FPSOs require high-pressure Quick Opening Closures (QOC) to maintain operational safety and reliability. In addition to providing safe access to pipelines and pigging facilities, QOC are integral to produced water treatment systems, production separators, and fuel gas filter separators.
By Joanne McIntyre, Stainless Steel World
The offshore production of hydrocarbons is moving into deeper and more remote locations. FPSOs have revolutionised deepwater drilling, allowing operations to produce oil in areas that were not previously viable. The economy and ease of deploying small-scale FPSO vessels to exploit smaller reservoirs, which would have traditionally necessitated the construction of an offshore platform, is being made even more attractive through Government incentives. However, design requirements are becoming more arduous.
What are QOC?
Quick Opening Closures (QOC) are highly engineered doors with a quick-action mechanism, used to quickly access pipelines or pressure vessels. Typical applications are end closures for pig launchers & receivers (scrapper trap doors), pressure vessel end closures (filter vessel quick open closures) and blow-down lines end closures. QOC are designed, engineered and manufactured according to the most stringent international standards applicable to Pressure Vessels for Oil, Gas and Petrochemical industry, such as ASME VIII div. 1 & 2, ISO EN 13445.
Operators must think ahead
Early consideration of design requirements for deep water, high pressure applications such as FPSOs is essential to ensure efficient supply chain operations, as is timely integration and installation of the QOC into pressure vessel design packages. This means FPSO operators must think ahead, as Carla Connolly, Global Sales Director for GD Engineering, explains.
“Traditional oil and gas mid-pressure applications have benefited from closures using standard materials and shorter lead times. Arduous applications such as deepwater FPSOs require more complex material specifications and specialised closure designs made to specification. Manufacture involves forging materials such as duplex stainless steel or using corrosion resistant weld overlay processes, with extensive testing requirements necessary to ensure reliability throughout the full product life cycle. Early engagement with specialist companies like ours is therefore essential to ensure that Quick Opening Closures for FPSOs are correctly specified, installed and maintained.”
Super duplex selected
GD Engineering has many years of experience in the design and development of Quick Opening Closures based on its Bandlock™2 design. The company has recently supplied QOC on 12” Guard Cartridge filters for an FPSO in South American waters. The filtration/closure combination is for a sulphate recovery system, with the filter designed to remove debris down to 10 microns. The closure allows safe and efficient access to the filter vessel within 60 seconds, using only one operator and without the need for any special tools. Both the closure and the vessels were supplied in super duplex stainless steel with complete documentation and QA packages to meet operator and regulatory requirements.
Bandlock™2 Quick Opening Closures from GD Engineering also feature on an FPSO located in the world’s largest global deepwater oil field. The operation includes FPSO interconnection to 13 wells, with the vessel and field projected to produce above two million barrels of oil per day. GD Engineering supplied 25 specially designed Quick Opening Closures for the project’s pig launcher and receivers, including a specially designed 10k rated closure which withstands in excess of 600 bar pressure, yet operates at the same speed, efficiency and safety levels as their standard designs.
To further ensure the safety of operators, the Bandlock™2 closures were supplied with mechanical key interlocks which are integrated into the valve operation sequence. This minimises safety risks and reduces human error using the key transfer principle to guarantee that operators follow the correct steps through the valve operations to the final opening of the pressure vessel access point once the system has been completely depressurised.
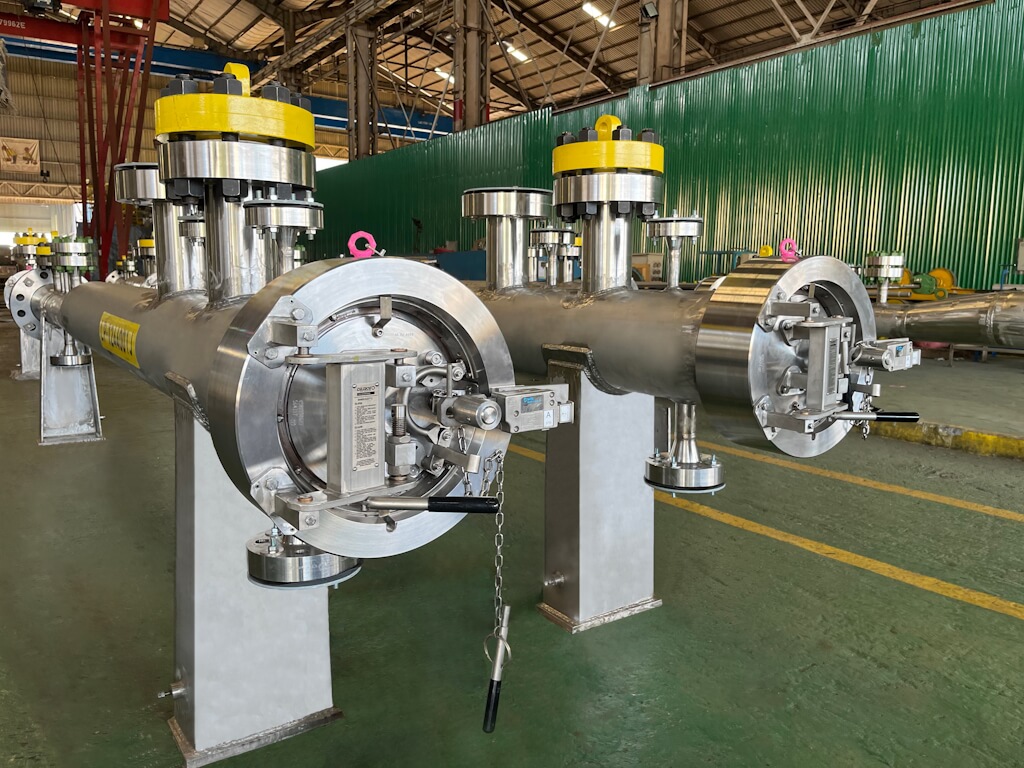
Challenging environment

The stringent conditions under which FPSOs are operated demand close attention from operators. QOC are critical equipment, and as such, poor maintenance and servicing by end users can lead to issues for the operator. “We focus on building good relationships with our customers and end users with training for the QOC installed base to make sure our customers are getting the most out of their QOC’s and assets,” explains Ms Connolly.
In the offshore environment, weight is an important factor, and the weight of closures can be high, depending on the design, continues Ms Cononolly. “At the design stage, both weight and size can be reduced by carefully selecting materials and design codes. Our experience in this area allows us to offer benefits to customers. When compared to BandlockTM2 QOCs, other closure designs can be very large and heavy in an effort to meet the design parameters, especially when dealing with the high pressures you see in the FPSO market.”
The superior corrosion resistance and strength of duplex stainless steel compared to alternative materials mean less material is required to achieve the same level of strength and safety, offering significant weight and space savings.
Fail-safe design
In addition to minimising weight and space, reliability and safety are key factors for QOC, and the BandlockTM2 QOC has a raft of safety measures. The internal locking band mechanism, which gives the range its name, is a duplex stainless steel conical thrust ring fitted between the door and hub, transmitting the pressure load uniformly around the full 360° circumference of the hub. This means that if the QOC is to be over-pressurised, the locking band will hold the QOC door closed, and all locking elements will remain in place. This is an advantage over other types of closures (bayonet, clamp (yoke), threaded, T-bolt) when the locking elements are in shear and are not in 360-degree contact, which can lead to failure if the closure is over-pressurised. The design also allows for 60 seconds or less single operator access to vessel/pipeline or application.
In addition, the closure cannot be operated when there is any pressure remaining in the system as all locking elements of the QOC are in compression, meaning that any pressure applied to the QOC would not allow for the closure to be operated and opened. The self-energising lip seal also has an integral anti-extrusion spring as a further safety feature.
About the company
GD Engineering is owned by Celeros Flow Technology, a company with a long history of serving worldwide businesses. The market sectors on which the company concentrates are oil & gas, power, chemical processing, water treatment and marine. Its brands aid in the correct specification, design and manufacture of mission-critical equipment, while its aftersales services ensure that assets are properly maintained and perform effectively throughout their operating life.
About this Featured Story
Appearing in the June 2024 issue of Stainless Steel World Magazine, this Featured Story is just one of many insightful articles we publish. Subscribe today to receive 10 issues a year, available monthly in print and digital formats. – SUBSCRIPTIONS TO OUR DIGITAL VERSION ARE NOW FREE.
Every week we share a new Featured Story with our Stainless Steel community. Join us and let’s share your Featured Story on Stainless Steel World online and in print.