The heart of the CMS experiment. Image courtesy of CERN.
The construction of particle accelerators like CERN’s Large Hadron Collider (LHC) and the HL-LHC project represents a pinnacle of scientific and engineering prowess. These endeavors demand precise materials and manufacturing processes, particularly stainless steel and nickel-base superalloys, to meet stringent requirements. This articles explores how innovation in materials drives progress in particle physics and high-energy experimentation.
By Stefano Sgobba, Katie Elizabeth Buchanan, CERN
The construction of the world’s largest and most powerful particle accelerator ever built, CERN’s Large Hadron Collider (LHC) and its ongoing upgrade, the High Luminosity LHC (HL-LHC) project, required a wide application of tightly specified advanced materials and manufacturing processes. “In modern large superconducting accelerators, stringent requirements are placed on the materials used for vacuum, cryogenic and structural systems. Their physical and mechanical properties, machinability, weldability and brazeability are key parameters. Adequate strength, ductility, magnetic properties at room as well as low temperatures are paramount factors”, says Stefano Sgobba, head of the Materials section at CERN, the European Organization for Nuclear Research based in Geneva, that operates the largest particle physics laboratory in the world. “Stainless steels”, continues Stefano Sgobba, “play a crucial role in most components of modern particle accelerators and high-energy physics experiments, of fusion reactors and their superconducting magnet structures working at cryogenic temperatures. The material challenges of such projects are enormous, requiring a wide application of tightly specified stainless steel and nickel-base superalloys products and grades. The final products must feature a controlled microstructure and adequate mechanical, physical, magnetic or vacuum properties and often a combination of them”.
Material assessment
CERN gained a deep experience in developing, selecting, specifying and assessing stainless steel grades, steelmaking and processing applied to achieve the final stringent properties, acquired within decades of building large systems that must guarantee a reliable, long-lasting service with limited interventions. ITER Organization, which is building in Cadarache, south of France, the largest and most integrated superconducting magnet system ever – with similar material challenges as featured by CERN – has had a Cooperation Agreement in place with the Materials service of CERN since 2009 to draw on the expertise in material assessment for magnets that was developed during the construction of the LHC machine and its large experiments.
The example of the dipole and quadrupole magnets of the LHC and HL-LHC is largely representative in this regard. A special austenitic high manganese and high nitrogen stainless steel was developed already in the mid-nineties in cooperation with Böhler Edelstahl for the beam screen and the cooling capillaries of the machine vacuum system. The steel retains high strength, ductility, and very low magnetic susceptibility at the working temperature between 10 K and 20 K. Since, several tens of kilometres of components had been produced in this special Electroslag Remelted (ESR) grade that will be used again for the beam screens of the HL-LHC project (3.1 km of finished strip for the beam screen and 4.6 km of seamless cold-drawn cooling tubes in lengths of up to 14 m, Fig. 1).

Magnet components
The LHC magnet cold bore is manufactured as a seamless 316LN tube. 316LN is also the grade of the shrinking cylinder of the dipole magnets. For the LHC, 2500 bent plates of 15.35 m length and 10 mm thick for a total weight of approximately 3000 tonnes were used, welded longitudinally by a special Surface Tension Transfer (STT) technique combined with traditional pulsed Metal Inert Gas (MIG) welding. For the HL-LHC magnets (Fig. 2), similar 316LN plates in thicknesses up to 15 mm were produced by ArcelorMittal Industeel under the same specification, same manufacturing route and forming process.
“Some components required innovative and unprecedented solutions”, argues Stefano. “An example is the more than 2800 magnet end covers of complex shape and large diameter (570 mm), including several nozzles that have been fabricated for the LHC, starting from HIPed 316LN powders and near net shaped into geometry close to the final form. They operate smoothly in the machine since decades at almost absolute zero temperature and are perfectly leak tight”. Between the magnets, some 1600 interconnections are installed, consisting of several thousand of components for which leak tightness is also paramount, mainly working at cryogenic temperature. These interconnection components are also essentially based on austenitic stainless steels. For the convolutions of the several thousands of bellows involved in the machine and working under cyclic load at 1.9 K, a special ESR high alloy and highly formable 316L grade was used showing an extremely low inclusion content and improved austenite stability at the working temperature.

Stainless steel solutions
High strength stainless steel solutions are also applied to structural components of the ITER magnet system. An example is the precompression structure of the Central Solenoid (CS) that consists of six independent coils kept together by a precompression support, providing a precompression load of 210 MN to ensure contact in between modules, by reacting vertical tensile loads and maintaining coil-to-coil contact when the solenoid is energized. The CS precompression system includes large open die forged components such as tie plates, lower and upper key blocks, load distribution and isolation plates and other attachment support and insulating hardware. The tie plates operating at 4 K are manufactured starting from forgings in a high-strength austenitic stainless steel (FXM-19) with a stringent specification. FXM-19 (also known through its proprietary version Nitronic® 50) is a high N and Mn bearing austenitic stainless steel, featuring ready weldability and forgeability, high strength and toughness in a wide temperature range including at cryogenic temperatures. The 27 tie plates operating at 4 K are manufactured by the company Rolf Kind GmbH from single forgings involving blanks of more than 15 m length (Fig. 3). Stefano reminds that in order to comply with the tight metallurgical requirements applicable to the final product (inclusion cleanliness, fineness of microstructure, limited ferrite content and magnetic permeability, internal soundness – the products are 100% ultrasonic checked), the steelmaking process includes a mandatory ESR step despite the heavy gauge ingots needed as starting products for forging.
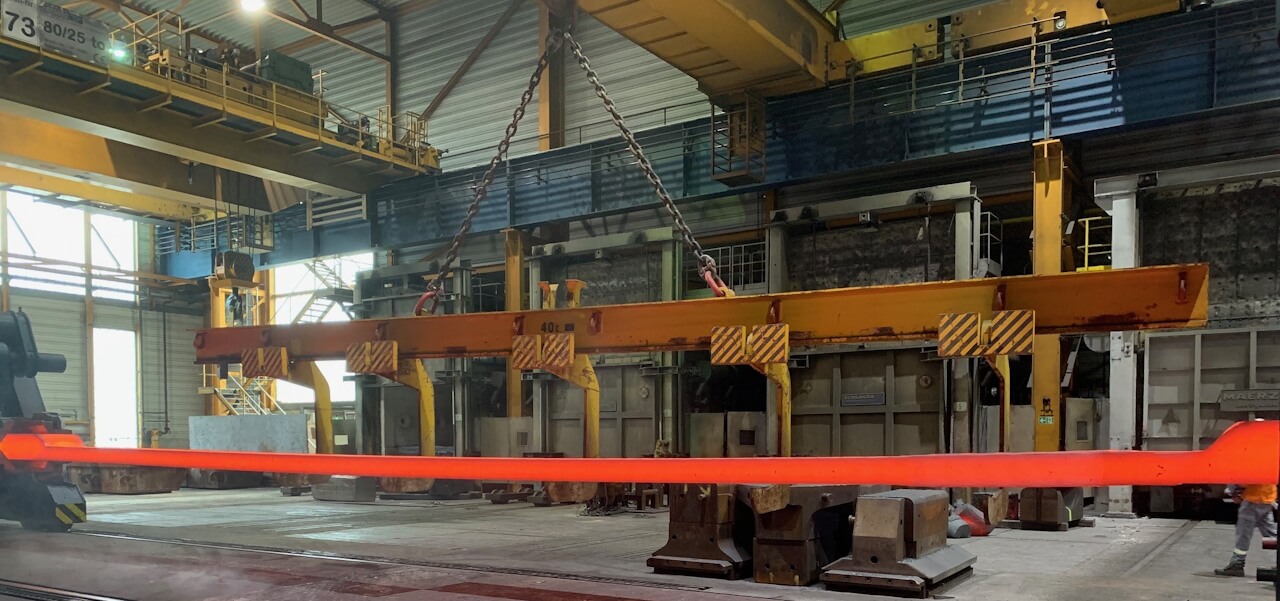
Upgrades for high luminosity operation
The beams inside the LHC collide at four locations around the ring, corresponding to the positions of four experiments. The Compact Muon Solenoid (CMS) is one of two large particle detectors at the LHC that, together with ATLAS is one of two general-purpose experiments having observed the Higgs boson decays. CMS contain the largest superconducting solenoid magnet ever constructed in terms of stored energy, featuring a length of 12.5 m, an inner diameter of 6 m and delivering a maximum magnetic field of 4 T (Fig. 4, see main phoot of this article).
As part of its HL-LHC upgrade programme, in 2026 major elements of the CMS detectors will be changed in order to operate at high luminosity. The high-granularity calorimeter (HGCal) is one of the major upgrades of CMS. It will feature an extremely high readout and granularity and will allow to cope with the harsh radiation environment during HL-LHC operation. The HGCal includes a so called “hadronic compartment” made out of austenitic stainless steel absorbers. HGCal will operate in the strong CMS magnetic field of 4 T. Therefore, all used materials shall be non-magnetic or at least, feature a very feeble, controlled and predictable magnetic permeability. The total weight of the stainless steel plates needed for HGCal absorber layers is around 564 tonnes. The relative magnetic permeability in the bulk plate material has been specified not to exceed 1.05, in order to limit the axial forces attracting the absorber plates to the centre of the CMS superconducting solenoid. The focal ways to avoid this value to be exceeded is a stringent control of delta-ferrite content and guaranteeing sufficient stability against martensitic transformations. This is paramount, taking into account that due to the quantity involved, cost effectiveness and easy machinability a 304L grade was selected. “In this constraining framework, two precautions were taken: selecting a steelmaking process based on ingot casting, to limit as much as possible residual delta-ferrite issued from primary solidification and difficult to revert in the subsequent hot rolling process, and specifying a high alloy 304L (1.4306) to reduce the risk of spontaneous and strain induced martensitic transformations”, says Katie Elizabeth Buchanan, staff materials engineer at the CERN Materials section. The material was produced by ArcelorMittal Industeel with an optimised well-balanced composition and is presently being machined in Pakistan. Due to the stringent requirements of magnetic permeability, the magnetic properties of each plate had to be extensively checked, not only at the surface but also at mid-thickness in several positions around the edges (Fig. 5).

Advanced inspection
“The relationship between the averaged magnetic properties measured on the faces and on the edge of the first produced plate and the average bulk magnetic properties measured by static-sample magnetometry on extracted samples of the plates could be consistently assessed”, continues Katie. “The magnetometer for volumetric characterisation of weak magnetic materials has been developed by the CERN Magnetic Measurement section, and results could be compared with standard inspection measurements performed with a portable magnetometer system on the field. This comparative approach paved the way to identify a reliable and industrially applicable method of assessing the permeability in line with the functional HGCal requirements, that was successfully applied for the whole production”. The selection of a 1.4306 product issued from ingot casting for this application has proven to be fully adequate. Katie reminds that only some products marginally featured a locally higher level of magnetic permeability, due to unavoidable variations in chemical composition or ingot segregation. These variations can result in some traces of delta-ferrite in the bulk of the products and result in an expected double peak of permeability, that indeed was measured around mid-thickness of some plates. “However, the volumetric studies demonstrated that the average bulk magnetic properties, which are relevant for the functionality of the products, were generally well within the acceptance criteria”, argues Katie, “and that the volumetric response of this ingot cast grade is fit for purpose”.
The examples above demonstrate that the successful application of a stainless steel for a demanding accelerator, fusion magnet or high energy physics component is not simply due to a selection based on a mere “chemical composition” or a designation. It needs to be the result of a proper specification, selection of an adequate steelmaking route, the definition and extent of suitable controls, as demonstrated by the successful application of magnetic permeability advanced inspection and assessment techniques to the HGCal absorber plates – conclude Katie and Stefano.
About the authors
Stefano Sgobba graduated in Nuclear Engineering from Politecnico di Milano in 1990 and obtained his PhD in 1994 at the Laboratory of Mechanical Metallurgy of the Ecole Polytechnique Fédérale de Lausanne under the guidance of Prof. Bernhard Ilschner. Immediately after he joined CERN as staff member, where he is responsible since 2001 of the Materials section, now within the Mechanical and Materials Engineering group of the Engineering Department. As from 2009 he is also in charge of the metallurgical and material testing support provided by CERN for the construction of the ITER Magnet System, in the framework of the CERN-ITER Cooperation Agreement.
Katie Elizabeth Buchanan received a first-class honour’s B.Sc. degree in Material Engineering from the Sheffield Hallam University in 2019. After her first employment with Intertek in the Production and Integrity Assurance in the Corrosion sector, she was recruited by CERN as a staff member in 2021 where she joined the Materials section.
Reference
“Understanding the passive behaviour of low-chromium high-strength Hybrid steel in corrosive environments”: https://www.nature.com/articles/s41529-023-00392-z
About this Featured Story
This Featured Story appeared in Stainless Steel World March 2024 magazine. To read many more articles like these on an (almost) monthly basis, subscribe to our magazine (available in print and digital format) – SUBSCRIPTIONS TO OUR DIGITAL VERSION ARE NOW FREE.
Every week we share a new Featured Story with our Stainless Steel community. Join us and let’s share your Featured Story on Stainless Steel World online and in print.