To manufacture the huge agitators required for PTA plants, Rolf Kind processes the largest titanium ingots in the world, weighing up to 15 metric tons.
Since its foundation in 1969, the family-run company Rolf Kind GmbH has pushed the boundaries of conventional forging technology. The company came up with innovative ideas and highly efficient manufacturing technologies to create extremely resilient forgings in high-end alloys, stainless steels and titanium. Stainless Steel World met with Managing Director Markus Kind to learn about his company’s projects, their unique approach to forging, and evolving customer needs.
By Joanne McIntyre
When size matters, customers know they can rely on Rolf Kind Gmbh (R. Kind) to produce top-quality open-die forgings in high-end alloys and titanium. Massive components for chemical and petrochemical equipment, machinery construction, oil & gas exploration, refineries and power plants are the day-to-day work for this highly specialised, family-owned company. The team
of forging specialists has decades of experience in processing ingots of nickel-based alloys, high-alloy stainless steel and titanium.
Holistic approach
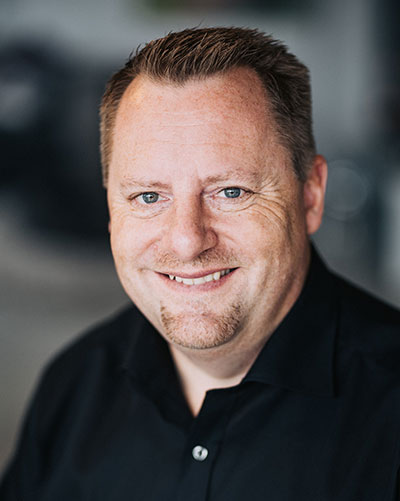
The company is growing from strength to strength in the global market, with a brand new headquarters and an expanding sales team. “We’ve recently welcomed several new sales members to the team,” explains Mr. Kind, who went on to highlight some examples. “Since September; Richard Burgdorf has been in charge of sales development in Asia with a particular focus on China, South Korea, and Japan; and in Germany, we welcomed Tobias Wagener to the European sales team.”
October was a particularly exciting month for the R. Kind team as they moved into their new HQ in Lindlar, Germany (east of Dusseldorf and Cologne). “Construction was delayed by almost
a year due to Covid-19, so we are very happy to have finally moved!”, Mr. Kind says. “The state-of-the-art facility will allow our company to continue growing, with plenty of room for our manufacturing capabilities and our staff to flourish. The design offers a holistic approach to our workspace, providing facilities to enhance our teams’ work life and promote well-being. The site covers over 1,200 m2 of working and recreation space, including a sports club and plenty of social areas.”
“Our work is very creative,” Mr. Kind continues, “so we need to sit around a table together over a cup of coffee and discuss how we will approach each individual customer’s needs. Effectively realising demanding forging requirements requires creativity and discussion. We’ve designed areas to facilitate this, spaces where we can look at drawings, brainstorm, and discuss what’s feasible and how to approach a project. The floors between the offices are called ‘communication areas’ and are very open with lots of natural light. It’s a very relaxed and pleasant work environment.”
Massive machining capabilities
As previously mentioned, R. Kind is very proficient in producing large-scale components. These require exceptionally large machines, and R. Kind continues to invest in state-of-the-art equipment.
“High-quality manufacturing leaves no room for compromise,” explains Mr. Kind. “The basis of our precision work is an optimally aligned production process. This is the only way for us to meet our customers’ requirements and our own high standards. Our in-house manufacturing specialises in turning, milling and drilling work of the highest quality, focusing on the processing and surface finishing of materials that are difficult to machine. With our NC- and CNC-controlled machines, we can meet the most complex requirements in perfect machining quality.”
The company recently purchased two new table-type boring and milling centres with the capacity to handle 3.5 m and 5 m diameter work pieces. “Our workshop has no problem machining alloy parts with a diameter of up to 3.8 meters, rings up to six meters in diameter, and components over 25 meters in length. Our Torni Tacchi (HD3-120H CNC) lathe can machine components with a length of up to 26 meters and a diameter of 1,540 mm – it’s probably one of the longest lathes in Europe. We manufacture all components to the tightest tolerances and highest surface requirements,” explains Mr. Kind. “To meet increasing customer demands, we have also invested in a 5-axis milling line, the Hedelius TILTENTA, which enables us to produce three-dimensional parts.”

Extra-ordinary sizes

At the heart of R. Kind’s business is open die forging projects based on customer drawings. Mr. Kind explains: “Around 95 per cent of our orders are placed directly by end-user customers, which is hardly surprising given the unique characteristics and dimensions of the items we produce. Typically, our products are used in applications that exceed the limits of conventional stainless steel. Every day we work on extraordinary items for projects”.
As mentioned earlier, R. Kind has specialised in products whose size and weight are far above average. “The bigger the better”, smiles Mr. Kind.
“In this segment, we are the absolute professionals. Our team can produce high alloy stainless steels and nickel-based alloy forged parts of up to 50 tons and titanium parts of up to 15 tons.”
Increasing demands on equipment
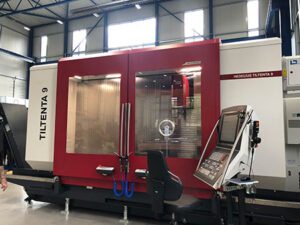
Ongoing investments in cutting-edge technology accommodate the evolving needs of customers, explains Mr. Kind. “We’ve seen a strong trend away from pre-machined components to completely machined, cleaned and ready-to-install components. Today, customers are demanding a plug-and-play service; it makes purchasing processes easier, reduces risk and saves logistics costs.”
The demands on equipment for the (petro) chemical industry have risen significantly over the past 15 years in terms of size and material grades, explains Mr. Kind. “Energy efficiency is crucial. In the past, customers built three different production lines and combined these at the end of the process. Today, they want a single, large production line with the same output because it’s more energy efficient. That’s driving the demand for larger equipment.”
“Secondly, the material requirements are getting higher. After the Deep Water Horizon disaster, extra material margins were added, and higher alloyed grades replaced standard materials. This is particularly true for equipment that needs to run for a long time. On the one hand, we have better control mechanisms and developments for remote-controlled equipment such as underwater testing equipment. On the other hand, customers require more super-critical alloys to be on the safe side. So companies who had used stainless steel or duplex now tend to use nickel-based alloys.”
Projects restarted
The past couple of years have been uncertain for most industries, and Mr. Kind was relieved to see order volumes picking up since the summer of 2021.
“Many projects that were postponed during the pandemic have restarted, and the oil price has increased dramatically, so we are seeing a return to normality in the sectors we serve. While business in Asia is still a little flat, exacerbated by ongoing travel restrictions, exceptions are the Purified Terephthalic Acid (PTA) and polysilicon industries, which continue to thrive. As we supply massive titanium forgings for these plants, it’s helped us that these industries have continued to experience strong growth.” “Within Europe, our business is very strong with orders are pouring in from a wide range of industries. For example, we are now busy producing anti-magnetic stainless steel components for submarine construction; it’s quite a diverse market at the moment.”
The market for large-scale heat exchangers is also very buoyant. “We recently manufactured a forged heat exchanger tube sheet in the material Titan Grade 2 US R50400 / W. No. 3.7035 FM AD 2,710 x 501 mm, with a forging weight of approx. 15,500 kilograms. These impressive tube plates will become the heart of a very large heat exchanger for an FPSO deep-water gas and condensate project in Asia,” explains Mr. Kind. “Another project for the same industry was four seamless, forged heat exchanger tube plates made of Alloy 254 SMO /Alloy F44 / UNS S31254 / W. No. 1.4547 measuring AD 2,700 x 370 mm and with a forging operating weight of 16,900 kilograms. These plates are destined for heat exchangers in an LNG project in Canada, one of the world’s largest energy projects.”
Time to diversify supply chains
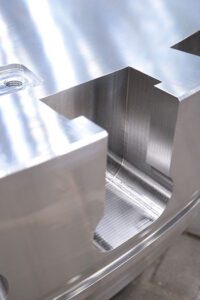
When asked about the implications of the global pandemic on
the industry, Mr. Kind reflects that companies experiencing increasing difficulty sourcing raw materials may choose to re-think their strategy. “It’s clear that many companies who are dependent on Asian suppliers, particularly from China, are suffering major disruptions. This is an ideal opportunity for European manufacturers to diversify their raw material sources because the situation may not improve quickly. For example, the Chinese government is investing so heavily in defence projects requiring titanium that their suppliers may no longer export titanium to Europe. Prices on the world market have risen dramatically, and many raw materials are in short supply. Even companies that purchase complete equipment such as electronics are experiencing problems. It’s time for companies to reconsider where they source their materials and whether local markets aren’t a better long term option.” Fortunately, R. Kind has avoided problems because it sources its stainless steel and nickel alloy ingots from Europe and the US, while its titanium comes from VSMPO-AVISMA in Russia, the world’s largest titanium producer. “Our suppliers have been very supportive, and we haven’t had any major difficulties. Deliveries have been steady and predictable with no serious disruptions to us or our customers.”
Fusion – energy of the future

(material XM19 W.Nr. 1.3964 / diameter 1,850mm) was made with a lot of know-how and precision by Rolf Kind.
Zooming in on the energy transition, there are several business opportunities for the company. Fusion energy is a key technology focus for R. Kind, and it promises enormous benefits for humanity and the planet as a clean, limitless source of energy.
“We’re actually involved in many nuclear fusion projects,” explains Mr. Kind. “We have over two decades of experience in this sector as we’ve produced specialised components for the particle accelerator in the Large Hadron Collider at the European Nuclear Research Center CERN Geneva; and for the experimental nuclear fusion reactor ITER in Cadarache, in the south of France.”
“The wider public perhaps does not realise that this technology is developing rapidly and that there are many experimental fusion reactors either working or under development worldwide. For example, there is the JT-60SA in Japan, K-Star in South Korea, Wendelstein W7X in Germany and CEFTA (Chinese Experimental Fusion Test Reactor) in China. In Europe we have Eurofusion, in the USA the Princeton Institute is developing laser-based technologies, and the Korean Fusion Institute is also very active. I’m excited that the next generation in our company will continue to embrace the many opportunities that this game-changing energy offers.”
Apart from fusion, there are ample opportunities in hydrogen, especially in producing, storing and transporting green hydrogen for various purposes. “Hydrogen will be important as the disadvantages of electric-powered cars become clear. In Germany, car batteries built in Asia using raw materials from South America are politically problematic for environmental reasons. I think electric vehicles are an intermediate phase. In the long term, new technologies are required, and hydrogen will be a key component. It’s an exciting development which Rolf Kind is ready to participate in.”
Stainless Steel World Asia 2022
Rolf Kind is an official sponsor of the Stainless Steel World Asia conference and exhibition, which takes place 26 & 27 October 2022 in Singapore. “We are very much looking forward to Stainless Steel World in Singapore next year. It will be a great event, especially for our Asian customers. Many of our Korean and Japanese customers have already confirmed that they will attend.”
For information, please visit: www.stainless-steel-world-asia.com
Every week we share a new Featured Story with our Stainless Steel community. Join us and let’s share your Featured Story on Stainless Steel World online and in print.
Featured Story by Joanne McIntyre