A large conveyor system project in the Netherlands relied on 18-metre stainless steel tubes to provide a lasting, economical solution.
Text by Stalatube
De Regt, a company specialising in developing and constructing internal transport systems and storage facilities, designed and built a conveyor system project from STALATUBE high-strength stainless steel tubes for Verbrugge Terminals B.V. The project required hollow sections with specific strength due to the 18-meter free span of the structures. De Regt designed, fabricated, welded, and installed the conveyor system. They chose high-strength stainless steel due to its strength, lightweight, 18-meter special lengths, corrosion resistance, and needed just-in-time delivery. The demanding project met the customer’s and the end customer’s requirements.
More strength and length options
De Regt recently undertook a project involving a 350-meter-long closed-frame construction with multiple conveyor belts inside. The project was commissioned by Verbrugge Terminals B.V. The Verbrugge terminal, situated at the harbour in Terneuzen, the Netherlands, serves to transport and store artificial materials, including fertilizers like ammonium sulphate and soda. The need for a new conveyor system arose when the old system, made from mild steel, reached the end of its lifespan.
The project posed challenges because the chosen material had to be strong, lightweight, and corrosion-resistant.
Additionally, the designers aimed to reuse the old concrete foundations. They needed to connect the frame sections with an 18-meter base span in their design.
“While our standard tube length is 6 meters, we accepted the challenge when the customer requested 18-meter tubes for their project. Our production, research, and logistics teams collaborated with De Regt’s engineers to achieve the best possible outcome for this project,” explains Stalatube’s Area Sales Manager Mike Hing.
De Regt opted for high-strength stainless steel due to its durability, elongation properties (compared to mild steel), and resistance to corrosion. Initially considering concrete, wood, and steel, the benefits of high-strength stainless steel became a focal point of discussion. “In such an aggressive environment, corrosion resistance is crucial,” says De Regt’s Project Manager Paz Boekhout. De Regt conducted several corrosion and welding tests since the different stainless steel grades would be used in the project.
Smart design
The weight of an 18-meter-long hollow section posed a challenge during the design process. This led to discussions about utilising Stalatube high-strength materials.
Strategically using high-strength tubes where maximum yield strength and bending resistance are crucial, designers can calculate optimal lightweight structures. De Regt’s engineers decided to combine standard stainless steel tubes with high-strength stainless tubes.
“The entire 350-meter-long structure consists of 18-meter-long tubes, with one section weighing approximately 15 tonnes. To address the forces working in the longitudinal direction, several 6-meter-long truss frame supports were interspersed between the longer frame segments,” explains Paz Boekhout.
De Regt ordered stainless steel tubes in various dimensions. Stalatube lasercut the tailored tubes according to the customer’s specifications.
The customer saved costs and reduced scrap during the manufacturing and installation phases using Stalatube, which provided exact lengths and customised tube connections.
Just-in-time delivery
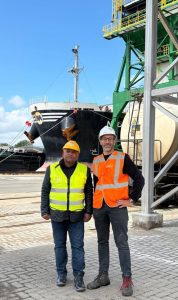
Photo: Stalatube
Keeping up with the project’s tight schedule was crucial, and any installation delays were unacceptable. The goal was to minimize disruptions to daily port operations, necessitating careful planning for the new conveyor system setup.
Material orders were strategically timed and delivered following project other activities and installation schedules during the project.
All preliminary work occurred off-site, and the installation had to proceed swiftly and according to plan. Consequently, just-in-time delivery played an important role.
“Offsite, we prepared each part as ready as possible beforehand, ensuring efficient installation at the port. To minimize disruptions to daily operations, we did the installation of the new frames in a very short period,” Paz Boekhout states.
The installation of four 18-meter-long structures took approximately one week at the port.
The engineers aimed to reduce connecting welds, as welding points are typically the weakest areas of a structure. De Regt’s engineers conducted welding tests to determine the optimal method, ultimately settling on MAG welding.
“Minimizing welded joints improves the overall strength. Welding points are inherently vulnerable,” continues Paz Boekhout.
Stalatube’s welding expert was also consulted, leading to the use of MAG welding after thorough testing.
Working together for the best possible outcome
According to both Paz and Mike, the lightweight but high strength, corrosion resistance, and project support from Stalatube were the critical factors for the collaboration.
“No installation delays occurred although we faced some unexpected challenges along the way that were beyond our control. Together we could solve them all,” says Mike Hing “Together with our customer Verbrugge we see the benefits in the use of highstrength stainless steel instead of mild steel. It is a bigger investment initially but will last longer and pay off in the long run. Also, with the smart design, we could reduce the overall costs,” concludes Paz Boekhout.
About this Featured Story
Appearing in the December 2024 issue of Stainless Steel World Magazine, this Featured Story is just one of many insightful articles we publish. Subscribe today to receive 10 issues a year, available monthly in print and digital formats. – SUBSCRIPTIONS TO OUR DIGITAL VERSION ARE NOW FREE.
Every week we share a new Featured Story with our Stainless Steel community. Join us and let’s share your Featured Story on Stainless Steel World online and in print.