
Austenitic stainless steels are an ideal candidate material for fusion-based additive manufacturing processes including wire arc additive manufacturing (WAAM).
Stainless Steel World is proud to present a series of technical articles on additive manufacturing written by additive manufacturing expert Prof. Todd Palmer from Pennsylvania State University. In Part 2, he considers the additive manufacturing of austenitic stainless steels.
By T.A. Palmer (a,b, a) Department of Materials Science and Engineering and (b) Department of Engineering Science and Mechanics, The Pennsylvania State University, USA
Austenitic stainless steels are produced in higher tonnages and in a larger number of product forms than any other class of stainless steel. The combination of their widespread use and easy accessibility to powder and wire product forms make it a popular material across a range of additive manufacturing processes. The mechanical and corrosion properties of additively manufactured austenitic stainless steels are similar to and at times exceed those of cast, wrought, and powder products. However, they also exhibit wide variations in properties owing to the complexity of the additive manufacturing processes and the rather wide range of microstructures formed in fusion and solid-state processing routes. Microstructural evolution is further complicated by the use of powder feedstock forms, which introduce higher levels of oxygen and nitrogen than are typically encountered in wrought forms. Existing knowledge of welding and powder processing will be invaluable in understanding these structure and property differences and in the eventual prediction of the performance of additively manufactured austenitic stainless steel components.
Popularity of austenitic stainless steels

Additive manufacturing may be touted as a revolutionary manufacturing technology, but it is still limited by a low number of available material systems, which were originally developed for wrought and cast processing routes [1]. Within the available stainless steel grades, austenitic stainless steels are a good place to start discussing the additive manufacturing of stainless steel, given their generally acceptable weldability and wide availability in suitable product forms. Austenitic stainless steels display a unique combination of corrosion resistance, mechanical strength, and low temperature properties that make them attractive for applications in the aerospace, food and beverage equipment, pharmaceutical, medical, automotive, and mining and chemical equipment industries [2]. With such widespread usage, it is not surprising that they are the most commonly used stainless steel grade and comprise approximately 70% of commercially produced stainless steels. From an academic and technical perspective, this widespread usage has made them probably the most studied of the various grades of stainless steel and as a result, a rather broad and extensive body of knowledge of their processing, structure, properties, and performance has been developed.
Austenitics ideal for fusion-based AM
Given their wide number of applications, there has been significant effort expended on the study of the welding of austenitic stainless steels, and the resulting fusion zone and heat-affected zone microstructures across the range of fusion and solid state welding processes.
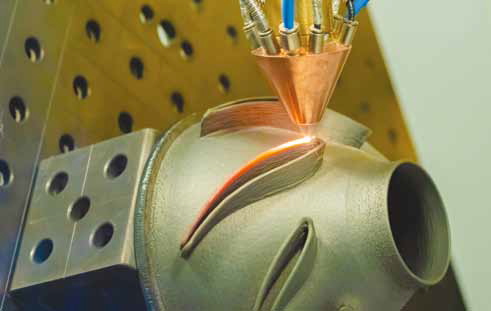
While considered to have generally good weldability, the alloys can also be susceptible to the formation of different processing-related defects that can form during solidification in the fusion zone or during repeated heating and cooling in the solid-state heat affected zone region [2]. The appearance of these defects can be governed by the composition of the alloy and the selection of the energy source. These energy sources, which can range from arcs to lasers to electron beams, alter the processing conditions and fusion zone geometries, thus producing a rather wide range of microstructures that can impact the properties and the prevalence of these process-related defects. It is fair to say that aside from plain carbon steels, austenitic stainless steels are probably the most studied materials in welding research, with more than 4,000 journal articles published on the general subject, according to the Web of Science.
Considering their widespread use, availability in both powder and wire forms, and the deep knowledge of their welding properties, austenitic stainless steels are an ideal candidate material for fusion-based additive manufacturing processes. Prominent additive manufacturing processes with austenitic stainless steels include laserbased powder bed fusion and directed energy deposition, and wire arc additive manufacturing (WAAM). They are also widely used in solid-state additive manufacturing processes, including binder jet printing and other filamentbased methods based on extrusion processes (i.e. Stratasys, Desktop Metal, MarkForged systems). However, these latter processes are not as prominent or widely applied as binder jet printing or fusion-based processes. One would be hard-pressed to identify a commercial system that did not offer an austenitic stainless steel as one of its available materials. This wide usage and availability in the industrial sector and across a range of additive manufacturing platforms has also translated into a significant interest in the academic and research communities, with nearly 3,000 articles published over the last decade on the additive manufacturing of stainless steels, according to the Web of Science. The vast majority of these articles have focused on the processing of austenitic stainless steels.
Even though there are a rather large number of austenitic stainless steel grades available, 316L austenitic stainless steel is by far the most widely used across the different additive manufacturing processes. Much of the focus on this specific grade can be traced to its widespread availability and ease of processing. The wide range of potential applications and how many of these critical applications require unique geometries which can only be produced through additive manufacturing processes has made this alloy the first choice of designers and manufacturing engineers. More importantly, though, the wide availability of spherical 316L stainless steel powder produced using gas atomization processes has driven much of this interest. Growing interest in the WAAM process, which primarily uses wire as the feedstock in a gas metal arc (GMA) welding process, is slightly expanding the use of different austenitic stainless steel grades. This expanded interest can be traced to the availability of different wire feedstock alloys, which are expanded by the wider range of wire compositions available as welding filler metal wire.
Challenges in fusion-based AM
Austenitic stainless steels have been commercially processed for decades and are generally considered something of a commodity product. However, from a materials standpoint, they are actually complex multi-component alloy systems that can undergo complex transformations during fusion-based additive manufacturing processes.
When considering their use in additive manufacturing, it is therefore important to consider the role that the processing route has on the evolution of the microstructure. These microstructures are much different from the well-defined equi-axed microstructures observed in wrought stainless steel sheet, plate, and other long product forms.
Highly controlled thermo-mechanical processing steps are required to obtain these uniform microstructures in wrought products. This level of control is not possible in fusion-based additive manufacturing processes, in which a powder or wire feedstock is deposited in a layer- by-layer manner. The resulting microstructures are characterized primarily by the segregation of alloying elements typically observed in rapidly solidified structures, but they also vary depending on the additive manufacturing process being utilized.
The scale of the microstructure and the presence of a cellular or columnar dendritic structure vary with different processing routes and determine the resulting corrosion and mechanical properties. These differences can be traced in simplistic terms to the magnitude of the heat input in powder bed fusion and directed energy deposition processes. For example, powder bed fusion processes are characterized by low heat inputs and rapid travel speeds (on the order of 1 m/sec) that produce fine solidification structures and are dominated by cellular solidification modes with sizes in the order of several microns. In directed energy deposition processes, higher heat inputs and lower travel speeds (10 mm/sec) are commonly encountered, resulting in coarser columnar dendritic structures [3].
The selection of a laser or an arc as the energy source in these directed energy deposition processes can also have a dramatic impact on the resulting microstructure and properties of the material, with the use of arcbasedprocesses leading to a further coarsening of the microstructure. Differences in processing conditions and microstructures lead to wide variations and uncertainty in the mechanical properties observed in similar austenitic stainless steel grades.

While these structures are complex and have unique features far different from those in more conventional wrought structures, they are similar to those obtained in welded structures. For example, the rapid and cyclic heating, melting, solidification, and cooling cycles characteristic of fusion-based additive manufacturing processes are encountered in fusion welding and have been characterized in a large body of existing literature. With this long-term experience in dealing with similar structures, the welding research community has provided us with several important tools that can be used to predict the resulting microstructures and determine the susceptibility of selected alloys to the formation of processrelated defects. In austenitic stainless steels, solidification cracking and other solid-state cracking phenomena are typically encountered and have been found to be dependent on composition and how the composition affects the first phases to form during solidification.
Role of oxygen & nitrogen
Since these tools are highly reliant on the composition, it is important to first note differences in the compositions of wrought materials and the feedstocks used in the additive manufacturing of austenitic stainless steels. It is typical to focus on the primary alloying elements (nickel, chromium, manganese, and molybdenum) that are traditionally associated with the properties that make austenitic stainless steels unique.
However, the use of powders as the feedstocks in fusion-based additive manufacturing processes introduces additional complexity to the process and is forcing the research community to consider the role of nitrogen and oxygen. Given that these alloying elements are not even consistently monitored in wrought systems, there is not a large knowledge base to predict performance. Because the powders are largely produced using gas atomization, and nitrogen can be used as both the atomizing gas and the cover gas in the electric arc furnace, nitrogen levels in the powders can be in the order of 0.10 wt.% or more, compared to 0.01 wt.% in wrought materials. Oxygen levels in the powders and parts built using these fusion-based AM processes (0.05 wt.% or more) are also typically an order of magnitude higher than those observed in wrought alloys.
High levels of nitrogen and oxygen can lead to changes in the prominent solidification modes in austenitic stainless steel. One of the prominent means for detailing the formation of ferrite or austenite formed during solidification involves the use of chromium (Creq) and nickel (Nieq) equivalent values. For each value, weighting factors are applied to the compositions of alloying elements, with ferrite stabilizing elements (Cr, Mo, Si, Nb) being included in the Creq value and the austenite stabilizing elements (Ni, C, N, Mn) included in the Nieq value. Definitions of both values have evolved as the amount of experimental data has grown, but there is no one uniform accepted definition for each value.
While these definitions have been used independently, they are intended as input data to Schaeffler diagrams, which are empirical tools for predicting the prominent solidification mode in the fusion zones of austenitic stainless steels.
The WRC 1992 diagram is the latest and most up-to-date of the various iterations of the Schaeffler diagram and widely used in the study of austenitic stainless steels [4]. These tools can provide insight into the structures formed during fusionbased additive manufacturing, but since they are largely empirical, their utility beyond the prediction of solidification structures can be rather limited.
High oxygen levels in both the powders and in the as-built materials produced using both powder bed fusion and directed energy deposition processes are leading to other unexpected issues.
While these high oxygen levels can be absorbed in a solid solution in selected alloy systems, they can also lead to the formation of second phase oxide inclusions [5]. The presence of oxide inclusions in the fusion zones of plain carbon steels is well established, and the filler metal compositions are tailored to promote their formation. In austenitic stainless steel powders, no similar alloy design effort has been undertaken. As a result, the structure and compositions of these phases can vary rather widely with small changes in the overall alloy composition. Preliminary work has shown that these oxide inclusions are actually amorphous in the powders and in the as-built condition and can evolve with post-process heat treatments into crystalline phases. When using wire feedstocks in WAAM based processes, it is expected that the oxygen levels will be decreased and the formation of these oxide inclusions less of an issue [6,7]. However, changes in the expected oxygen levels in these builds and their corresponding impact on the formation of oxide inclusions have been largely unexplored.
The presence of these oxide inclusions in additively manufactured materials is also being connected to changes in properties and failure mechanisms. For the most part, it is generally found that mechanical and corrosion properties of additively manufactured components are in line or even enhanced over those typically observed in their wrought counterparts. However, most of the testing is performed under both static loading and generally ambient conditions. As applications of austenitic stainless steels produced using additive manufacturing expand, the performance of the materials under more extreme conditions, whether at low or high temperatures or under fatigue or higher strain rates, will become more of a consideration. Initial work has indicated that these oxide inclusions are impacting performance under these more extreme conditions and will warrant further study as additively manufactured components are implemented in more challenging environments.
Path forward for AM of austenitic stainless steels
It should be expected that the use of additive manufacturing for fabricating austenitic stainless steel components will continue to grow and become an important tool for designers and manufacturing engineers. The application of the process will likely expand in the next few years as newly designed components tailored to additive manufacturing processes emerge and production of existing and legacy components, particularly in the near term, expands. However, the mechanisms driving the high levels of property uncertainty and differences in the microstructures produced by the common fusion-based processing routes are not well understood, particularly in cases where there are variations in alloying element compositions.
For the additive manufacturing of austenitic stainless steels to meet this rather ambitious promise, many of these materials issues will need to be addressed. One area within austenitic stainless steels involves the nearly complete focus on a single grade, 316L austenitic stainless steel, particularly in powder bed and powder-based directed energy deposition processes. There are other austenitic stainless steels that complement or exceed the properties observed in 316L and can be produced in either powder or wire feedstock forms. By growing the number of alloys available for processing in this manner, the application space for additive manufacturing will inevitably grow.
While this growth in the range of alloy grades is attractive, many of the issues with variations in composition and the presence of oxide inclusions will need to be further investigated. Much of the uncertainty that is inherent in the properties of AM fabricated materials can be traced to small changes in compositions, even within the allowable limits outlined in the current standards for wrought products. Since these alloys are complex multi-component systems, it will be impossible to capture the interactions between alloying elements and their role in microstructural evolution through experimental methods and post-build microscopy.
New computational tools based on integrated computational materials engineering (ICME) principles will need to be integrated with advanced characterization tools to capture the complex physical phenomena occurring in the additive manufacturing process. The use of these tools will also drive the development of new standards applicable to different additive manufacturing processes, as well as the development of specific alloy systems tailored to each additive manufacturing process.
References
[1] T.A. Palmer, Materials Challenges in the Additive Manufacturing of Metals, Weld. J. 99 (2020) 31–35.
[2] J.C. Lippold, D.J. Kotecki, Welding Metallurgy and Weldability of Stainless Steels, John Wiley & Sons, 2005.
[3] T. DebRoy, H.L. Wei, J.S. Zuback, T. Mukherjee, J.W. Elmer, J.O. Milewski, A.M. Beese, A. Wilson-Heid, A. De, W. Zhang, Additive manufacturing of metallic components – Process, structure and properties, Prog. Mater. Sci. 92 (2018) 112–224. doi:10.1016/j. pmatsci.2017.10.001.
[4] D.J. Kotecki, T.A. Siewert, WRC-1992 constitution diagram for stainless steel weld metals: a modification of the WRC-1988 diagram, Weld. J. 71.5 (1992) 171–178.
[5] A.D. Iams, J.S. Keist, L.A. Giannuzzi, T.A. Palmer, The Evolution of Oxygen-Based Inclusions in an Additively Manufactured Super-Duplex Stainless Steel, Metall. Mater. Trans. A. (2021). doi:10.1007/s11661-021-06311-8.
[6] J.W. Elmer, G. Gibbs, The effect of atmosphere on the composition of wire arc additive manufactured metal components, Sci. Technol. Weld. Join. 24 (2019) 367–374. doi:10.108 0/13621718.2019.1605473.
[7] J.W. Elmer, G. Gibbs, J.S. Carpenter, D.R. Coughlin, P. Hochanadel, J. Vaja, P. Gurung, A. Johnson, M.J. Dvornak, Wire-Based Additive Manufacturing of Stainless Steel Components, Weld. J. 99 (2020) 8s-24s. doi:10.29391/2020.99.002.