plant fleet. Article by Joanne McIntyre
Back on track after closure
Every company in the stainless steel industry has been affected by the Covid-19 pandemic, and the Mannesmann Stainless Tubes team openly shared the impact on their business.
“It’s clear that the pandemic took the world by surprise,” begins Mr. Le Rigoleur. “Our production plant in Costa Volpino, Italy, is located in one of the most affected regions and was closed for three weeks before resuming activities with safety measures in place. Fortunately, our other facilities in Germany, France and Houston remained open. It’s thanks to the strong commitment and professionalism of our staff that we were able to be back working at full capacity across the company very quickly.”
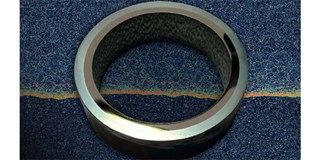
Throughout those initial difficult first weeks, the MST team remained in close contact with their customers. “Our staff rapidly adjusted to working from their home offices when necessary, which allowed us to carry on almost as normal. As a result, the financial impact on the company was not as severe as we initially feared. This prompt reactivity and close customer communication enabled us to avoid a negative impact on our customer requirements while maintaining the business on a secure footing for the future”. With production facilities working well, albeit within the constraints of the situation, the company quickly focused on rectifying any delays that were created and reached ‘normality’ by July. “We want to express our deep appreciation to our customers and employees during this time. We’d also like to particularly thank our raw material suppliers, who stayed in close contact with us and operated with solidarity and cooperation to alleviate any potential problems”.
Investments in development
Before the Covid-19 crisis began, Mannesmann Stainless Tubes was executing an extensive investment and development plan. “We recently made significant investments at our plant in Remscheid, Germany including the addition of a large cold pilger mill to increase both our capacity and capabilities,” Mr. Le Rigoleur explains.
“This is particularly useful for producing OCTG tubing destined for the oil and gas industry.”
Another investment was a state of the art straightener at the same facility. This almost fully-automated machine automatically straightens tubes and pipes, measures any deviations along the entire length and then corrects these by moving itself along the tube. The 1,000-ton machine can straighten tubes ranging from Ø 80 – 400 mm. “The cold pilger mill and the stamp straightener represent significant investments and will enable us to expand in both new and existing markets,” explains Mr. Le Rigoleur.
The company has also improved its offering of small instrumentation tubing and invested in leading technology equipment for small-bore tubing production in Costa Volpino, Italy.
This being complemented by the capabilities of our Issoudun, France (SOTEP) facility where we offer specialist tubes for instrumentation and process measurement. These improvements will allow it to offer greater flexibility to customers in this market.
The MST team expect the current depressed oil and gas prices to bounce back and are well-positioned for when the market recovers. “Until then, we will continue to work through our current backlog. Early this year we received some substantial orders which we will be working on into 2021.”
Power generation expertise
MST has a long history of serving the power generation industry. Today it is widely recognised as one of the leading producers of tubes and pipes for USC (Ultra Super Critical) coal and lignite-fired power plants. The company offers a wide range of alloys for conventional power generation, including DMV 304HCu (1.4907; UNS S30432) and DMV 310N (1.4952; UNS S31042).
The in-house experts at MST have worked for over a decade on the next generation of power plants known as Advanced Ultra Super Critical (A-USC), which operate at temperatures over 700°C. MST has developed stainless steel and nickel-alloy power plant test loops for many notable projects including Cooretec, COMTES 700, GKM 725°C / HWT 1 & 2, the Japanese METI project, the Chinese TPRI qualification project, etc.
Mr. Schraven explains: “Every modern power plant built in the last fifteen years uses high-temperature superheaters. We produce the stainless steel and nickel alloys for these and have become the most experienced supplier, particularly with grades such as DMV 617 modified, DMV 263 and DMV 141. Despite the downturn in the coal-fired sector in recent years, there are still a significant number of ongoing and planned projects in China, Southeast Asia and India.”
HRSG superheater tubing
For the Heat Recovery Steam Generator (HRSG) sector, MST is globally the only company producing and supplying standard austenitic and nickel alloys as well as USC grades including DMV 304HCu (UNS S30432) in a single seamless tube length up to 30m.
This unique capability has led to the awarding of several projects for HTSG superheater tubes for both HL-class and 702F5-class gas turbines. “We’ve successfully delivered these tubes to fabricators in Korea, China, Mexico,” explains Mr. Schraven.
“While there is a limited number of modern combined cycle plants today, we expect that to change in the near future as combined cycle gas-powered plants emit less CO2 per MWh than other fossil fuel power plants. Our ability to manufacture 30m seamless tubing means we are well-placed for this transition. We are currently in the middle of a trial and development project with a major combined cycle OEM to develop the next generation of HRSGs in Ni alloys.”
Click to read the full article.