Featured Story: BUTTING – More than pipes
BUTTING is a renowned pipe specialist with a worldwide reputation. More than 44,000 tons of its longitudinally welded stainless steel pipes and clad pipes are used in many industrial sectors each year. However, BUTTING offers much more than this. Do you require prefabricated pipelines, vessels or sophisticated components? Then BUTTING is your partner. Extensive production capacities are available at its plants in Knesebeck and Schwedt in Germany, and in Tieling in China.

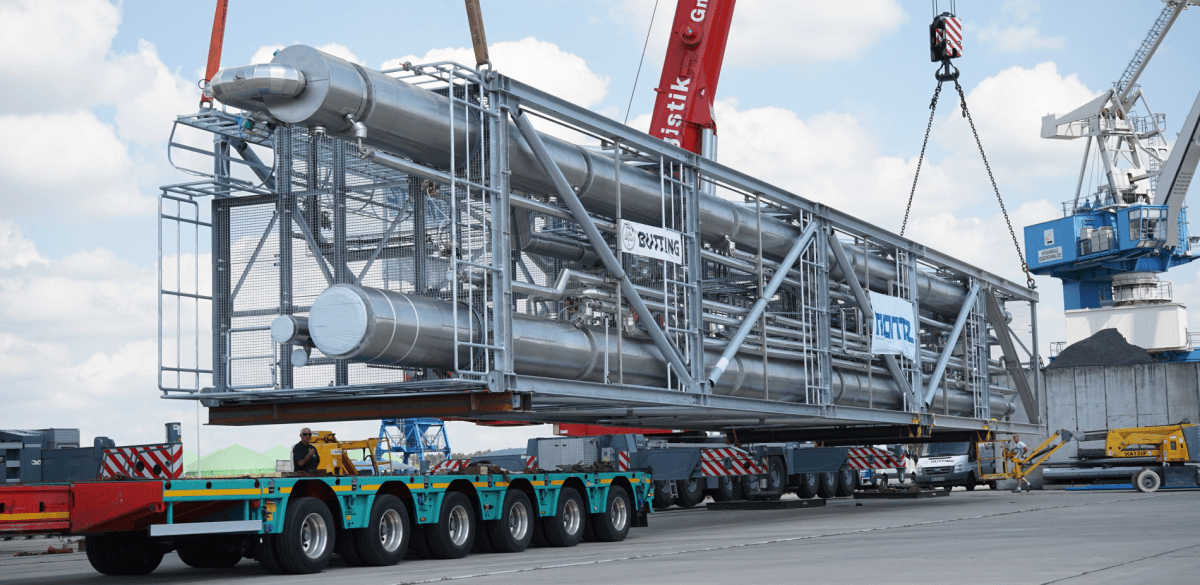
The use of semi-finished products from own production and extensive prefabrication with a high degree of automation, supported by highly
qualified staff, guarantee first-rate product quality and high operational
safety.
State-of-the-art equipment and expertise in forming, milling and welding technologies are put to the test at BUTTING on a regular basis. For example, BUTTING Anlagenbau in Schwedt has a vessel production line equipped with innovative welding automats.
The family business undertakes extensive prefabrication of stainless steel pipelines and vessels according to models, isometric drawings, piping plans, as well as their assembly on behalf of its customers. Performing
preparatory assembly work at the corresponding production sites optimises the quality of the pipelines, ensuring end-users in many industrial fields receive ready-for-installation products at fair prices.
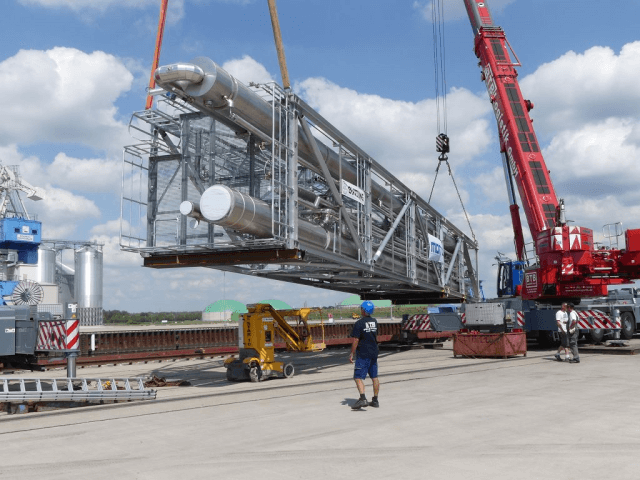
Marcel Bartels, Managing Director of BUTTING International, states:
“In terms of prices, our production location in China provides our customers with a clear advantage in a market where stiff competition prevails. Industrial sectors suffering from heavy pressure on prices benefit from our various locations and can commission European project management if they wish.”
At all locations, in-house construction departments take on upstream project tasks. The Managing Director adds: “The layouts for vessels and tanks according to all international standards are our daily business at all our production sites, however, in China, complete preliminary designs of vessels according to ASME, API or EN are also possible. Upon request,
BUTTING is also able to support customers with the design and construction of pipelines according to their unique requirements, thereby
improving the planning quality and reducing production throughput times and costs.”
Many industrial sectors are won over by the high product quality and great
savings potentials prefabrication offers, e.g.
• chemical and petrochemical industry
• water treatment plants
• oil and gas industry
• power and environmental engineering
• paper and pulp industry
Many examples from the past years are proof of the broad competences.

Skids for seawater desalination in superduplex.

By extensive prefabrication and further processing BUTTING is
able to optimise the quality of the pipelines and offer products
ready for installation at reasonable prices.
Summing Up
BUTTING in Knesebeck was commissioned for the production of four tanks and numerous spools for the pipelines required in the FPSO’s Sulphate Removal Unit of the Johan-Castberg project. For the majority of the spools, super duplex material was specified due to the operating conditions in the Barents Sea.
Dieter Kleen explains: “More than 2,000 spools, a total of more than 96 tons of material, were prefabricated by us such a way that they could be installed on-site with a minimum effort.” In case of such complex orders,
BUTTING in Knesebeck not only demonstrates its expertise in production engineering: the vast number of pipeline components had to be carefully coordinated and managed in terms of production planning and logistics.
Acceptance under the internationally recognised NORSOK standard is mandatory for material used in the Norwegian offshore industry. Several
inspectors were constantly present right from the start of production and
confirmed that BUTTING in Knesebeck fully complied with the NORSOK
regulations.
“The production of components for an FPSO is one of the most demanding
tasks in the field of marine technology. The special materials, the stringent
requirements on tolerances, welding technology, forming technology and
quality assurance are unique. We were able to deliver our products to the
complete satisfaction of our customers, and inspired them,” says Dieter Kleen, drawing a positive conclusion.
Video
BUTTING is a seventh-generation family business that has grown steadily for more than 240 years. With our products made of stainless steel and clad materials, we contribute to a better quality of life in everyone’s everyday life.
The Schwedt site is our expert unit for tank and pipeline construction, international assembly and industrial services. With over 350 employees, more than 14,000 square meters of hall space and hall heights of up to 21 meters, extensive capacities are available.
For our family business, training is an investment in the future – in the future of the company and in the future of young people. Therefore, we offer highly qualified training in which we impart extensive theoretical and practical knowledge.
About this Featured Story
This Featured Story is an abstract of the 4 page Featured Story in our Stainless Steel Magazine. To read the full Featured Story and many more articles, subscribe to our print magazine.
“Every two weeks we share a new Featured Story with our Stainless Steel community. Here you can find here the online abstract, and you can access the full story in our print magazine. Join us and let’s share your Featured Story on Stainless Steel World online and in print.”
Read the full story.
– FEATURED STORY BY BRITTANI SCHROEDER