Biomass is an important, if controversial, source of energy, which first rose to prominence in ethanol facilities and has been growing ever since. The industry makes perfect sense as part of the circular economy and provides plentiful opportunities for stainless steel suppliers.
By James Chater
Outlook
Amid all the publicity surrounding wind and solar energy, it is easy to forget that bioenergy (the generation of energy from biomass) accounts for about 55% of all renewable energy, or roughly one-tenth of the world’s primary energy supply. The IEA foresees a rapid increase in the use of bioenergy to displace fossil fuels, and demand is rising by about 6% or 7% a year (1). This upward trend is supported by generous subsidies in the USA and many European countries.
Biomass
Biomass is organic matter used as feedstock in bioenergy facilities. The earliest form of industrial bioenergy was mostly ethanol, a corrosive alcohol used, among other things, as motor fuel. It is made from corn, yeast, sweet sorghum or sugar cane using a fermentation process. With the passing of time, more feedstocks and more products were developed. Forest and agricultural residues, crops, straw, waste, sewage, landfill gas and algae (see box) were used to create new products such as liquid biofuels (especially biodiesel) and biomethane (biogas). Biofuels are especially important in aviation, and biomass-fired power plants fuelled by organic matter such as waste, often in combination with natural gas or coal, have become increasingly popular. Many fossil-fuel power stations have been converted to biomass. Most biomass power plants feature cogeneration (combined heat and power, or CHP) for district heating, making them more efficient. A case in point is the Fortum Värtaverket KVV8 CHP plant in Stockholm, which has been operating since 2016 using advanced technology supplied by Andritz (boilers, automation etc.) and actuators from Auma. It runs on forest residues but can switch to coal, and supplies heat to 190,000 households.
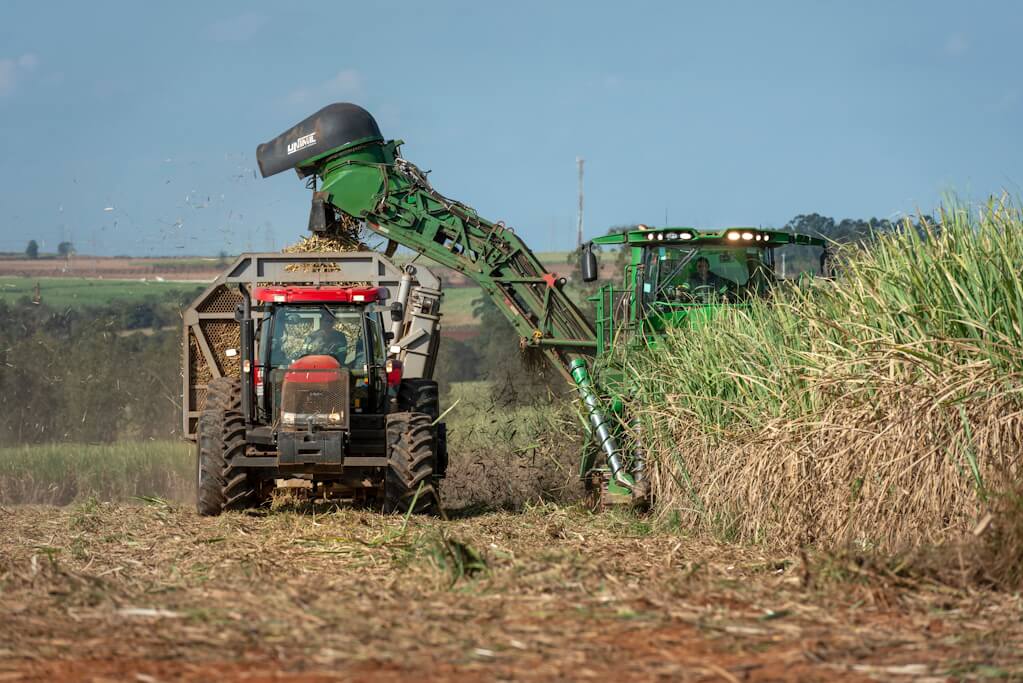

Liquid biofuels
Liquid biofuels include ethanol and biodiesel. Ethanol is used as an engine fuel and as a fuel additive such as E10. The largest producers by far are the United States and Brazil.
Biodiesel is produced from organic matter through a chemical process known as transesterification. It replaces diesel in ships, trains and automobiles. Aviation biofuel (bio-jet fuel; sustainable aviation fuel – SAF) is used to fuel aircraft, either partially (blended with conventional fuel) or 100%. It is made from biomass using pyrolysis processed with a Fischer-Tropsch process; using alcohol from waste fermentation; or from synthetic biology through a solar reactor.
Biogas
Biogas is made by putting organic waste inside a closed container and allowing it to undergo anaerobic digestion, a process in which microbes break down organic matter to produce CO2 and methane; the latter can be used further to produce electricity, power vehicles (trains, buses, automobiles) or heat homes, or liquefied to produce bio-LNG. The residue from this process can be converted into biofertiliser. Europe is the largest producer, especially Germany, with two-thirds of Europe’s capacity. China and the USA are large producers, and the remaining production comes from the rest of Asia, notably Thailand and India.
Are algae a viable fuel source?
In the past decade, algae have been viewed as a promising biomass from which to produce energy. However, investment has greatly diminished because of the perceived drawbacks and costs. Although algae grow fast and can easily be turned into oil, they require vast quantities of water, and there are high costs and difficulties of oil extraction. Among companies that have closed their algae operations are Algenol, while Shell and Chevron discontinued their R&D programmes. However, Totalenergies and Veolia are building a demo biofuel facility near Marseille, France, which will harness algae to produce oil by 2025. Reliance Industries is working to convert sunshine, CO2 and seawater into bio-oil.
Other organisations are taking up the challenge, using new technology to improve productivity. The USA’s National Renewable Energy Laboratory uses medium temperature and low pH to more extract lipids from the algae to further process them into biodiesel. Indian Institute of Technology, Delhi has designed different models of biofilm reactors to cultivate microalgae.
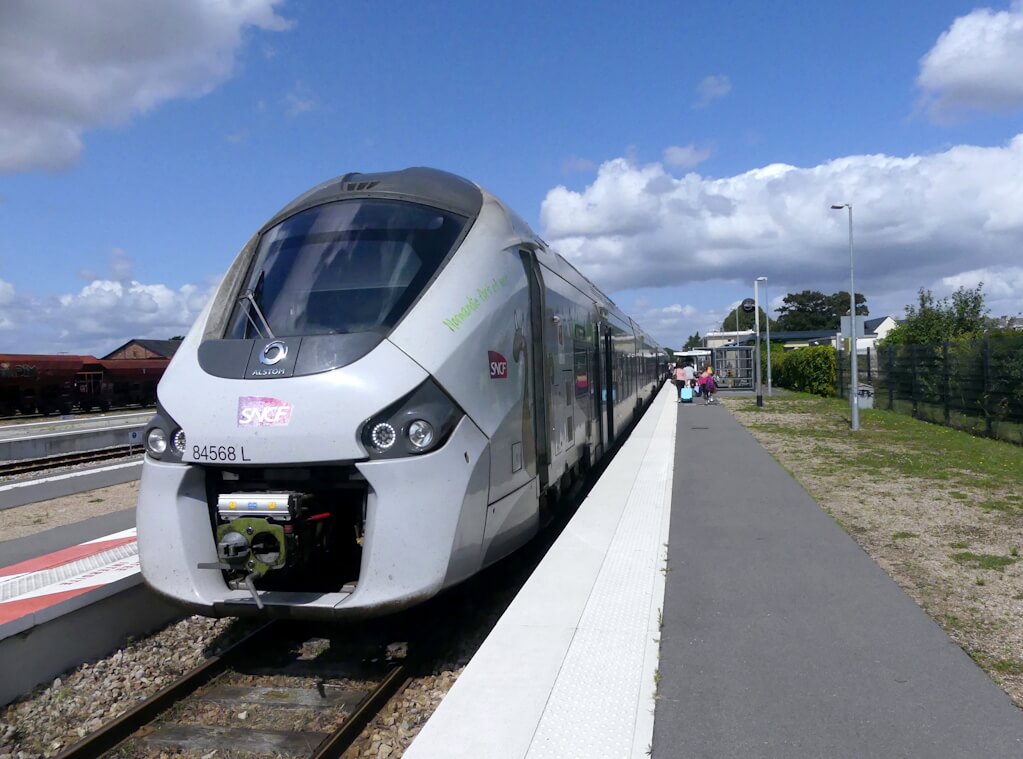
Projects
Several recent and ongoing projects demonstrate the versatility of modern biorefineries (biomass treatment plants). In 2021 Eni began production in a refinery in Gela, Sicily, Italy.
The plant recycles cooking oil and fats from fish and meat processing to produce biodiesel, bio-naphtha, bioLPG and bio-jet fuel. The company is planning to convert an industrial site near Livorno on Italy’s west coast into a biorefinery. It will consist of a biogenic feedstock pre-treatment unit, a 500,000 tonne/year Ecofining™ plant, and a plant to produce hydrogen from methane gas. Eni is also studying a possible biorefinery in Malaysia along with Japan’s Euglena and Malaysia’s Petroliam Nasional Berhad.
In 2022 Fintoil completed its biorefinery at the port of Hamina-Kotka in south-eastern Finland. The plant makes renewable fuels using fractional distillation, in which heat energy and negative pressure are used to distil the raw material to its constituents, separating the wanted fractions. Its main product is crude tall oil, which comes from the Finnish evergreen and is a by-product of the kraft pulping process.
One of the leading biogas technology suppliers is Weltec Biopower. It has built four biogas plants in Japan, the latest being a biogas-cum-cogeneration power plant located in Saitama Prefecture, which went into operation in February 2022. Weltec assisted McCulla Transport in expanding its plant in Lisburn, UK, and supplied stainless-steel technologies to a plant in Taiwan. Another leading supplier is Wärtsilä, which formed its Wärtsilä Biogas Solutions division in 2019. It is supplying the world’s second-largest plant (in Burghaun near Fulda, Germany), capable of liquefying bio-methane and synthetic methane as LNG for use as transportation fuel. Recently it supplied Transwaste (Hull, UK) with technology for a plant that will turn municipal waste into gas. In 2023 the Baltics’ first biogas plant fired with household and commercial biowaste will go into operation. Built by BioWOIMA Finland Oy in Tallinn, it will produce biomethane for the natural gas network and fuel for CNG-powered vehicles.
Pros and cons
Bioenergy is a somewhat controversial industry. Is it worth supporting, given recent advances in wind, solar, storage and green hydrogen? Using wood as a biomass can lead to deforestation, meaning less absorption of CO2. The land taken up by growing biomass is competitive with food production. The potential for abuse is considerable: subsidies granted for forest residues have been used to cut down whole trees (2). Traditional burning of biomass to produce heat, as practiced in poor countries, is polluting and harmful to health.
But modern bioenergy production, with proper safeguards and using advanced technology such as carbon capture and scrubbing to reduce emissions, has its place in the circular economy. It is only logical to recycle landfill gas, to prevent it seeping into the atmosphere, or to recycle residues and waste to create biofuels.

Materials
The various processes used in biomass treatment use the whole gamut of stainless steels and nickel alloys. Most corrosive conditions in the fabrication of biofuels process are covered by 304(L) and 316(L). Lean duplex grades (2101, 2003, 2304) have also been applied in biomass treatment plants. One US facility used 2101 on all its storage and fermentation tanks, instead of the traditional 304L.
For severe corrosion, stronger grades are required, and the high-temperature applications in the ethanol process require special stainless grades of Ni alloys. The pre-treatment phase in ethanol processing is especially corrosive, requiring duplex (2205), superduplex (2507) and superaustenitic grades, Ni alloy C-276 and alloys 317(L). Likewise, biodiesel plants require duplex and superduplex grades for pretreatment systems and other stages. Recently Ampo Service supplied 15 pressure seal design gate valves in Inconel 625 and WC6 to La Rabida Energy Park in Andalusia, Spain, where CEPSA produces biodiesel from used cooking oils.
The anaerobic digestion process in biogas production is also corrosive. Here 304(L) and 316(L) will serve in most applications, but 904L is used where hydrogen sulphide is present, and SSC-6MO where there are high chloride levels. In 2021 Sandvik Materials Technology (now Alleima) received an order to supply its Sanicro® 28 grade for a US biodiesel refinery. This is the first time this austenitic, originally developed for the fertiliser industry and also used in the upstream oil and gas industry, has been applied in a biodiesel plant. Here it was applied in the reactor effluent air coolers (REAC) of the hydro-processing unit. A year later, it was Alleima’s Sanicro® 35 grade that was ordered for a biogas facility in Texas that processes landfill into natural gas. Sanicro® 35 will be used to replace failed heat exchanger tubes made from 316L in a renewable natural gas plant in Texas.
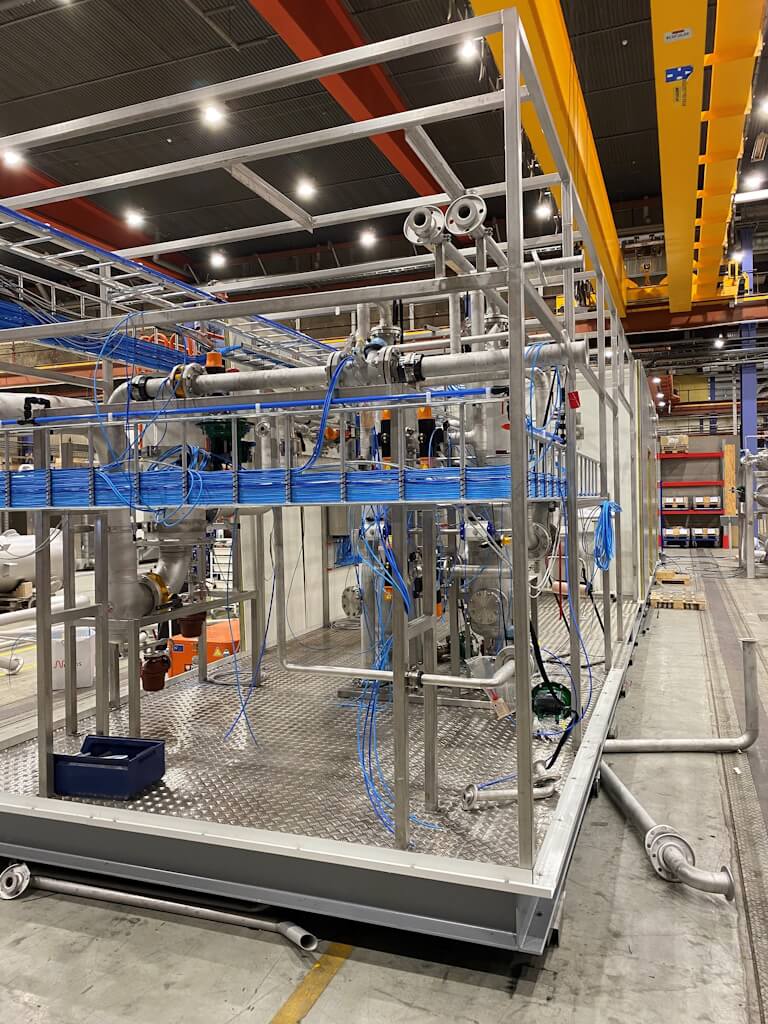
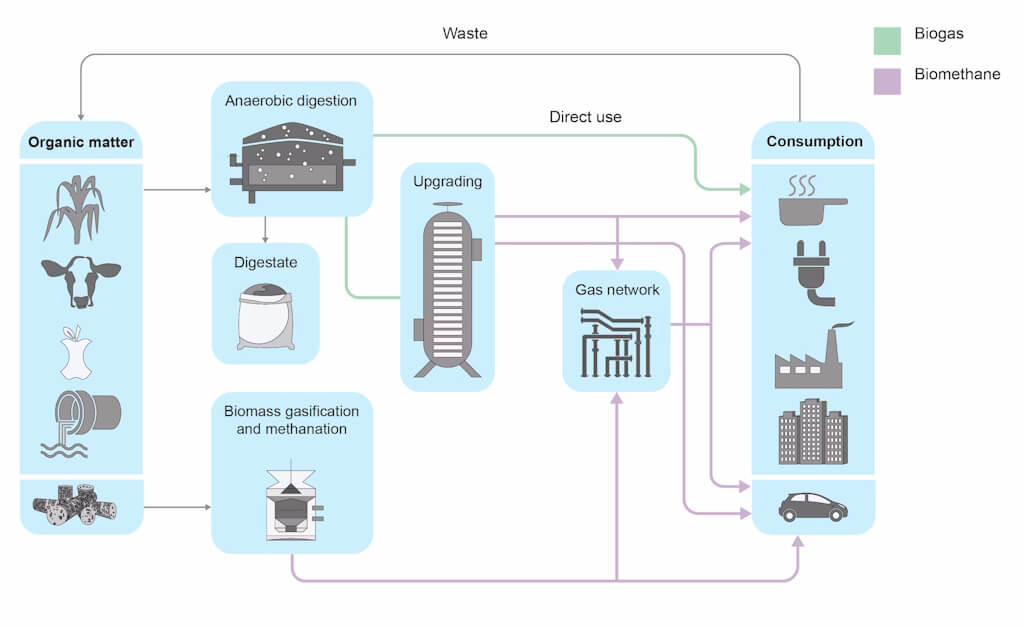
About this Featured Story
This Featured Story appeared in Stainless Steel World September 2023 magazine. To read many more articles like these on an (almost) monthly basis, subscribe to our magazine (available in print and digital format) – SUBSCRIPTIONS TO OUR DIGITAL VERSION ARE NOW FREE.
Every week we share a new Featured Story with our Stainless Steel community. Join us and let’s share your Featured Story on Stainless Steel World online and in print.