of KRSA-A31 have high-pressure resistance.
Studies on the dimensional stability during the simulated brazing heat treatment of KRSA-A31 showed that while duplex stainless steel deformed at high temperatures, KRSA-A31 had only a small degree of deformation and could offer excellent shape stability. Corrosion resistance is also an important property necessary for fuel injection pipes. KRSA-A31 indicated higher pitting corrosion resistance potential in chlorinated environments due to the effect of nitrogen addition. This proves that KRSA-A31 is a material that offers excellent strength, corrosion resistance, and dimensional stability after the brazing heat treatment. Maruichi plans to continue its research and development for a decarbonised society by utilising and applying the high-pressure hydrogen piping and high-strength technology they have developed so far.
Decarbonisation
One of the Maruichi Steel Tube Group’s major decarbonisation targets is the reduction of CO2 emissions, which it plans to reduce by 46% by 2030 compared to 2013, in line with national guidelines. Mr Onishi: “As Maruichi Stainless Tube has the largest number of heat treatment facilities in the Group, it generates a large amount of CO2. Therefore we need to take the lead in reducing emissions. Upgrading work on our stainless steel tube heat treatment furnaces will reduce fuel consumption by approximately 10% compared to the current level. In addition, solar panels have been installed on the roof of the office building.”
“Scope 1 (direct emissions) are our top priority, after which we will tackle Scope 2 (indirect emissions). The Group is taking measures in a ‘no exceptions’ approach by paying attention to the smallest of details.”
Relationships based on trust
Maruichi has built relationships based on trust in a range of industries across the globe over many years of business. Its high-quality products and exceptional customer care have cemented its role as an indispensable mill for its customers around the globe. As one of the top suppliers of seamless stainless steel pipes, Maruichi has many plans to continue providing the best products and innovations to the market.

About this Featured Story
This Featured Story appeared in Stainless Steel World October 2022 magazine. To read many more articles like these on an (almost) monthly basis, subscribe to our magazine (available in print and digital format – SUBSCRIPTIONS TO OUR DIGITAL VERSION ARE NOW FREE) .
Want to contribute as author? Please contact Joanne.
Every week we share a new Featured Story with our Stainless Steel community. Join us and let’s share your Featured Story on Stainless Steel World online and in print.