Preem’s IsoCracker plant (ICR) in Lysekil. Photo: Preem
In 2024, work commenced on rebuilding Preem’s so-called IsoCracker plant (ICR) at the company’s refinery in Lysekil, Sweden. The plant is currently being used for the production of diesel. After the conversion, the plant will produce renewable aviation fuel (biojet/SAF) and renewable diesel.
By KCI Editorial
The reconstruction of the Lysekil plant began in 2024 and is scheduled for completion in 2027. It is expected to provide Preem with an additional 1.2 million cubic meters of renewable production capacity. This can be compared to the total capacity of about 530,000 cubic meters per year in 2023. At the same time, Preem is reducing its fossil fuel production capacity by an equivalent amount.
With this investment, Preem aims to become the largest producer of renewable aviation fuel in Northern Europe, and one of the largest producers of renewable fuels for road transportation.
Data shows that the investment is expected to reduce annual fossil fuel emissions at the user level by 2-3 million tons of CO2e, and around 200,000 tons of CO2e locally at the Lysekil refinery.
According to Tommy Johansson, Project Director ICR Revamp Project, the investment decision means that Preem will take another significant step towards the goal of increased production capacity of renewable fuels and ultimately towards climate neutrality. He notes that the plant will mainly produce HVO-100 (hydrotreated vegetable oil, also known as renewable diesel fuel) and SAF (sustainable aviation fuels) but also a small amount of naphtha. In total, production of renewable products will increase by just over 1.1 million m3, of which up to about 600,000 m3 SAF.
Discussing unique features of the ICR project, Mr Johansson says: “We are building our first facility where we can pretreat renewable raw materials ourselves, before feeding them into our production facilities. The plant is designed to handle a large variety of raw materials such as vegetable and animal oils and fats such as rapeseed oil (RSO), used cooking oil (UCO) and rendered fat (Tallow). The project, consisting of a new pretreatment plant and a reconstruction of the existing ICR plant, will be slightly staggered. The pretreatment plant will be initiated first, and the detailed infrastructure design for the ICR will follow later.”
Drop-in jet fuel
In January 2024, Topsoe announced it had been selected as technology provider for Preem’s renewable fuels plant in Sweden, having signed a licensing and engineering agreement with Preem to provide its HydroFlex™ technology for renewable fuels production in Sweden. According to Topsoe, HydroFlex™ enables the conversion of various fats, oils and greases into drop-in renewable jet fuel and diesel that meet all globally aviation fuel and renewable diesel accepted specifications for these fuels. The technology can be deployed in both grassroots units and revamps for co-processing or fully renewable applications.
The demand for SAF is rapidly growing says Topsoe. According to the International Energy Agency’s Net Zero Scenario, over 10% of fuel consumption in aviation by 2030 needs to be SAF to stay on course for net zero CO2 emissions by 2050. In 2022, the International Air Transport Association estimated global SAF production to make up only around 0.1% to 0.15% of total jet fuel demand. At Preem’s lysekil refinery in Sweden, Topsoe’s HydroFlex™ technology will be utilized in Preem’s IsoCracker (a unit that breaks down molecules into lighter components). Topsoe will thereby supports Preem’s long-term target of producing five million cubic meters of renewable fuels and achieving a climate neutral value chain by 2035.
Elena Scaltritti, Chief Commercial Officer at Topsoe, said: “Society needs a significant upscaling of renewable fuels for aviation. We’re excited to take another step on the path to reduce carbon emissions in the transportation sector and aviation in particular. Together with Preem, we already have a proven track-record of delivering impactful results within renewable fuels production, and we’re looking forward to continuing working with Preem on this important task.”
ICR project in brief
Refinery: | Lysekil |
Plant: | ICR (IsoCracker |
Investment: | Approximately SEK 5.5 billion |
Project start: | 2024 |
Start of production: | 2027 |
Renewable production capability: | +1.2 million m3 |
Fossil phase-out: | -1.2 million m3 |
Reduced fossil emissions (Scope 1-3): | Approx. 2-3 million tons CO2e |
Reduced fossil emissions (Scope 1): | Approx. 200,000 tons CO2e |
Products: | Biojet/SAF, HVO |
Production capacity, SAF | ~600,000 m3 |
Production capacity, HVO | ~600,000 m3 |
Peter Abrahamsson, Director of Sustainable Development at Preem, said: “We’re thrilled about the revamp of Lysekil refinery, which is one of the most significant climate investments in Sweden. The demand for sustainable aviation fuels is increasing rapidly, and we are already in dialogue with several major airlines. With this investment, Preem takes another decisive step in the transition from fossil to renewable production. We’re happy to continue working with Topsoe on increasing renewable fuels production.”
Austenitic stainless
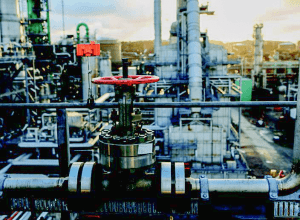
As per a related news update, Alleima is to supply Preem with heat exchanger tubes to be used in the conversion of the Lysekil refinery from fossil to renewable fuels. The investment is an important part of Sweden’s green energy transition and will make Preem the largest producer of renewable jet fuel in northern Europe. The changeover means that Preem will no longer use fossil raw materials such as crude oil, but renewable raw materials instead. To make this possible, advanced technology is required, not least in the pre-treatment unit (PTU) that is to be built. The raw materials will be pre-treated and purified at high temperatures before being used in the production of renewable fuels such as HVO and SAF. The processes in refineries often place high demands on the materials used and renewable fuels are particularly challenging. The raw materials used usually contain chlorides, which can cause corrosion. Therefore, special materials are required that can withstand high temperatures and aggressive chemical environments without corroding.
Group Coek, a heat exchanger manufacturer and one of Alleima’s long-standing customers, booked the order with Preem. “Sanicro® 35 is used for the heat exchanger tubes, channels, and baffles of the heat exchangers.
The material was chosen primarily because of its good corrosion resistance. We at Group Coek are very pleased with this collaboration with Alleima, a company with which we have a long and constructive working relationship,” says Patrick van Roy, CSO of Group Coek.
“We are very happy that Alleima has been trusted to supply heat exchanger tubes and pipes to Preem. Alleima has a long history as a supplier of special steel to Preem’s refineries. The special alloy Sanicro® 35, is an austenitic stainless-steel alloy intended for extremely corrosive environments and an alternative to the use of nickel bases in the heat exchangers for preheating and cooling the renewable raw materials in the PTU. Before a decision could be made, we conducted extensive lab tests together with Preem, which showed that Sanicro® 35 can withstand the extreme conditions and process environments of the pretreatment plant. This resulted in a strong alternative to the more expensive nickel- based alloys that are otherwise used,” says Barinder Ghai, Director Technical Marketing, New Business Development for the Tube division at Alleima.
About Preem
With two refineries in Sweden, Preem accounts for around 80 per cent of the country’s production capacity. About half of all liquid fuel used in Sweden comes from Preem. The company also produces heating and lubricating oils, and supplies many industries with heat and energy.
Around two-thirds of the fuel production is sold to international customers, mainly in Northern Europe.
Preem is currently carrying out a large-scale transition, phasing out fossil fuels in favour of renewables. During the transition the company aims to maintain the reliability of supply in Sweden and abroad.
Preem’s stated aim is to achieve a climate-neutral value chain with net zero emissions by 2035.
About this Featured Story
Appearing in the March 2025 issue of Stainless Steel World Magazine, this Featured Story is just one of many insightful articles we publish. Subscribe today to receive 10 issues a year, available monthly in print and digital formats. – SUBSCRIPTIONS TO OUR DIGITAL VERSION ARE NOW FREE.
Every week we share a new Featured Story with our Stainless Steel community. Join us and let’s share your Featured Story on Stainless Steel World online and in print.