Seawater desalination is an industrial process used to obtain water for drinking, irrigation or industrial use. Desalination can be achieved using various methods: the most common exploit well-known natural phenomena such as evaporation or osmotic pressure of a saline solution.
Text & images by Inossidable magazine Nr 225 by Centro Inox
Evaporative desalination is carried out thermally by evaporating seawater. The resulting condensation of the steam produced is practically free of salts. Two different industrial processes are used for this method: Multi-Stage Flash (MSF) or Multi-Effect Distillation (MED).
MED and MSF plants
Multi-Effect Distillation plants exploits the phenomenon of the osmotic pressure of two solutions with different saline concentrations on either side of a membrane which is permeable to water molecules and impermeable to dissolved salts. Seawater is pumped against these membranes; water passes through and is collected and the salts which cannot pass through become concentrated and removed. This process has increased in popularity since the 1980s. It is still the subject of studies to improve the quality of the membranes by optimising yield.
Multi-Stage Flash desalination plants (Figure 1) consist of several evaporation stages which generally vary, depending on the desired performance, from a minimum of 15 to a maximum of 20-22.
In these desalinators, preheated and deaerated seawater passes through the tube bundles installed in the evaporation chambers. Flowing inside the tube bundle, on the outside of which the released steam condenses, the water recovers energy by heating itself. Once it has come out of the tube bundle that works at the highest temperature (1st stage), the water is brought to the required temperature with the brine heater and then fed into the first evaporation chamber. Each evaporation stage is connected to a vacuum system capable of maintaining pressure inside the stage which is slightly lower than the equilibrium pressure at the operating temperature. The water evaporates, and the vapour is condensed outside the tube bundle and then recovered
as a distillate. The process is repeated in all subsequent stages, which work at gradually decreasing temperatures and pressures. Part of the brine is extracted and discharged from the last evaporation chamber, while a portion is recovered, mixed with preheated seawater and put back into circulation. A Multi-Stage Flash desalinator requires about 6-9 m3 of seawater for each cubic meter of distilled product.
Multi-Effect Distillation plants contain a number of evaporation chambers (called ‘effects’) which vary according to the desired performance. The evaporation chambers are connected to a vacuum system, which maintains a pressure slightly lower than that of equilibrium at the operating temperature inside each chamber. The seawater is super-heated with respect to the operating temperature of the chamber into which it is injected. It releases steam which is condensed and collected in the form of distillate. A Multiple Effect Desalinator must be fed with approximately 5-6m3 of sea water for each cubic meter of distilled product. In de-salted osmosis desalination plants (Figure 2), seawater is previously filtered and purified. Powerful high-pressure pumps (about 60-65 bar) bring the water to the semipermeable membranes. Some water passes through the membranes to be collected as permeate, while the brine is concentrated and discharged. Reverse osmosis desalination plants require approximately 2.5-4m3 of seawater for every m3 of permeate produced.


Material selection
In thermal and reverse osmosis desalination plants, particular attention must be given to selecting the construction materials as these remain in contact with seawater or saline solutions throughout the plant’s entire life. The two techniques described require different considerations, leading to the use of different types of stainless steel and, above all, different quantities. The main factors that must be taken into consideration when selecting the materials to be used are:
– the fluid in contact with the system;
– the presence of oxygen or chemicals;
– operating temperature;
– operating pressure;
– the part of the plant or equipment under consideration and its required structural and corrosion resistance.

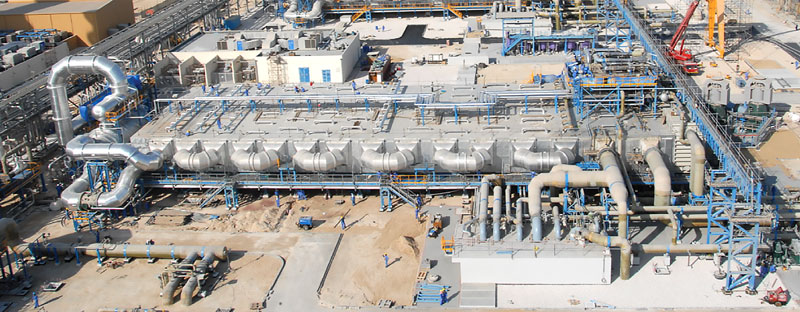
Thermal desalination
In thermal desalination, the steels are selected based on the working conditions:
– fluid: seawater, brine, distillate, non-condensable gases (CO2, O2, chlorinated mixtures, bromine) in the presence of water vapour:
– the presence of oxygen: concentration from a few ppb to a few ppm depending on the sections of the plant;
– the presence of chemicals: in the seawater inlet section, hypochlorite in solution is present (max. 1 ppm expected); possible occasional dosage of acids used for cleaning;
– operating temperature: from 20-35°C at the inlet, up to 110-112°C within the plant;
– working pressure: from absolute vacuum to 6 bar.
These factors and experience have led to the selection of the following stainless steels in the various plant sections:
– aerated seawater: EN 1.4547 (UNS S31254) or EN 1.4410 (type 2507) with a PREN value> 40;
– deaerated seawater or deaerated brine: UNS S31803 or EN 1.4162 ((UNS S32101);
– distilled, drinking water: EN 1.4404 (type 316L);
– non-condensable gases: EN 1.4404, preferably in the versions with high molybdenum content (EN 1.4432 /EN1.4435), or EN 1.4410.
Equipment such as pumps and valves are made from castings. The desalination units are largely constructed using sheets with thicknesses from 4-8 mm for non-structural details and from 8-15 mm for structural parts, partitions, the roof and floor of the evaporator. Sheets are also used to make larger diameter pipes. Figure 3 shows a cross-section of a Multi-Stage Flash desalinator. The dividing walls, floor, roof and the lateral walls of the evaporator, which are coloured green, are made from sheets of high-alloy steel.
Steels in reverse osmosis desalination
The operating conditions to which steels are subjected to during desalination by reverse osmosis are:
– fluid: seawater, brine, permeate;
– the presence of oxygen: some ppm depending on the solubility of oxygen in seawater;
– the presence of chemical substances: the seawater inlet may be exposed to the occasional presence of hypochlorite in solution (expected max. 2 ppm), acid/base dosing for pH correction and for surface cleaning;
– operating temperature: from 20-35ºC;
– working pressure: up to 70 bar.
Subsequently, the selection of materials is as follows:
– aerated seawater or aerated brine: EN 1.4410 with PREN> 40;
– permeate, drinking water: EN 1.4404.
The indicated selection concerns:
– equipment such as pumps and valves that are made from castings;
– high-pressure seawater and brine pipes.
Reverse osmosis systems are considerably more ‘compact’ than thermal systems, whether they are Multi-Stage (MSF) or Multiple Effect (MED). Figure 4 shows the overall view of a multi-stage plant. Figure 5 shows the vertical pipes for feeding seawater to the membranes: for a reverse osmosis system, they work at a pressure of about 60-65 bar and are constructed from EN 1.4410. Pipes operating at lower pressures at 5-10 bar are usually constructed from plastic materials such as fibreglass. Figure 6 shows the high-pressure pump used to feed seawater to the reverse osmosis membranes constructed from casting Gr 5A duplex (ASTM A995).

Quantities of stainless steel in desalination plants

The quantities of high-alloy stainless steel used in desalination plants depend on the type of system (thermal/reverse osmosis) and plant capacity.
Experience shows that a medium-sized thermal desalination plant, which produces about 1500 m3/h of distillate, requires 900-1000 tons of stainless steel. This evaluation includes the steel required to construct the desalinator, connecting pipes, equipment such as pumps and valves for the desalinator, and the main auxiliary systems.
For reverse osmosis systems, the use of high-alloy stainless steel is limited to the pumps, valves and tubes working at higher pressures. These plants require far less stainless steel than thermal desalination plants; for example, a plant producing 1500m3/h of permeate requires about 30-40 tons of the aforementioned materials.
Like all industrial installations, even desalination plants, whether thermal or reverse osmosis, are subject to a scale factor. Therefore, an increase in the plant’s production capacity does not result in a linear increase in the quantities of stainless steel required.
Acknowledgement: Thanks to the company Fisia Italimpianti SpA for the material provided
About Centro Inox
This article was provided by Centro Inox (through its magazine Inossidabile), a non-profit association involved in the study and development of stainless steel applications in Italy. For information visit www.centroinox.it/
About this Featured Story
This Featured Story appeared in Stainless Steel World November 2022 magazine. To read many more articles like these on an (almost) monthly basis, subscribe to our magazine (available in print and digital format – SUBSCRIPTIONS TO OUR DIGITAL VERSION ARE NOW FREE) .
Want to contribute as author? Please contact Joanne.
Every week we share a new Featured Story with our Stainless Steel community. Join us and let’s share your Featured Story on Stainless Steel World online and in print.