Over the last few decades, carbon dioxide emissions have been recognized as a major concern in our society. As a direct consequence, new environmental policies have been established to control and measure CO2 emissions. The stainless steels industry, just like any other industry, quantifies and communicates its CO2 emissions performance.
Text & images by worldstainless (formerly International Stainless Steel Forum (ISSF))
Like any other major industry, the stainless steels industry endeavours to reduce its operational CO2 emissions on an ongoing basis. It should however be noted that within the stainless steels industry there are essentially two production systems, namely;
- The scrap-based production system in which the bulk of used raw materials are end-of-life stainless steels and/or similar alloy materials that are recycled to produce new stainless steels. This production system is aligned to geographical locations where the availability of end-of-life materials and scrap is high.
- The Nickel Pig Iron (NPI) production system in which the bulk of the nickel units required for stainless steel production is not derived from stainless steel scrap, but from extracted nickel ores which are converted into NPI. This production system is aligned to geographical locations where the availability of stainless steel scrap is low.
There is currently insufficient available end-of-life stainless steel scrap in all regions of the world to permit only scrap-based production to exist. This situation is likely to remain true for several decades to come.
What emissions & where?
The purpose of this article is to clarify what emissions exist and where they originate from, and in order to achieve these objectives, we have quantified the CO2 emissions from the following three sources.
- Scope 1 Emissions cover direct emissions from business-owned or business-controlled emission sources.
- Scope 2 Emissions cover indirect emissions from the generation of purchased electricity, steam, heating and cooling consumed by the reporting company.
- Scope 3 Emissions are associated with the extraction, preparation and transport of ores and the subsequent production and transport of ferroalloys, including the electricity needed for these processes.
Special note: There is no data currently available from stainless steel producers for the emissions associated with the extraction of nickel ore and the subsequent production of Nickel Pig Iron (NPI). This situation is due to current country-specific legally-imposed disclosure restrictions. However, some of this data is available from industry research groups and as such, this data has been used to provide some ‘indicative guidance numbers’ later in this article.
These described three sources allow us to provide a cradle-to-gate view of the stainless steel industry’s CO2 emissions.
General facts
For the stainless steel industry, scrap has a high intrinsic value. The only limitation is the availability of scrap, especially in emerging countries. The durability of stainless steel restricts the availability of scrap. For example, when stainless steel is used in buildings,
it remains there for many years and cannot be reused before the building is dismantled.
Stainless steel is 100 % recyclable and has one of the highest recycling rates of any material. It is estimated that at least 85% of stainless steels are recycled at the end of their life (see Table 1). Depending on the type, location and availability of stainless steel scrap, production via the EAF route can be economically advantageous. In addition, the recycling system for stainless steel is very efficient and requires no subsidies.
Over the past 20 years the world has produced approximately 670 million metric tons of stainless steel (ISSF, 2021). World production increased from 19 million tons to over 50 millions of tons over the same time period. The growth in the use of stainless steel
has been the highest of any material in the world (ISSF, 2021). Stainless steel’s properties, such as its 100 % recyclability, reusability, durability, low maintenance and product safety partly explain this amazing consumption growth.
Figure 1 shows that the flow of stainless steel is connected by the generation and use of scrap. According to the Yale study, around 50% of the materials to produce stainless steel are scrap (stainless steel and carbon steel scrap) and raw materials make up around 50% of the material used to produce stainless steel. The research carried by Yale University (2019) also provides key estimates of the life cycle of stainless steel products in six main application sectors (see Table 1).

CO2 Emissions
Recent sustainability studies conducted by the ISSF (between 2007 and 2018) show that emissions from the production and use of stainless steels are generally low. However, and in order to clearly quantify the CO2 emissions during the production of stainless steel, we will identify the CO2 emissions from the categories previously defined as Scope 1, Scope 2 and Scope 3.
Please note that the presented emissions data is highly representative of the scrap-based (recycled content) producers. The calculated data for Nickel Pig Iron (NPI) based producers is for indicative guidance only.
Scope 1 Emissions – The current scrap-based producer average is 0.39 tonnes of CO2 per tonne of stainless steel produced. 80% of the producer results sit (normally distributed) in the range 0.20 to 0.60 tonnes of CO2 per tonne of stainless steel produced.
Scope 2 Emissions – The current scrap-based producer average is 0.49 tonnes of CO2 per tonne of stainless steel produced. 93% of the producer results sit (normally distributed) in the range 0.30 to 0.70 tonnes of CO2 per tonne of stainless steel produced.
Scope 3 Emissions – Scope 3 emissions cannot be defined in the same manner. We currently know that there is a linear relationship between the amount of recycled content (scrap stainless steel and low alloy steels) charged and the magnitude of Scope 3 emissions. The higher the recycled content the lower the Scope 3 emissions.
Furthermore, the available data only covers recycled content (also known as the scrap mix) between 40% scrap and 90% scrap. The most common range of recycled content is between 50% and 85% scrap which yields the following Scope 3 emission levels.
- 50% scrap; 2.45 tonnes of CO2 per tonne of stainless steel produced
- 75% scrap; 1.59 tonnes of CO2 per tonne of stainless steel produced
- 85% scrap; 1.25 tonnes of CO2 per tonne of stainless steel produced
The linear relationship is not predicted to continue below a recycled content of 40% because this represents the region where NPI-based production becomes more commonplace. NPI production produces emissions in the average range (specified by geographical source) of 60 to 85 tonnes of CO2 per tonne of nickel produced. This means that if NPI is used to make an 8% nickel-containing stainless steel, the increase in Scope 3 emissions (when compared to a 40% scrap mix) associated with this route will typically be between 4.0 and 6.0 tonnes of CO2 per tonne of stainless steel produced. NB; For comparative purposes, a 40% scrap mix with zero NPI delivers a Scope 3 emissions level of 2.80 tonnes of CO2 per tonne of stainless steel produced. The summary table of emissions is shown in Table 2.
CO2 emissions over 110 years
Figure 2 shows the CO2 production and maintenance emissions for stainless steel, carbon steel and aluminium. Two different types of produced stainless steel have been included, namely Stainless 1 which is produced with an 80% recycled content and Stainless 2 which is produced with a 60% recycled content.
The data comprises CO2 tons emitted per ton of material produced (Scope 1 + Scope 2 + Scope 3) plus any CO2 emissions associated with regular maintenance needs. The carbon steel emissions increase every 10 years due to regular maintenance needed to suppress corrosion. Stainless steel and aluminium emissions do not increase as their passive films prevent the need for regular maintenance. The lifetime of stainless steels in service beyond 110 years is unknown as the industry is currently 108 years old.
The CO2 emissions data and associated included recycling credits are industry supplied figures.
The aluminium data has been adjusted downwards to reflect the fact that the density of aluminium is about one third that of carbon steel and stainless steels.
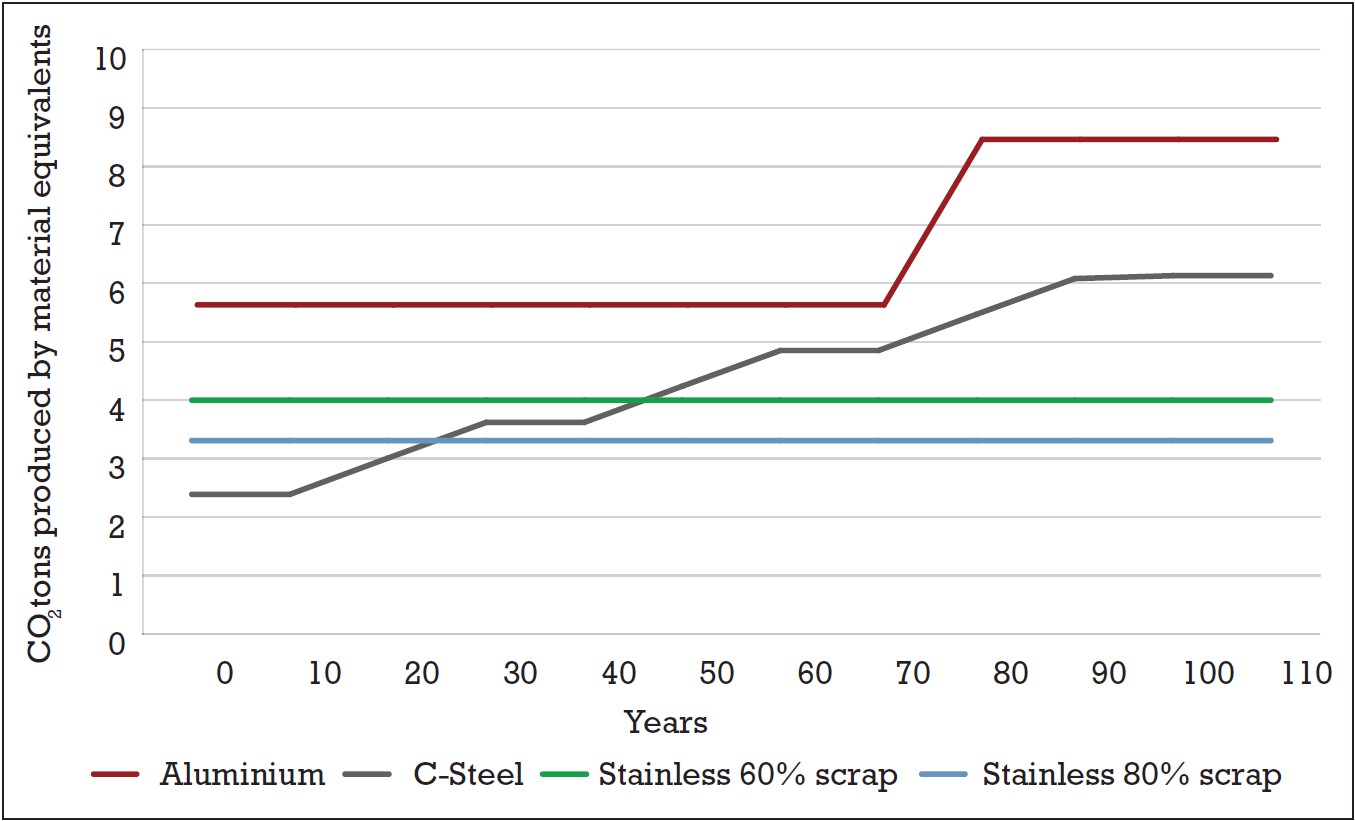