The Hempel Special Metals Group is an international sales specialist for highperformance materials in demanding industries such as implants, offshore, aviation and the process industry.
The company has been active in distributing nitrogen-enriched stainless steels since 2004 when it patented grade 316LMoNCu (1.4435NCu). This stainless steel has added nitrogen to create a delta-ferrite free material in demand most notably for the high-end watches.
Another alloy the company is selling in that field is the P2000, a double melted no nickel, high containing nitrogen austenitic stainless steel, which has interesting properties for special bearings, springs and for medical applications.
Finally the company offers the 1.4318 which is a low-nickel 304 standard grade. Given the volatility of nickel prices, nitrogen and manganese added, low-nickel stainless steel offer interesting economical alternatives with superior properties as increasing strength.
Hempel’s

Hempel has in-house shear-, plasma-, waterjet- and laser cutting facilities
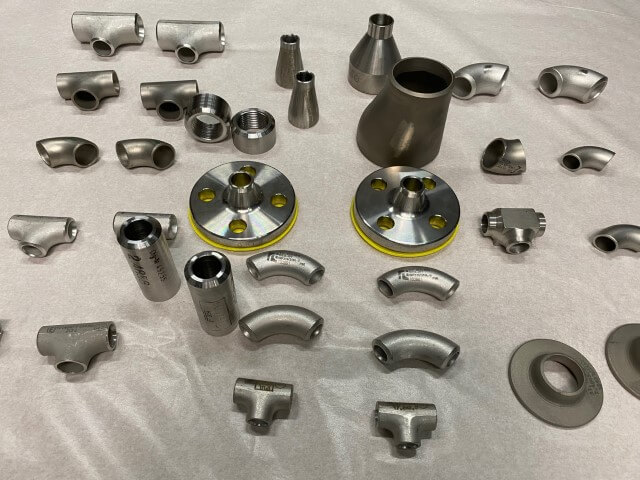
Hempel produces a very wide range of fittings and machined components, including German pressure vessel regulation AD 2000 accredited fittings.
Continued growth through diversification
“With the development of Alloy 24, a new austenitic stainless steel has become available – delivering the highest strength and excellent weldability with outstanding corrosion resistance in chloride-containing media,” explains Mr. Kirchheiner.
What is Alloy 24?
Alloy 24 is a super austenitic alloy that positively distinguishes itself from classic stainless steels, duplex and other alloyed 6%Mo steels. In a variety of industrial applications, ìt can replace the established lower representatives of nickel-based alloys.
With their highly developed application potential, super austenitics fill the gap between the standard grades of stainless steels and nickel-based alloys.
One of the driving forces for the use of super austenites is economy, as they must be able to stand up technically and economically against the higher alloyed nickel-based alloys. The technical superiority of super austenites over standard steels is assumed, and Alloy 24 is an outstanding example of this.
The neutral designation ‘Alloy 24’ is derived from the proportion of the materials average chromium content of 24%. The material number for the original material is 1.4565; the UNS number is S34565. In Alloy 24, the role of the cheapest alloying element nitrogen (N max 0.6%) is exploited in several ways. Nitrogen has several positive features in the formation of the fully austenitic structure of Alloy 24:
- Austenite stabilisation
- Significant increase in strength
- Minimisation of negative carbide precipitation
- Increase of corrosion resistance in synergy with chromium and molybdenum
This technically and economically sophisticated alloy design allows Alloy 24 to be labelled as a Smart Super Austenite. The chemical composition is shown in Table 1.
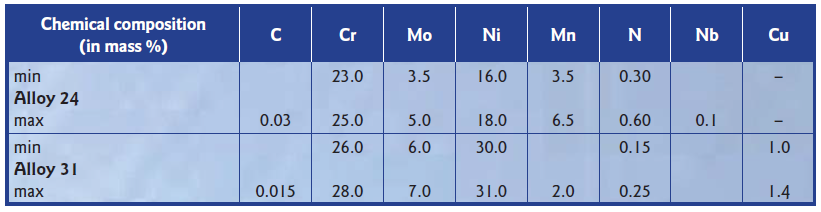
Table 1. Chemical composition of Alloy 24/1.4565 (nominal) and Alloy 31 (1.4562)

Figure 1. Critical pitting & crevice corrosion temperatures in FeCl3 solutions; tests acc to ASTM G48 E & F (1)
(1) PREN = %Cr + 3.3 x %Mo + 30 x %N2 > Calculation focused on pitting corrosion
Corrosion behaviour
Testing Alloy 24 in ferric chloride solution according to standard ASTM G 48 (E), an actual critical pitting temperature (CPT) = 85°C was determined. Under these testing conditions, the same CPT was achieved only by the Ni-base Alloy 625 N06625 (Figure 1).
Similar behaviour was found testing Alloy 24 in ferric chloride solution under crevice conditions according to the MTI standard or ASTM G 48 (F). Again, the actual critical crevice temperature range of 45-55°C is achieved only by the Ni-base alloy 625, under the same conditions.
Value creation through new services and acquisitions
In addition to launching new materials such as Alloy 24, the Hempel team continues to focus on value creation in its business development. New services are being integrated, among other things through acquisitions. Firmus Metals was purchased in the UK in 2016; TK Fittings in Germany one year later. The companies fit well into Hempel’s strategy, bringing new services (precision slitting and production of fittings) into the proven range of materials. The company is continuously renewing and expanding its workshop equipment. In Oberhausen, a new plasma cutting machine with a 12.x meter bed was installed in 2019.
“We are constantly expanding our valueadding services for customers and can provide complete packages of specialist steels, cut, forged and machined,” explains Mr. Hempel.
Hempel produces a very wide range of fittings and machined components, including German pressure vessel regulation AD 2000 accredited fittings.
The company is qualified with the German pressure vessel regulation AD 2000, which allows it to produce certified fittings for this sector. Hempel has a long history of forging strong partnerships in the industry.
“You cannot develop success in our industry without the right partners,” explains Mr. Hempel. “We’ve done this with producers of titanium and stainless steels, we enjoyed a strong partnership with VDM for more than 30 years until 2008, and have optimised a special stainless steel for the watch industry together with our Japanese mill. Moreover, several other semi-product producers are long-term partners. So today we’re building up our close partnership with the mill producing Alloy 24. Working together with them and other stakeholders, we see a huge potential for Alloy 24.”
Technical Expertise
The Hempel team knew they needed an in-house expert to reintroduce Alloy 24 to the market effectively. Therefore, Mr. Rolf Kirchheiner (Dipl-Ing. / Master of Science) was recruited to the team last year.
“He was the right expert for us since we have known him for more than 20 years, the time he worked within VDM’s R&D and technical marketing,” explains Mr. Hempel. “He was involved in the initial development of both Alloy 24 and Alloy 31 and was, in fact, one of the patent holders for Alloy 31. He was deeply involved in the research and market qualification for Alloy 24. His expertise will be very valuable to promote the alloy further.”
About this Featured Story
This Featured Story is an abstract of the 4 page Featured Story in our Stainless Steel Magazine. To read the full Featured Story and many more articles, subscribe to our print magazine.
Read the full story.
“Every two weeks we share a new Featured Story with our Stainless Steel community. Here you can find here the online abstract, and you can access the full story in our print magazine. Join us and let’s share your Featured Story on Stainless Steel World online and in print.”
– FEATURED STORY BY JOANNE MCINTYRE