Story by: James Chater
In recent years, the fate of 3D printing and special metals have become intertwined. Manufacturing in titanium has become both easier and more sustainable, bearing fruit in better products and new alloys. Aerospace and orthopaedics are the industries that benefit most, but auto parts, sports equipment, tooling, mining and oil & gas are also increasingly reliant on 3D-printed titanium. The recent pandemic disrupted the titanium markets, but the long-term fundamentals have not changed.
Market overview
As luck would have it, Covid-19 dealt the titanium industry – and titanium powders in particular – a double blow. Two of its most important markets were affected; aerospace and orthopaedics. Commercial aircraft were virtually grounded, with 2020 seeing the worst ever year in aviation; orthopaedic implants were delayed while hospitals used their limited capacity to cope with Covid patients. Once the pandemic is over, however, we can expect pent-up demand to be released. The price of oil, which famously turned negative in spring 2020, has bounced back to pre-Covid levels, eloquently making a case for lightweight metals such as titanium to be used to save weight and fuel in aircraft, racing cars and motorbikes.
3D printing
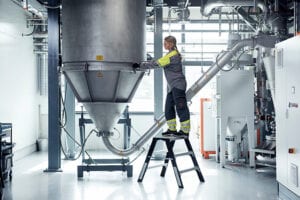
A number of new projects show that 3D printing is still a growth industry, with titanium playing a crucial role. Prominent among these is Sandvik’s titanium powder plant, inaugurated in Sweden in late 2019. The purpose was to profit from the growing trend in 3D-printing of titanium parts and break free of the restrictions and waste of machining titanium billet. Sandvik thereby dramatically extended their titanium offering to industries such as aerospace, medicine, mining, sports equipment and machining.
A number of other projects and agreements paint a similar picture: 5N is to distribute Metalpine’s metal powders in North America; an Australian company, Titomic, is developing its TKF kinetic fusion process for 3D-printing of Ti parts using CP Ti grade 2 powder and has signed an agreement to supply AP&C; Germany’s Philipp Group is to start 3D printing of titanium aircraft parts.
Titanium also plays a role in manufacturers’ efforts to improve the strength of 3D-printed components. Researchers at RMIT University (Melbourne) used Ti-6Al-4V and Ni superalloy Inconel 625 to demonstrate the use of ultrasound to vary microscopic structures, shaking alloy grains into tighter formations during 3D printing. Airbus Defence and EOS Technology were able to exploit 3D printing technology to redesign the titanium brackets of satellites to eliminate thermal stress that weakened the connection of the brackets with the carbon panel of feed and reflector assembly.
New Ti alloys
Additionally, 3D printing is driving the development of numerous new materials, including Ti alloys. For example, RMIT University led a project to develop titanium-copper alloys with ultra-fine grain size to overcome the problems of cracking and distortion associated with alloys using column-shaped grains. These stronger alloys will make 3D printing more viable across a range of industries, from aerospace and defence to hydraulic systems, compressor blades, medical implants, sporting equipment and more.
Aerospace

Aerospace is still the main market driver, and a virtuous circle has been established whereby 3D-printed components lead to better strength-to-weight ratios, leading to more efficient aircraft requiring 3D-printed components. Titanium is at the centre of all this. It is a leading metal in the drive to create lighter components for greater fuel efficiency. This can be shown from GE’s new turbofan engine the GE9X, which sets new standards for efficiency, emissions and quietness and is to be used on Boeing’s wide-body, long-range airliner the 777X. TiAl has replaced nickel in the low-pressure turbine airfoils for greater lightness and strength. The airfoils were 3D-printed to create a design that would have been impossible using traditional manufacturing. The same aircraft will have titanium engine exhaust systems made by Aircelle (Safran). These come with a complex nozzle shape to improve the aerodynamic flow of exhaust from the engines.
Meanwhile, Rolls-Royce is developing its UltraFan jet engine, which will enter commercial use later this decade. It will reduce fuel burn by 25% compared with existing Trent engines and will have the world’s largest fan blades, made of carbon-fibre pre-filled with resin. Each blade is finished with a thin titanium leading edge, which offers protection against erosion, foreign objects and bird strikes.

Boeing rival Airbus has also been making headway with 3D-printed titanium parts. The Toulouse-based company has speeded up the production of its A320 family by using a Concept Laser M2 printer from GE Additive, which can use two lasers simultaneously. Airbus has also signed a contract with Norsk Titanium for the 3D printing of aircraft parts. Its wide-body A330-800, which received EASA and FAA certification in February 2020, achieved its first deliveries in October 2020.
Apart from commercial aircraft, titanium plays a major role in rocket technology and space vessels, as well as in drones. It is now possible to 3D-print entire rocket engines. In November 2019 Titomic, an Australian manufacturer, unveiled a 5.5-metre-long rocket which was 3D-printed in just 27.6 hours.
The same company has produced the world’s largest 3D-printed drone, using a patented method to spray titanium particles onto the printing medium at high speed.
Titanium on Mars

If human settlements ever take shape on Mars, the settlers will not be short of the minerals they need, as the red planet holds abundant resources of minerals such as iron, nickel, aluminium, sulphur as well as titanium.
Many, if not all, of the vessels that have landed on Mars make use of titanium in their construction. The recently deployed Perseverance Rover has six wheels, each with its own motor and their legs and spokes are made of titanium, a tough, springy material able to sustain the bumps and knocks of Mars’s rugged terrein.
Auto
3D-printed titanium is also being used in other industries. The auto sector is turning more and more to 3D printing. The Bugatti sports car maker uses selective laser melting to 3D-print brake calipers in Ti6Al4V and titanium exhaust systems on its Chiron Pur Sport, for weight reduction and heat resistance. Not only parts but whole engines can be 3D-printed. A titanium internal combustion engine was demonstrated by students at the University of Canterbury in New Zealand at the Shell Eco-marathon in 2020.
Medical
The World Health Organization has estimated that 30 million people worldwide need prosthetic and orthotic devices. This growing demand can be more easily met if the manufacturing process can be streamlined by 3D printing. Titanium, one of the few metals that does not harm the human body, plays a crucial role in this. Until recently, the task of ensuring that an implant perfectly fitted the patient’s body was difficult and time-consuming. However, with 3D-printing from titanium powder, it is now possible to tailor-make a device directly from a patient’s anatomical data.
One drawback is that the vanadium used in the popular Ti-6Al-4V alloy can cause allergic reactions. Therefore, new Ti alloys are being developed using manganese.
Other industries
Whether accompanied by 3D printing or not, titanium is gaining ground in other industries. Following is a selection of recent, innovative applications.
Mining
A new application is a titanium-clad mining autoclave produced by Coek Engineering for gold ore extraction by Polymetal in Russia. Ti grade 17 was selected for its superior chemical resistance and ability to operate at extreme temperature and pressure.

Tooling When Sandvik Coromorant wanted to add a lightweight mill to their CoroMill® 390 family, they turned to Sandvik Additive Manufacturing to develop an optimized and 3D-printed version of the milling device from titanium powder, thereby lowering the weight by 80%, reducing vibration and boosting productivity by up to 200%.
Refrigeration A 3D-printed NiTi alloy has been proposed by researchers at the University of Maryland as a cooling material used in refrigeration. Shape-memory alloys have an elastocaloric cooling effect, i.e. can undergo stress-induced reversible phase transformations during which latent heat is released or absorbed.
Oil and gas Emerson has produced a titanium-housed transducer for its gas ultrasonic flow meters, the Daniel™ T-200. 3D printing was used to enhance the acoustical performance of the flow meters. The titanium housing provides a barrier from corrosive hydrocarbon fluids and wet gas.
Marine
The sea’s highly corrosive saline environment makes titanium an attractive choice for the marine scrubbers that control pollution on tankers, cargo ships, and other sea vessels. Compared with stainless steel and the nickel alloys currently in use, titanium offers superior resistance
to sulphurous exhaust gases, higher temperatures and saline corrosion and can therefore last longer.
Expanite, specialists in surface hardening of stainless steel and titanium, have developed an autonomous underwater winch that will provide physical and biogeochemical data from the surface of the Arctic Ocean. The winch’s surface hardening will allow the stressed titanium components to withstand wear and thus extend long-term use of the winch system.

Electric bucycles Titanium has long been used to make sports bikes lighter and more ableto withstand wear and tear. Sandvik supplied GSD Global, an engineering and design company focusing on electric bikes, with motor nodes to attach the electric motor to the bike frame. These are costly to machine, so the device was 3D-printed in Sandvik Osprey® Ti-6Al-4V, which reduced the total costs by 75% while simultaneously boosting durability.
Conclusion
Despite the current pandemic, the fundamentals driving the demand
for titanium have not changed: the relative ease of manufacturing in 3D printing, life-cycle considerations, low maintenance, less waste and fuel efficiency. Confidence is high, as can be seen not only by Sandvik’s new titanium powder mill but also by other investments: a new Ti ingot plant in Panzhihua, China; a Ti alloy joint venture between TVEL Fuel (Rosatom) and Hermith (Germany); and two new furnaces commissioned by Perryman. Despite short-term disruptions, titanium as an industrial metal continues to gleam.
Every week we share a new Featured Story with our Stainless Steel community. Join us and let’s share your Featured Story on Stainless Steel World online and in print.
Featured Story by: James Chater
All images were taken before the COVID-19 pandemic, or in compliance with social distancing.