Cast products that require a high level of customer order specifications in the pressure vessel industries go through rigorous evaluation, inspection, and testing procedures that verify all identifying criteria have been met. These procedures are developed based on standardized documentation from organizing bodies such as ASTM, ASME, ISO/EN and others.
The agreements made between the producer and customer are finalized in the certificate of conformance and are the guidelines by which high-specification castings are to be manufactured.
By Michael Porfilio, Director of Quality and Technical Services, SF&E
Following all the rules and regulations required to cast, process, and eventually certify high-specification castings, there must be an astute and detail-orientated team of individuals that understand all aspects of the foundry and customer base serviced. Dedicated Metallurgists, Process Engineers, Foundry Engineers, and QM/QA personnel are a mandatory element for success. The customer’s final product demands that all codes, directives, and specifications must be followed prudently and treated with respect.
Contract review
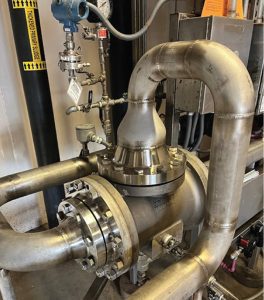
The customer will specify the level of criticality during testing and inspection that is required by their internally developed standards.
Once all the required inspection and testing operations are reviewed, NDE/NDT technicians and level III professionals must submit their technical procedures and time personnel records to numerous agencies for approval. These documents are submitted sequentially and can vary greatly in length to gain approvals for the testing and inspection operations.
Material specifications
Metallurgical specifications contain chemical ranges and mechanical properties such as tensile strength, yield strength, percent elongation, and percent of area reduction. These properties ensure that the produced material and the heat treatment applied to them meet the minimum properties of that specification. Other metallurgical items that are useful in high alloy work are hardness measurements to verify the heat treatment process was effective. Processing specifications include but are not limited to different types of heat treatment, cleaning methods, machining, and welding. Tables or declarations show what heat treatment is allowed for each individual alloy. Very specialized welding programs are indicated in the material specifications that are required for staying compliant with the needs of the high-specification contracts. Control of filler materials, welder qualifications, equipment calibration, development of welding procedures and many other elements are required to be compliant with the relevant standards.
EN/ISO Pressure Equipment Directives and Regulations
Since 1997 the European Union (EU) has been developing new directives to regulate pressure vessel activities and certification of designs, components, and source materials like castings and forgings. In January of 2022 the United Kingdom had a Pressure Equipment (Safety) Regulation following the same types of alignment and rules. The BREXIT UK Pressure Directive is in force for England, Northern Ireland, Wales, and Scotland. Producing castings for these standards has many complexities. These two directives have provisions where ASTM and ASME materials can be used for supplied projects using a completed and endorsed notified body with a document called a Particular Material Appraisal (PMA). This PMA document has specific design conditions such as temperature (lowest operating temperature), pressure for usage, and other design considerations. It will also list a material for use which could be an American cast grade.
Inspection personnel qualification
All non-destructive testing methods on both ASME or PED require highly trained, evaluated, and certified personnel to perform these types of tests and evaluations. Each NDE / NDT method has rigorous classroom and hands-on training that needs to be documented prior to certification.
Inspection
High-specification products require qualification of the physical condition of the casting both on the surface and volumetrically. The use of different types of NDE/NDT methods verifies conformance to the standards that are agreed upon with the customer. Common foundry techniques to verify the level of quality on the surface, sub-surface, and volumetric analysis are detailed in Table 2.
NDE / NDT overview
These are just some of the more common tests that may be performed on high-specification work that end up in pressure applications. The pressure codes all require different levels of inspection to ensure quality.
The PED follows the inspection activities listed in Table 2.
Table 1. Some of the EU/UK vs. US material and testing specifications.
Special process or testing technique | ISO or EN test method specification required | ASME or ASTM test method specifications required for PMA PED UK PESR orders |
Welding | EN ISO 9606 – 1 thru 5 assorted welding activities EN ISO 15164 – Welder personnel qualification |
ASME BPVC, Section IX welding code ASTM A488 – Foundry welding code |
Chemical Analysis | EN ISO 15350 – Determining C & S EN ISO 10720 – Determining N & O EN ISO 10200 – Chemical analysis of ferrous materials |
ASTM A751 – Test methods chemical analysis |
Tensile testing | EN ISO 6892-1Tension testing EN895 Destructive weld tensile test |
ASTM E8 – Standard method of tension testing |
Impact testing | EN ISO 148-1 | ASTM E23 – Notched bar impact testing |
Hardness testing | ISO 6506 – Brinell testing ISO 6508 Rockwell testing |
ASTM E10 – Brinell testing ASTM E18 – Rockwell testing |
NDE / NDT personnel Qualification |
EN ISO 9712 – Qualification and certification of testing personnel | ASNT SNT-TC-1A for personnel qualification |
NDT – X-Ray (RT) | EN ISO 5579 – Radiographic testing of metallic materials | ASTM E94 – Standard RT film methods ASTM E2035 – Computed radiographic method |
NDT – Liquid penetrant (PT) | ISO 3452 – Liquid penetrant, general principals | ASTM E165 – General industrial method ASTM E1209-Fluorescent method |
NDT – Magnetic particle (MT) | EN ISO 9934 – Magnetic particle testing ISO 17638 – Magnetic particle testing of welds |
ASTM E1444 – Standard practice for MT |
NDT – Ultrasonic (UT) | ISO 4992-1 – Ultrasonic testing of castings EN ISO 17640 – NDT of welds |
ASTM A609 – Casting inspection |
NDT – Visual (VT) | EN13018 – Visual testing, general concepts ISO 17637 – Visual testing of weld joints |
ASTM A802 – Visual ‘MSS SP-55 |
Material certification | EN 10205 – Metallic inspection documents EN 764-5 – Inspection documentation of metallic materials and compliance with the material specifications |
ASTM A703 – Pressure containing parts |
Material properties testing
With the American pressure codes and the EU/UK pressure directives being material based, the common metallurgical testing techniques are very vital to proper compliance. Following is an overview of these techniques.

– Chemical analysis – Optical Emission Spectrometry (OES):
Optical emission spectrometry has been widely used as a method to control the production of steel and other alloys in primary producing manufacturers such as foundries due to its speed, accuracy, and efficiency. In the case of highly specified cast alloys, OES analysis is a common technique to confirm the chemical composition of a metallic sample. OES allows for the analysis of many elements in a large magnitude of concentrations in a single measurement making it a useful tool to certify high specification cast alloys. Ni, Cr, Cu, Mo, Va are residual elements that can be of concern in certain steel grades for high spec work.
– Tensile testing
Tensile testing consists of applying a pulling force on a test material in two opposite directions. This allows us to determine how strong a material is and how much deformation it
can withstand. Ultimate tensile strength, elasticity, yield strength, and strain deformation are typical properties reported, but several other characteristics can also be determined. Calculations for yield strength can be affected by the 1.0 or 0.2 offset vs. 0.5 extension under load (EUL) between different specification orders and alloy combinations.
These tests are generally performed on an electromechanical or universal testing machine and are standardized by ASTM E8, ASTM A370, and ISO 6892. The degree to which a material is tested is governed by the level of specification required by the customer.
– Hardness testing
Hardness testing is a way to measure the surface quality of a cast material. It allows for the determination of a material’s resistance to permanent indentation in a non-destructive manner.
– Impact testing
Impact testing evaluates the amount of work required to rupture a test material in a destructive fashion. The Charpy test is the most used technique in measuring this material property for high specification cast alloys.
ASTM E23 and ISO 148-1 are the governing guidelines for Charpy impact testing of V-notch metallic materials. There are three main characteristics that can be measured by a Charpy Impact Test: total absorbed energy, lateral expansion, and percent shear fracture area.
– Metallurgical testing summary
In high-specification work, the need to determine the chemical, mechanical, and material properties of cast metal is crucial in ensuring that the customer receives a product that meets their design requirements. OES, tensile, hardness, impact, corrosion, metallography, and ferrite prediction testing are all essential methods to satisfy the stringency of high-specification castings. The governing bodies that encompass the standards for these tests are continually audited and revised to ensure that industry repeatability and accuracy are maintained.
NDE / NDT method | General applications and positive attributes | Limitations |
Radiography (RT) | Can be used for ferrous and non-ferrous materials. Has a great reference library from ASTM (E192, E186, E280, E446) for steels. Many different classifications of defects are showcased in the above reference radiographs |
Casting wall thickness vs. thinness and the ability to maintain proper levels of sensitivity. Is not reliable to exhibit cracking and linear indications. |
Magnetic Particle (MT) | Used for ferro-magnetic materials with being extremely sensitive to cracks and does well highlighting larger rounded indications. | Smaller (0.062” diameter and smaller indications) are hard to ascertain. Relies on being able to magnetize with coil or cabling. |
Liquid Penetrant (PT) | Used on non-magnetic materials highlighting cracks of all sizes but is more sensitive when used as a fluorescent method. Does very well with all sizes of rounded indications. | Can leave many false indications on the surface of certain alloys. Method is limited to surface evaluation only. |
Ultrasonic Testing (UT) | Must be used on fine grained materials. Larger grained microstructures like austenitic materials and nickel-based alloys lose the back reflections. | Needs very experienced technician to be able to ascertain reflections from the material being tested. |
Visual Testing (VT) | Used to verify cast external and internal surfaces using reference photographs or tactile plates. Easy to use magnification to assist in evaluation. | Can be very subjective to determine conformance to specifications, difficult to find readily available Level III personnel |
Source inspection
A source inspector from the Notified Body is an individual who is required by a customer or the engineering group overseeing the project to witness milestones in the creation of the casting. Common occurrences are some of the following operations:
- Contract review
- Melt and pouring
- Stamping of heat numbers for traceability – castings and test material
- Heat treatment
- Welding
- Post-weld heat treatment
- All inspection operations – VT, RT, MT, PT, dimensional, etc.
- Endorsement of the certification package
- Shipping operations
QA Material certifications including dual certification
Materials produced to the pressure vessel codes and directives require rigorous certification. Following the tenants of EN10204 for the inspection and certification documents is required for all PED activities. A common request is to produce castings that meet the dual certification requirements of both ASME and PED/UK PESR. Overlapping chemistry ranges, as well as congruent mechanical properties, are needed for dual certification.
Application and vessel manufacturer – Hydro-Thermal’s Direct Steam Injection (DSI) heaters
Hydro-Thermal is a global leader in on-demand steam injection fluid heating, cooking, and processing systems. Direct Steam Injection (DSI) technology revolutionizes how industries handle heat transfer. By mixing steam and processing fluids directly, DSI heaters deliver precise and consistent results across various industries, including ethanol, chemicals, wastewater treatment, food and beverage, and meat and poultry processing all in need of different levels of pressure governance.
Direct Steam Injection (DSI), offers several advantages over traditional heat exchangers. DSI heaters modulate steam at the injection point, providing exceptional heat transfer efficiency. This results in significant energy cost savings, efficient control of process fluids, and the ability to handle high-viscosity slurries without burn-on.
The importance of Hydro-Thermal’s PED Certification
Hydro-Thermal’s holds a 2014/68/EU PED certification promoting conformance as well as safety. This certification process is conducted through an authorized equipment insurer, ensuring that every step meets stringent standards. Vessels of specific sizes, adhering to prescribed rules and documentation, are manufactured to ensure compliance and guarantee that our products are built to last and perform at their best.
Hydro-Thermal has been delivering its technology of directly injecting steam into any fluid to heat that fluid to an exact temperature worldwide for 90 years. To deliver in Europe and in other countries, its quality and engineering department maintains the ISO 9001 quality standard, a design file, and proper documentation.
“Our vendors of the pressure vessel are cast by Stainless Foundry & Engineering. Hydro-Thermal delivers about 40% of its product overseas (EU) and that is a large part of its growth plan, especially recently with its expanded product offering due to new product development for pressure service. They work closely with the technical staff in designing patterns and, ultimately, their castings,” explains Jim Zaiser, President and CEO – Hydro-Thermal Corporation. “Ultimately it’s the partnership of these two firms in working together to provide the best solution compliment to the needs of their customers worldwide that has been successful.”
Conclusion
Choices with the pressure directives and codes are available for both EU and UK requirements as well as American codes. Choices for customer applications follow one of the below scenarios:
- Castings are to be supplied in accordance with the EU’s Pressure Equipment Directive 2014/68/EU PED, or:
- Castings are to be supplied in accordance with the UK’s Pressure Equipment (Safety) Regulation 2016/1105, or:
- When jobs require a PMA to non-harmonized materials (ASME, ASTM, etc.) to either of the above directives/regulations, this must be attached every time with the customer’s purchase orders. The purchase order must also reference one of the first two bulleted clauses above in addition to the PMA reference.
Following the directives is critical, as there will be more requirements governing our production of high-spec castings in the future.
About the author
Michael Porfilio is Director of Quality and Technical Services at Stainless Foundry & Engineering, Inc. He has been servicing and working in the foundry industry since 1980, primarily in Metallurgy, Quality Management, Operations, Sales, and as an educator. Michael is NDE Level III and ASME NQA-1 Lead rep.
About this Tech Article
Appearing in the September 2024 issue of Stainless Steel World Magazine, this technical article is just one of many insightful articles we publish. Subscribe today to receive 10 issues a year, available monthly in print and digital formats. – SUBSCRIPTIONS TO OUR DIGITAL VERSION ARE NOW FREE.
Every week we share a new technical articles with our Stainless Steel community. Join us and let’s share your technical articles on Stainless Steel World online and in print.