For over 245 years, industrial plant construction has played an important role in BUTTING’s success. Recently, the company’s sites handling this activity were placed under joint management, with Marcel Bartels becoming CEO of the BUTTING Group’s Plant Construction division at the beginning of 2024.
By Joanne McIntyre, Stainless Steel World
SSW: What objectives are you pursuing with your Plant Construction division?
Marcel Bartels (MB): BUTTING Anlagenbau aims to implement the best solution for the customer’s requirements at the best location within the BUTTING Group.
The division’s locations are designed in such a way that we can cover all customer expectations. As a quality leader in highly specialised plant construction, we cover every aspect, from special material applications, high processing depth, metal cutting, special approvals, etc., to cost leadership in classic pipeline and vessel construction.
This range of services is complemented by a production site in Tieling in north-east China, which is managed according to BUTTING values and standards. BUTTING CryoTech in Burgkirchen, Germany, fills a niche in the division by manufacturing couplings, valves, vacuum-insulated pipes (VIPs) and complete skids for cryogenic applications in the gas sector.
The breadth of the Group and our optimised cost structures allow us to support customers throughout the entire lifecycle of their products. Project management, logistics, supervision, procurement benefits and comprehensive project support are provided at all locations, rounded off by value engineering and entirely new developments.
SSW: How is this approach implemented in day-to-day business?
MB: Imagine you are a buyer in the pulp and paper industry, and you need vessels, pipelines, and on-site expertise to supervise your construction site. BUTTING Anlagenbau in Schwedt is your ideal partner – this location remains our expert unit for vessel and pipeline construction, assembly and industrial services. With locations in Schwedt and China, the BUTTING Group is broadly positioned in the field of plant construction. Both sites are also expanding their capacity on a project-by-project to meet tight deadlines. Our focus is on efficient structures and cost-effective processes.
As CEO of the Plant Construction division, Marcel Bartels focuses on managing all plant construction activities in the BUTTING Group, including the pipeline and plant construction business unit in Knesebeck.
SSW: Can you give us another example?
MB: If you are responsible for procurement in the aerospace industry, you expect the highest quality, along with the necessary approvals in accordance with EN ISO 9100 or NADCAP for production in this highly sensitive industry. Or perhaps you need piping components made from special materials with complex hydroforming processes. Our team at the Knesebeck site is the right partner for you, especially if the components are to be installed in a container made of nickel-based alloys, such as Alloy 602CA, or if acceptance according to ASME VIII Div. 1 is required. We specialise in this field at our Knesebeck site.
SSW: Those are some very complex requirements.
MB: Yes, and it can get even more complex and more innovative: we develop our own products in close cooperation with our customers.
An example is developments for cryotechnical applications where we serve a qualitatively demanding and growing niche market.
We also want to develop our own standards in this market and play an active role in the energy transition. We’re putting our slogan “more than pipes – for a better quality of life” into practice!
SSW: Where do you see the most added value for your customers in plant construction?
MB: Our customers can draw on the BUTTING Group’s extensive human resources in all areas of value creation – for design services and welding, materials and forming technology, as well as in quality assurance and project management. We utilise this specialist expertise across all locations. At the same time, we can optimise our existing capacities worldwide. Everyone concentrates on their core area of expertise while focusing on each specific customer’s needs. BUTTING also has a strong financial position, which creates trust with our contractual partners.
SSW: What is your vision for plant construction?
MB: The BUTTING Group is growing and investing at all locations to benefit our customers, employees and the environment. We give pipes a purpose! With our services, we want to make our customers more successful – working in partnership to realise projects, positively shape the future and contribute to society.
I am grateful to be able to write part of the company’s history with my teams and I’m convinced that, together with our customers, we can pass on the BUTTING family business to the 8th generation as an owner-managed, self-determined and healthy company.

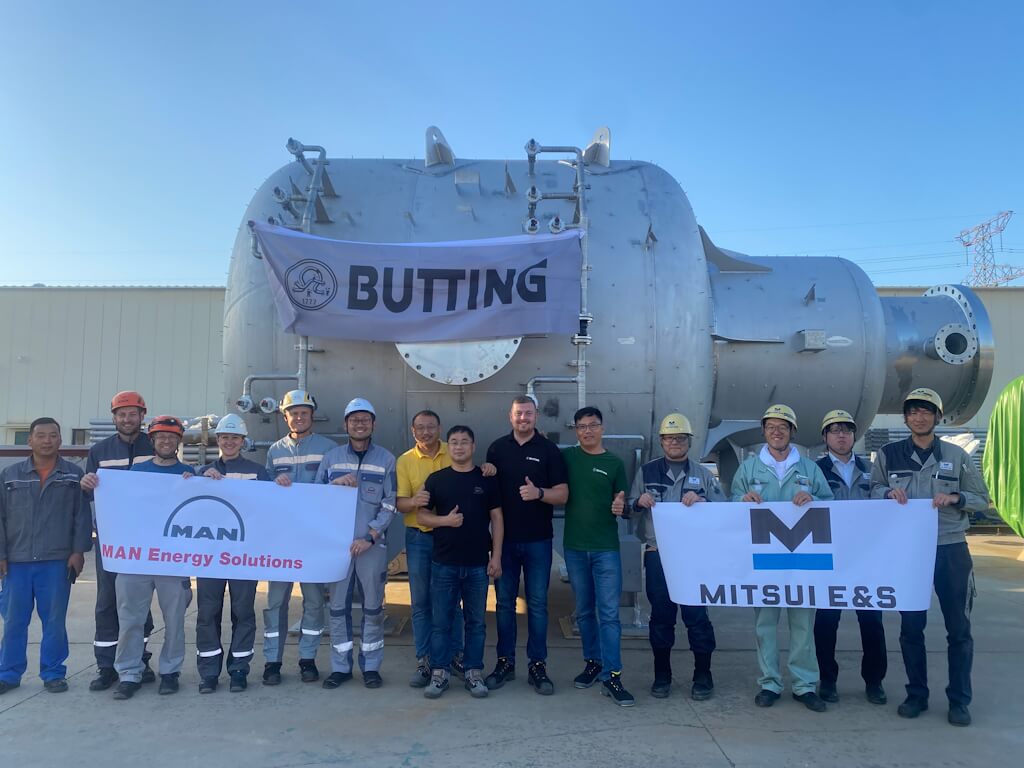
Plant construction worldwide
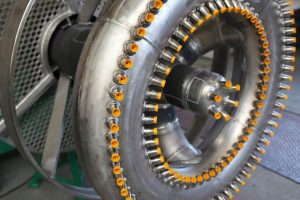
While BUTTING has built many SCR (Selective Catalytic Reduction) catalytic converters for MAN Energy Solutions, at the end of 2023, a new milestone was the production of a massive Cluster 5 Double Layer. The converters are used in cruise ships and cargo ships to reduce nitrogen oxide emissions by up to 90%. The clusters, ranging in size from 1 to 5, are produced for both high and low-pressure ranges.
The family business relocated its series production for SCR catalytic converters from Knesebeck to Tieling in China at the beginning of 2023 to generate economic benefits for its customers. Engineering and prototype construction is supported by the headquarters.
The Cluster 5 Double Layer has a diameter of 3,900 mm and a total weight of 28 metric tonnes. “We are proud of our team’s performance and very confident that the Cluster 5 Double Layer will be a successful product for our customer,” states Steven Schlabritz, Project Manager at BUTTING.
Plant construction in Knesebeck
Recently BUTTING successfully delivered a ring burner – an important component for ammonia production – for its longstanding customer Topsøe.
The main plant in Knesebeck was commissioned for the first time to produce this one-off item, which delighted the customer in all respects. With a diameter of 1,200 mm and a length of 3,000 mm, the ring burner is used for the Sohar International Urea & Chemical Industries LLC (SIUCI) project in Oman, where hydrogen and nitrogen are converted into ammonia at high temperatures and pressure with the help of a catalyst.
The many forming operations and the welding of various temperature-resistant nickel-based alloys proved to be a challenge. Particularly noteworthy are the very sophisticated manual welding operations. Both the machining of the component and the final assembly had to meet tight tolerances. Andreas Kasten, Sales Manager Spools and Plant Construction, states: “Kudos to our manufacturing team, which has mastered their craft to make such a precise component. Plant Construction at Knesebeck focuses on products with a level of vertical integration that calls for special competencies in material grade technology, as well as extensive skill and expertise regarding approvals and quality assurance.”
Plant construction in Schwedt
Large quantities of pulp and paper are produced in Kemi, in the far north of Finland. Recently, an existing pulp mill in the seaport city was converted into the largest fossil-free, sustainable pulp mill in Europe using BUTTING pipes. The new bioproduct plant focuses on achieving high environmental, energy, and raw material efficiency. Marko Busse, Managing Director of BUTTING Anlagenbau in Schwedt, explains: “The pulp and paper industry is an important yet challenging industry regarding sustainability because production and environmental protection are often in conflict. However, the modernisation of the Kemi mill shows that sustainable production is possible. Advanced technologies and innovative processes minimise resource consumption, energy demand and environmental impact.”
The BUTTING Anlagenbau site was awarded the piping contract for the cooking plant, fiber line and rainwater areas. Over 1,035 mt of piping material and 430 metric tonnes of support material (V2A, V4A, carbon steel, titanium, duplex and super duplex) were delivered to Finland.
An experienced, 300-strong installation team laid almost 39 km of pipelines with dimensions from DN 15 to DN 1,200 on-site. Christoph Kunkel, the installation manager sent by Knesebeck, reports: “The tight schedule and extreme weather conditions presented significant challenges. We worked in freezing temperatures down to -27 °C and strong, icy winds. Work was completed successfully, resulting in additional orders from the client.”
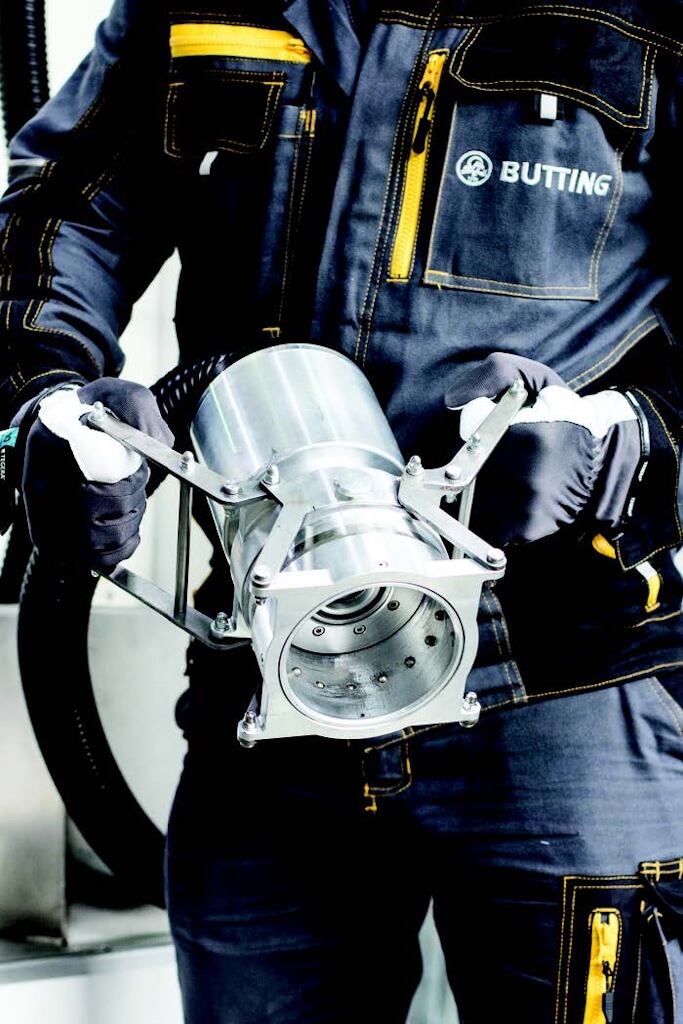


Plant construction in China
Drinking water supply is a major challenge in regions where natural resources are scarce. BUTTING is a one-stop shop that supplies entire modules and connecting pipework for new desalination plants.
For a recent project, 192 modules were manufactured in the Tieling factory. Almost 5 km of piping components in the dimensions ½˝ to 24˝, weighing 200 metric tonnes, and 2,800 stainless steel fittings weighing 100 metric tonnes and largely made of super duplex, were 100% prefabricated then non-destructively tested and installed in base frames. 3,500 high-pressure filters were installed, aligned and piped, and over 900 control valves, flow meters, etc., were installed and wired to the more than 390 control cabinets.
Jens Ellermann, Managing Director at BUTTING China, explains: “We not only assemble the piping components in the base frame but also install all required equipment insulate items at the customer’s request.”
The modules are used as a central component in the desalination and treatment process of the plant and must reliably withstand heavy stresses in a highly corrosive environment. At the customer’s request, an elaborate three-coat paint finish was applied to all modules. High demands for dimensional accuracy were met to ensure a precise fit.
Mr Ellermann adds, “The advantages of BUTTING prefabrication pay off here with over 95% of the welding seams produced in-house. This shop welding and pickling of whole components ensures the required seam and surface quality. In addition, non-destructive tests carried out on BUTTING’s premises mean that pressure, FE and x-ray testing are not required on the construction site.”
The modules and pipelines are completed according to just-in-time delivery for precise operational planning that meets customer requirements.
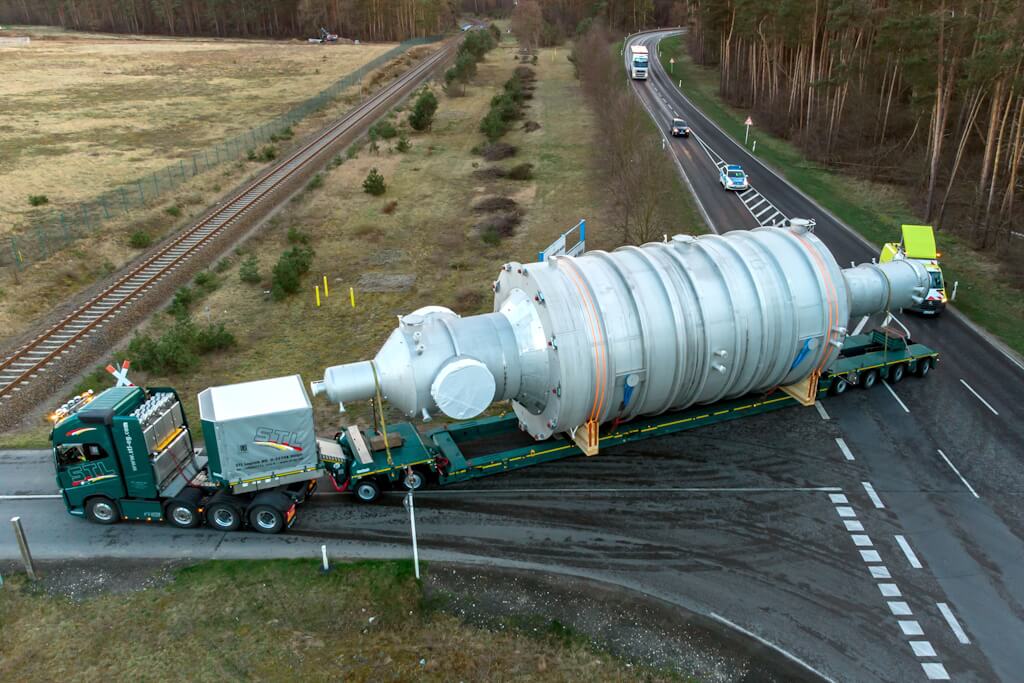
Plant construction from BUTTING CryoTech in Burgkirchen
Fusion energy is a forward-looking approach to sustainable energy production that offers the potential for a limitless, clean, and environmentally friendly energy source. BUTTING’s extensive range of key technologies demonstrates its commitment to environmentally sustainable energy production. These include vacuum-insulated pipelines (VIP pipelines) in customised designs for fusion reactors, cryogenic valves, skid assemblies, pressure vessels and customised components. State-of-the-art technologies such as finite element analysis guarantee the highest product quality. Mr Bartels sees further benefits for customers: “Thanks to our global presence, we can send experienced technicians to supervise assembly and installations. This has resulted in successful partnerships with leading companies in Boston and Australia.”
“We are always seeking promising new partnerships and are flexible to meet the diverse requirements of fusion energy. Our materials meet the highest standards, and our designs comply with the ASME B 31.3 code. Production occurs at our BUTTING Group sites – either in Knesebeck or primarily in Burgkirchen,” explains Patrice Brossard, Sales Director North America.
About this Featured Story
This Featured Story appeared in Stainless Steel World April 2024 magazine. To read many more articles like these on an (almost) monthly basis, subscribe to our magazine (available in print and digital format) – SUBSCRIPTIONS TO OUR DIGITAL VERSION ARE NOW FREE.
Every week we share a new Featured Story with our Stainless Steel community. Join us and let’s share your Featured Story on Stainless Steel World online and in print.