Wang Hao, steam cracker operator, carries out a routine inspection of the deaerator V-900 in BASF-YPC, China
Thanks to the global pandemic and certain geopolitical tensions, we are living in a very different world from three years ago. This article attempts to sketch these changes and the challenges they pose, as they affect the tubes, pipes and fittings industry.
By James Chater
Background
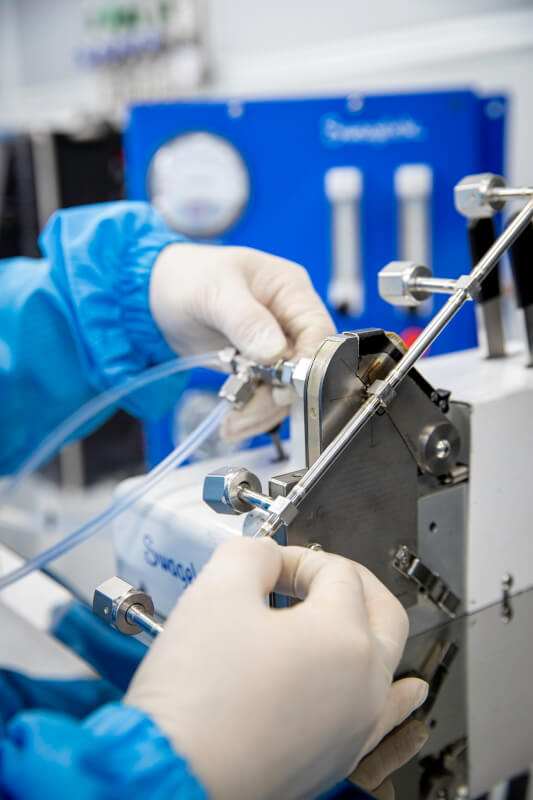
This year is off to a rocky start. Geopolitical tensions in eastern Europe and the Middle East, unresolved differences between the USA and China over trade, inflation, scarcity of materials, container shortages, supply disruptions, empty supermarket shelves… How is all this affecting the tubes, pipes and fittings market?
Not badly, as it turns out – at least so far. It is true that suppliers are having to shoulder higher costs due mainly to soaring raw material costs (titanium, nickel, iron, chromium, molybdenum) and energy costs (electricity, gas, coal) – the latter a special problem due to the energy-intensive nature of the business. Last year, steel and stainless steel were themselves in short supply. Much depends on the extent to which manufacturers can pass on the price increases to their customers.
Many of these problems can be attributed to the process of catching up after the slowdown caused by Covid 19, though some of them, for instance freight delays, already existed and were merely exacerbated by the pandemic.
How long the price surges, delays and scarcities last depends on when the pandemic abates. No one knows this for certain, though the arrival of vaccines gives cause for cautious optimism. However, the end of the pandemic will not mean that things go back to how they were before. Soaring freight charges could have the effect of localizing markets after decades of globalization and could give a spurt to the recycling industry.
Productivity
One problem high-tech manufacturing faces – and one of the factors behind inflation – is staff shortages. Here the golden bullet is productivity, in other words the implementation of new technology to compensate for the shortage of workers. We may expect to see several pipe and tube manufacturers upgrading, retooling, and considering new technologies such as 3D printing. The efficiency of welding processes is especially crucial. (For instance, welding defects are a major factor in the delayed completion of the Flamanville nuclear reactor in France).
Industrial sectors

The demand for tubes, pipes and fittings varies from industry to industry. Since the Covid vaccine rollout, it has been rising, and the only question is the extent to which consumers and end users are willing and able to afford the higher prices.
Oil & gas, petrochemical/chemical, power generation, auto and aerospace are among the industries that have rebounded from the slowdown of 2020. Demand from oil & gas fell sharply in 2020 but has since recovered, and the price surge in oil, coal and natural gas has been nothing less than dramatic. Europe is likely to face an energy squeeze after Germany phased out its nuclear power plants and because of uncertainties about the supply of natural gas from Russia via Nord Stream 2. If Europe turns to the USA for its gas supply, this will be bullish for US shale gas and LNG. Future output will be conditioned by several factors besides Covid 19, for instance inflation and the timetable for replacing fossils with renewables. Especially critical in this regard is the future role of hydrogen (see below).
Power generation

A major challenge, shared with all fossil-fuel industries, is the need to reduce carbon emissions and switch to renewable energy. There are two opposed risks: if traditional energy sources are phased out too quickly, there will be energy shortages; yet not acting in time will make it more difficult to combat climate chaos. Tube and pipe suppliers have indicated to me that they are actively seeking opportunities in low-carbon and other new industries, such as the renewable power generation, hydrogen and semiconductor sectors. Let us consider each in turn.
According to the IAE, the transition to renewables needs to accelerate if the target of keeping within 1.5% emissions reduction is to be met (1). To achieve this requires not only new capacity but also efficiency gains. This is why Sandvik Materials Technology and its Kanthal division are collaborating in the EU-funded Nextower project to advance solar power technology. One of the aims is to increase the temperature of stored heat from 550°C to 750°C, which would involve replacing molten salt by molten lead. An iron-chromium-aluminium (FeCrAl) heat-resistant alloy by Kanthal is central to the project. It is being newly developed for use in energy applications where corrosion is an issue. From it, Kanthal aims to develop a tube made of two different alloys for the plant’s heat exchangers, one that can withstand both the corrosive environment of the molten lead and the internal pressures.
Hydrogen
Hydrogen is rapidly being developed as a greener way of powering industry, fuelling heavy vehicles and storing energy. The traditional production method is to use methane as a feedstock, but “green” hydrogen using electrolysis powered by renewable energy is gaining ground. Hydrogen is clean, and its only emission is water. Another important advantage is that it can be transported along pipelines that were constructed for natural gas. One drawback of using hydrogen as a fuel is that is bulky and therefore needs to be compressed or liquefied, thereby adding to the cost. Another is its tendency to leak, causing explosions; there have been several accidents. Hydrogen is a small molecule that can elude all but the tightest of fittings, making leaks more likely. Therefore the criteria for leak tightness are especially stringent, requiring fittings that can withstand high stress, vibrations and pressures.
The most widely used stainless grades in hydrogen production are 304 and 304L, with 316, 316L, 321 and 347 also used. Welding wires include 308 and 308L as fillers for welding types 304 and 304L, respectively, while 347 is used as a filler material for 321. But these grades may be insufficient for handling hydrogen as a liquid. Since hydrogen has a melting temperature of -252.8°C, it requires pressurized and insulated containers, hoses, pumps, valves, piping and tubes when stored or transported as a liquid and can require embrittlement-resistant alloys that are higher than 304 or 316, such as Hastelloy and Inconel grades.
The pipes often come with an inner and an outer pipe to prevent excessive warming. In 2015 NSSMC introduced a newer grade stronger than 316, HRX19TM, for high-pressure hydrogen environments. This is an austenitic with high strength (allowing for thinner walls), high resistance to embrittlement and excellent weldability (which reduces the need for valves and joints).

Ammonia
One efficient way of storing and transporting hydrogen may be to use ammonia as a “carrier”. Ammonia has long been in use as a precursor to fertilizers and traditionally is obtained via the energy-intensive Haber-Bosch process, whereby hydrogen is reacted with atmospheric nitrogen under pressure. Now several firms are developing “green” ammonia made with hydrogen that comes from electrolysis powered by renewable energy. Ammonia is now being considered as a candidate chemical for capturing, storing and transporting hydrogen.
It is possible to transport ammonia, then “disassociate” it to recover the hydrogen, which can then be used to fuel heavy vehicles. “Green” ammonia is expensive to produce. However, ammonia could be more cost-effective than hydrogen as it has a higher energy density and, in its liquid form, can be stored at a much less energy-intensive –33°C compared to –253°C for hydrogen.
Semiconductors
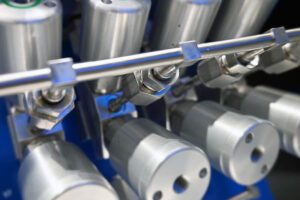
Demand for semiconductors (chips, microchips) has risen rapidly. 2021 saw a marked shortage of these, so it is likely that more facilities will be set up to meet the shortfall. Several of the manufacturers I spoke to said they are looking to expand in this field. Demand for these items, so essential to modern electronics, is rising. 2021 saw a marked shortage of semiconductors (or “chips” as they are often called), so it is likely that more facilities will be set up to meet the shortfall. Because chips are getting smaller but also more powerful, the technology is still evolving. Semiconductors work by allowing only some of the electric current to pass through an electronic device. This is achieved by taking a wafer (usually made of silicon) and adding impurities (often phosphorus or boron) to it so that its conductivity is affected. This process, called “doping”, is brought about by chemical vapour deposition. The gases used in this process are highly toxic and sometimes inflammable. Corrosion due to gas concentration or moisture is a major challenge. The standard material is high-purity 316/316L, obtained through processes such as argon oxygen decarburization (AOD), vacuum induction melting (VIM) and vacuum arc re-melting (VAR). Another alloy that is used is Hastelloy® C-22®, which is replacing 316L in reactive gas handling systems. Tests have shown that it resists corrosion by as much as 288 times that of 316L stainless steel in humidified or high-temperature hydrochloric acid gas streams, and it is believed that its use can reduce defects due to contamination during wafer processing.
Conclusion
These are just some of the ways in which our increasingly high-tech world is affecting the demand for tubes, pipes and fittings. The requirements for precision, purity and material integrity are likely to increase as technology evolves. Welcome to the brave new world!
* This article had benefitted from the input of certain suppliers who answered a questionnaire. My thanks to Mannesmann, Raccortubi and three Japanese companies (who wish to remain anonymous) for their input.
Every week we share a new Featured Story with our Stainless Steel community. Join us and let’s share your Featured Story on Stainless Steel World online and in print.