The largest stainless steel drinking water storage facility in Europe was constructed largely of 316L stainless steel, lean duplex and super duplex. With a total volume of 12,000 m³ (3 x 4,000 m³), the massive facility was built for Stadtwerke Ulm (SWU) in Kuhberg, Germany, and started operation at the end of 2023.
By Joanne McIntyre, Stainless Steel World
In Ulm, Germany, a substantial water infrastructure project has been completed. A large drinking water storage facility, built for Stadtwerke Ulm (SWU), began operations in late 2023. The facility has a total volume of 12,000 m³, divided among three 4,000 m³ tanks, and utilises stainless steel for large-scale water storage.
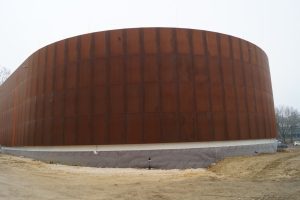
The facility’s design incorporates several engineering features.
Hydro-Elektrik GmbH, the company responsible for this project, optimised the steel supporting structure to reduce material usage while maintaining structural integrity. A notable element is the use of three stainless steel pillars centrally positioned in each tank to support the roof, which is an uncommon approach for stainless steel drinking water storage tanks.
The tanks themselves represent state-of-the-art metallurgy, employing three distinct grades of stainless steel to address specific requirements:
- The central columns, essential for supporting the building’s flat roof, are constructed from thick-walled DN 250 (D273x12.5) pipes using grade 1.4404 (316L) stainless steel.
- Tank bottoms and the lower 6.4 metres of the shell are fabricated from 1.4162 (Lean Duplex 2101 /S32101) steel. This duplex steel, recognised for its high strength and corrosion resistance, is used in 3mm thickness for the bottom plates and 4mm for the lower shell.
- The upper section of the shell and the roof are composed of Super Duplex 1.4462 (318LN / S31803) steel.
This strategic material selection addresses particular challenges, notably the presence of chlorine dioxide used to stabilise the incoming drinking water. Chlorine dioxide, which partially evaporates, can compromise less alloyed stainless steels in the upper reservoir space, necessitating more resistant grades in these areas.
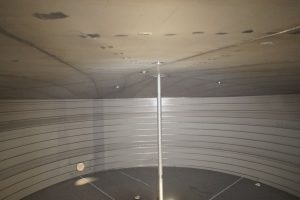
Each tank incorporates approximately 21 tonnes of duplex steel, 30 tonnes of super-duplex steel, and 0.3 tonnes of 316L steel for the pillars. The tank shells were manufactured using Hydro-Elektrik GmbH’s proprietary spiral winding process. This method continuously unwinds sheet metal from 10-tonne coils, forming it into a spiral shape to create the tank shell
The process offers several advantages: it creates seamless, large-diameter tanks with minimal welding, reducing potential weak points and improving structural integrity. It also allows precise control over shell thickness and diameter. The method is particularly suitable for large-scale tanks due to its efficiency, reducing production time compared to conventional plate-by-plate assembly. Additionally, the use of large coils minimises material waste, contributing to cost savings and environmental sustainability.
Automated cleaning system
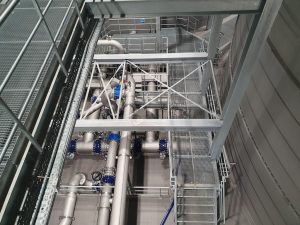
These stainless steel tanks include an automated cleaning system. The system, operated from an external platform, uses high-pressure nozzles to clean internal surfaces. This method reduces maintenance requirements compared to traditional concrete tanks, which may be advantageous for large-scale water storage applications.
Environmental considerations
A comparative life cycle analysis conducted for the Kuhberg project indicated that the stainless steel tank solution results in lower CO2 equivalent emissions compared to conventional alternatives. This analysis, performed within defined system boundaries and in accordance with DIN EN 15804, highlights the environmental benefits of stainless steel in large-scale water infrastructure.
Overcoming engineering challenges
The project encountered several engineering challenges, primarily in designing the tank overflow system. This system needed to manage an overflow volume of 2000 m³/h, requiring a specialised design based on finite element method (FEM) analysis. Rigorous theoretical verification was conducted before production began, ensuring the system’s capacity to meet these demanding specifications.
Water infrastructure evolution

The water storage industry has seen significant changes over the past five decades. Early innovations involved lining concrete tanks with stainless steel to improve durability and water quality. More recently, fully stainless steel tanks with integrated cleaning systems have been developed, addressing various water storage challenges.
Modern stainless steel tanks for water storage are typically fully welded, pickled, and passivated. This process eliminates the need for sealing materials, which can degrade over time and potentially affect water quality. Various grades of stainless steel are used in these applications, including 304, 316L, 316Ti, and duplex steels such as LDX 2101. Each grade offers different properties in terms of strength, corrosion resistance, and cost, allowing for tailored solutions to specific project requirements.
The development of these technologies reflects the industry’s ongoing efforts to improve water storage efficiency, maintain water quality, and reduce long-term maintenance needs. As water management becomes increasingly critical globally, such innovations in materials and design play a crucial role in developing sustainable water infrastructure.


Stainless steel in water infrastructure
The success of the Kuhberg project underscores the numerous advantages of stainless steel in water storage applications:
- Stainless steel’s inherent resistance to chemical corrosion ensures longevity, reducing maintenance needs and lifecycle costs.
- As an inert material, stainless steel helps maintain the purity of stored water, a critical factor in drinking water applications.
- The smooth surface of stainless steel, combined with the integrated cleaning system, ensures high hygienic standards can be easily maintained.
- The recyclability of stainless steel and its lower environmental impact over the structure’s lifecycle contribute to more sustainable water infrastructure.
- The ability to use different grades of stainless steel in various parts of the tank allows for optimisation of material properties and cost.
Conclusion
The Kuhberg drinking water storage facility represents a significant advancement in water infrastructure design and construction. By leveraging the properties of stainless steel and innovative engineering approaches, Hydro-Elektrik GmbH has created a solution that not only meets the immediate needs of water storage but also establishes new standards for efficiency, sustainability, and longevity in the industry.
As water management becomes an increasingly critical global issue, projects like this demonstrate the potential for stainless steel to play a crucial role in developing resilient, efficient, and sustainable water infrastructure. The success of this project may serve as a model for future large-scale water storage initiatives worldwide, emphasising the importance of material selection and innovative design in addressing the water challenges of the 21st century.
About the Company
Hydro-Elektrik GmbH, founded in 1977, is a German company specialising in water treatment and storage solutions. Based in Ravensburg, Baden-Württemberg, the company has established itself as a leader in innovative water infrastructure technologies. With a focus on stainless steel applications in water storage and treatment, Hydro-Elektrik GmbH has developed a range of proprietary technologies and products, including their HydroSystemTanks®.
About this Featured Story
Appearing in the October 2024 issue of Stainless Steel World Magazine, this Featured Story is just one of many insightful articles we publish. Subscribe today to receive 10 issues a year, available monthly in print and digital formats. – SUBSCRIPTIONS TO OUR DIGITAL VERSION ARE NOW FREE.
Every week we share a new Featured Story with our Stainless Steel community. Join us and let’s share your Featured Story on Stainless Steel World online and in print.