Picture credit: NASA.GOV
2020 marked the start of an exciting new decade in space exploration and innovation with nickel-containing alloys playing an important role in the construction of rockets, wheels, and catalysts, to name a few applications.
By Geir Moe, PEng., Nickel Institute
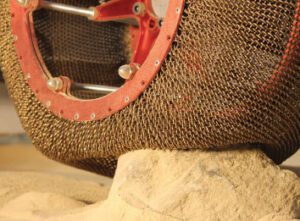
SpaceX, the American company committed to aerospace manufacture and reusable space transportation, fabricated its Starship and Super Heavy rockets from a version of nickel-containing 304 (S30400) stainless steel. SpaceX selected stainless steel for the job because it is inexpensive compared to carbon fibre which costs over sixty times more per kilogram. It is also much more resistant to heat than carbon fibre or other metals such as aluminium and thus requires much less, or possibly no, additional heat shielding.
Meanwhile, NASA is exploring another potential application for nickel-containing materials in the wheels of its Rovers. Rubber wheels are impractical on the Moon or Mars, so the wheels on the original Apollo Lunar Rovers were constructed from spring steel. However, spring steel wheels will deform on the larger and heavier vehicles that are designed to be used on Mars. To combat this, NASA is currently developing a metal mesh tire constructed from Nitinol (UNS N01555), a nickel-titanium alloy, with shape memory properties which can handle 30 times the deformation of the spring steel wheels.
With the goal to eventually transport humans to Mars, the SpaceX Starship with a Raptor rocket engine is one of the first to be powered by liquid methane and liquid oxygen and designed to be reused 1,000 times.
Methane was selected because of the intent to produce rocket fuel on Mars to fuel the return trip. Methane can be produced from carbon dioxide and hydrogen through the Sabatier reaction, where hydrogen reacts with carbon dioxide at elevated temperatures (optimally 300–400 ºC) and high pressure with a catalyst, to produce methane and water. One of the possible catalysts is nickel. While the Martian atmosphere is composed of 95% carbon dioxide, NASA has confirmed the presence of water on Mars, the raw materials necessary to produce methane and oxygen as a rocket propellant as well as breathable oxygen for the astronauts. And the low ambient temperature on the red planet, plus the low temperatures required for handling liquefied methane, hydrogen and oxygen will also require nickel-containing materials.
Ni-Cu Alloy K-500 (N05500) also possesses excellent ductility at cryo-genic temperatures and resistance to ignition in pure oxygen. This makes it a preferred choice in oxygen boost pumps supplying oxygen to the rocket engine.
One-piece rocket engines

Alloy 718 is the workhorse of super alloys. A high-strength, corrosion-resistant nickel-chromium alloy used in the temperature range of -252 ° to 700 °C (-423 ° to 1300 °F). Its strength and resistance to oxidation at high temperatures make it a top choice for rocket engines. And its ductility at cryogenic temperatures enables its selection for tanks holding liquefied rocket fuel.
With its high strength and toughness, Alloy 718 (N07718), a precipitation- hardenable nickel-chromium alloy used in aircraft turbojet engines, is also used in rocket engines and pressure vessels so they can handle cryogenic liquefied gases for pro-pulsion down to -250 °C. However, Alloy 718’s properties make machining and forming more difficult than other materials. Investment casting can be problematic as Alloy 718 is susceptible to porosity, segregation and very coarse grain sizes, which calls for subsequent processing steps.
The solution? 3D printing allows for more efficient utilisation of nickel- base alloys, such as Alloy 718, in high-performance applications with complicated designs.
3D printing can make Alloy 718 processing more convenient, straightforward and ensure material properties are well preserved. This process avoids welding and machining and thus minimises material waste.
The benefit of this manufacturing method is demonstrated by the 3D printed Alloy 718 rocket engine prototype, which was entirely designed by artificial intelligence – and developed by German software company Hyperganic.
Unlike a traditional rocket engine, which consists of individually designed parts that are joined together, the 3D printed prototype is one continuous piece. It includes the combustion chamber where fuel and oxidiser are burned, as well as the surface channels through which the fuel is circulated to cool the chamber and keep it from overheating. The one-piece fabrication results in the lowest weight and most effective cooling, providing the highest possible performance for a given rocket.
3D printing has also been used by the University of California at San Diego in the Ignus II Alloy 718 rocket engine for their Vulcan II rocket project.
With each new application, nickel is helping space exploration go further in the future.
About the Nickel Institute
The Nickel Institute is the global association of leading primary nickel producers. Its mission is to promote and support the proper use of nickel in appropriate applications.
For information, visit: www.nickelinstitute.org
Every week we share a new Featured Story with our Stainless Steel community. Join us and let’s share your Featured Story on Stainless Steel World online and in print.
Featured Story by: Geir Moe, PEng., Nickel Institute
All images were taken before the COVID-19 pandemic, or in compliance with social distancing.