Feeding a growing global population presents a significant challenge, with the world’s population expected to climb from 7.9 billion people currently to around 9.7 billion people by 2050, according to the United Nations. Ensuring food security in the face of limited land availability, climate change, and water scarcity make the problem more challenging. Fertilisers have an important role to play, helping to increase crop yields, soil fertility and crop resilience.
By Rodney Rice, Langley Alloys
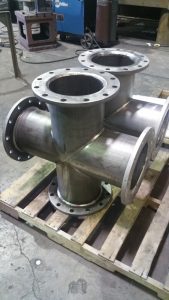
Inorganic fertilisers are manufactured via a number of different means, such as processing natural mineral deposits to make potassium-containing fertilisers, or synthesising nitrogen-based fertilisers from ammonia using natural gas as a source of hydrogen along with atmospheric nitrogen. For phosphorus-based fertilisers, the process relies upon the production of phosphoric acid from naturally occurring phosphate rock, which is subsequently reacted with ammonia to form various compounds. Equipment used during fertiliser production processes needs to operate continuously despite the aggressive conditions. Those found during the manufacture of phosphorus-based fertilisers include the combination of:
- Erosion corrosion from solid particles. For the phosphorus-based fertilisers, abrasive conditions exist in the “attack tanks” as the phosphate rock is broken down in the presence of an acid such as sulphuric acid. Components such as agitators and mixing tanks need to withstand the physical erosion that occurs due to the high velocities of this particulate matter. This can lead to far quicker corrosion than if the metal was exposed to the acid solution alone – as the protective ‘passive layer’ can be damaged and removed by the highly abrasive conditions found when the phosphate rock is broken down in larger tanks employing agitators.
- Effects of elevated temperature. Processes are operated at elevated temperatures, typically up to 110°C/230°F, to increase the productivity of the process steps.
- Uniform corrosion from sulphuric and phosphoric acid. Sulphuric acid is commonly used during the early process stages before phosphoric acid is subsequently formed and concentrations between 20-50% are common.
- Uniform corrosion from impurities(HF, H2SiF6 etc.).
- Localised corrosion due to chlorides. The presence of impurities will depend upon the source of the phosphate rock, so different plants may experience varying conditions.
- Localised corrosion under deposits during filtration.
The design and operation of the process might also encourage more challenging conditions than anticipated. Despite agitation, dead spots can occur within tanks and pipework, and deposits during filtration could also accelerate corrosion.
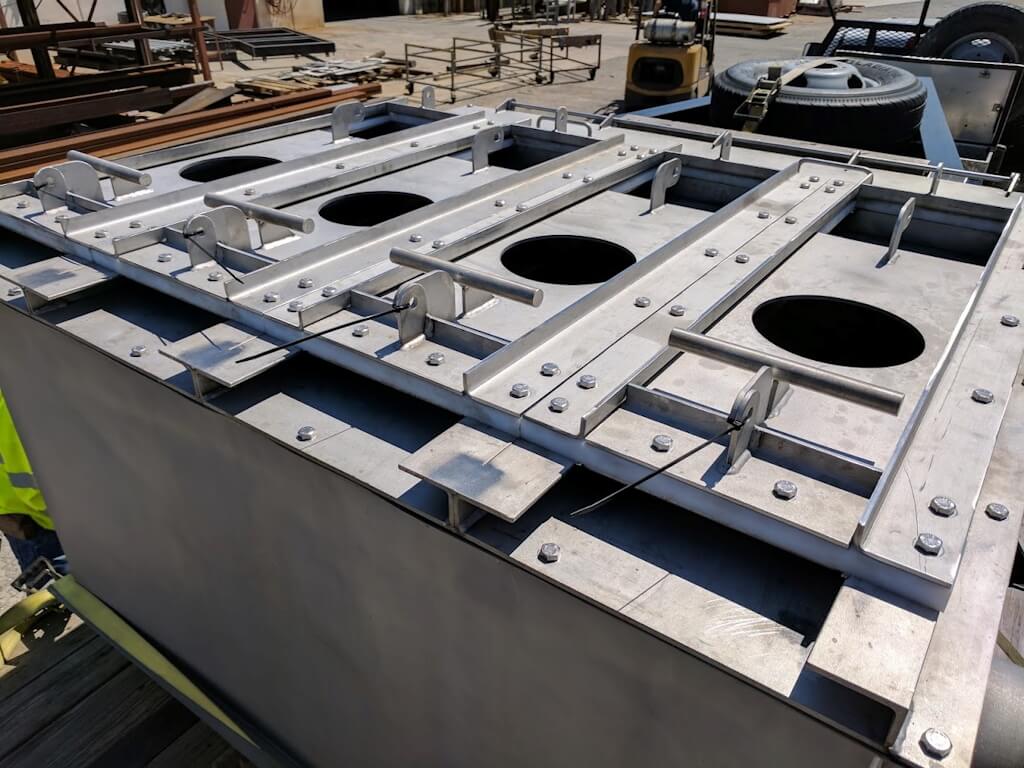
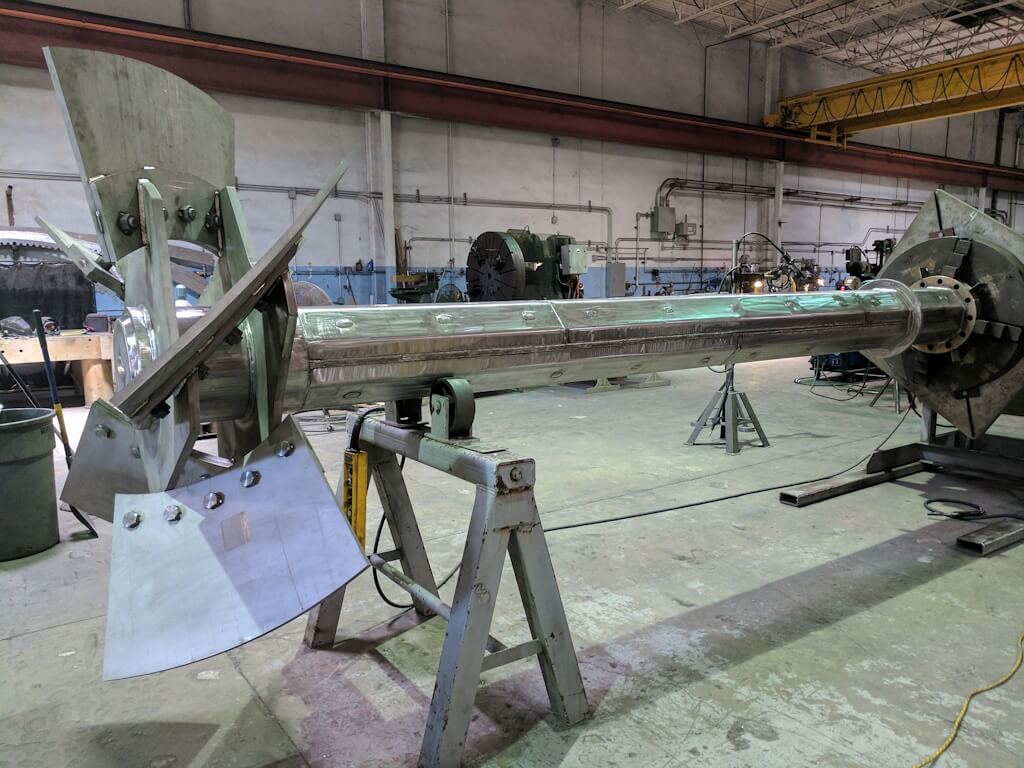
Ferralium 255 meets the challenge
Fortunately, the attractive properties of super duplex stainless steels are well suited to these myriad challenges, leading to their ongoing use in equipment throughout fertiliser production processes worldwide. Rodney Rice, director of Langley Alloys shared, “We have supplied our Ferralium 255 (S32550) super duplex stainless steel grade to projects over many years. Various technical papers have demonstrated its superior performance over more highly alloyed, and therefore more expensive solutions, such as the super-austenitic stainless steels Alloy 904L and Alloy 254. This can be attributed to the combination of desirable physical and mechanical properties – combating the combined effects of abrasion and corrosion. The higher strength makes for more effective material use – reducing the weight and cost of fabricated components, so it’s a win-win for end users.” Ferralium 255 was the first commercial grade of super duplex stainless steel available, having been patented by Langley Alloys in 1968. This grade is built around a 25% chromium content, utilising nitrogen as a cost-effective alternative to nickel, reducing the alloy’s cost whilst increasing its relative resistance to pitting corrosion. The other significant part of its composition is the inclusion of up to 2% copper, known to be particularly effective in resisting sulphuric acid – an effect also used in other copper-containing alloys such as Alloy 825 and Alloy 20. In bar form, the yield strength is higher than alternative grades, achieving >85ksi compared with >80ksi for others.
Rice continues, “Ferralium was produced under licence by Haynes International in the USA throughout the 1980’s, and they did an excellent job of demonstrating its performance in use. Although we like to mention the use of Ferralium 255 in the refurbishment of The Statue of Liberty, the most valuable work was done convincing the many operators of its virtues in industrial applications. In later years, after the Langley Alloys patent had lapsed, Industeel also promoted a similar grade under their Uranus 52N+ designation, for this application. The result of that collective effort is a continued demand for Ferralium 255 from end users that have had positive experiences in their operations.”
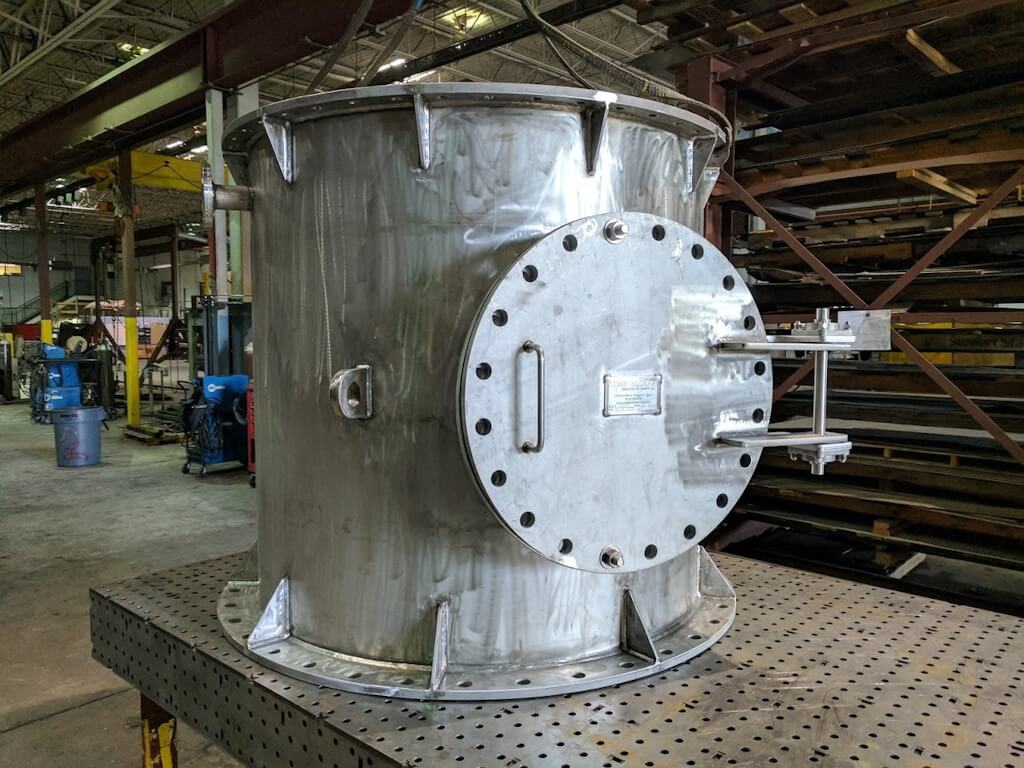
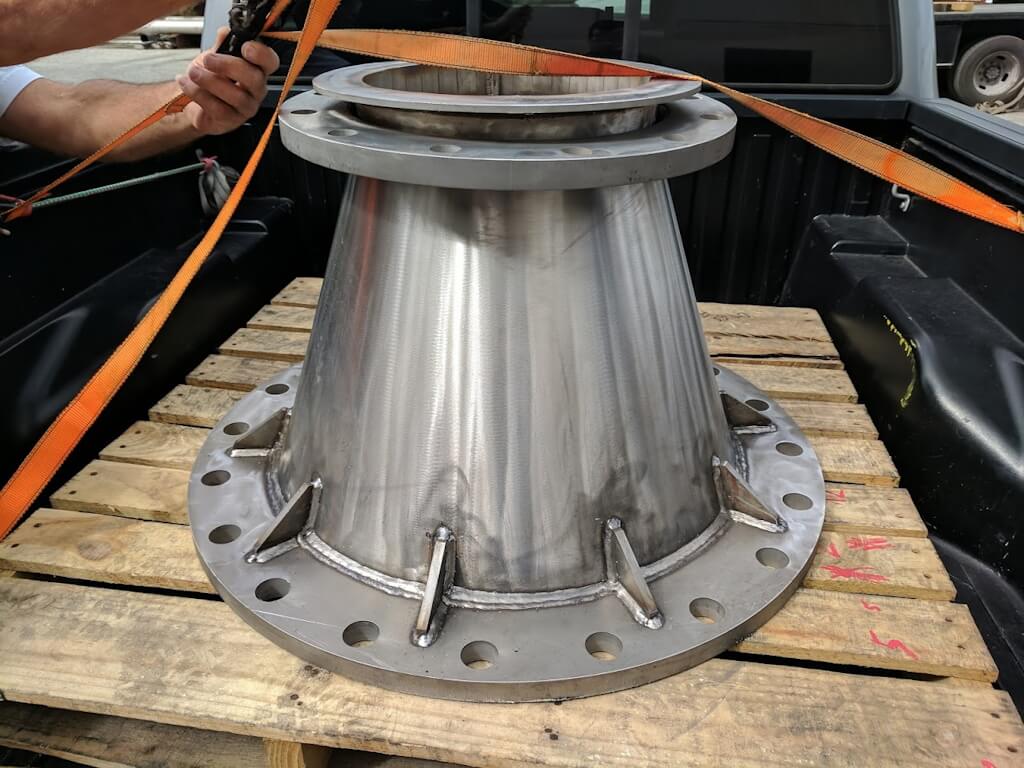
Ferralium plate & bar
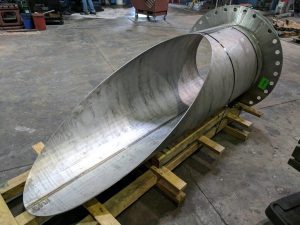
“The images shown include a range of components fabricated by Metalcraft Inc (USA) from recent projects,” continues Rodney. “They include a very large agitator, fabricated from plate rather than using a solid bar shaft, together with bolted blades to allow their straightforward replacement. The ‘splitter box’ serves as a distribution point for phosphate (P2O5) solution coming from the evaporators (at 28%, 40%, and 50% acid concentrations respectively) going to primary storage tanks. Its design has been customised by the plant operators to aid routine maintenance. Connectors, reducers and other sections of process pipework were also produced in this grade, mostly fabricated from plate.” “Although weldability has historically been seen as a limiting factor in the uptake of super duplex stainless steels, those fabricators who are routinely processing such grades find them no more complicated than many other metals. Just a case of using the correct consumables and following qualified weld procedures. Our customer Metalcraft Inc continues to produce a wide range of components in Ferralium 255, with positive feedback from the end user.”
“As well as projects in North America, we are routinely providing metal to end users across North Africa and Europe for the fabrication of very similar components. Off-gas impeller fans are also another common application we supply, for fertiliser production and mining applications. The challenges remain the same, with particulate matter, high throughputs and the presence of corrosive wet fume combining.”
“Not all applications are fabricated from plate, for instance smaller agitators may use a solid bar as the shaft, with plate only used for the blades themselves. We are also supplying Ferralium 255 bar, sometimes with additional heat treatment processing, machining and inspection, to produce pump and valve components for new facilities.”
With fertiliser production expected to continue growing year-on-year, the ongoing use of this family of super duplex alloys is almost certain to continue – that combination of their high strength, excellent corrosion resistance, cost effectiveness and ready availability proving a winning combination.
About this Featured Story
This Featured Story appeared in Stainless Steel World April 2024 magazine. To read many more articles like these on an (almost) monthly basis, subscribe to our magazine (available in print and digital format) – SUBSCRIPTIONS TO OUR DIGITAL VERSION ARE NOW FREE.
Every week we share a new Featured Story with our Stainless Steel community. Join us and let’s share your Featured Story on Stainless Steel World online and in print.