The RAM3D team in their facilities in Tauranga, New Zealand. Warwick Downing is pictured on the right, second from the top.
A New Zealand company is printing high-end alloy components for some of the world’s most demanding industries in a bespoke facility in the city of Tauranga. Stainless Steel World met with the Chief Executive of RAM3D, Warwick Downing, to learn how the Southern Hemisphere’s largest metal additive manufacturing producer rose to success in just one decade.
By Joanne McIntyre, Stainless Steel World
In 2005, in the early days of metal additive manufacturing (AM), New Zealand engineers Ian Macrae and Warwick Downing sensed an opportunity. They teamed up to research the possibilities for powder metallurgy in the region. “Initially, we researched metal injection moulding, which was well-known worldwide but not yet in New Zealand. That led us to other powder metallurgy techniques. We eventually focused on additive manufacturing because it was new and virtually unknown.”
The following few years were filled with travel as the partners learned as much as possible from European and US research organisations. “At that time, the focus was on plastics, and very few companies did metal AM. In 2008, we established a private research company focusing on powdered metals, which led to our first purchase: an EOS 270M metal AM machine. We installed it and naively believed the manufacturer who had told us we could simply push the start button and begin printing! Of course, it wasn’t as simple as that. We were using alloy titanium 64 and soon realised that additive manufacturing was far more complex than we were led to believe.” The duo spent the next couple of years learning all about the technology. When
they founded RAM3D in 2012, private shareholders provided funding to buy an SLM Solutions 280 machine. Installed in early 2013, it was the company’s first ‘open’ system machine, allowing them to modify operational parameters such as laser power, speed, gas flow, etc. The SLM machine allowed the RAM3D team to establish themselves commercially, leading to a breakthrough order to supply parts to the space industry. Today the company operates an additional ten Renishaw machines. The original EOS machine is based in a research organisation and is mostly used by a local university. The company produces components in alloy titanium 64, stainless steel 316L, stainless steel 15-5, Inconel 718 and Inconel 625.

New mindset required
Designing effectively for additive manufacturing requires a significant change in mindset, explains Warwick. “You must design for the best function achievable for an item, then choose the manufacturing technique based on that. Traditionally, fabricators took a piece of metal, drilled holes where needed, and machined it to finish it. AM creates an entirely new way of looking at the functionality of the components. You need to focus on what you are trying to achieve.”

“A classic example is a valve block, where you start with a large metal block which is drilled and filled, and has some square angles. When you design from an AM perspective, the holes don’t have to be in the same place, they can align differently, and there are no corners, so the flow and pressure drops are different. There are countless options to reconsider the functionality. However, AM will not replace machining, as many of our components still need some machining. It’s an interrelationship.”
“A common myth is that AM always creates a sintered part. While that may be so with a filament-based approach, using a laser results in a melted part with the same strength as a billet, or in some cases, it’s actually stronger. For example, SS 316L is slightly stronger when 3D-printed than billet material, which is an additional benefit on top of the functionality.”
Precision & quality foremost
Because the RAM3D team come from an R&D background, the company culture is one of care and quality. “We carry out extensive testing in-house and have one of the world’s largest databases of tensile results for metal additive manufactured parts,” explains Warwick. “Several universities have tried to buy it; however, it’s solely for in-house use. The data allows us to align very minor changes in the data with variations within the process. We’re always looking for improvements, and none of our machines operate as originally delivered. We’ve developed bespoke laser parameters, operating processes, and powder management systems. Managing the powder is a crucial factor which people often underestimate.”
Modifying technology

Partnerships are key to success in any business, and the RAM3D team work closely with several companies. They have a good rapport with Renishaw, whose representatives have visited to learn about the modifications made to their AM technology.
RAM3D is a development partner for Autodesk Netfabb, with whom they exchange ideas on modifying their software.
“Obviously, we’re doing these modifications for our advantage, but we are happy to share our research so that others can also benefit,” continues Warwick. “For example, our research has enabled us to use Autodesk Netfabb to build significantly larger unsupported areas than we have seen anywhere else.
In fact, we recently had a video call with a machine manufacturer who boasted about the size of unsupported areas their machines could produce: when we showed them what we are doing, it was twice as big!”
“Our strategy is to constantly improve and help our clients, many of whom choose us because of our focus on quality, which largely stems from our R&D roots.”
Another attraction for clients is RAM3D’s competitive prices, due partly to the scale of production the company engages in. “We’re now the largest AM service provider in the Southern Hemisphere, based on information from the last Wholers report.”
Key industries
The space industry is a massive adopter of AM technology and was one of the first, explains Warwick.
“AM allowed private companies such as SpaceEx and Rocket Lab to create cost-effective outcomes, and many satellite manufacturers are following that lead. Around 7,000 of our components have been incorporated into spacecraft. We produce 2,500-3,000 spacecraft components per year for companies worldwide, mostly for propulsion systems. This industry has very exacting requirements. Getting parts flight certified takes a lot of effort, and we’ve managed this with multiple companies.” Customised high-tech racing bikes are another important market.
“These are high-end bikes utilising a lot of titanium and stainless steel, most of which are destined for Europe, the UK, Japan and Australia. We apply the same rigorous quality controls to bikes as for spacecraft components. Our AM machines operate in the same way for every item they produce, regardless of whether it’s destined for space, bikes or the marine industry.”
The company also supplies items for the defence industry, such as suppressors. Oceania Defence, a world leader in firearms suppressors, relocated its business to RAM3D’s factory in 2019, and the relationship continues to go from strength to strength. The suppressors are 3D printed in both Titanium 64 and Inconel 718 powders.
“The military and police have always pushed the boundaries regarding leading-edge technology, so they were early adopters of additive manufacturing. Complex geometries that would be difficult to create using traditional manufacturing can be achieved. Organic shapes, non-uniform sections and hollow areas become possible, leading to a part optimised for function and costs.” The company also prints parts for other industries, including marine, oil and gas, and geothermal energy.

Significant advantages
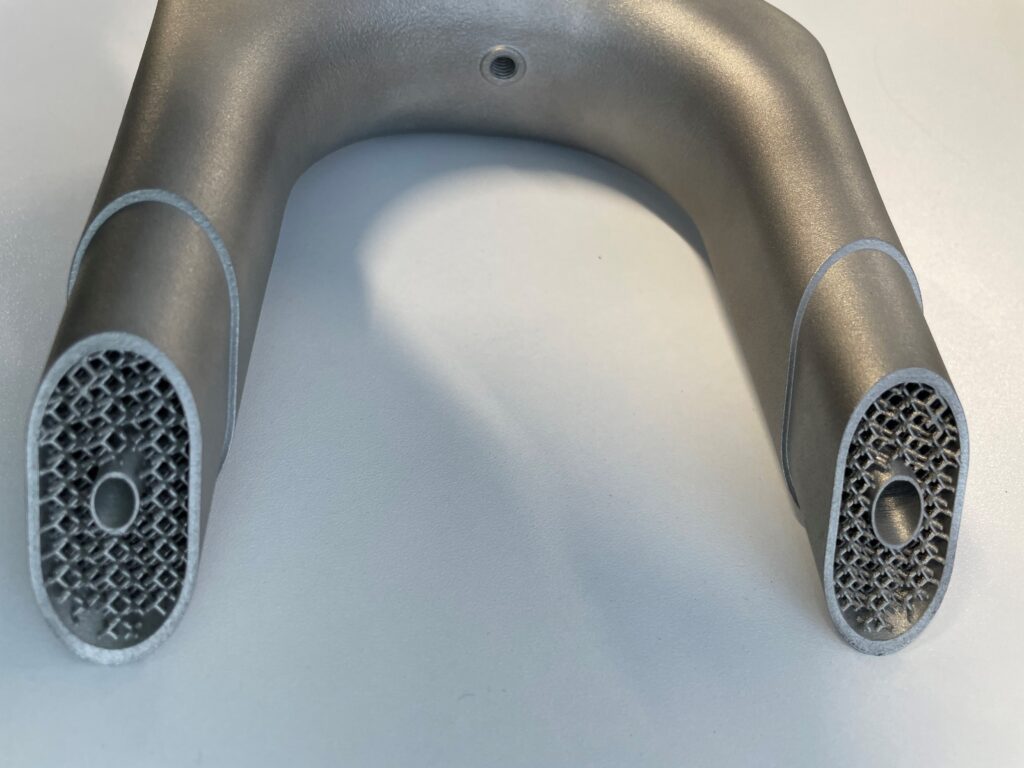
The high complexity of parts at a relatively low cost is the main criterion for clients to choose metal AM, explains Warwick. “It would be too difficult and expensive to produce some aerospace parts any other way. AM products are superior to cast or sintered products as they offer high complexity and lower weight with the strength of a machined part.”
“Racing bikes can be customised very cost-effectively. Many are made to fit an individual rider: sometimes, their name is even printed into the frame! Yet many of our custom bikes are roughly the same price as any high-end off-the-shelf bike.”
Another advantage is that with additive manufacturing, lead times can be reduced to days, shortening the product development cycle. Printing parts on demand also offers an alternative to keeping stock.
Sustainable technology
Although most of their customers are outside New Zealand, the RAM3D team have no problem delivering their products on time.
“New Zealand may seem far away, but we’re very well-connected. The maximum size of our products is approx. 245 x 245 x 300 mm. A bicycle fits into a container smaller than a shoe box, making it simple and fast to freight with a very low carbon footprint. Our metal powder also has a low carbon footprint because there is no wasted space. Indeed, there is almost no waste in the AM industry as 99% of the powder can be reused, and the 5-10% of powder which becomes print support material ends up being recycled as part of the circular economy.”
In the general engineering market, many people don’t yet understand the possibilities that AM offers, explains Warwick. “We are seeing change as young engineers enter the workforce with some background knowledge of 3D printing. I expect this technology will be used in a wider range of industries in the coming years.”
About this Featured Story
This Featured Story appeared in Stainless Steel World August 2023 magazine. To read many more articles like these on an (almost) monthly basis, subscribe to our magazine (available in print and digital format – SUBSCRIPTIONS TO OUR DIGITAL VERSION ARE NOW FREE.
Every week we share a new Featured Story with our Stainless Steel community. Join us and let’s share your Featured Story on Stainless Steel World online and in print.