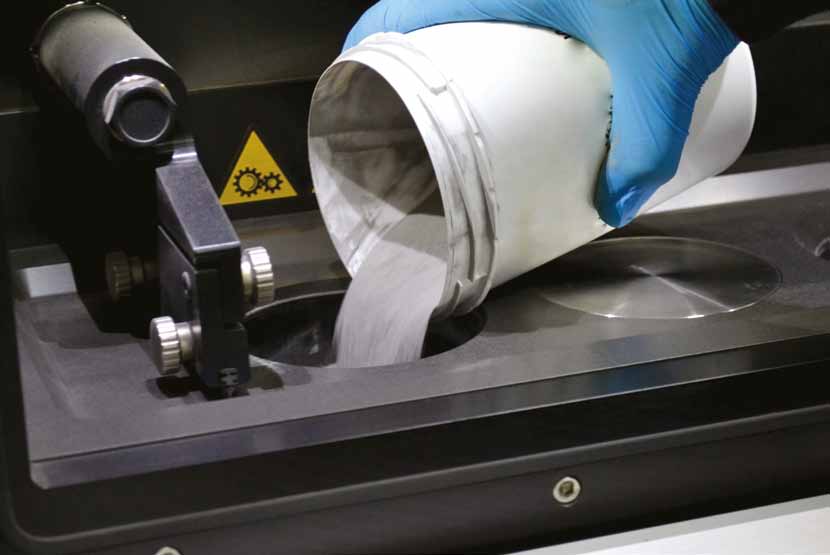
Stainless Steel World is proud to present a series of technical articles on additive manufacturing written by additive manufacturing expert Prof. Todd Palmer from Pennsylvania State University. In Part 3, he considers the additive manufacturing of duplex stainless steels.
By T.A. Palmer (a,b, a) Department of Materials Science and Engineering and (b) Department of Engineering Science and Mechanics, The Pennsylvania State University, USA
Duplex stainless steels are characterized by a balanced ferrite-austenite microstructure which gives them high strength and superior corrosion resistance. While not as popular as austenitic stainless steel, they are used across a range of applications in the petroleum, marine, and nuclear power generation industries. This combination of properties and high value-added applications makes them an attractive material for additive manufacturing. Lower levels of nickel in these alloy grades also make them a potential lower-cost alternative to austenitic stainless steels while maintaining equivalent or even superior corrosion properties. However, these alloys are particularly susceptible to the formation of deleterious secondary phases and disruption of the balanced ferrite and austenite levels when exposed to high temperatures, leading to a degradation of corrosion and mechanical properties. Controlling the microstructure during welding and additive manufacturing can be particularly challenging, especially when coupled with the additional compositional complexity introduced by powder feedstocks. Leveraging existing knowledge and exploring the role of composition, processing routes, and post-process heat treatments will be needed to expand their implementation through this unique processing route.
A unique class of stainless steels

Among the various classes of stainless steel in common usage, duplex stainless steels are rather unique. While ferritic, austenitic, and martensitic stainless steels contain a dominant single phase or microstructure, duplex stainless steels contain equal amounts of ferrite and austenite. This combination of two unique phases helps to impart both corrosion resistance and high strength not achievable in the other grades. Such a unique combination of properties makes them suitable for use in environments that are too harsh for austenitic or ferritic steels, making them an attractive option for highperformance applications in the energy generation and oil and natural gas exploration sectors. Their use, however, is somewhat limited to low-temperature applications given their susceptibility to disruptions in the balanced ferrite/austenite microstructure and precipitation of deleterious secondary phases at temperatures above 375°C. Duplex stainless steels cover a wide range of compositions and can be sub-divided into lean, standard, super, and hyper duplex grades. Even though all of the grades contain the same major alloying elements, such as Cr, Ni, Mo, and Mn, the individual levels vary. A summary of compositions for common alloys in each grade is shown in Table 1 [1,2]. As the levels of specific alloying elements increase, particularly in moving from the lean to the hyper duplex grades, so does the severity of the corrosive environment in which the alloys operate. Nitrogen is a critical alloying element addition and acts as an austenite stabilizer in duplex.
While it is also commonly present in austenitic grades, the nitrogen levels in duplex stainless steels are much higher, reaching levels of nearly 0.40 wt.% in hyper duplex stainless steels. There is also an overlap in the applications for austenitic and duplex stainless steels. Rising material costs, however, are bringing economic issues to the forefront, and leading to consideration of lower-cost materials, providing additional opportunities for duplex. Much of the material cost originates in the common alloying elements utilized in the different grades. Chromium contents for the duplex stainless steels are typically higher than that specified for the common austenitic grades, but the nickel levels are notably lower. This decrease in the nickel composition is countered, in part, by the higher allowable nitrogen levels, both of which promote the formation of austenite during processing. Even with the slightly elevated levels of molybdenum, the duplex grades are an attractive economical alternative to austenitic stainless steels, particularly with the current volatility in nickel prices, while maintaining similar performance and properties. One common example of the substitution of lean duplex stainless steels for austenitic stainless steels is spent pool fuel liners [3].
The selection of materials systems for use in additive manufacturing is based on several broad yet ill-defined criteria, primarily focused on the more efficient use of higher cost materials. Considering their combination of highperformance levels, applicability in high value-added applications, relatively lower costs, and wide availability in wire and powder forms, it would seem that duplex stainless steels should be ideal candidates for additive manufacturing. However, there is relatively little work reported on the additive manufacturing of these alloy systems, especially when compared with austenitic grades. Even though they do not suffer from solidification or solid-state cracking phenomena typically associated with poor weldability, there are issues with maintaining the ferrite/austenite phase balance under the conditions prevalent in fusion-based additive manufacturing processes.
Challenges in controlling balanced microstructures
This balanced ferrite/austenite microstructure is obtained in the wrought condition primarily through a series of highly controlled processing steps. Duplex stainless steels can also be produced through solid-state processing routes involving the use of powers, such as traditional press and sinter and hot isostatic pressing (HIP) processes. Through these routes, the ferrite/austenite phase balance can be controlled, and the formation of undesirable secondary phases, such as CrxN and sigma phase is avoided through thermo-mechanical and heat treatment processes. A microstructure containing alternating plates of ferrite and austenite is obtained using these processing routes, providing the attractive combination of corrosion resistance, high strength, and lowtemperature fracture toughness characteristic of this alloy system. Fusion-based additive manufacturing processes, on the other hand, undergo a series of rapid heating, melting, solidification, and cooling cycles driven by its unique layer-by-layer deposition methodology [4]. Since the duplex stainless steel compositions were originally designed for wrought processing routes, these complex thermal histories make it difficult to obtain the balanced ferrite/austenite microstructure and impact the resulting microstructure and properties. The closest corollary to the microstructures observed in additively manufactured duplex stainless steels are the fusion zone microstructures in autogenously welded duplex stainless steels [5]. These structures are mainly ferritic with low levels of austenite, consisting primarily as grain boundary and Widmanstätten austenite interspersed with low levels of intragranular austenite.

Mitigation strategies for increasing the austenite phase fractions in the weld metal can be divided into thermal and chemical strategies. Thermal strategies typically combine preheating to reduce the cooling rates and post-process heat treatments to produce more acceptable ferrite/austenite phase balances.
Chemical strategies primarily involve the addition of austenite stabilizing alloying elements through either the addition of nickel through the filler metal or the addition of nitrogen through the shielding gas. Different additive manufacturing processing routes also have noticeable impacts on the resulting microstructures. In powder bed fusion processes, the rapid cooling rates, in the order of 105-106 ºC/sec, produce almost complete ferrite microstructures with small amounts of grain boundary austenite6. Much of the austenite can be recovered through follow on heat treatments at temperatures in the order of 1000ºC for less than one hour. While these austenite levels can reach levels close to those present in the wrought conditions, the austenite tends to take on a different appearance, with small austenite grains existing in the ferritic matrix.
The directed energy deposition processing of duplex stainless steels is more applicable than the powder bed fusion route for large structures and the repair of existing components. Much of the current work has been directed at the use of gas metal arc (GMA) deposition processes typically referred to as wire arc additive manufacturing (WAAM) [7]. Since these processes use commercial weld filler metal wire with increased levels of nickel, the resulting austenite levels can reach or even exceed those in the wrought component. However, the austenite exists in different morphologies, with grain boundary, Widmanstätten, and intragranular forms being dominant. Laser-based directed energy deposition using powder feedstocks is also an emerging processing route for these alloys. Recent work has shown that austenite levels close to those observed in wrought materials are attained in the as-deposited condition for the lean, standard, and super grades [8].
Similar to the results obtained with the WAAM process, the austenite existed in the common grain boundary, Widmanstätten, and intragranular forms. In these materials, however, the intragranular austenite form was dominant, comprising between 55% and 76% of the austenite present. Even though the as-deposited microstructures contain rather attractive austenite levels, the additively manufactured duplex stainless steels are also typically HIP post-processed. The HIP postprocessed heat treatments are commonly used to heal processrelated defects and to convert the grain boundary, Widmanstätten, and intragranular austenite morphologies present in the as-deposited materials. After processing at temperatures around 1170°C, the austenite takes on an appearance more similar to that present in the wrought condition but without the same preferential orientations and with the finer austenite grains becoming much more evenly distributed.
Oxide inclusions

In addition to the higher levels of austenite, other microstructural features emerge resulting from the specific properties of the powders. For example, these powders contain oxygen levels nearly five times higher than that present in comparable wrought forms. Such high oxygen levels lead to the formation of a range of oxide inclusions which originate in the powders. These oxide inclusions exhibited complex structures with a combination of amorphous, metastable, and stable phases across these different conditions. In the powder particles, which experienced rapid cooling rates during the gas atomization process, amorphous inclusions that were rich in Mn, Cr, Si, and oxygen were observed and surrounded by small crystalline MnS particles. After additive manufacturing, these inclusions transformed to a combination of rhodonite (MnSiO3) and spinel (MnCr2O4) with amorphous regions around the exterior. They also served as nucleation sites for the intragranular austenite, providing a potential route for promoting the formation of higher austenite levels. Post-process hot isostatic pressing treatments, which replicate conditions most similar to equilibrium, resulted in the formation of a stable spinel oxide with MnS particles around the exterior [9].
Even with these different microstructural features, room temperature mechanical properties of additively manufactured duplex stainless steels are often similar to and even exceed those observed in the wrought condition. In the AM material, the finely dispersed ferrite and austenite phases produced a ductile failure mode and appear to be unaffected by the presence of the oxide inclusions. However, these testing conditions do not capture the performance of these alloys at high strain rates and low temperatures. At these low temperatures, impact energies have been recently shown to be significantly degraded, falling well short of the wrought material requirements in both the as-deposited and HIP conditions. This loss of properties is connected to the fine distribution of ferrite and austenite in the as-deposited and post-processed microstructures and the presence of the oxide inclusions, which drive the transition to brittle fracture mechanisms at these low temperatures.

The path forward

The additive manufacturing of duplex stainless steels is still in the early stages of development. A means to produce balanced ferrite/austenite microstructures and avoid the formation of undesirable secondary phases during additive manufacturing is needed to reach eventual largescale implementation,. There are three routes that can be explored to control these microstructures and involve the specification of appropriate compositions in the powders, control of the processing conditions, and the use of post-processing heat treatments, such as HIP post-processing. Of the three, the most easily implemented solution involves the development and use of these post-processing heat treatments.
The use of powder feedstock represents another challenge, particularly in terms of the presence of higher levels of oxygen in the powders. With these high levels of oxygen, oxide inclusions have been observed in additively manufactured stainless steels, including austenitic, duplex, and precipitation hardened grades. Their transformation from the powder feedstock through post-process heat-treating remains largely unexplored. Preliminary work has shown that they evolve from amorphous structures in the powder feedstock to different crystalline structures in the as-deposited and post-processed conditions, depending on the alloy composition. Even though they appear to promote the nucleation of intragranular austenite in the duplex stainless steel grades, their impact on the properties is still rather vague.
The room temperature quasi-static mechanical properties of standard and super duplex stainless steels fabricated using laser-based directed energy deposition met the minimum standard requirements. However, the performance of the additively manufactured materials is significantly degraded when exposed to extreme environments and more aggressive testing by the presence of lack-of-fusion defects, non-uniform microstructures, and oxygen-rich inclusions. Post-process hot isostatic pressing reduced the severity of these issues, but the presence of oxygen-based inclusions could not completely be eliminated. Tighter controls of oxygen contents and overall powder chemistry will be required, but the requirements will vary with different grades and will be difficult to implement.
References
1 ASTM_A276, Standard Specification for Stainless Steel Bars and Shapes, ASTM Int. 10 (2012) 1–7. doi:10.1520/A0276.
2 American Society of Testing Materials, ASTM A240 Standard Specification for Chromium and Chromium-Nickel Stainless Steel Plate, Sheet and Strip for Pressure Vessels and for General Applications, ASTM Int. I (2004) 12. doi:10.1520/A0240.
3 G. V. Rao, Confirmatory Corrosion Testing of S32101/LDX 2101® Duplex Stainless Steel Base and Weld Materials, 2010.
4 T. DebRoy, H.L. Wei, J.S. Zuback, T. Mukherjee, J.W. Elmer, J.O. Milewski, A.M. Beese, A. Wilson-Heid, A. De, W. Zhang, Additive manufacturing of metallic components – Process, structure and properties, Prog. Mater. Sci. 92 (2018) 112–224. doi:10.1016/j. pmatsci.2017.10.001.
5 V. Muthupandi, P. Bala Srinivasan, V. Shankar, S.K. Seshadri, S. Sundaresan, Effect of nickel and nitrogen addition on the microstructure and mechanical properties of power beam processed duplex stainless steel (UNS 31803) weld metals, Mater. Lett. 59 (2005) 2305–2309. doi:10.1016/j.matlet.2005.03.010.
6 K. Davidson, S. Singamneni, Selective Laser Melting of Duplex Stainless Steel Powders: An Investigation, Mater. Manuf. Process. 31 (2016) 1543–1555. doi:10.1080/10426914.2015.1090605.
7 M. Eriksson, M. Lervåg, C. Sørensen, A. Robertstad, B.M. Brønstad, B. Nyhus, R. Aune, X. Ren, O.M. Akselsen, Additive manufacture of superduplex stainless steel using WAAM, MATEC Web Conf. 188 (2018) 1–8. doi:10.1051/matecconf/201818803014.
8 A.D. Iams, J.S. Keist, T.A. Palmer, Formation of Austenite in Additively Manufactured and Post-Processed Duplex Stainless Steel Alloys, Metall. Mater. Trans. A Phys. Metall. Mater. Sci. 51 (2020). doi:10.1007/s11661- 019-05562-w.
9 A.D. Iams, J.S. Keist, L.A. Giannuzzi, T.A. Palmer, The Evolution of Oxygen- Based Inclusions in an Additively Manufactured Super-Duplex Stainless Steel, Metall. Mater. Trans. A. (2021). doi:10.1007/s11661-021-06311-8.