A KHS Innofill glass bottle filling machine. Photo ©KHS Group
According to a report by Vantage Market Research, the global beverage packaging market was valued at USD 145.91 billion in 2021, projected to grow to USD 193.22 billion by 20281. Success in this lucrative and fast-evolving industry requires companies to anticipate trends and maintain efficiencies. Stainless steels play a key role.
Text Joanne McIntyre, Stainless Steel World
Food and beverage packaging companies face a multitude of challenges. Suppliers may discontinue delivery of components, environmental standards require adaptation, while digital processes need system updates. Adaptation is essential to maintain efficient, sustainable and stable production. To meet these challenges, KHS Group, an international manufacturer of filling and packaging technologies focusing on the beverage and liquid food sectors, offers support to customers including predictive discontinuation management and technical upgrades.
The system supplier also provides advice on the fulfilment of legal environmental requirements and the implementation of ambitious sustainability goals. Stainless steels play an important role in the industry in fulfilling hygiene, sustainability and longevity requirements.
Demanding environment for stainless steels
Alexander Hoffeins, from KHS GmbH’s Standardisation Central Division Technology Management, explains the importance of materials in food and beverage packing equipment. “Various requirements are made of the stainless steels and other materials used in KHS equipment, depending on the type of machine,” he begins.
“The greatest demands on the stainless-steel alloys are made by machines and system parts that come into direct contact with beverages and food. These are the machines responsible for preparing and filling the product.” “Corrosion resistance must be ensured in relation to the product to be filled (mineral water, beer, fruit juice, etc.) but also with regard to the ambient conditions present, such as oxygen and the cleaning media used.”
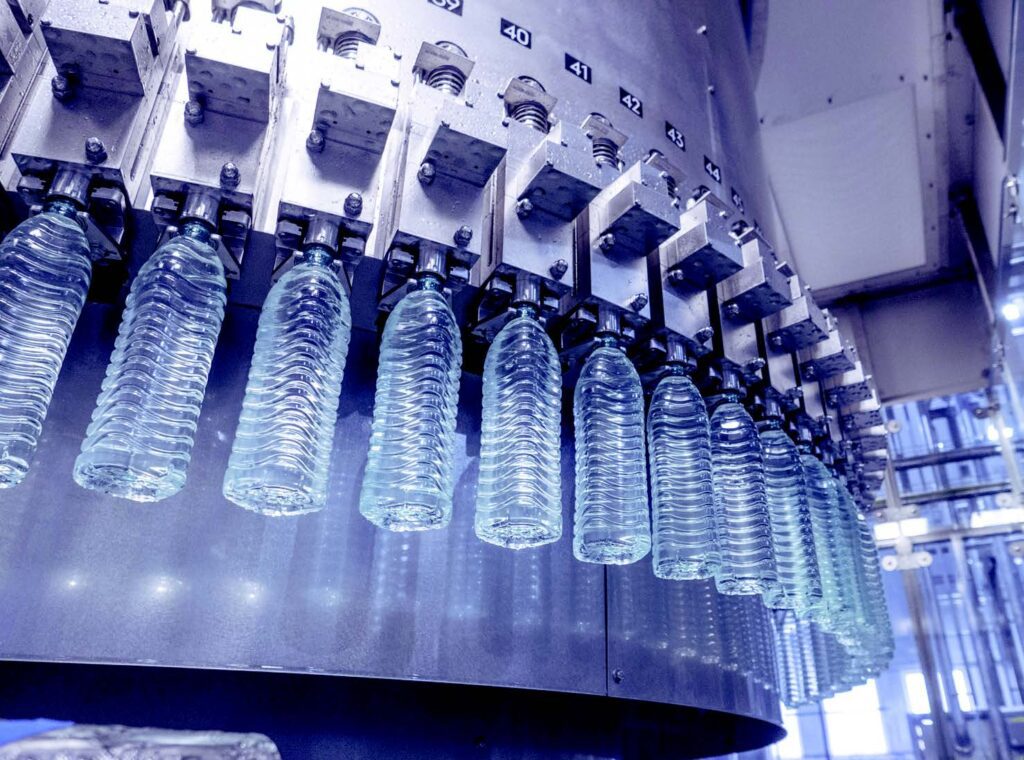
Alexander explains that beverages that come into contact with the materials (permanent contact) include:
- Beer (0–70°C)
- Carbonated soft drinks (0–30°C)
- Mineral water (0–30°C)
- Water with ozone 4 ppm (0–35°C)
- Wine (0–70°C)
- Sparkling wine (0–30°C)
- Fruit juice (5–95°C)
- Vegetable juice (95°C)
- Spirits (5–30°C/20–60% ABV)
- Milk/cocoa(0–30°C)
Cleaning agents that come into contact with the materials include:
- Alkaline cleaning based on NaOH (max. concentration of 2%)
- Combined cleaning and disinfection based on NaOH and Na hypochlorite (NaOCl; max. 3%)
- Cleaning boosters (additives) based on peroxide (H2O2) or peracetic acid (max. 0.3–0.5%)
- Acidic cleaners based on HNO3 (nitric acid; max. 1%)
- Acidic cleaners based on H3PO4 or in combination with HNO3 (phosphoric and nitric acid; max. 2%)
- Disinfection based on Na hypochlorite (NaOCI)
- Disinfection based on peracetic acid (PAA; 300–500 ppm)
- Disinfection based on chlorine oxide (ClO2; max. 10 ppm)
- Hot water (86–115°C)
- Steam (130°C)
- Ozone (max. 10 ppm)
The assumed daily contact time varies from 15 to 45 minutes depending on the medium.
Hygiene requirements
The material of construction for equipment which comes into direct contact with products in the food and beverage industry must meet strict hygiene and safety standards. These include:
- The materials used must not give off or release any substances or particles that could contaminate the product to be filled;
- The surfaces of the components exposed to product must be thoroughly cleanable;
- Attack from germs and bacteria must be completely prevented; and
- For the countries in the European Community, EC Regulation no.
1935/2004 defines which types of steel can be used when handling food.
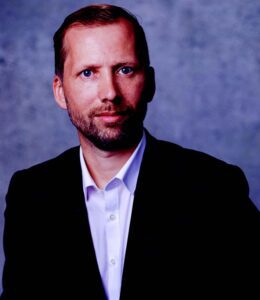
Alexander explains that stainless steel is the ideal material to meet these requirements. “Grade 1.4404/316L stainless steel is primarily used on filling lines and machines at KHS. With its addition of 2–2.5% molybdenum, this material has a much better resistance to corrosion than 1.4301/1.4307/AISI304L stainless steel, for example, that has now been fully substituted.
The surface finish and polishability of 1.4404 are also perfect. This is important, as surfaces exposed to the product must be free of defects such as grooves, folds and cracks. Larger product contact areas must have a roughness of Ra = 0.8 µm or better.”
As KHS has its own pipe bending center, the pipes used must be bendable. “This is ensured in the standard by the specified form of execution: welded/annealed according to DIN EN 10357 BC quality from cold-rolled stainless steel, smoothed seam, heat treated; inner surface: Ra < 0.8 µm; interior welding seam: Ra < 1.6 µm.”
Stainless for greater sustainability
Stainless steel also helps food and beverage clients to achieve their sustainability goals. Not only is it 100% recyclable, and manufactured using a high degree of recycled material, it also guarantees a long service life. Some of KHS’s clients are still using machines that have been in service for 40 years and continue to be supported by KHS Service. Worldwide, its machines are considered to have particularly long life cycles. Through regular conversions and the integration of up-to-date solutions, users are able to increase the efficiency and sustainability over the entire life cycle.
References
About KHS Group
The KHS Group is a leading manufacturer of filling and packaging systems for the beverage and liquid food sectors. In addition to the parent company (KHS GmbH), the company group has production sites in Ahmedabad (India) and Waukesha (USA), Zinacantepec (Mexico), São Paulo (Brazil) and Kunshan (China).
KHS manufactures modern filling and packaging systems for the high-capacity range at its headquarters in Dortmund, Germany, and at its plants in Bad Kreuznach, Kleve, Worms and Hamburg. The KHS Group is a wholly owned subsidiary of the SDAX-listed Salzgitter AG corporation. In 2022 the KHS Group and its 5.002 employees achieved a turnover of around EUR 1.291 billion.
About this Featured Story
This Featured Story appeared in Stainless Steel World May 2023 magazine. To read many more articles like these on an (almost) monthly basis, subscribe to our magazine (available in print and digital format – SUBSCRIPTIONS TO OUR DIGITAL VERSION ARE NOW FREE.
Every week we share a new Featured Story with our Stainless Steel community. Join us and let’s share your Featured Story on Stainless Steel World online and in print.